Grain accumulation within piping systems is a critical concern that significantly impacts their performance and overall safety. The buildup of various types of grains, such as solid particles, sediment, and debris, can have detrimental effects on fluid flow, pressure drop, and the integrity of the piping infrastructure. In this comprehensive guide, we will delve into the world of grain testing in piping systems, exploring its significance, methods, procedures, and mitigation strategies to ensure optimal system operation.
Table of Contents
Understanding Grain Accumulation in Piping
Grain accumulation occurs when solid particles, contaminants, or other particulate matter gather within the interior of piping systems. This accumulation can result from a combination of factors, including fluid properties, flow rates, piping design, and the nature of transported materials. As grains accumulate over time, they can lead to reduced flow efficiency, increased pressure drop, and even corrosion of the piping materials.
Types of Grains in Piping Systems
Grains that accumulate within piping systems can vary widely in composition and origin. Common types of grains include:
- Solid Particles: These can range from fine particulates to larger solid objects that find their way into the system.
- Sediment: Settled particles that accumulate at the bottom of the pipes due to gravity.
- Debris: Foreign materials that enter the system, often as a result of poor maintenance or faulty equipment.
- Corrosion Byproducts: Chemical reactions within the system can lead to the accumulation of corrosion byproducts.
Factors Contributing to Grain Accumulation
Several factors contribute to the buildup of grains within piping systems:
- Fluid Characteristics: The nature of the fluid being transported, including its viscosity, density, and particulate content, can influence grain accumulation.
- Flow Rates: Higher flow rates might prevent some accumulation, but they can also lead to erosion and increased turbulence, potentially dislodging particles and causing them to accumulate elsewhere.
- Piping Design: Poor piping design, with sections that promote stagnant flow or turbulent areas, can encourage grain buildup.
- Material Transported: The material being transported through the pipes can introduce particles or react with the pipe’s inner surface, leading to accumulation.
Understanding these factors is crucial for recognizing the potential for grain accumulation within piping systems and the subsequent need for effective grain testing and maintenance. In the following sections, we will explore the significance of grain testing and the various methods used to detect and address grain accumulation within piping systems.
Significance of Grain Testing
Effective grain testing within piping systems is paramount for ensuring the longevity, efficiency, and safety of industrial processes and infrastructure. The consequences of unchecked grain accumulation can be extensive and far-reaching, impacting various aspects of system operation.
Implications of Grain Accumulation
Grain buildup can lead to several adverse effects:
- Reduced Flow Efficiency: Accumulated grains obstruct the smooth flow of fluids, leading to increased friction and decreased flow rates. This can hinder the performance of processes and equipment that rely on consistent fluid movement.
- Increased Pressure Drop: As grains accumulate, they create additional resistance to fluid flow. This results in higher pressure drops across the system, requiring pumps to work harder to maintain desired flow rates.
- Corrosion and Erosion: Accumulated grains can promote localized corrosion and erosion, weakening the piping materials and increasing the risk of leaks or failures.
- Blockages and Clogs: Excessive grain accumulation can lead to partial or complete blockages within the piping, causing disruptions in production, system shutdowns, and potential safety hazards.
- Contaminant Transport: Grains within the piping can carry contaminants or particulates that compromise product quality or introduce impurities into the system.
Importance of Maintaining Optimal Flow Conditions
In various industrial processes, maintaining consistent flow conditions is crucial for product quality, efficiency, and safety. Piping systems are central to these processes, and any deviation from optimal flow conditions can result in reduced productivity, increased operational costs, and potential safety risks.
Effective grain testing provides the means to identify and address potential issues before they escalate. By regularly assessing the condition of piping systems and identifying grain accumulation, industries can proactively implement maintenance measures, optimize system performance, and minimize downtime.
In the following sections, we will explore the different types of grain testing methods available for detecting and analyzing grain accumulation in piping systems. These methods are essential tools in the arsenal of maintenance and optimization strategies for ensuring the smooth operation of industrial processes.
Types of Grain Testing
Grain testing methods are diverse and tailored to the specific characteristics of different piping systems and the types of grains they may accumulate. These methods range from visual inspections to advanced analytical techniques, each offering valuable insights into the condition of the piping system.
1. Visual Inspection
Visual inspection involves physically examining the interior of the piping system to identify visible signs of grain accumulation. This method is often the first step in detecting potential issues and can provide immediate indications of the system’s condition.
