Introduction
In various industries, the smooth and controlled flow of fluids and gases is crucial for efficient operations. One pivotal component that ensures this fluid regulation is the gate valve. Among gate valves, the API 6A standard holds particular significance, especially within the context of the oil and gas sector.
Table of Contents
Don’t Miss Detailed course on Components of API 6A Gate Valves
Enrollment link
Importance of Gate Valves
Gate valves are indispensable devices that allow or block the passage of fluids through a pipe or pipeline. Their pivotal role lies in their capability to provide a full unobstructed flow path when open and a complete shutoff when closed. This characteristic makes gate valves vital for applications where precise control over fluid flow is essential. They are commonly employed in industries such as oil and gas, petrochemicals, water treatment, and more.
API 6A Standard for Gate Valves
In the realm of oil and gas, the API 6A standard takes the lead in defining the stringent requirements for gate valves. Specifically designed for wellhead and Christmas tree applications, the API 6A standard ensures that gate valves used in these critical components of oil and gas exploration and production meet rigorous quality, safety, and performance standards.
By adhering to the API 6A standard, gate valves are constructed to withstand the harsh conditions of high-pressure and high-temperature environments commonly encountered in oil and gas operations. This standardization not only guarantees operational reliability but also contributes to the overall safety of personnel, equipment, and the environment.
In the following sections, we will delve into the intricate details of API 6A gate valves, exploring their design considerations, key features, applications, advantages, challenges, and the trends shaping their evolution. By understanding the significance of these specialized gate valves, industries can ensure smoother operations and minimize risks in their critical fluid handling processes.
Understanding API 6A Gate Valves
The API 6A gate valve is a specialized type of valve that has been meticulously designed to meet the demanding requirements of the oil and gas industry. This section will provide a comprehensive understanding of the API 6A standard and delve into the distinguishing characteristics that set API 6A gate valves apart from other valve types.
API 6A Standard and Its Significance
The American Petroleum Institute (API) established the API 6A standard to ensure the reliable performance of wellhead and Christmas tree equipment used in the exploration and production of oil and gas. Gate valves play a pivotal role in these components, controlling the flow of hydrocarbons from the reservoir to the surface. The API 6A standard encompasses a wide range of technical specifications that pertain to the design, materials, manufacturing, testing, and performance of gate valves used in these critical applications.
Adherence to the API 6A standard is essential for several reasons. First and foremost, it ensures the safety of personnel working in the vicinity of high-pressure and high-temperature wellhead equipment. It also guarantees the integrity of the equipment itself, preventing leaks and malfunctions that could lead to environmental hazards or production interruptions.
Characteristics of API 6A Gate Valves
API 6A gate valves are characterized by several distinctive features that make them suitable for the extreme conditions of the oil and gas industry:
- High-Pressure and High-Temperature Environments: One of the most prominent features of API 6A gate valves is their ability to withstand extreme pressures and temperatures. These valves are designed to operate reliably in environments where pressure levels can reach several thousand pounds per square inch (psi), and temperatures can exceed 1000°F (538°C).
- Robust Construction: API 6A gate valves are constructed using high-quality materials such as carbon steel, stainless steel, and exotic alloys. This robust construction ensures longevity and resistance to corrosion, erosion, and other forms of degradation that are common in oil and gas environments.
- Rigorous Testing: Gate valves manufactured according to the API 6A standard undergo rigorous testing procedures to ensure their integrity and performance. These tests include hydrostatic testing, gas testing, and fire testing, among others, to simulate the harsh conditions they might encounter during operation.
- Precise Sealing Mechanisms: API 6A gate valves employ advanced sealing mechanisms to prevent leakage. These mechanisms can include metal-to-metal seals, elastomeric seals, or a combination of both, depending on the specific application and requirements.
Materials Used in API 6A Gate Valve Construction
The selection of materials for API 6A gate valves is a critical aspect of their design. The choice of materials depends on factors such as the nature of the fluids being transported, the operating conditions, and the potential for corrosion and erosion. Common materials used in API 6A gate valve construction include stainless steel, duplex stainless steel, nickel-based alloys, and more. These materials are chosen for their mechanical properties, resistance to corrosion, and compatibility with the intended operating environment.
