Introduction
HDPE pipes, short for High-Density Polyethylene pipes, are at the forefront of modern construction and infrastructure development. With their exceptional durability, versatility, and environmental friendliness, HDPE pipes have become a go-to choice in various industries and applications. This article delves into the world of HDPE pipes, exploring their history, functions, types, applications, advantages, disadvantages, associated codes and standards, and answering some frequently asked questions.
Table of Contents
Don’t miss the Complete Course on Piping Engineering: Check Now
Enrollment Link
Brief History
Origins of HDPE
HDPE, which stands for High-Density Polyethylene, is a thermoplastic polymer. It was first discovered by a German chemist named Hans von Pechmann in 1898. However, it wasn’t until the 1950s that a breakthrough in its synthesis and industrial application was made by two British scientists, John Rex Whinfield and James T. Dickson. Their work laid the foundation for the development of HDPE pipes as we know them today.
Milestones in HDPE Pipe Development
Over the years, HDPE pipes have seen significant milestones in their development and use. In the 1950s, the first HDPE pipe was produced, and by the 1960s, it found use in various applications. The 1980s witnessed further advancements in the material, leading to increased adoption. Today, HDPE pipes have become a staple in modern infrastructure and construction, offering a range of benefits over traditional materials like metal and concrete.
Basic Function and Working Principle
How HDPE Pipes Work
HDPE pipes are made from high-density polyethylene, a thermoplastic material known for its excellent strength-to-density ratio. These pipes are manufactured through an extrusion process, which involves melting the HDPE material and then forming it into the desired shape. The result is a robust and flexible pipe that can transport various substances, including water, sewage, and chemicals.
Key Features of HDPE Material
- Durability: HDPE pipes are known for their long lifespan, often exceeding 50 years. They resist corrosion and chemical damage, making them ideal for underground and underwater applications.
- Flexibility: HDPE pipes are highly flexible, allowing them to withstand ground movements and adapt to changing environmental conditions.
- Lightweight: Compared to traditional materials like steel or concrete, HDPE pipes are lightweight, making them easier to transport, handle, and install.
- Low Maintenance: These pipes require minimal maintenance, reducing long-term costs for infrastructure projects.

Advantages of Using HDPE Pipes
HDPE pipes offer several advantages over alternative materials, making them a preferred choice for many applications. Some of the key benefits include:
- Leak-Free Joints: HDPE pipes are often joined using heat fusion, creating leak-free connections that minimize the risk of water contamination.
- Corrosion Resistance: Unlike metal pipes, HDPE pipes are immune to rust and corrosion, ensuring water quality remains high.
- Smooth Interior: HDPE pipes have a smooth interior, reducing friction and improving the flow of water or other substances.
- Environmentally Friendly: HDPE is a recyclable material, contributing to sustainable practices in the construction industry.
Manufacturing Process of HDPE Pipes
High-Density Polyethylene (HDPE) pipes are manufactured using a highly controlled and precise process. The production process of HDPE pipes involves several key steps to ensure the material’s quality, strength, and durability. Here’s a detailed explanation of the manufacturing process of HDPE pipes:
1. Resin Preparation
The first step in manufacturing HDPE pipes is the preparation of the HDPE resin. HDPE is a thermoplastic polymer derived from petrochemical sources. The resin is typically in the form of small pellets or granules. It undergoes several processing steps to prepare it for extrusion, which is the primary method used to form HDPE pipes.
2. Extrusion
Extrusion is the core process in HDPE pipe manufacturing. It involves the following steps:
a. Material Loading
The prepared HDPE resin is loaded into a hopper, where it is gravity-fed into an extruder. The extruder is a machine that consists of a screw-like mechanism inside a barrel.
b. Melting and Mixing
Within the extruder, the resin is heated and melted as it moves along the screw. Simultaneously, any additives, pigments, or stabilizers required for specific pipe applications are introduced into the molten resin. The screw’s rotation ensures thorough mixing of the additives with the melted HDPE resin.
c. Formation of the Pipe
Once the HDPE resin is thoroughly melted and mixed with additives, it is pushed through a die. The die is a specially designed shape that imparts the desired dimensions to the extruded pipe. As the molten HDPE exits the die, it forms a continuous, cylindrical shape.
