Introduction
Cold cutting is a modern and innovative technique that has revolutionized the field of cutting operations across various industries. Unlike traditional methods that involve heat, cold cutting utilizes specialized tools and technologies to perform precise cuts without generating heat-affected zones (HAZ) or sparks. In this comprehensive guide, we’ll delve into the different methods of cold cutting, its numerous benefits, and its wide range of applications.
Table of Contents
Don’t miss the Complete Course on Piping Engineering: Check Now
By EPCLand.com
Understanding Cold Cutting
What is Cold Cutting?
Cold cutting refers to the process of severing materials without the use of heat. Traditional cutting methods like flame cutting or plasma cutting generate intense heat, which can lead to thermal deformation, distortion, and the creation of HAZ. Cold cutting eliminates these issues by employing techniques that do not produce heat, making it ideal for applications where precision, safety, and minimal alteration of material properties are paramount.
Methods of Cold Cutting
Mechanical Cold Cutting
Mechanical cold cutting involves using tools such as saws, shears, or abrasive wheels to physically cut through materials. This method is versatile and effective for various materials, including metals, plastics, and composites. It’s commonly used in industries like manufacturing, construction, and shipbuilding.
Waterjet Cutting
Waterjet cutting employs a high-velocity stream of water mixed with abrasive particles to erode and cut through materials. The precision and versatility of waterjet cutting make it suitable for intricate shapes and delicate materials like glass and ceramics.
Laser Cutting
Laser cutting utilizes focused laser beams to melt, vaporize, or blow away material, resulting in precise and clean cuts. It’s widely used in industries such as aerospace, automotive, and electronics due to its exceptional accuracy.
Cold Cutting for Piping: A Modern Solution
The realm of modern cold cutting has ushered in a revolutionary approach to pipe cutting, spanning a remarkable range from pipes under 1 inch in diameter to those exceeding a staggering 120 inches. This cutting-edge technique even extends its prowess to include the precision cutting of commonly used weld joint bevels as it deftly shapes the pipe ends. In stark contrast to the risks posed by torch cutting and grinding, which can create perilous situations in the presence of hydrocarbons, cold cutting stands as a beacon of safety. True to its name, this method refrains from generating sparks and minimizes heat production, resulting in an inherently secure cutting process.
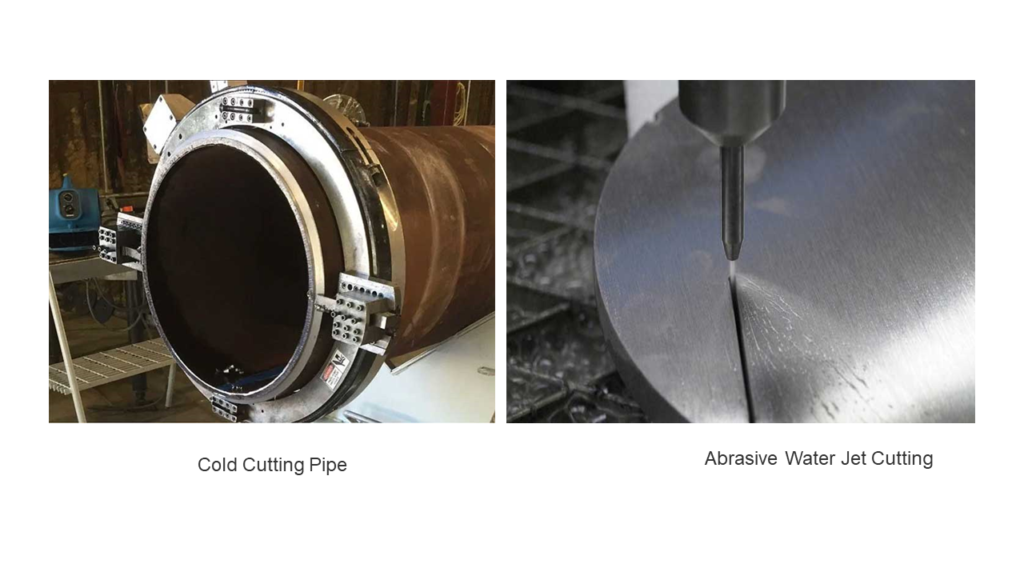
Don’t miss the Complete Course on Piping Engineering: Check Now
By EPCLand.com
Cold Cutting: Versatile, Precise, and Safe
Cold cutting emerges as an embodiment of versatility, precision, and safety in the domain of pipe cutting. What sets cold cutting apart is its capability to enable workers to operate the cutting tool from a safe distance. This distance minimizes potential risks, allowing operators to carry out the cutting operation without endangering their well-being.