In the upcoming sections, we will delve deeper into the key features and components of API 6A gate valves, exploring their gate mechanisms, sealing mechanisms, applications, advantages, challenges, and the trends that are shaping their development in various industries.
Don’t Miss Detailed course on Components of API 6A Gate Valves
Enrollment link
Key Features and Components of API 6A Gate Valves
API 6A gate valves are designed with a multitude of features and components that enable them to function effectively in high-pressure and high-temperature environments. This section will provide an in-depth exploration of the key design elements that distinguish API 6A gate valves and contribute to their exceptional performance.
1. Design and Construction
API 6A gate valves are meticulously engineered to meet the stringent requirements of wellhead and Christmas tree applications in the oil and gas industry. Several design considerations are taken into account:
- High-Pressure and High-Temperature Considerations: These valves are constructed to handle extreme pressures and temperatures encountered in oil and gas operations. Specialized materials and engineering techniques are employed to ensure the valves’ integrity under such conditions.
- Bonnet and Body Designs: The bonnet and body of API 6A gate valves are designed to enhance their structural integrity and sealing performance. The bonnet provides protection for internal components, while the body design facilitates smooth flow and minimal pressure drop.
2. Gate Mechanism
The gate mechanism of API 6A gate valves is a crucial component that directly influences their sealing capabilities and operational efficiency. Two primary gate designs are commonly used:
- Slab Gate Design: This design features a flat gate that moves perpendicular to the flow direction. The slab gate design provides reliable sealing by pressing against the valve seats.
- Expanding Gate Design: In this design, the gate expands in the radial direction as it closes, ensuring effective sealing even in high-pressure environments. The expanding gate mechanism enhances the sealing performance and reduces the likelihood of gate jamming.
3. Sealing Mechanisms
Effective sealing mechanisms are vital to prevent leakage and ensure the proper functioning of API 6A gate valves. Several sealing options are employed:
- Metal-to-Metal Seals: These seals use metal surfaces to create a tight seal when the valve is closed. Metal-to-metal seals are particularly effective in high-pressure and high-temperature environments where elastomeric seals might degrade.
- Elastomeric Seals: Elastomeric seals, made from materials like rubber or synthetic polymers, provide flexibility and effective sealing. They are often used in less extreme conditions.
- Hybrid Seals: Some API 6A gate valves combine metal-to-metal and elastomeric sealing mechanisms to achieve optimal sealing performance across a range of operating conditions.
In the upcoming sections, we will delve into the various applications where API 6A gate valves find their use, the advantages they offer in critical operations, the challenges they face, and the maintenance considerations necessary to ensure their prolonged functionality. Furthermore, we will explore the trends and innovations that are shaping the evolution of API 6A gate valves in response to industry demands.
Applications of API 6A Gate Valves
API 6A gate valves play a pivotal role in various applications within the oil and gas industry, ensuring the safe and efficient control of fluid flow in critical operations. This section will delve into the diverse range of applications where API 6A gate valves are employed.
Oil and Gas Industry
The oil and gas industry relies heavily on API 6A gate valves for a multitude of applications throughout the production and distribution process:
- Wellhead and Christmas Tree Assemblies: API 6A gate valves are integral components of wellhead and Christmas tree assemblies. They are used to control the flow of hydrocarbons from the wellbore to the surface and to isolate the well in case of emergencies.
- Choke and Kill Manifold Systems: Choke and kill manifold systems are vital for well control operations. API 6A gate valves are employed to regulate the flow of drilling fluids and control pressure during well interventions and emergencies.
- Offshore and Subsea Installations: In offshore and subsea environments, API 6A gate valves are used to control production flow and isolate wells. Their robust design and reliable sealing mechanisms are crucial for withstanding the harsh conditions of the sea.
