Introduction
In the realm of industrial processes, where the efficient control of fluid flow is paramount, the role of API 600 stands as a crucial beacon. At its core, API 600 is a standard developed by the American Petroleum Institute (API) that sets the bar for the design and manufacturing of gate valves. These valves, omnipresent in a wide array of industries, serve as critical components for regulating the passage of liquids and gases.
In this article, we embark on a journey to unravel the essence of API 600, delving into its historical underpinnings, its significance in ensuring safety and reliability, and its far-reaching impact on various sectors. As we explore the nuances of this standard, we gain insights into the bedrock of industrial valve integrity and the broader implications for diverse applications.
Table of Contents
Don’t miss the Detailed Course on Components of API 600 Valves
Enrollment link
History of API 600 Gate Valve
The history of API 600 is rooted in the development of standardized practices within the industrial sector, particularly in the realm of valve design and manufacturing. Here’s a brief overview of the history of API 600:
Early Industry Standardization Efforts:
In the early 20th century, the industrial landscape was witnessing rapid growth, especially in sectors like oil and gas, chemical processing, and power generation. However, there was a lack of consistency and uniformity in terms of manufacturing practices and product specifications, leading to safety concerns and operational inefficiencies.
Formation of the American Petroleum Institute (API):
In 1919, recognizing the need for standardized practices to ensure safety, quality, and efficiency in the oil and gas industry, a group of industry leaders founded the American Petroleum Institute (API). API’s primary goal was to develop industry standards that would govern various aspects of oil exploration, production, and refining.
Emergence of API Standards:
Over time, API expanded its reach beyond oil and gas, encompassing a wide range of industries and sectors. One critical area that API addressed was the standardization of industrial equipment and components, including valves. The need for reliable and consistent valve designs and manufacturing processes became apparent as industries demanded greater control over fluid flow in their operations.
API 600: Standardizing Gate Valve Design and Manufacturing:
In response to industry demands, API developed various standards to address specific components and equipment. API 600, specifically focusing on gate valves, was established to provide a comprehensive framework for the design, materials, manufacturing processes, and testing procedures for gate valves. This standardization aimed to ensure that gate valves used across industries met consistent quality and safety requirements.
Evolution and Impact:
API 600 evolved over time, incorporating advancements in materials, manufacturing technologies, and industry practices. As industrial processes became more complex and demanding, the API 600 standard continued to adapt to meet new challenges while maintaining its core principles of safety, reliability, and interoperability.
Today, API 600 remains a cornerstone in the valve manufacturing industry, guiding manufacturers, engineers, and operators in the production of gate valves that meet rigorous quality and performance standards. Its historical roots in promoting safety and efficiency have left a lasting impact on industries reliant on fluid control, contributing to safer and more streamlined operations.
Don’t miss the Detailed Course on Components of API 600 Valves
Enrollment link
Understanding API 600: Gate Valves Standard
1. Background and Development
The roots of API 600 trace back to the American Petroleum Institute, a renowned industry organization renowned for its role in shaping standards that ensure safety, efficiency, and quality across the oil and gas sector and beyond. The inception of API 600 marked a pivotal moment, as it aimed to establish a unified framework for the design and manufacturing of gate valves.
2. Scope and Objectives
API 600 casts its influence over a comprehensive scope, encompassing a range of factors critical to gate valve functionality. Its objectives are deeply rooted in guaranteeing safety, reliability, and cross-industry compatibility. The standard sets out to harmonize the diverse aspects of valve production, from materials to design considerations, thereby fostering a cohesive ecosystem of gate valves that can be seamlessly integrated into various industrial systems.
3. Key Requirements
Within the realm of API 600, a multitude of key requirements underpin the standard’s effectiveness:
Design Criteria
The standard delineates stringent design criteria that manufacturers must adhere to. These criteria encompass factors such as the selection of appropriate materials, pressure-temperature ratings that valves must withstand, and precise dimensions and tolerances to ensure proper fit and functionality.