Moreover, the remarkable advantage of cold cutting lies in the absence of a heat-affected zone (HAZ). Traditional cutting methods involving heat can alter the properties of the material being cut due to the generation of heat, potentially compromising its structural integrity. Cold cutting circumvents this concern entirely, ensuring that the material retains its original properties without any changes introduced by heat.
In summary, modern cold cutting for piping is a transformative technique that offers an extensive range of cutting possibilities while prioritizing safety, precision, and material integrity. This method not only eliminates sparks and excessive heat but also guarantees that workers can confidently perform cutting tasks from a secure distance. With its capability to maintain the material’s original properties, cold cutting secures its place as a cutting-edge solution in the realm of pipe cutting technology.
Why Opt for Cold Cutting?
Cold cutting technology presents a compelling solution by eradicating a significant portion of severe incidents attributed to the absence of heat generation during cutting procedures. Particularly in industries dealing with hydrocarbons, heat and flame pose considerable hazards. The cold cutting process, with its heat-free nature, delivers a distinct advantage across a spectrum of tasks including pipe and pipeline repair, maintenance, shutdown operations, as well as commissioning and decommissioning processes.
By adopting cold cutting techniques, the risks associated with thermal or hot cutting are effectively nullified. This stands as the primary driving force behind the escalating popularity of cold cutting for pipes and structural components. The pivotal motives for embracing cold cutting procedures include:
Enhanced Safety: The absence of heat transforms the work environment for cold cutting into a secure space for tool operators, significantly minimizing potential risks.
Cost Efficiency: Cold cutting offers a more economical approach compared to hot cutting methods. Moreover, it facilitates quicker execution, making it conducive to cost-effective solutions that seamlessly align with budget constraints.
Benefits of Cold Cutting
Preservation of Material Integrity
Cold cutting preserves the structural and chemical integrity of materials, as there’s no heat to cause changes in material properties. This is crucial for applications where the material’s original characteristics must be maintained.
Enhanced Safety
Unlike traditional methods that generate sparks and heat, cold cutting significantly reduces the risk of fires, explosions, and operator burns. This makes it a safer option, especially in environments with flammable materials.
Minimal Environmental Impact
Cold cutting produces fewer fumes, emissions, and hazardous byproducts compared to heat-based methods. This aligns with environmentally conscious practices and regulatory requirements.
Precision and Accuracy
Cold cutting techniques offer exceptional precision, resulting in clean and accurate cuts with minimal need for secondary finishing or machining operations.
Versatility Across Materials
From metals to composites, plastics to ceramics, cold cutting can be applied to a wide range of materials, making it suitable for diverse industries and applications.
Varieties of Pipe Cold Cutting Machines
Pipe cold cutting machines, also commonly referred to as clamshell lathes, split-frame cutters, or clamshell cutters, offer versatile solutions for precise pipe cutting tasks. Featuring a circular design, these machines are adept at enveloping the pipe using two halves, secured together via a hinge. The rotational cutting tool executes its operation around the circumference of the pipe. Based on their size and capabilities, pipe cold cutting machines can be categorized into three distinct types:
- Low-Profile Cold Pipe Cutter: Designed for compactness and maneuverability, the low-profile cold pipe cutter is adept at handling pipes of varying diameters while maintaining a lightweight and space-efficient form. This type of cutter is ideal for situations where accessibility and tight spaces are a concern.
- Mid-Size Pipe Cold Cutting Machine: The mid-size variant strikes a balance between size and power, making it suitable for a broader range of pipe diameters. With enhanced capabilities, it is well-suited for tasks that require a moderate cutting capacity and versatility.
- Heavy-Duty Cold Pipe Cutting Machine: Engineered to tackle demanding and robust cutting operations, the heavy-duty cold pipe cutting machine is tailored for substantial pipe diameters. Its robust construction and powerful cutting mechanism ensure it can handle larger pipes while maintaining precision and efficiency.
Pipe cold cutting machines exhibit their prowess across a spectrum of pipe diameters, catering to applications that necessitate both precision and high productivity.
These machines stand as invaluable assets, effortlessly handling intricate cutting tasks while offering solutions that align with the specific requirements of the project.
Don’t miss the Complete Course on Piping Engineering: Check Now
By EPCLand.com
Illustrative Instances of Cold Cutting Machines
In the realm of industrial applications, an array of pipe cold cutting machines play pivotal roles. Among these, the clamshell cutter stands as a prominent example, widely embraced for pipe cutting tasks.