Don’t Miss Detailed course on Components of API 6A Gate Valves
Enrollment link
High-Pressure and High-Temperature Processing Environments
Beyond the oil and gas industry, API 6A gate valves find applications in other industries that require precise flow control in high-pressure and high-temperature environments:
- Chemical and Petrochemical Industry: In chemical and petrochemical plants, API 6A gate valves are used to control the flow of aggressive and corrosive fluids at elevated pressures and temperatures.
- Power Generation: API 6A gate valves are employed in power plants to regulate steam flow, particularly in high-temperature and high-pressure steam systems.
- Mining and Minerals Processing: Industries such as mining and minerals processing utilize API 6A gate valves to control abrasive slurries and high-temperature gases.
- Water Treatment and Distribution: Municipal water treatment facilities use API 6A gate valves for managing water flow in pipelines, especially in applications requiring corrosion resistance and longevity.
Advantages of API 6A Gate Valves
The utilization of API 6A gate valves offers numerous advantages, including:
- Enhanced Pressure and Temperature Capabilities: API 6A gate valves are designed to operate reliably under extreme pressures and temperatures, ensuring safety and efficiency in critical operations.
- Superior Sealing Performance: The advanced sealing mechanisms of API 6A gate valves prevent leakage and ensure the integrity of fluid containment.
- Minimal Pressure Drop: When fully open, API 6A gate valves exhibit minimal pressure drop, allowing for efficient fluid flow without significant energy losses.
- Reliability in Critical Applications: The robust construction and rigorous testing procedures of API 6A gate valves ensure their reliability in demanding applications.
- Compliance with Standards and Regulations: Adherence to the API 6A standard ensures compliance with industry regulations, promoting safe and environmentally responsible operations.
In the upcoming sections, we will delve into the challenges associated with API 6A gate valves, the considerations for maintenance, and the industry trends and innovations that are shaping the future of these essential valves.
Challenges and Maintenance Considerations
While API 6A gate valves offer exceptional performance in high-pressure and high-temperature applications, they also face challenges related to their operating environment. This section will address these challenges and highlight the maintenance considerations necessary to ensure the continued functionality of API 6A gate valves.
Addressing Challenges
Corrosion and Erosion
The aggressive nature of fluids in oil and gas operations can lead to corrosion and erosion of valve components over time. Corrosion-resistant materials and protective coatings are used to mitigate these effects and extend the lifespan of API 6A gate valves.
Mechanical Wear
Frequent cycling and exposure to high pressures and temperatures can lead to mechanical wear in valve components. Proper material selection, precision manufacturing, and regular maintenance help reduce wear and ensure smooth operation.
Environmental Factors
API 6A gate valves in offshore and subsea installations are exposed to challenging environmental conditions, including saltwater corrosion and underwater pressure differentials. Design modifications and materials resistant to marine environments are essential to address these challenges.
Maintenance Considerations
Regular Inspection
Routine inspections are crucial to identify signs of wear, corrosion, or damage. Timely detection allows for proactive maintenance and replacement of components as needed.
Lubrication
Proper lubrication of moving parts, such as stems and gears, reduces friction and wear. Lubrication schedules should align with operational demands and environmental conditions.
Preventive Maintenance
Scheduled maintenance routines, including cleaning, inspection, and replacement of worn components, prevent unexpected failures and ensure consistent performance.
Trained Personnel
Qualified personnel with expertise in API 6A gate valves should conduct maintenance and repair tasks to ensure proper procedures are followed and safety is maintained.
In the subsequent sections, we will delve into the latest industry trends and innovations surrounding API 6A gate valves. These advancements aim to address the challenges faced and enhance the valves’ performance, reliability, and efficiency in various applications.
Don’t Miss Detailed course on Components of API 6A Gate Valves
Enrollment link
Industry Trends and Innovations
The field of API 6A gate valves is continuously evolving to meet the ever-changing demands of industries such as oil and gas, petrochemicals, and more. This section will explore the latest trends and innovations that are shaping the design, manufacturing, and application of API 6A gate valves.