Manufacturing and Testing Requirements
API 600 outlines manufacturing processes that contribute to valve durability and integrity. It emphasizes stringent quality control measures to mitigate defects. Furthermore, the standard mandates thorough testing protocols, including non-destructive testing techniques, to verify the valves’ fitness for operation under diverse conditions.
End Connections and Pressure Seal Design
In recognizing the importance of secure connections, API 600 sets guidelines for end connections that guarantee leak-free operation. Additionally, pressure seal design considerations ensure valves can effectively withstand the demanding pressures they encounter during their service life.
As we explore these requirements, a comprehensive understanding of API 600’s intricacies unfolds, revealing its pivotal role in shaping the very foundation of gate valve reliability and safety.
Don’t miss the Detailed Course on Components of API 600 Valves
Enrollment link
Benefits of API 600 Gate Valve Compliance
The adherence to API 600 brings forth a multitude of benefits that reverberate through industrial processes, bolstering safety, efficiency, and compatibility.
1. Safety and Reliability
API 600 compliance stands as a steadfast guardian of safety. By adhering to standardized manufacturing processes and material requirements, the risk of valve failures and subsequent leaks is significantly reduced. This enhanced reliability not only safeguards personnel and the environment but also contributes to uninterrupted operations and minimized downtime.
2. Interoperability and Compatibility
The hallmark of API 600 is its role in promoting interoperability. Valves adhering to this standard possess standardized dimensions and specifications, allowing them to seamlessly integrate into various systems without compatibility concerns. This compatibility extends beyond the immediate application, facilitating easy replacements and upgrades in the future.
3. Industry Recognition and Compliance
API 600 compliance carries a powerful message of commitment to quality and safety. Regulatory bodies and industry peers recognize and value this compliance, influencing procurement decisions. By adhering to the standard, manufacturers and operators position themselves as stewards of excellence, fostering trust and confidence among stakeholders.
As we contemplate these benefits, the profound impact of API 600 on industrial practices becomes evident. The standard not only enhances individual valve performance but also contributes to a harmonious industrial landscape characterized by enhanced safety, efficiency, and collaboration.
Challenges and Considerations
While API 600 offers a robust framework for gate valve standardization, its implementation is not without challenges and considerations.
1. Implementation Challenges
The complex nature of valve manufacturing presents challenges in adhering to API 600 requirements. Meeting stringent material and manufacturing standards can be resource-intensive and may require specialized expertise. Striking a balance between meeting these standards and accommodating customization needs for specific applications can pose a significant challenge.
2. Evolving Industry Needs
The industrial landscape is in a constant state of evolution, with emerging technologies and novel applications reshaping requirements. As industries embrace automation, IoT, and other advancements, API 600 must remain adaptable to accommodate these changes without compromising its foundational principles. Striking a harmonious balance between traditional valve designs and the demands of a rapidly evolving landscape is an ongoing consideration.
Navigating these challenges requires a forward-thinking approach that embraces innovation while upholding the core tenets of API 600. By doing so, industries can effectively leverage the benefits of standardization while embracing the dynamic nature of technological progress.
In the subsequent sections, we delve into real-world applications, offering insights into how API 600 manifests in critical sectors such as the oil and gas industry and power generation. These case studies shed light on the tangible impact of API 600 compliance on operational excellence and safety.
Don’t miss the Complete Course on Piping Engineering: Check Now
By EPCLand.com
Case Studies: Real-world Applications of API 600 Gate Valve
1. Oil and Gas Industry
The oil and gas sector, known for its complex and demanding operations, relies heavily on gate valves meeting the API 600 standard. In the upstream, midstream, and downstream segments, these valves play a pivotal role in controlling the flow of liquids and gases. For instance:
Case Study: Gate Valves in Oil Refineries
In oil refineries, where the refining process is a delicate balance of various chemical reactions and physical processes, API 600-compliant gate valves ensure the precise control of feedstocks, byproducts, and final products. These valves, designed to handle high pressures and extreme temperatures, contribute to the efficient and safe operation of crucial refinery units.
