1. Introduction
In the realm of industrial fluid control, the Knife Edge Gate Valve stands as a testament to precision engineering. In today’s fast-paced industrial landscape, the ability to regulate and isolate the flow of various fluids is paramount. This article delves into the intricate world of Knife Edge Gate Valves, exploring their history, functioning, components, applications, and the standards that govern their manufacturing.
Table of Contents
Don’t miss the Complete Course on Piping Engineering: Check Now
Enrollment Link
2. Brief History
The history of the Knife Edge Gate Valve is a journey through time and innovation. Dating back to the early days of the industrial revolution, the need for efficient flow control became apparent. The first iterations were rudimentary, yet they paved the way for the sophisticated valves we see today. Early inventors tinkered with designs, aiming to create a valve capable of handling diverse fluids while ensuring minimal pressure drop.
One of the pioneering moments in the evolution of these valves was the development of a robust gate mechanism. This gate, with its distinctive knife-edge profile, became the hallmark of the Knife Edge Gate Valve. Over the years, advancements in materials and manufacturing techniques led to valves that could withstand corrosive environments and handle abrasive substances with finesse.
3. Basic Function and Working Principle
At its core, the Knife Edge Gate Valve operates on a simple yet effective principle. The valve comprises a body, gate, actuator, stem, and seating. When the valve is in the open position, the gate retracts into the body, allowing unobstructed fluid flow. Upon closure, the gate moves down, forming a tight seal with the seating, preventing any further flow.
The knife-edge design of the gate serves a crucial purpose. It enables the valve to cut through slurries, powders, and other viscous fluids, ensuring a secure seal even in challenging conditions. This design also minimizes the chances of clogging, making these valves ideal for applications involving suspended solids.
4. Main Components & Their Functions
Body: The body serves as the foundation of the valve, providing structural support and housing the gate and other components. It is designed to withstand varying pressure levels and fluid types, making it a critical part of the valve’s durability.
Gate: The gate, with its sharp knife-edge, is the heart of the Knife Edge Gate Valve. When open, it allows the fluid to flow freely. During closure, it descends to create a secure seal, preventing any leakage. The knife-edge design enables the valve to cut through substances, ensuring a reliable shut-off.
Actuator: The actuator is the muscle of the valve, responsible for moving the gate. Depending on the application, actuators can be manual, pneumatic, hydraulic, or electric. These actuators provide the necessary force to open or close the valve swiftly and precisely.
Stem: The stem connects the actuator to the gate, transmitting the actuating force. It ensures that the movement of the actuator is translated accurately to the gate, allowing for seamless operation.
Seating: Seating forms the sealing surface for the gate. It is engineered to create a tight seal when the valve is closed, preventing any leakage. The material and design of the seating are crucial factors in the valve’s performance, especially in demanding environments.
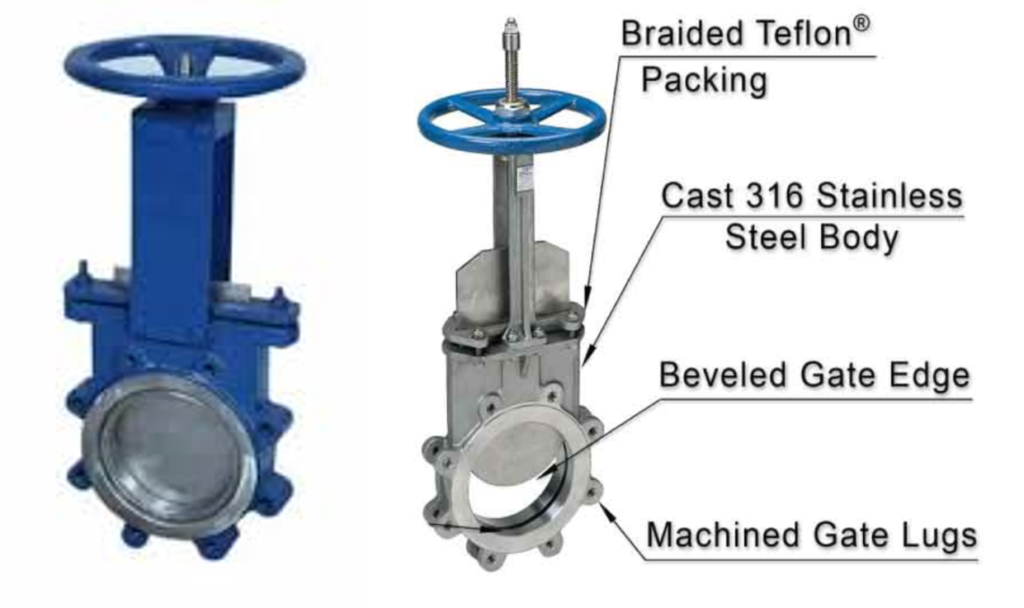
5. Applications of Knife Edge Gate Valve
The versatility of Knife Edge Gate Valves finds application across various industries, each with its unique fluid control challenges. In wastewater treatment plants, these valves are instrumental in handling sludge and abrasive media. Their ability to cut through solids ensures uninterrupted flow, making them indispensable in this sector.