Evolution of Materials and Coatings
Advancements in material science have led to the development of new alloys and coatings that offer enhanced corrosion resistance, durability, and high-temperature capabilities. These materials allow API 6A gate valves to withstand even more challenging operating conditions, extending their service life and reducing maintenance requirements.
Integration of Smart Technology
The integration of smart technology, such as sensors and remote monitoring systems, is transforming the way API 6A gate valves are managed and maintained. Real-time data collection and analysis enable predictive maintenance, reducing downtime and optimizing operational efficiency.
Advances in Manufacturing Techniques
Precision engineering and advanced manufacturing techniques, such as additive manufacturing (3D printing), are being applied to the production of API 6A gate valves. These techniques offer the potential for complex geometries, improved component strength, and faster production cycles.
Enhanced Sealing Mechanisms
Continued research and development are leading to innovative sealing mechanisms that offer improved reliability and performance. Hybrid sealing solutions, combining metal-to-metal and elastomeric seals, are becoming more prevalent, allowing valves to adapt to varying operating conditions.
Environmental Sustainability
With a growing focus on environmental responsibility, API 6A gate valve manufacturers are exploring ways to reduce energy consumption, emissions, and waste during the production process. Sustainable materials and manufacturing practices are being adopted to minimize the environmental impact of valve production.
Customization and Modular Design
The trend toward customization and modular design allows for more flexible solutions that can be tailored to specific applications. Manufacturers are offering a range of customizable features, sizes, and configurations to meet the unique needs of different industries.
In the concluding section, we will summarize the significance of API 6A gate valves in various industries and highlight the key takeaways from our exploration of their design, applications, advantages, challenges, and industry trends.
Conclusion
API 6A gate valves stand as indispensable components in industries where the controlled flow of fluids is paramount. Their ability to regulate flow, provide shutoff capabilities, and withstand extreme pressures and temperatures make them essential for critical operations. From the oil and gas sector to chemical processing, power generation, and beyond, these valves play a vital role in ensuring safety, efficiency, and environmental compliance.
The API 6A standard serves as a foundation for the design, manufacturing, and testing of gate valves used in wellhead and Christmas tree assemblies. By adhering to this standard, industries can ensure the integrity and reliability of their equipment, safeguarding personnel, equipment, and the environment from potential hazards.
Throughout this article, we have explored the intricacies of API 6A gate valves, delving into their key features, materials, applications, advantages, challenges, and the innovative trends shaping their evolution. As industries continue to evolve and demand more robust, efficient, and environmentally conscious solutions, the realm of API 6A gate valves will undoubtedly keep pushing the boundaries of engineering and technology.
In conclusion, the significance of API 6A gate valves extends far beyond their mechanical components—they represent a commitment to operational excellence, safety, and the advancement of industries that rely on precise fluid control. As technology advances and industries evolve, these valves will remain an essential cornerstone of critical applications, ensuring the continued success of various sectors around the world.
FAQs
Frequently asked questions (FAQs) about API 6A gate valves along with their answers:
1. What is the API 6A standard?
- The API 6A standard, established by the American Petroleum Institute (API), defines the specifications and requirements for wellhead and Christmas tree equipment used in the oil and gas industry. It ensures that gate valves and other components meet rigorous quality, safety, and performance standards in high-pressure and high-temperature environments.
2. What makes API 6A gate valves different from other types of valves?
- API 6A gate valves are designed specifically for extreme conditions encountered in the oil and gas industry. They are constructed to withstand high pressures, high temperatures, and corrosive environments. Their robust materials, advanced sealing mechanisms, and adherence to the API 6A standard distinguish them from other valve types.
3. What are the key applications of API 6A gate valves?
- API 6A gate valves are extensively used in the oil and gas industry for applications such as wellhead and Christmas tree assemblies, choke and kill manifold systems, and offshore installations. They are also employed in industries like chemical processing, power generation, water treatment, and minerals processing that require reliable flow control in high-pressure and high-temperature environments.