2. Particle Size Analysis
Particle size analysis involves measuring and characterizing the sizes of particles present within the piping system. Techniques such as microscopy and laser diffraction are used to determine the distribution of particle sizes, which can offer insights into the nature of accumulated grains and their potential effects on flow and system integrity.
3. Density and Composition Analysis
Density and composition analysis techniques, such as X-ray fluorescence (XRF) and energy-dispersive X-ray spectroscopy (EDS), provide information about the elemental composition of accumulated grains. These methods help identify the sources of the grains and any potential chemical reactions that might be contributing to their accumulation.
4. Flow Rate and Pressure Drop Testing
Changes in flow rates and pressure drops can indicate the presence of grain accumulation. By conducting controlled flow rate and pressure drop tests, operators can assess the efficiency of the piping system and identify any abnormalities that might be linked to grain buildup.
In the subsequent sections, we will delve into the procedures involved in each type of grain testing, outlining the steps to be taken, the equipment required, and the interpretation of results. These methods collectively offer a comprehensive approach to understanding the extent of grain accumulation and formulating effective mitigation strategies to address any issues detected.
Grain Testing Procedures
Effective grain testing requires a systematic approach that encompasses various stages, from preparation to result interpretation. Here, we outline the key steps involved in conducting grain testing within piping systems.
1. Preparation
Before initiating grain testing, it’s crucial to prepare the piping system adequately:
- Isolation: Isolate the section of the piping system that needs testing to prevent flow interference from other parts of the system.
- Draining: Ensure that the section being tested is drained of any fluids to facilitate clear visual inspection and accurate testing.
- Cleaning: Thoroughly clean the interior of the piping to remove any surface contaminants that could interfere with testing.
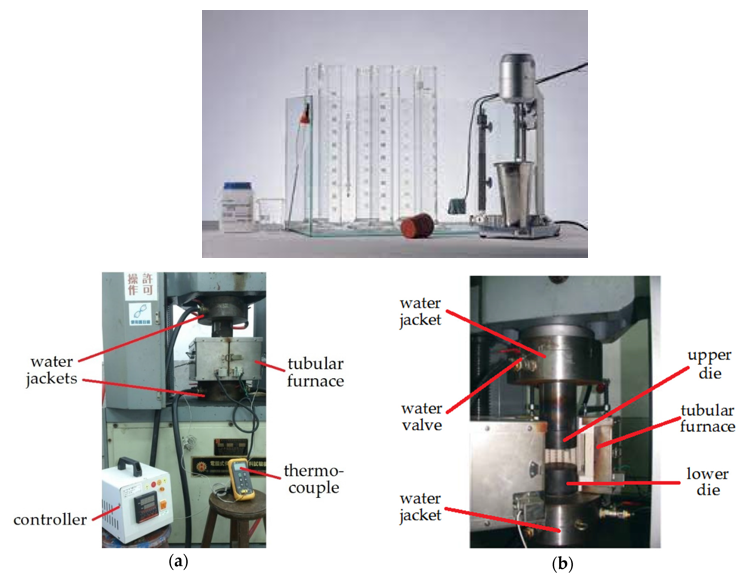
2. Testing Process
Depending on the chosen testing method, follow these procedures:
Visual Inspection
- Use appropriate lighting and inspection equipment, such as borescopes, to visually assess the interior of the piping.
- Look for signs of grain accumulation, including discoloration, deposits, or visible blockages.
- Document any findings for reference and comparison during future inspections.
Particle Size Analysis
- Collect samples of accumulated grains from the piping system.
- Prepare the samples for analysis according to the specific requirements of the chosen particle size analysis technique.
- Use microscopy or laser diffraction equipment to determine the size distribution of particles in the samples.
Density and Composition Analysis
- Extract samples of accumulated grains for analysis.
- Perform XRF or EDS analysis to identify the elemental composition of the grains.
- Compare the composition to known sources to understand the origin of the grains and potential causes of accumulation.
Flow Rate and Pressure Drop Testing
- Control and measure the flow rate of fluid through the isolated piping section.
- Record the pressure drop across the section using pressure sensors or gauges.
- Compare the obtained flow rate and pressure drop values with expected values to identify any deviations that might indicate grain accumulation.
3. Interpreting Results
After conducting the tests, the results need to be carefully analyzed:
- Visual Inspection: Interpret the visible signs of grain accumulation and compare them with previous inspection findings to assess the rate of accumulation.