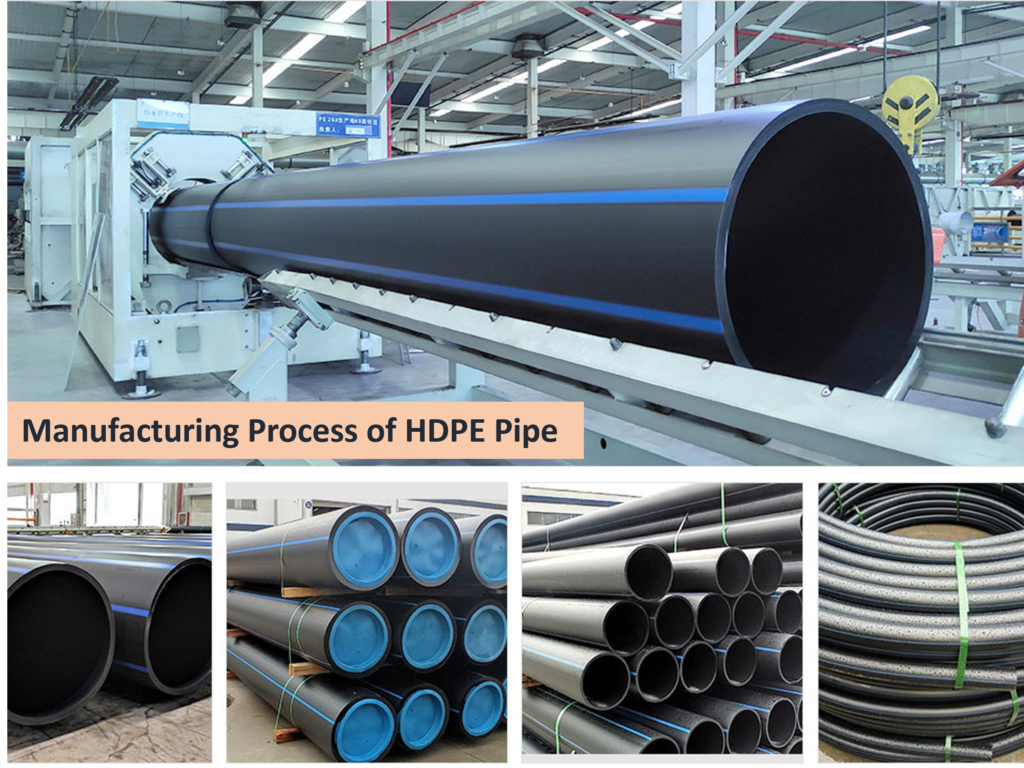
d. Cooling
The newly formed HDPE pipe is then subjected to a cooling process. This can involve various methods, such as water tanks, air cooling, or a combination of both. Rapid cooling is essential to maintain the pipe’s shape and dimensions.
3. Sizing and Wall Thickness Control
After the extruded HDPE pipe has cooled, it passes through a sizing or calibrating system. This system ensures that the pipe achieves its desired outer diameter and wall thickness. The sizing process often involves passing the pipe through a set of calibrated vacuum tanks or a sizing sleeve. This step is crucial for maintaining uniformity and precision in the pipe’s dimensions.
4. Cutting and Length Control
Once the pipe has been sized and its dimensions are within specification, it is cut into individual pipe lengths. The cutting process can involve automated saws or cutting wheels, ensuring precise lengths for each pipe. The lengths of HDPE pipes can vary depending on project requirements, but they are typically available in standard lengths of 20 feet or 40 feet.
5. Quality Control
Quality control is an integral part of HDPE pipe manufacturing. During and after the production process, the pipes are subject to various quality tests to ensure they meet industry standards and customer requirements. Some common quality control checks include:
a. Visual Inspection
Inspecting the pipes for any visible defects, irregularities, or surface imperfections.
b. Dimensional Checks
Measuring the outer diameter, wall thickness, and length of the pipes to confirm they meet specifications.
c. Hydrostatic Testing
Subjecting the pipes to high-pressure water testing to check for leaks or weaknesses.
d. Density and Melt Flow Index Testing
Analyzing the material’s properties to ensure it meets the desired standards.
e. Color and Appearance Testing
Inspecting the color and surface finish of the pipes.