2. Power Generation Sector
Power plants, serving as the backbone of modern societies, rely on gate valves that adhere to API 600 standards to manage steam and water flow. These valves are crucial for regulating the movement of fluids that drive turbines and generators. A prime example:
Case Study: Gate Valves in Power Plant Steam Control
In power generation, steam turbines convert thermal energy into mechanical energy, which then drives generators to produce electricity. API 600-compliant gate valves are used to control the flow of steam to the turbines, ensuring optimal efficiency and preventing overheating. The standard’s specifications play a vital role in maintaining stable and reliable power production.
Through these case studies, it becomes apparent that API 600 compliance is not just a theoretical framework but a tangible force driving operational success and safety in intricate industrial scenarios. The standard’s impact is felt across diverse sectors, underlining its significance in critical applications.
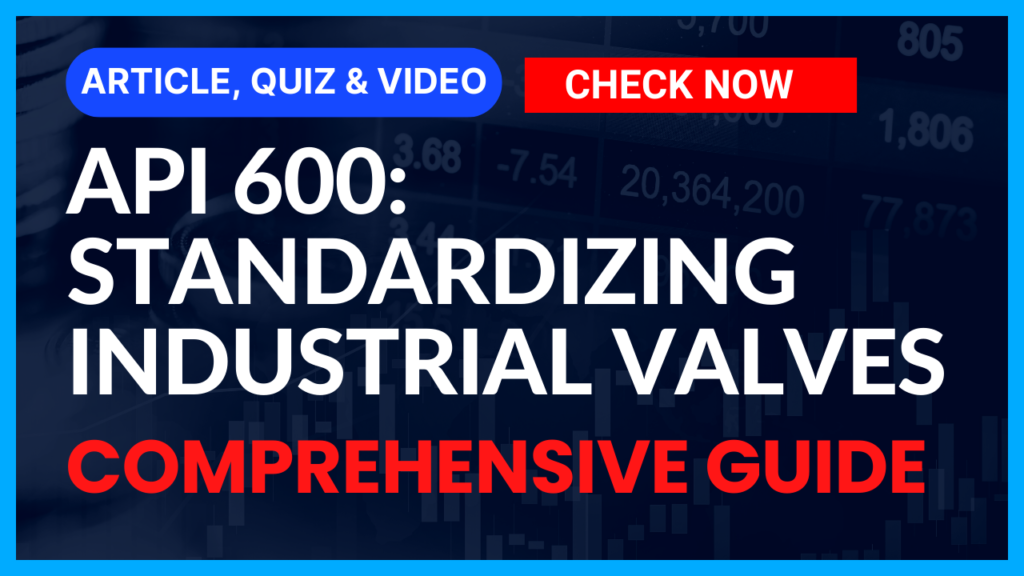
Future Outlook: API 600 Gate Valve and Beyond
As industries continue to evolve and technologies advance, the role of API 600 is set to expand beyond its current boundaries. The future outlook for API 600 includes the integration of its principles with emerging trends and challenges.
1. Advancements in Valve Technology
The realm of valve technology is witnessing a transformation with the infusion of smart technology, automation, and data-driven insights. API 600’s principles will likely adapt to accommodate these innovations, ensuring that valves remain reliable, safe, and compatible with cutting-edge systems.
2. IoT and Remote Monitoring
The Internet of Things (IoT) is revolutionizing industrial processes by enabling real-time monitoring and control. Future iterations of API 600 might incorporate requirements for IoT-enabled valves that can communicate their operational status, contributing to predictive maintenance strategies and heightened efficiency.
3. Sustainable Practices
As sustainability becomes a top priority, API 600 could incorporate eco-friendly materials and design considerations that minimize environmental impact. Valves designed with sustainability in mind can contribute to greener operations across industries.