- Particle Size Analysis: Analyze the particle size distribution to determine the range and concentration of accumulated grains.
- Density and Composition Analysis: Interpret the composition analysis to identify potential sources of grains and assess the risk factors associated with the composition.
- Flow Rate and Pressure Drop Testing: Compare the flow rate and pressure drop values with baseline values to ascertain the impact of grain accumulation on system performance.
In the subsequent sections, we will delve deeper into the specifics of each testing method, providing detailed guidance on conducting the tests effectively and interpreting the results accurately. These procedures serve as essential tools for maintaining optimal system performance and addressing any grain-related issues promptly.
Mitigation Strategies
Upon identifying grain accumulation within piping systems, it’s crucial to implement effective mitigation strategies to prevent further issues and ensure the continued smooth operation of the system. These strategies aim to remove or manage the accumulated grains and address the root causes of their buildup.
Regular Maintenance Schedules
Implementing regular maintenance schedules is essential for preventing excessive grain accumulation. Scheduled cleanings, inspections, and testing can help identify and address issues before they escalate, reducing the risk of downtime and costly repairs.
Fluid Filtration Systems
Installing appropriate fluid filtration systems can help capture and remove particles before they enter the piping system. Filters are available in various sizes and materials to suit the specific needs of different industries and applications.
Improved Piping Design
Consider upgrading or modifying the piping design to minimize areas where grain accumulation is likely to occur. This might involve optimizing flow patterns, incorporating smoother surfaces, and ensuring proper drainage.
Chemical Treatments
In some cases, chemical treatments can be employed to prevent or mitigate grain accumulation. These treatments might involve using additives that inhibit particle adhesion or chemical reactions that lead to accumulation.
Root Cause Analysis
Identifying and addressing the root causes of grain accumulation is crucial for long-term prevention. Whether it’s poor maintenance practices, inadequate filtration, or design flaws, addressing these underlying issues can significantly reduce the frequency and severity of grain buildup.
Data-Driven Decision-Making
Utilize the data gathered from grain testing to make informed decisions about maintenance schedules, system modifications, and mitigation strategies. Data-driven approaches enable proactive management and optimization of the piping system’s performance.
In the following sections, we will delve into real-world case studies that showcase how grain testing and the subsequent implementation of mitigation strategies have positively impacted various industries and applications. These examples provide insights into the practical applications of the strategies discussed and highlight their effectiveness in maintaining optimal system performance.
Case Studies
Real-world case studies provide valuable insights into the practical application of grain testing and the resulting mitigation strategies. These examples demonstrate how industries have addressed grain accumulation issues to improve system performance, efficiency, and safety.
Case Study 1: Manufacturing Facility
In a manufacturing facility, grain accumulation within the coolant piping system was causing reduced coolant flow and increased pressure drop. Regular visual inspections revealed significant buildup of sediment and debris. By implementing a proactive maintenance schedule involving periodic visual inspections and particle size analysis, the facility was able to identify trends in grain accumulation and adjust their maintenance practices accordingly. This resulted in improved coolant flow, reduced pressure drop, and extended equipment lifespan.
Case Study 2: Chemical Processing Plant
A chemical processing plant experienced frequent disruptions due to blockages in their piping system. Particle size analysis revealed that solid particles of varying sizes were accumulating, leading to intermittent clogs. By incorporating advanced particle filtration systems and conducting regular particle size analysis, the plant managed to significantly reduce the frequency of blockages, resulting in uninterrupted production and cost savings.
Case Study 3: Municipal Water Treatment
A municipal water treatment plant detected increased pressure drop in their water distribution piping system. Flow rate and pressure drop testing indicated abnormal conditions. Further analysis using density and composition analysis identified the presence of corrosion byproducts. The plant addressed the issue by implementing targeted corrosion control measures and adjusting the chemical composition of the treated water. As a result, pressure drop was reduced, and the longevity of the piping system was improved.
Best Practices
From these case studies, several best practices emerge for effective grain testing and mitigation:
- Regular Monitoring: Implement routine monitoring and testing to detect grain accumulation early and prevent major issues.
- Data Utilization: Use data collected from various testing methods to make informed decisions and adjustments.
- Proactive Maintenance: Develop and adhere to a maintenance schedule that includes cleaning, inspection, and testing.
- Customized Solutions: Tailor mitigation strategies to the specific characteristics and needs of each piping system.