6. Marking and Printing
HDPE pipes are often marked or printed with essential information. This can include manufacturer’s information, pipe size, pressure ratings, and relevant standards or codes.
7. Packaging and Storage
The final step in the manufacturing process is the packaging and storage of the HDPE pipes. They are typically bundled, stacked, and securely packaged for transport to distribution centers or directly to construction sites. Proper storage is crucial to prevent any damage or deformation of the pipes before installation.
In summary, the manufacturing process of HDPE pipes involves resin preparation, extrusion, sizing, wall thickness control, cutting, quality control, marking, and packaging. The use of high-quality materials, precise machinery, and rigorous quality checks ensures that HDPE pipes meet the demanding requirements of various applications, providing reliable and long-lasting infrastructure solutions.
Don’t miss the Complete Course on Piping Engineering: Check Now
Enrollment Link
Types of HDPE Pipes
Different Classifications
HDPE pipes come in various classifications, primarily determined by their density. The two common classifications are High-Density Polyethylene (HDPE) and Low-Density Polyethylene (LDPE). High-density polyethylene is preferred for most applications due to its superior strength and durability.
Key Specifications
HDPE pipes are available in a range of sizes and dimensions to accommodate different needs. They are typically classified by their Outer Diameter (OD) and pressure rating. Common pressure ratings include PN4, PN6, PN8, PN10, PN12.5, PN16, PN20, and PN25, indicating the maximum allowable working pressure.
Notable Variations
- HDPE Water Pipes: These are designed for transporting potable water and are color-coded in blue for easy identification.
- HDPE Gas Pipes: Specially designed for gas distribution, these pipes are typically yellow and can withstand the demands of natural gas transportation.
- HDPE Sewer Pipes: Ideal for sewage and wastewater applications, these pipes are often green or black, signifying their use in underground systems.
- HDPE Geothermal Pipes: Engineered for geothermal energy systems, these pipes offer efficient heat exchange and long-term durability.
- HDPE Mining Pipes: These pipes are robust enough to handle the challenges of mining applications, including abrasive materials and rugged environments.
Applications of HDPE Pipes
Versatility Across Industries
HDPE pipes find applications in a wide range of industries and sectors due to their versatility and adaptability. Some of the industries that commonly use HDPE pipes include:
1. Water Supply and Distribution
HDPE pipes are the go-to choice for water supply systems, from municipal water distribution to rural and agricultural water networks. Their durability ensures the safe delivery of clean water to communities.
2. Wastewater Management
Sewer and wastewater systems benefit from the corrosion resistance of HDPE pipes, reducing the risk of leaks and contamination. Their smooth interiors allow for efficient flow, reducing blockages.
3. Gas Distribution
HDPE gas pipes are the preferred choice for natural gas distribution due to their safety, durability, and resistance to corrosion. They are also used for transporting industrial gases.
4. Mining Industry
In the mining sector, HDPE pipes are used to transport abrasive materials, slurry, and mine waste. Their toughness and resistance to chemical erosion make them ideal for these demanding applications.
5. Agriculture
Agricultural irrigation systems rely on HDPE pipes for their flexibility and efficiency. They are suitable for transporting both potable and non-potable water for crop irrigation.
6. Geothermal Energy
HDPE geothermal pipes are crucial for the efficient exchange of heat in geothermal systems, contributing to renewable energy solutions.
7. Industrial Applications
Many industries use HDPE pipes for various purposes, including chemical transport, industrial effluent disposal, and cooling water systems.
Real-World Examples and Case Studies
To understand the practical significance of HDPE pipes, let’s explore some real-world examples and case studies:
Case Study 1: Water Supply in a Developing Nation
In a developing nation facing water scarcity, HDPE pipes were used to create a robust and reliable water supply network. The flexibility of HDPE allowed for easy installation in challenging terrain, providing clean water to remote villages.
Case Study 2: Gas Distribution Upgrade
An aging gas distribution system in a major city was upgraded with HDPE gas pipes. The new system enhanced safety, reduced maintenance costs, and improved the overall efficiency of gas delivery.
Case Study 3: Mining Efficiency
A mining company adopted HDPE mining pipes to transport abrasive materials from their mining site to a processing plant. The durability of HDPE reduced maintenance downtime and increased productivity.