In the mining industry, where abrasive materials are prevalent, Knife Edge Gate Valves shine. They effectively manage the flow of ores, slurries, and tailings, enhancing the overall efficiency of the extraction process. Moreover, these valves play a significant role in the pulp and paper industry, where they regulate the flow of pulp, chemicals, and paper stock with precision, contributing to the production of high-quality paper products.
Don’t miss the Complete Course on Piping Engineering: Check Now
Enrollment Link
6. Advantages & Disadvantages
Advantages:
Advantage | Description |
---|---|
Precise Flow Control | Knife Edge Gate Valves offer exceptional control over fluid flow, allowing operators to regulate the volume accurately. |
Minimal Pressure Drop | Due to their streamlined design, these valves incur minimal pressure drop, ensuring efficient flow without significant energy losses. |
Suitable for Abrasive Fluids | The knife-edge gate can cut through abrasive substances, making these valves ideal for applications involving slurries and powders. |
Low Maintenance Requirements | With fewer internal components, Knife Edge Gate Valves require minimal maintenance, reducing downtime and operational costs. |
Disadvantages:
Disadvantage | Description |
---|---|
Limited Use for High-Temperature and High-Pressure Applications | Knife Edge Gate Valves have limitations when it comes to handling extreme temperatures and pressures, making them unsuitable for specific industrial processes. |
Potential for Gate Wear and Erosion | In environments with highly abrasive media, the gate of the valve may experience wear and erosion over time, affecting its performance. |
7. Associated Codes & Standards
The manufacturing and implementation of Knife Edge Gate Valves are governed by industry-specific standards and codes. Adhering to these standards is paramount, ensuring the valves’ reliability, safety, and compatibility with various systems. Some of the key standards include:
Standard | Description |
---|---|
API 600 | Specifies requirements for steel gate valves suitable for petroleum and natural gas industries. |
MSS SP-81 | Covers dimensions and testing for Knife Gate Valves. |
ASME B16.34 | Provides standard specifications for valves, flanges, fittings, and gaskets used in pressure-containing service. |
ISO 9001:2015 | Defines the criteria for a quality management system, ensuring consistent quality and customer satisfaction. |
8. Conclusion
In conclusion, the Knife Edge Gate Valve stands as a marvel of engineering, catering to the intricate fluid control needs of diverse industries. Its evolution from rudimentary designs to the sophisticated valves we have today showcases the relentless pursuit of efficiency and precision in industrial processes.
The advantages of precise flow control, minimal pressure drop, and suitability for abrasive fluids make Knife Edge Gate Valves indispensable in applications where reliability is non-negotiable. However, like any technology, these valves have their limitations, particularly in extreme conditions. Understanding these limitations is key to making informed decisions about their implementation.
Furthermore, the adherence to industry standards and codes underscores the importance of quality and safety. Manufacturers and end-users alike must prioritize compliance with these standards, ensuring that Knife Edge Gate Valves meet stringent criteria for performance and durability.
As industries continue to evolve, so will the technology behind Knife Edge Gate Valves. With ongoing research and development, these valves are likely to become even more efficient, durable, and versatile, further revolutionizing the landscape of industrial fluid control.
FAQs
1. What distinguishes a Knife Edge Gate Valve from other types of valves?
A Knife Edge Gate Valve is specifically designed to handle fluids containing suspended solids, slurries, or powders. Its distinctive knife-edge gate allows it to cut through these materials, ensuring a secure shut-off and minimal clogging. This feature sets it apart from other valves, making it ideal for applications with abrasive media.
