1. Introduction
The oil and gas industry operates in demanding environments where efficiency and safety are paramount. Hose couplings, though seemingly small components, play a crucial role in ensuring seamless operations. These devices facilitate the transfer of fluids within various segments of the industry, from exploration to transportation and refining. Understanding their evolution, functionality, and applications is vital for project success.
Table of Contents
Don’t miss the Complete Course on Piping Engineering: Check Now
Enrollment Link
2. Brief History
Hose couplings have come a long way since their inception. Initially, rudimentary designs were used, but over the years, technological advancements have transformed these couplings into highly efficient components. The journey of hose couplings in the oil and gas sector mirrors the industry’s growth, marked by innovations and improvements that have enhanced performance and reliability.
3. Basic Function and Working Principle
At its core, a hose coupling serves the purpose of connecting hoses securely, allowing the transfer of various fluids, including oil and gas. The working principle involves a secure locking mechanism that prevents leakages and ensures a continuous flow. The coupling’s design and materials are meticulously chosen to withstand the industry’s harsh conditions, including high pressures and extreme temperatures.
4. Main Components & their Functions
Components of a Hose Coupling and Their Functions
Component | Function |
---|---|
Body | Provides structural integrity and support |
Gasket | Ensures a tight seal, preventing leakages |
Locking Mechanism | Secures the connection, preventing disconnections |
Handles/Levers | Facilitate easy connection and disconnection (if present) |
A typical hose coupling comprises several components, each serving a specific function. The main parts include the body, gasket, locking mechanism, and sometimes additional features such as handles or levers. The body provides structural integrity, the gasket ensures a tight seal, and the locking mechanism secures the connection. Understanding these components is essential for choosing the right coupling for specific applications, ensuring optimal performance and longevity.
Understanding these components is essential for choosing the right coupling for specific applications, ensuring optimal performance and longevity.
5. Types of Hose Couplings
Types of Hose Couplings and Their Applications
Type | Application |
---|---|
Quick Disconnect | Rapid connections and disconnections |
Cam and Groove | Secure and leak-proof connections |
Flanged | Robust design for high-pressure scenarios |
Bauer | Versatile and easy to use |
Specialized Variants | Unique applications (e.g., chemical transfer) |
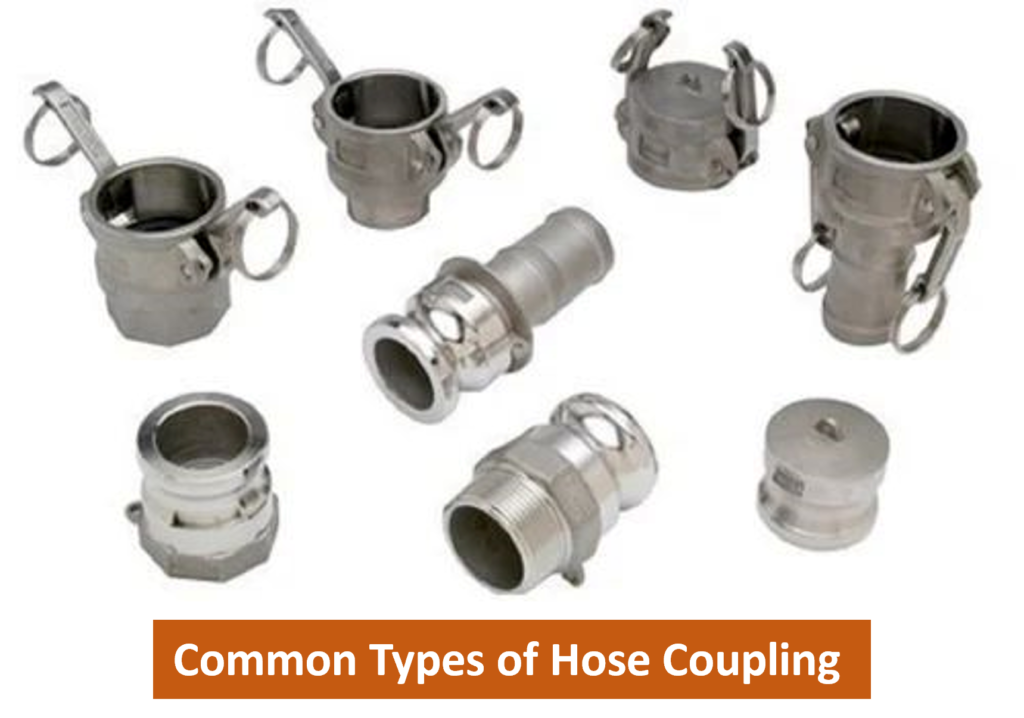
In the oil and gas industry, various types of hose couplings are employed based on specific requirements. Quick disconnect couplings offer rapid connections and disconnections, enhancing operational efficiency. Cam and groove couplings provide a secure and leak-proof connection, widely used in fluid transfer applications. Flanged couplings are favored for their robustness, ideal for high-pressure scenarios, while Bauer couplings are renowned for their versatility and ease of use. Additionally, specialized variants cater to unique demands, highlighting the adaptability of hose couplings in diverse applications.
