Introduction
Destructive testing emerges as a crucial technique in the evaluation of piping system strength and integrity. Piping systems play a pivotal role in a multitude of industries, facilitating the transportation of fluids, gases, and various materials. The structural integrity of these piping systems is of paramount importance to ensure safety, reliability, and optimal functionality. This article delves into the realm of destructive testing methods employed for piping, shedding light on their significance and applications.
Table of Contents
Don’t miss the Complete Course on Piping Engineering: Check Now
By EPCLand.com
Purpose of the Article
The primary objective of this article is to provide an in-depth exploration of the various destructive testing methods utilized in the assessment of piping systems. By examining these techniques, readers will gain insights into the methodologies that enable us to ascertain the robustness of piping components and materials. Through a comprehensive overview of destructive testing, this article aims to highlight its vital role in ensuring the safety and effectiveness of piping systems in diverse industries.
Understanding Destructive Testing
Destructive testing stands as a pivotal approach in evaluating the structural properties and performance of materials and components. Unlike non-destructive testing, which seeks to assess properties without causing permanent damage, destructive testing involves subjecting test specimens to controlled stresses that result in the failure of the specimen. This deliberate failure provides valuable information about the material’s behavior, limits, and potential failure modes.
The Balance of Testing Approaches
Destructive testing strikes a balance alongside non-destructive testing methods, collectively forming a comprehensive toolkit for assessing material integrity. While non-destructive techniques like ultrasonic testing and radiography allow for inspecting components without altering their structure, destructive testing provides a deeper understanding of material properties and their response to various stressors.
Necessity in Critical Industries
In industries where failure can have catastrophic consequences—such as aerospace, nuclear, and petrochemical—destructive testing is indispensable. By simulating extreme conditions and pushing materials to their limits, this method uncovers weaknesses that might otherwise remain hidden. This preventive approach contributes significantly to enhancing overall safety and mitigating potential hazards.
Through its deliberate nature, destructive testing offers insights that aid in designing, manufacturing, and maintaining materials and components to withstand demanding operational conditions. The next sections of this article delve into specific destructive testing methods used for piping, shedding light on their distinct applications and advantages.
Common Destructive Testing Methods for Piping
Destructive testing encompasses a variety of methods tailored to assess different aspects of piping materials and components. These methods yield essential data that aids in understanding material behavior, weld quality, and structural integrity. Several widely-used destructive testing methods for piping include:
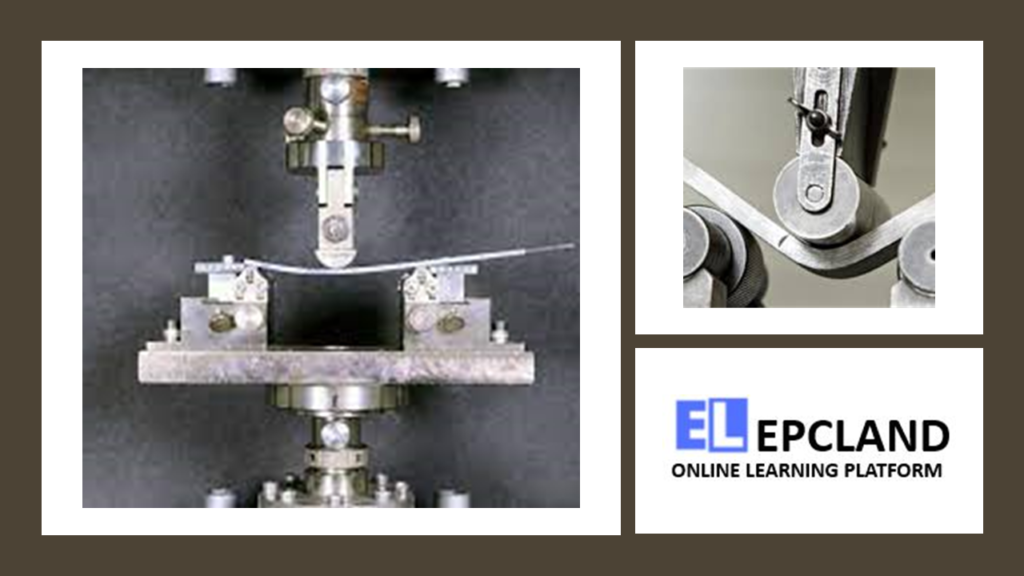
Tensile Testing
Tensile testing is a fundamental method to determine a material’s mechanical properties, such as its yield strength, ultimate tensile strength, and elongation. In the context of piping, this test involves subjecting a cylindrical specimen to axial forces until it fractures. The resulting stress-strain curve provides insights into material behavior under tension, aiding in material selection and design.
Bend Testing
Bend testing assesses a material’s ductility and the quality of welded joints. The guided bend test involves bending a specimen to a specified angle without inducing tensile stress on the outer surface, evaluating the soundness of welds. The side bend test, on the other hand, examines welds by bending the specimen to a specific angle with the outer surface in tension.