1. Clamshell Pipe Cutter: The clamshell pipe cutter is a portable and versatile cold cutting machine, meticulously designed for both cutting and bevelling pipes. Characterized by its reduced weight and compact dimensions, this tool is available across an extensive range of cutter configurations. It shines in the realm of cutting various materials, including Steel, Stainless Steel (SS), Hastelloy, Super Duplex Stainless Steel (SDSS), Inconel, Alloy Steel, and Cladded pipes. Leveraging split-frame technology, the clamshell pipe cutter is adept at handling pipes with considerable thicknesses. It boasts distinct features, including:
- Swifter and Precise Processing
- Comprehensive Machining System with Complementary Accessories
- High-Quality Precision Cuts
- Equipped with Tracking Slides for Uniform Land Machining
Key Components of a Cold Pipe Cutting Machine:
- Frame
- Split Gear Mechanism
- Drive System
- Ball Bearings
- Tool Carriage
- Clamping Feet
2. Band Saws and Diamond Wire Saws: Band Saws and Diamond Wire Saws find their roles in the chemical industries, particularly in situations where precision cutting isn’t the primary requirement. Operating through hydraulic power, these tools require suitable hoses and hydraulic power packs.
Band Saws generate heat on the cutting surface, necessitating the use of suitable coolants during operation.
Diamond Wire Saws, ideal for cutting through pipelines, piles, and caissons, derive their name from the beaded rope adorned with small diamonds on the outer surface. The diamond-encrusted rope facilitates efficient cutting without the issues of compression and jamming.
3. Abrasive Water Jet Cutting: Precision Through Accelerated Erosion
Abrasive Water Jet Cold Cutting stands as an ingenious technique for cutting structures on-site, all without the utilization of heat. This attribute renders the method particularly suitable for environments laden with fire or explosion risks.
The Mechanism of Waterjet Cutting:
At its core, Abrasive Waterjet Cutting entails an accelerated erosion process. This process involves propelling ultra-high pressure water through a ruby or diamond orifice, directed into a “mixing chamber.” This chamber creates a vacuum, compelling garnet sand to merge with the water stream. As a result, waterjet cutting becomes an exceptionally potent and adaptable tool, embraced worldwide across an extensive array of applications.
The journey commences at a sizeable electric-driven oil pump, which thrusts oil at a pressure of 2750 PSI (190 bar) into a heavy-duty intensifier assembly, also known as a pressure amplifier.
Within the intensifier, the pressure undergoes a significant boost. It ascends from domestic supply pressure, which typically hovers around 50-60 PSI (3.45 bar-4.15 bar), skyrocketing to an astonishing 55,000 PSI (3792 bar). This amplification is attributed to the hydraulic piston’s expansive surface area, which is about 20 times larger than that of the water piston. The hydraulic piston’s augmented surface area contributes to a 20-fold increase in water pressure compared to the oil pressure. The ultra-high pressure water then embarks on its journey through pressure piping, eventually reaching the cutting head.
Upon arrival at the cutting head, the stream of high-pressure water undergoes focused manipulation. It passes through a ruby, sapphire, or diamond orifice, resulting in the concentration of the water into a fine “needle” of sorts.
Subsequently, the ultra-high pressure water enters a mixing chamber. Within this chamber, abrasive garnet sand is drawn into the water stream, creating a fusion of abrasive and water. The concoction then exits the cutting head through a focusing tube at velocities up to mach 2, effectively giving birth to an exceptionally potent and efficient cutting tool.
In essence, Abrasive Water Jet Cutting harnesses the principles of accelerated erosion, where ultra-high pressure water combined with abrasive garnet sand forms a dynamic force that conquers a vast array of cutting applications with precision and efficiency.
Distinguishing Pure Water Cutting from Abrasive Water Cutting
When it comes to waterjet cutting technology, two main approaches emerge: pure water cutting and abrasive water cutting. Both methods harness the power of water under high pressure for precision cutting, yet they cater to different types of materials and applications.
Pure Water Cutting:
Pure water cutting, also known as non-abrasive waterjet cutting, is tailored for soft materials that demand delicate yet accurate cutting processes. These materials encompass rubber, foam, gaskets, leather, textiles, and even food products. The technology involves pressurizing water to ultra-high pressure levels and propelling it through a small orifice made of materials like ruby, sapphire, or diamond. The resulting cutting stream is remarkably intense. Operating at speeds of up to 2.5 times the speed of sound, the jet stream facilitates high feed rates, rendering it a powerful precision cutting tool.
Key Points:
- Materials: Soft materials including rubber, foam, gaskets, leather, textiles, and food.
- Orifice: Uses small ruby, sapphire, or diamond orifice.
- Velocity: Jet stream moves at speeds up to 2.5 times the speed of sound.
- Advantage: Effective for high feed rates and precise cuts.