Don’t miss the Complete Course on Piping Engineering: Check Now
Enrollment Link
6. Applications of Hose Couplings in Oil & Gas Industry
Applications of Hose Couplings in the Oil & Gas Industry
Application | Description |
---|---|
Exploration and Drilling | Transfer of drilling fluids for seamless operations |
Oil and Gas Transport | Safe transfer of crude oil and natural gas |
Refining and Processing | Efficient movement of fluids within processing plants |
Emergency Response | Rapid deployment for containment and cleanup efforts |
Hose couplings find extensive applications across the oil and gas sector. During exploration and drilling operations, they facilitate the transfer of drilling fluids, ensuring the seamless functioning of drilling equipment. In oil and gas transport, these couplings enable the safe transfer of crude oil and natural gas from extraction sites to processing plants or refineries. Moreover, hose couplings play a critical role in refining and processing plants, ensuring the efficient movement of various fluids within the intricate network of pipelines. Additionally, these couplings are vital in emergency response scenarios, allowing rapid deployment of hoses for containment and cleanup efforts during spills or leaks.
7. Advantages and Disadvantages
Advantages of Hose Couplings in Oil & Gas Projects
Advantage | Description |
---|---|
Efficient Fluid Transfer | Swift and efficient transfer of fluids |
Versatility in Application | Adaptable to a wide range of operational needs |
Durability and Longevity | Withstands harsh environmental conditions |
Ease of Maintenance | Modular design allows for easy maintenance |
- Efficient Fluid Transfer: Hose couplings facilitate swift and efficient transfer of fluids, minimizing downtime and optimizing productivity.
- Versatility in Application: Their diverse types cater to a wide range of applications, making them adaptable to various operational needs.
- Durability and Longevity: Constructed from robust materials, hose couplings are designed to withstand harsh environmental conditions, ensuring long-term functionality.
- Ease of Maintenance: Their modular design allows for easy maintenance, reducing operational disruptions and maintenance costs.
Disadvantages of Hose Couplings in Oil & Gas Projects
Disadvantage | Description |
---|---|
Limited Pressure and Temperature | Certain couplings have limitations in extreme conditions |
Potential for Leakage | Improper installation or wear can lead to leaks |
Regular Inspection Requirements | Periodic checks are necessary to identify wear and tear |
- Limited Pressure and Temperature Range: Certain hose couplings have limitations concerning pressure and temperature, necessitating careful selection based on operational requirements.
- Potential for Leakage: Improper installation or wear and tear can lead to leakages, compromising safety and efficiency.
- Regular Inspection Requirements: Periodic inspections are crucial to identify wear and tear, requiring proactive maintenance efforts to prevent failures.
8. Codes & Standards for Hose Couplings
Codes & Standards for Hose Couplings
Organization | Standards |
---|---|
American Petroleum Institute (API) | API RP 1610, API Spec 7K |
American National Standards Institute (ANSI) | ANSI B16.5, ANSI B31.3 |
International Organization for Standardization (ISO) | ISO 7241-1, ISO 7241-2 |
Don’t miss the Complete Course on Piping Engineering: Check Now
Enrollment Link
The oil and gas industry adheres to stringent codes and standards to ensure the safety and reliability of equipment, including hose couplings. Organizations like the American Petroleum Institute (API), American National Standards Institute (ANSI), and International Organization for Standardization (ISO) have established guidelines governing the design, manufacturing, and usage of hose couplings. Compliance with these standards is essential to guarantee the quality and performance of couplings in diverse operational environments.
9. Conclusion
In conclusion, hose couplings stand as unsung heroes in the oil and gas industry, enabling the seamless flow of fluids that power the world. Their evolution from simple connectors to sophisticated, specialized components mirrors the industry’s growth. Understanding the nuances of hose couplings is not just a technical necessity but a strategic advantage. By choosing the right coupling for specific applications and adhering to industry standards, companies can enhance efficiency, ensure safety, and contribute to the sustainable progress of the oil and gas sector.