Charpy Impact Testing
Charpy impact testing evaluates a material’s resistance to sudden loading and its ability to absorb energy. A notched specimen is subjected to an impact load, and the energy absorbed in fracture is measured. In the context of piping, this test provides crucial data about a material’s behavior under dynamic loading conditions, helping to predict its performance in real-world scenarios.
Hardness Testing
Hardness testing involves indenting a material’s surface using a standardized indenter, allowing measurement of its resistance to penetration. This test aids in understanding a material’s strength, wear resistance, and machinability. Various methods, such as Brinell, Rockwell, and Vickers, offer different scales to measure hardness.
These destructive testing methods provide critical information for evaluating piping materials, welds, and components. The subsequent sections of this article delve into the significance of destructive testing in ensuring safety, material selection, and design validation within piping systems.
Don’t miss the Complete Course on Piping Engineering: Check Now
By EPCLand.com
Importance of Destructive Testing in Piping
Destructive testing plays a pivotal role in maintaining the safety, reliability, and effectiveness of piping systems. By subjecting materials and components to controlled stresses that lead to failure, this testing approach provides invaluable insights into various aspects of piping systems.
Safety and Reliability
Ensuring the safety of personnel, facilities, and the environment is a paramount concern in industries reliant on piping systems. Destructive testing identifies weak points in materials, welds, and components that could potentially lead to failures under operational conditions. By preemptively detecting these vulnerabilities, catastrophic incidents can be prevented.
Material Selection and Quality Control
The selection of suitable materials for specific piping applications is critical. Destructive testing aids in determining the mechanical properties and behavior of different materials under stress, allowing engineers to make informed choices. Moreover, these tests are employed during quality control processes to validate the integrity of materials and components before they are incorporated into the piping system.
Design Validation
Destructive testing contributes to the validation of piping system designs. By subjecting prototypes or representative samples to controlled stresses, engineers can verify whether the design meets performance and safety criteria. This validation process enhances the confidence in the chosen design and assists in optimizing factors such as material thickness and structural dimensions.
Through these roles, destructive testing contributes to the overall robustness and efficiency of piping systems, ensuring they can withstand the demands of their intended applications. The subsequent sections of this article delve into the challenges and limitations associated with destructive testing, as well as potential future trends in testing methodologies.
Challenges and Limitations
While destructive testing provides invaluable insights, it is not without its challenges and limitations that need to be considered:
Sample Preparation and Test Specimens
The accuracy and representativeness of test results heavily depend on proper sample preparation and the use of relevant test specimens. Variations in sample preparation, such as machining, can introduce discrepancies in test outcomes. Additionally, small-sized specimens might not perfectly mirror the behavior of full-scale piping systems, potentially leading to discrepancies between test results and real-world performance.
Resource and Time Intensive
Destructive testing requires dedicated resources, including materials, equipment, and skilled personnel. Furthermore, the process can be time-consuming, potentially slowing down production schedules. Striking a balance between testing requirements and production demands is essential to avoid delays while ensuring the quality and safety of piping systems.
Future Trends and Innovations
Advanced Testing Techniques
Emerging technologies like digital image correlation (DIC) and acoustic emission testing hold promise in advancing destructive testing methodologies. DIC involves tracking deformations using image analysis, providing detailed insights into material behavior during testing. Acoustic emission testing detects stress-related signals during testing, enabling real-time monitoring of material responses.
Simulation and Modeling
Computer simulations are increasingly complementing destructive testing. Advanced modeling techniques, such as finite element analysis (FEA), allow engineers to simulate stress and strain distributions within materials under various conditions. Integrating simulations with destructive testing can reduce the number of physical tests required, optimizing testing efficiency and resource allocation.
As the field of destructive testing evolves, these innovations are poised to enhance the accuracy, efficiency, and predictive capabilities of testing methodologies for piping systems. Such developments are critical in addressing the challenges posed by the dynamic and demanding nature of modern industries.
In conclusion, destructive testing stands as an essential tool in evaluating the structural integrity and safety of piping systems. Its role in identifying vulnerabilities, aiding material selection, and validating designs is pivotal to preventing failures and ensuring the overall reliability of piping systems across various sectors.
Conclusion
In the intricate web of industries that rely on piping systems, the importance of ensuring structural integrity and safety cannot be overstated. Destructive testing emerges as a cornerstone technique in achieving these crucial objectives. Through a comprehensive exploration of various destructive testing methods, this article has underscored their significance and applications in the realm of piping.
By subjecting materials and components to deliberate stress-induced failures, destructive testing offers a unique lens through which engineers and experts can dissect the behavior of piping systems. This technique enables us to unravel critical insights that aid in the selection of suitable materials, assessment of weld quality, and validation of designs.
As industries grow more complex and safety becomes a paramount concern, the role of destructive testing becomes even more vital. The ability to preemptively identify potential weak points, validate designs, and ensure the reliability of materials and components can ultimately prevent catastrophic incidents and safeguard lives, environments, and resources.