4. International Collaboration
Given API’s global influence, future iterations of API 600 may involve increased collaboration with international standards organizations to create a harmonized global standard for gate valves. This would further enhance interoperability and streamline international trade.
In essence, the future of API 600 is one of adaptability, innovation, and collaboration. As industries continue to push boundaries, API 600 will evolve to provide a stable foundation for gate valve excellence while embracing the dynamic landscape of technological progress.
Don’t miss the Detailed Course on Components of API 600 Valves
Enrollment link
Conclusion
In the intricate dance of industrial processes, where fluid flow regulation is paramount, API 600 shines as a guiding star. Its historical development, comprehensive scope, and stringent requirements underscore its importance in ensuring safety, reliability, and compatibility in gate valves. By adhering to API 600, industries not only secure operational excellence but also contribute to a landscape of safety, innovation, and sustainable practices. As we move forward, the principles of API 600 will continue to illuminate the path to a future where valve technology thrives in harmony with emerging industrial trends.
Frequently Asked Questions (FAQs)
1. What is API 600?
API 600, developed by the American Petroleum Institute (API), is a standardized set of guidelines for the design and manufacturing of gate valves. These valves are crucial components used to control the flow of liquids and gases in various industries.
2. Why is API 600 important?
API 600 is important because it ensures the safety, reliability, and compatibility of gate valves across different industrial applications. By adhering to API 600 standards, manufacturers and industries can enhance valve performance, reduce the risk of leaks, and promote interoperability.
3. How does API 600 benefit industries?
API 600 compliance offers several benefits to industries. It enhances safety and reliability by setting strict manufacturing and testing requirements. It also promotes interoperability through standardized dimensions and specifications, allowing valves to seamlessly integrate into diverse systems. Moreover, API 600 compliance signals a commitment to quality and safety, influencing procurement decisions and fostering industry recognition.
4. What challenges does API 600 implementation face?
Implementing API 600 can be challenging due to the complexity of valve manufacturing and the strict material and process requirements. Balancing standardization with customization for specific applications poses a significant challenge. Additionally, API 600 must evolve to address emerging industry needs, such as automation and smart technology integration, while maintaining its foundational principles.
5. How does API 600 impact real-world industries?
API 600 has a tangible impact on industries such as oil and gas and power generation. In oil refineries, compliant gate valves ensure precise control of feedstocks and products, contributing to efficient and safe operations. In power plants, these valves manage steam flow, maintaining stable and reliable power generation. API 600’s influence extends beyond theory, playing a critical role in ensuring operational excellence and safety in diverse sectors.
Recommended courses (Published on EPCLand)
- Basics of Piping Engineering
- Piping Layout Engineering
- Piping Material Engineering
- Piping Stress Analysis
- Complete Course on Piping Engineering
- Material Requisitions
- Piping Material Specifications
- Valve Material Specifications
Don’t miss the published articles on following:
Related Video
Attempt Quiz
Question 1:
What does API 600 refer to?
Explanation: API 600 is the standard specification for Bolted Bonnet Steel Gate Valves, which are used in various industries for controlling the flow of liquids and gases.
Question 2:
Which of the following materials is commonly used for the body and bonnet of gate valves in accordance with API 600?
Explanation: Carbon steel is commonly used for the body and bonnet of gate valves in accordance with API 600. This material provides strength and durability required for the valve’s functioning.
Question 3:
What type of end connections are specified in API 600 for gate valves?
Explanation: API 600 specifies flanged end connections for gate valves. Flanged connections provide easy installation and maintenance of the valves in piping systems.
Question 4:
What is the primary function of a gate valve as per API 600?
Explanation: The primary function of a gate valve as per API 600 is to provide on/off isolation by allowing or blocking the flow of fluids through the pipeline.
Question 5:
What is the recommended temperature range for the application of API 600 gate valves?
Explanation: The recommended temperature range for the application of API 600 gate valves is between -20°F and 100°F (-29°C and 38°C). These valves are not designed for extreme temperature conditions.