4. What are the challenges associated with API 6A gate valves?
- Challenges include corrosion and erosion due to aggressive fluids, mechanical wear from frequent cycling, and environmental factors in offshore and subsea installations. Proper material selection, maintenance, and adherence to industry standards are essential to address these challenges.
5. How are API 6A gate valves evolving with industry trends?
- API 6A gate valves are evolving through the use of advanced materials and coatings for improved durability and corrosion resistance. Smart technology integration enables remote monitoring and predictive maintenance. Advances in manufacturing techniques, enhanced sealing mechanisms, and a focus on environmental sustainability are shaping the design and production of these valves.
Recommended courses (Published on EPCLand)
- Basics of Piping Engineering
- Piping Layout Engineering
- Piping Material Engineering
- Piping Stress Analysis
- Complete Course on Piping Engineering
- Material Requisitions
- Piping Material Specifications
- Valve Material Specifications
Don’t miss the published articles on following:
Related Video
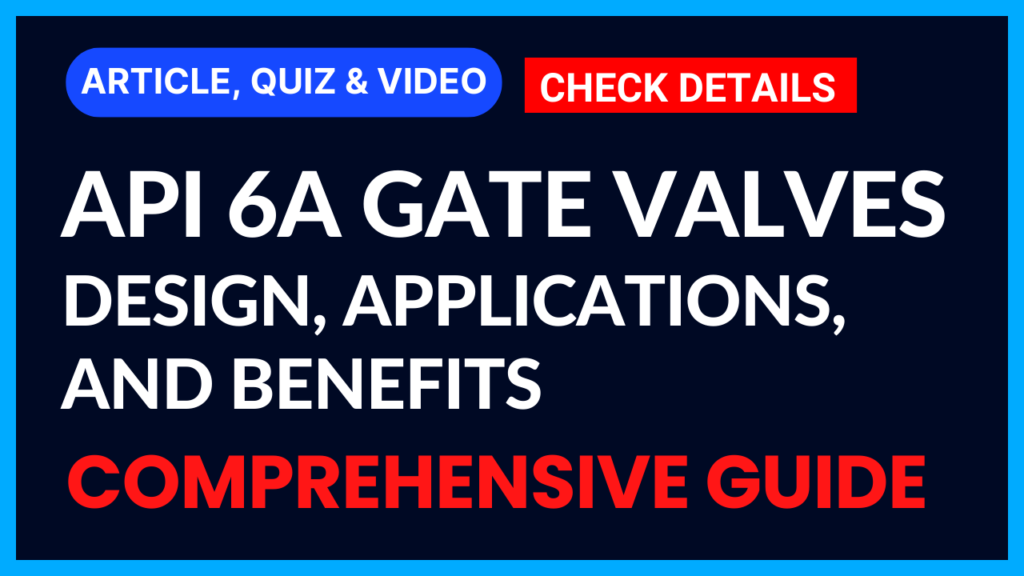
Attempt Quiz
Question 1:
What does API 6A refer to?
Explanation: API 6A is a specification developed by the American Petroleum Institute (API) that covers the requirements for wellhead and Christmas tree equipment, including gate valves, used in the oil and gas industry.
Question 2:
What is the primary function of an API 6A gate valve?
Explanation: The primary function of an API 6A gate valve is to control the flow of fluids in a pipeline by either allowing or blocking the passage of fluids through the valve.
Question 3:
Which type of valve closure mechanism is commonly used in API 6A gate valves?
Explanation: API 6A gate valves commonly use a wedge closure mechanism. The gate or wedge moves up and down to open or close the flow passage, providing a tight seal when closed.
Question 4:
What is the purpose of the API 6A gate valve’s bonnet?
Explanation: The bonnet of an API 6A gate valve houses the valve’s operating mechanism, which includes the stem, handwheel, and other components that control the movement of the gate or wedge.
Question 5:
What is the purpose of API 6A gate valves in the oil and gas industry?
Explanation: The purpose of API 6A gate valves in the oil and gas industry is to control the flow of fluids during drilling and production operations. They play a crucial role in managing the flow of oil, gas, and other fluids in wellhead and Christmas tree equipment.