- Collaboration: Involve multidisciplinary teams in addressing grain accumulation issues, including maintenance, engineering, and operations personnel.
In the concluding section, we’ll summarize the key takeaways from this guide and emphasize the importance of maintaining a proactive approach to grain testing in piping systems.
Conclusion
Grain testing in piping systems plays a crucial role in maintaining the efficiency, reliability, and safety of industrial processes. The accumulation of solid particles, sediment, and debris can lead to a range of issues, from reduced flow efficiency to increased pressure drop and corrosion. This comprehensive guide has highlighted the significance of grain testing and explored various methods for its effective implementation.
By understanding the types of grains that can accumulate, the factors contributing to their buildup, and the implications of unchecked accumulation, industries can take proactive measures to ensure optimal system performance. Visual inspections, particle size analysis, density and composition analysis, and flow rate and pressure drop testing collectively offer a robust toolkit for detecting and addressing grain accumulation.
Through diligent preparation, systematic testing procedures, and careful result interpretation, operators can gain valuable insights into the condition of their piping systems. The data gathered from these tests can guide the implementation of appropriate mitigation strategies, including regular maintenance, improved filtration systems, and tailored design modifications.
Real-world case studies have demonstrated the tangible benefits of grain testing and mitigation strategies across various industries. These examples highlight the positive impact of proactive maintenance on system efficiency, cost savings, and overall productivity.
In conclusion, prioritizing grain testing as a fundamental aspect of piping system management is essential for achieving long-term success in industrial processes. By adhering to best practices and leveraging the insights gained from testing, industries can maintain optimal flow conditions, mitigate risks, and ensure the reliable operation of their piping systems.
FAQs
1. Why is grain testing important in piping systems? Grain testing is crucial because it helps identify the accumulation of solid particles, sediment, and debris within piping systems. Accumulated grains can lead to reduced flow efficiency, increased pressure drop, and corrosion, ultimately affecting the performance and safety of industrial processes.
2. What are the common methods of grain testing? Common methods of grain testing include visual inspection, particle size analysis, density and composition analysis (using techniques like X-ray fluorescence), and flow rate and pressure drop testing. These methods provide valuable insights into the presence, nature, and impact of grain accumulation.
3. How does particle size analysis help in grain testing? Particle size analysis involves measuring the sizes of particles within the piping system. This method provides information about the distribution and concentration of particles, which can help in understanding the effects of grain accumulation on fluid flow and system integrity.
4. Can grain testing prevent corrosion in piping systems? Yes, grain testing can contribute to the prevention of corrosion in piping systems. By identifying the composition of accumulated grains, such as corrosion byproducts, operators can implement targeted corrosion control measures and adjust fluid compositions to mitigate the risk of corrosion-related issues.
5. How often should grain testing be performed? The frequency of grain testing depends on factors such as the industry, the nature of transported materials, and the specific characteristics of the piping system. In general, it’s recommended to incorporate grain testing into routine maintenance schedules, with visual inspections possibly conducted more frequently and other methods employed periodically based on the system’s needs.
Recommended courses (Published on EPCLand)
- Basics of Piping Engineering
- Piping Layout Engineering
- Piping Material Engineering
- Piping Stress Analysis
- Complete Course on Piping Engineering
- Material Requisitions
- Piping Material Specifications
- Valve Material Specifications
Don’t miss the published articles on following:
Related Video
Attempt Quiz
Question 1:
What is the purpose of grain testing in piping?
Explanation: Grain testing in piping involves examining the microstructure of the metal to assess factors such as weld quality, material properties, and potential defects.
Question 2:
Which method is commonly used for grain testing in piping?
Explanation: Metallographic examination, also known as microscopic analysis, is commonly used for grain testing in piping. It involves preparing samples, sectioning, polishing, and observing the microstructure under a microscope.
Question 3:
What does grain size in piping refer to?
Explanation: Grain size in piping refers to the average diameter of individual grains in the metal’s microstructure. It is an important factor that can affect the mechanical properties and performance of the material.
Question 4:
Why is proper grain size important in piping?
Explanation: Proper grain size is important in piping because it affects material properties such as strength, ductility, toughness, and resistance to cracks and fractures. Uniform grain size helps avoid defects and ensures consistent performance.
Question 5:
Which ASTM standard is commonly referenced for grain size determination?
Explanation: ASTM E8 is commonly referenced for determining grain size using the standard test method for macroetch testing of steel bars, billets, blooms, and forgings.