FAQs
1. What is the primary function of hose couplings in the oil and gas industry?
Hose couplings in the oil and gas industry serve the essential function of securely connecting hoses, enabling the transfer of various fluids such as oil, gas, and drilling fluids. These couplings ensure leak-proof and efficient fluid transfer, making them integral components in different stages of the industry’s operations.
2. How do I choose the right type of hose coupling for my specific application in the oil and gas sector?
Choosing the right hose coupling involves considering factors such as the type of fluid being transferred, operating pressure and temperature, environmental conditions, and safety requirements. It’s crucial to consult industry standards and work with experts who can assess your specific needs to recommend the most suitable type and material of hose coupling for your application.
3. What maintenance practices are essential to prolong the lifespan of hose couplings?
Regular maintenance is vital to ensure the longevity and optimal performance of hose couplings. This includes inspecting for signs of wear, corrosion, or damage, checking seals and gaskets for integrity, and lubricating moving parts if applicable. Additionally, following the manufacturer’s guidelines and scheduling routine inspections can help identify issues early, preventing costly failures.
4. What safety precautions should be taken when handling hose couplings in oil and gas operations?
Safety is paramount when handling hose couplings. Proper training of personnel involved in assembly, disassembly, and maintenance is crucial. Workers should wear appropriate personal protective equipment (PPE) such as gloves and safety goggles. Additionally, it’s essential to depressurize and properly secure hoses before attempting to connect or disconnect couplings to prevent accidents and injuries.
5. How do industry standards and regulations ensure the quality and reliability of hose couplings in the oil and gas sector?
Industry standards and regulations, set forth by organizations like API, ANSI, and ISO, establish guidelines for the design, manufacturing, and usage of hose couplings. Compliance with these standards ensures that couplings meet specific quality and performance criteria. Manufacturers often undergo rigorous testing processes to obtain certifications, providing users with confidence in the reliability and safety of the couplings they use in their operations.
Recommended courses (Published on EPCLand)
- Basics of Piping Engineering
- Piping Layout Engineering
- Piping Material Engineering
- Piping Stress Analysis
- Complete Course on Piping Engineering
- Material Requisitions
- Piping Material Specifications
- Valve Material Specifications
Don’t miss the published articles on following:
Don’t miss the Complete Course on Piping Engineering: Check Now
Enrollment Link
Attempt Quiz
Question 1:
What is the primary function of flexible hoses in the Oil & Gas Industry?
Explanation: Flexible hoses in the Oil & Gas Industry are used to connect rigid pipes and absorb vibration, allowing movement and flexibility in the system.
Question 2:
Which material is commonly used in the construction of flexible hoses for Oil & Gas applications?
Explanation: Stainless Steel is commonly used in the construction of flexible hoses for Oil & Gas applications due to its strength and corrosion resistance.
Question 3:
What is the purpose of corrugation in flexible hoses?
Explanation: Corrugation in flexible hoses enhances flexibility and allows movement, making them suitable for various applications in the Oil & Gas Industry.
Question 4:
What is the purpose of end fittings in flexible hoses?
Explanation: End fittings are used to connect flexible hoses to equipment or pipelines, ensuring a secure and leak-free connection in the Oil & Gas Industry.
Question 5:
What is the maximum temperature range flexible hoses in the Oil & Gas Industry are designed to handle?
Explanation: Flexible hoses in the Oil & Gas Industry are designed to handle a wide temperature range, typically from -40°C to 150°C, allowing them to be used in various operating conditions.
Question 6:
What type of fluids can flexible hoses in the Oil & Gas Industry transport?
Explanation: Flexible hoses in the Oil & Gas Industry are versatile and can transport a wide range of fluids, including oil, gas, and various chemicals.
Question 7:
What is the main advantage of using flexible hoses over rigid piping in the Oil & Gas Industry?
Explanation: The main advantage of using flexible hoses in the Oil & Gas Industry is easier installation and flexibility in movement, allowing for adaptability in various situations.
Question 8:
Which industry standard is commonly followed in the manufacturing of flexible hoses for Oil & Gas applications?
Explanation: API 17J is a commonly followed industry standard for the manufacturing of flexible hoses used in Oil & Gas applications.
Question 9:
What is the purpose of the outer protective layer in flexible hoses?
Explanation: The outer protective layer in flexible hoses protects against abrasion, chemicals, and weather, ensuring the hose’s durability and safety in various conditions.
Question 10:
What is the typical lifespan of high-quality flexible hoses in the Oil & Gas Industry?
Explanation: High-quality flexible hoses in the Oil & Gas Industry typically have a lifespan ranging from 15 to 20 years when properly maintained and used under appropriate conditions.