Looking ahead, the integration of emerging technologies and innovative testing methodologies promises to refine and augment destructive testing practices. With advanced simulations, real-time monitoring, and refined testing techniques, the field is poised to push the boundaries of our understanding and predictive capabilities.
In a world where precision and reliability are paramount, the marriage of destructive testing with cutting-edge innovations will continue to drive the progress of piping systems across industries, ushering in an era of enhanced safety, efficiency, and performance.
Don’t miss the Complete Course on Piping Engineering: Check Now
By EPCLand.com
Frequently Asked Questions (FAQs) About Destructive Testing for Piping
1. What is destructive testing?
Destructive testing involves subjecting materials or components to controlled stresses that cause them to fail. This intentional failure provides insights into material behavior, properties, and potential failure modes, helping engineers understand performance limits and safety margins.
2. How does destructive testing differ from non-destructive testing?
Non-destructive testing methods, such as ultrasonic testing and radiography, assess material integrity without causing permanent damage. Destructive testing deliberately induces failure to gather detailed information about material properties and behavior under stress.
3. Why is destructive testing important in the context of piping systems?
Destructive testing is crucial for ensuring the safety and reliability of piping systems in critical industries. It identifies weak points in materials, welds, and components that could lead to failures, preventing catastrophic incidents and enhancing overall safety.
4. What are some common destructive testing methods for piping?
Several common destructive testing methods for piping include:
- Tensile Testing: Measures material strength and elongation under tension.
- Bend Testing: Assesses ductility and weld quality through controlled bending.
- Charpy Impact Testing: Evaluates material resistance to sudden impact loading.
- Hardness Testing: Measures material’s resistance to indentation, indicating strength and wear resistance.
5. How does destructive testing contribute to design validation?
Destructive testing validates the design of piping systems by subjecting prototypes or representative samples to controlled stresses. This process helps engineers verify if the design meets performance and safety requirements, aiding in optimizing factors such as material thickness and structural dimensions.
Table for Pros & Cons on Destructive Testing
Table outlining the pros and cons of destructive testing for piping:
Pros of Destructive Testing | Cons of Destructive Testing |
---|---|
Provides Accurate Data: Destructive testing offers precise and detailed information about material properties, behavior, and failure modes. | Irreversible Damage: Testing leads to the destruction of test specimens, making them unsuitable for further analysis or use. |
Reveals Weaknesses: Identifies vulnerabilities in materials, welds, and components, enabling preventive measures against potential failures. | Resource Intensive: Requires specialized equipment, materials, and skilled personnel, which can increase testing costs and time. |
Enhances Safety: Helps prevent catastrophic incidents by identifying flaws that could lead to failures in operational conditions. | Limited Sample Size: Test specimens might not perfectly represent the behavior of full-scale piping systems, potentially leading to discrepancies. |
Aids Material Selection: Provides crucial data for selecting suitable materials based on their mechanical properties and performance under stress. | Incomplete Real-World Simulation: While it simulates extreme conditions, actual operational scenarios might differ, impacting the accuracy of predictions. |
Validates Designs: Validates piping system designs by subjecting prototypes or samples to controlled stresses, ensuring they meet performance and safety requirements. | May Disrupt Production: Testing processes can cause delays in production schedules, impacting project timelines. |
Supports Quality Control: Validates the integrity of materials and components before integration into piping systems, ensuring overall system reliability. | Requires Skilled Interpretation: Test results often need experienced interpretation to extract meaningful insights and conclusions. |
It’s important to note that while destructive testing offers valuable insights, it should be balanced with non-destructive testing methods to achieve a comprehensive evaluation of piping systems.
Recommended courses (Published on EPCLand)
- Basics of Piping Engineering
- Piping Layout Engineering
- Piping Material Engineering
- Piping Stress Analysis
- Complete Course on Piping Engineering
- Material Requisitions
- Piping Material Specifications
- Valve Material Specifications
Don’t miss the published articles on following:
Related Video
Attempt Quiz
Question 1:
What is destructive testing?
Explanation: Destructive testing involves subjecting a specimen to conditions that cause damage or failure to assess material properties, strength, and behavior under stress.
Question 2:
Which of the following is an example of destructive testing?
Explanation: Tensile testing, which involves applying tension until a material breaks, is an example of destructive testing used to determine material strength and ductility.
Question 3:
What is the primary disadvantage of destructive testing?
Explanation: The primary disadvantage of destructive testing is that it destroys the tested specimen, making it unsuitable for further testing or use.
Question 4:
Which destructive testing method is commonly used to assess material hardness?
Explanation: Hardness testing is a destructive method used to determine a material’s resistance to indentation or scratching, providing insights into its mechanical properties.
Question 5:
Why is destructive testing still used despite its disadvantages?
Explanation: Destructive testing is used because it offers detailed insights into material properties and behavior that are not easily obtained through non-destructive methods, despite its drawbacks.