Advantages of HDPE Pipes in Various Applications
HDPE pipes offer several advantages across different applications, including:
- Cost-Efficiency: Reduced installation and maintenance costs due to lightweight and easy-to-handle pipes.
- Environmental Sustainability: Recyclable material with a lower carbon footprint compared to alternative materials.
- Leak Prevention: Heat fusion joints eliminate the risk of leaks, maintaining the integrity of the transported substance.
- Longevity: HDPE pipes have a long service life, reducing the need for frequent replacements.
Don’t miss the Complete Course on Piping Engineering: Check Now
Enrollment Link
Advantages & Disadvantages
Table: Advantages of HDPE Pipes
Advantages | Description |
---|---|
Durability | HDPE pipes have a long lifespan, exceeding 50 years. |
Corrosion Resistance | Immune to rust and corrosion, ensuring water quality. |
Lightweight | Easy to transport, handle, and install. |
Flexibility | Can withstand ground movements and adapt to changes. |
Low Maintenance | Requires minimal maintenance, reducing long-term costs. |
Table: Disadvantages of HDPE Pipes
Disadvantages | Description |
---|---|
Limited Temperature Resistance | Sensitive to extreme heat or cold. |
Susceptibility to UV Degradation | Prolonged exposure to UV radiation can degrade the material. |
Installation Challenges | Requires specific techniques and equipment for proper installation. |
Environmental Concerns | Concerns related to the disposal and recycling of HDPE materials. |
Associated Codes & Standards
Industry Standards
HDPE pipes are subject to industry standards to ensure quality, safety, and performance. Some of the notable standards and organizations include:
- ASTM International: ASTM provides standards for HDPE pipes used in various applications, ensuring quality and performance.
- ISO 4427: An international standard for HDPE pipes used in water supply systems, specifying requirements and test methods.
- EN 12201: European standards for HDPE pipes for water supply, including dimensions, quality, and performance criteria.
- AGA (American Gas Association): AGA sets standards for HDPE pipes used in gas distribution systems to ensure safety and reliability.
Conclusion
HDPE pipes, short for High-Density Polyethylene pipes, represent a remarkable evolution in the world of modern infrastructure and construction. These versatile, durable, and eco-friendly pipes have become indispensable across various industries and applications, making them a symbol of progress and innovation in the construction field.
The brief history of HDPE pipes reveals the journey from their discovery in the early 20th century to their breakthrough and widespread adoption in the mid-20th century. Over the years, HDPE pipes have gone through numerous innovations and improvements, solidifying their position as a reliable and efficient choice for many applications.
The basic function and working principle of HDPE pipes, driven by the outstanding properties of the material, underscore their appeal. HDPE pipes boast key features like durability, flexibility, lightweight design, and low maintenance requirements. Their advantages extend beyond these attributes, including leak-free joints, corrosion resistance, smooth interior surfaces, and environmental sustainability.
HDPE pipes come in various classifications, with High-Density Polyethylene (HDPE) being the predominant choice due to its superior strength and durability. They are available in different sizes and pressure ratings, making them suitable for a wide range of applications.
These applications span various industries, from water supply and wastewater management to gas distribution, mining, agriculture, geothermal energy, and industrial processes. Real-world case studies demonstrate the tangible impact of HDPE pipes in improving efficiency, safety, and sustainability in these industries. The advantages of HDPE pipes in these applications are evident in terms of cost-efficiency, environmental responsibility, leak prevention, and longevity.
Nevertheless, it’s essential to acknowledge the limitations of HDPE pipes, as highlighted in the disadvantages section. These limitations include limited temperature resistance, susceptibility to UV degradation, installation challenges, and environmental concerns related to material disposal and recycling.
To ensure the quality, safety, and performance of HDPE pipes, they are subject to industry standards set by organizations like ASTM International, ISO 4427, EN 12201, and the American Gas Association (AGA). These standards help maintain the integrity and reliability of HDPE pipe systems.
Finally, the Frequently Asked Questions (FAQs) address common queries about HDPE pipes, offering a comprehensive understanding of their significance, applications, installation, environmental considerations, and comparisons with other pipe materials.