Abrasive Water Cutting:
Abrasive waterjet cutting, on the other hand, caters to hard materials that cannot be effectively cut with water alone. In this method, the water nozzle is swapped with an abrasive cutting head. The high-velocity water stream creates a vacuum, drawing abrasive particles into a mixing chamber. This blend results in a potent abrasive jet stream that’s coherent and forceful. This technique is the go-to solution for cutting materials in sheet or slab form, including challenging substances such as mild and stainless steel, aluminum, sheet metal, composites, decorative stone, synthetic ceramics, and glass.
Key Points:
- Materials: Hard materials in sheet or slab form, such as metals, ceramics, glass, and more.
- Abrasive: Involves introducing abrasive particles into the water stream.
- Power: Generates a powerful abrasive jet stream for effective cutting.
- Application: Suitable for a wide range of tough materials.
In summary, pure water cutting excels in precision cutting of soft materials, utilizing pressurized water to achieve accurate results. In contrast, abrasive water cutting tackles the challenge of hard materials by incorporating abrasive particles into the water stream, producing a forceful jet stream capable of cutting through even the toughest substances. The choice between these methods depends on the nature of the material being cut and the desired precision and efficiency of the cutting process.
Applications of Cold Cutting
Oil and Gas Industry
Cold cutting is used for pipeline maintenance, decommissioning, and repairs. It allows for safe removal of sections of pipelines without the risk of igniting flammable substances.
Shipbuilding and Marine
In shipyards, cold cutting is employed for precision cutting of materials during ship construction, maintenance, and repairs, ensuring the structural integrity of vessels.
Demolition and Decommissioning
Cold cutting is valuable in controlled demolition and dismantling, enabling selective removal of sections without causing structural damage to surrounding areas.
Aerospace and Aviation
Precision and minimal heat-affected zones make cold cutting suitable for aerospace applications, including the cutting of intricate parts and components.
Nuclear Industry
Cold cutting is used in nuclear facilities for dismantling and decommissioning, minimizing the risk of radioactive contamination and ensuring worker safety.
FAQs
Q1: Is cold cutting suitable for all types of materials? A1: Cold cutting is versatile and can be applied to a wide range of materials, including metals, plastics, composites, and ceramics.
Q2: How does cold cutting enhance safety compared to traditional methods? A2: Cold cutting eliminates the generation of sparks and heat, significantly reducing the risk of fires, explosions, and operator burns.
Q3: What industries benefit from cold cutting? A3: Industries such as oil and gas, shipbuilding, demolition, aerospace, and nuclear utilize cold cutting for various applications.
Q4: Does cold cutting produce any heat-affected zones? A4: No, cold cutting methods are designed to eliminate heat-affected zones, preserving the original material properties.
Q5: How precise is cold cutting compared to traditional methods? A5: Cold cutting techniques, such as laser cutting and waterjet cutting, offer exceptional precision and accuracy, often requiring minimal secondary finishing.
In conclusion, cold cutting is a cutting-edge technique that offers a multitude of benefits across industries. From enhancing safety and preserving material integrity to enabling precise cuts and minimizing environmental impact, cold cutting has transformed the way we approach cutting operations. As technology continues to advance, the applications of cold cutting are likely to expand, making it an indispensable tool for various industries seeking safer, more precise, and environmentally-friendly cutting solutions.
Recommended courses (Published on EPCLand)
- Basics of Piping Engineering
- Piping Layout Engineering
- Piping Material Engineering
- Piping Stress Analysis
- Complete Course on Piping Engineering
- Material Requisitions
- Piping Material Specifications
- Valve Material Specifications
Don’t miss the published articles on following:
Related Video
Attempt Quiz
Question 1:
What is cold cutting?
Explanation: Cold cutting is a technique for cutting materials without generating heat. It is often used to prevent heat-affected zones and minimize material distortion.
Question 2:
Which of the following is a common application of cold cutting?
Explanation: Cold cutting is commonly used for tasks such as trimming sheet metal, where the goal is to avoid heat-related distortions or changes in material properties.
Question 3:
Which cutting method is a type of cold cutting?
Explanation: Waterjet cutting is a type of cold cutting method that uses high-pressure water mixed with abrasive particles to cut through materials without generating heat.
Question 4:
What is a key advantage of cold cutting?
Explanation: A key advantage of cold cutting is that it results in minimal distortion and heat-affected zones, making it suitable for applications where preserving material properties is crucial.
Question 5:
Which safety consideration is important when performing cold cutting?
Explanation: Ensuring proper eye protection and respiratory equipment is important when performing cold cutting, as particles and debris can be generated during the cutting process.