2. In which industries are Knife Edge Gate Valves commonly used?
Knife Edge Gate Valves find widespread use in industries dealing with challenging fluid conditions. They are commonly employed in wastewater treatment plants for sludge handling, mining operations for ore and tailings management, and the pulp and paper industry for regulating pulp flow. These valves are also utilized in chemical processing, power generation, and food processing industries.
3. What are the main considerations for selecting the right Knife Edge Gate Valve for a specific application?
Several factors need to be considered when selecting a Knife Edge Gate Valve, including the nature of the fluid (viscosity, temperature, and chemical composition), operating pressure and temperature, required flow rate, and the presence of abrasive particles. Additionally, factors such as the valve material, actuation method (manual, pneumatic, electric), and compliance with industry standards play a crucial role in the selection process.
4. How can maintenance challenges associated with Knife Edge Gate Valves be mitigated?
While Knife Edge Gate Valves are known for their low maintenance requirements, regular inspection and preventive maintenance are essential to ensure their optimal performance. Proper lubrication of moving parts, periodic checks for wear and erosion, and timely replacement of worn-out components can significantly extend the valve’s lifespan. Additionally, following the manufacturer’s maintenance guidelines and conducting routine tests can help mitigate potential issues.
5. Are Knife Edge Gate Valves suitable for high-pressure and high-temperature applications?
Knife Edge Gate Valves have limitations when it comes to handling extremely high pressures and temperatures. For applications involving high-pressure fluids or elevated temperatures, it’s crucial to consult with valve experts or engineers to select an appropriate valve design and material that can withstand the specific operating conditions. In cases where both high pressure and high temperature are present, alternative valve types designed for such conditions might be more suitable.
Don’t miss the Complete Course on Piping Engineering: Check Now
Enrollment Link
Recommended courses (Published on EPCLand)
- Basics of Piping Engineering
- Piping Layout Engineering
- Piping Material Engineering
- Piping Stress Analysis
- Complete Course on Piping Engineering
- Material Requisitions
- Piping Material Specifications
- Valve Material Specifications
Don’t miss the published articles on following:
Attempt Quiz
Question 1:
What is the primary function of a Knife Edge Gate Valve?
Explanation: Knife Edge Gate Valves are specifically designed to cut and isolate the flow of abrasive slurries, powders, and viscous fluids.
Question 2:
Which industry commonly uses Knife Edge Gate Valves?
Explanation: Knife Edge Gate Valves are commonly used in industries such as Mining and Mineral Processing.
Question 3:
What material is often used for the knife gate in Knife Edge Gate Valves?
Explanation: Stainless Steel is often used for the knife gate in Knife Edge Gate Valves due to its durability and resistance to corrosion.
Question 4:
What is the typical operation of a Knife Edge Gate Valve?
Explanation: Knife Edge Gate Valves typically operate with linear motion, moving the gate up and down to cut off or allow the flow.
Question 5:
What is the advantage of a full-port Knife Edge Gate Valve?
Explanation: A full-port Knife Edge Gate Valve offers the advantage of minimized pressure drop, allowing efficient fluid flow.
Question 6:
Which type of fluids are Knife Edge Gate Valves especially suitable for?
Explanation: Knife Edge Gate Valves are especially suitable for high-viscosity fluids and solids due to their ability to cut through and isolate such materials.
Question 7:
What is the purpose of the resilient seat in a Knife Edge Gate Valve?
Explanation: The resilient seat in a Knife Edge Gate Valve provides cushioning and ensures tight shut-off when the valve is closed.
Question 8:
What is the main advantage of the uni-directional Knife Edge Gate Valve?
Explanation: The main advantage of the uni-directional Knife Edge Gate Valve is that it allows flow in one direction only, providing effective flow control.
Question 9:
What is the typical range of sizes for Knife Edge Gate Valves?
Explanation: Knife Edge Gate Valves are typically available in sizes ranging from 2 inches to 8 inches for various industrial applications.
Question 10:
What is the advantage of the rising stem design in Knife Edge Gate Valves?
Explanation: The rising stem design in Knife Edge Gate Valves allows visual indication of the valve position, aiding in easy monitoring and control.