In conclusion, HDPE pipes are at the forefront of modern infrastructure development, providing solutions to critical challenges in the construction industry. Their success is grounded in a perfect blend of innovation, durability, and sustainability. As construction and infrastructure needs continue to evolve, HDPE pipes are expected to maintain their essential role, making them a symbol of progress and advancement in the field of construction and infrastructure development.
Frequently Asked Questions (FAQs)
FAQ 1: What is HDPE, and why is it used for pipes?
Answer: HDPE stands for High-Density Polyethylene, a thermoplastic material known for its exceptional strength and durability. It is used for pipes due to its corrosion resistance, flexibility, low maintenance requirements, and longevity, making it an ideal choice for various applications.
FAQ 2: What are the common applications of HDPE pipes?
Answer: HDPE pipes are commonly used in water supply and distribution, wastewater management, gas distribution, mining, agriculture, geothermal energy, and various industrial applications due to their versatility and durability.
FAQ 3: How are HDPE pipes installed and maintained?
Answer: HDPE pipes are typically installed using heat fusion techniques, which create leak-free joints. Maintenance requirements are minimal, thanks to the material’s durability and resistance to corrosion.
FAQ 4: Are there environmental concerns with HDPE pipes?
Answer: While HDPE is recyclable, concerns exist regarding the disposal and recycling of HDPE materials. Proper recycling and disposal practices are essential to mitigate environmental impacts.
FAQ 5: How do HDPE pipes compare to other pipe materials?
Answer: HDPE pipes offer advantages over traditional materials like metal and concrete, including corrosion resistance, flexibility, and low maintenance. The choice between materials depends on the specific application and requirements.
Recommended courses (Published on EPCLand)
- Complete Course on Piping Engineering
- Basics of Piping Engineering
- Piping Layout Engineering
- Piping Material Engineering
- Piping Stress Analysis
- Material Requisitions
- Piping Material Specifications
- Valve Material Specifications
- Plant Design & Layouts-OISD 118
- Isometric Management
Library of Technical Articles
Don’t miss out the collection of 15+ articles on following topics:
- Basics of Oil and Gas Industry
- Valves
- Testing
- Tank
- Piping Bulk Items
- Pipe
- Metallurgy
- Piping Materials
- Layout
- Instrumentation
- Heat Exchanger
- Type of Contracts
- Codes and Standards
- ASTM Standards
- Articles on Piping Specialty Items
Video details of Complete Course on Piping Engineering
Don’t miss the Complete Course on Piping Engineering: Check Now
Enrollment Link
Attempt Quiz
Question 1:
What is the primary advantage of using HDPE pipes in Oil & Gas projects?
Explanation: The primary advantage of using HDPE pipes in Oil & Gas projects is their high corrosion resistance and flexibility.
Question 2:
What is the main drawback of using HDPE pipes in high-temperature applications?
Explanation: The main drawback of using HDPE pipes in high-temperature applications is their low temperature resistance.
Question 3:
Which type of joints are commonly used to connect HDPE pipes in Oil & Gas projects?
Explanation: Welded joints are commonly used to connect HDPE pipes in Oil & Gas projects.
Question 4:
What is the primary application of HDPE pipes in offshore Oil & Gas projects?
Explanation: The primary application of HDPE pipes in offshore Oil & Gas projects is subsea water injection.
Question 5:
Which factor makes HDPE pipes suitable for trenchless installation methods?
Explanation: HDPE pipes are suitable for trenchless installation methods due to their high impact resistance.
Question 6:
What does the term “PE” in HDPE stand for?
Explanation: The term “PE” in HDPE stands for Polyethylene.
Question 7:
What is the typical color of HDPE pipes used in Oil & Gas projects?
Explanation: The typical color of HDPE pipes used in Oil & Gas projects is black.
Question 8:
What is the primary factor that makes HDPE pipes resistant to chemical corrosion?
Explanation: The primary factor that makes HDPE pipes resistant to chemical corrosion is their high chemical inertness.
Question 9:
What is the standard temperature range HDPE pipes can typically withstand?
Explanation: HDPE pipes can typically withstand a temperature range from -20°C to 80°C.
Question 10:
What is the typical lifespan of well-maintained HDPE pipes in Oil & Gas projects?
Explanation: Well-maintained HDPE pipes in Oil & Gas projects can have a typical lifespan of 30 to 50 years.