The oil and gas industry is a cornerstone of modern civilization, providing the energy and raw materials needed for a vast array of processes, from powering our vehicles to heating our homes. Key to this industry are the complex networks of pipes that transport oil and gas from production facilities to end-users. In this article, we’ll delve into the world of pipes used in oil and gas projects, exploring their history, functions, working principles, types, applications, advantages, disadvantages, and associated codes and standards.
Table of Contents
Don’t miss the Complete Course on Piping Engineering: Check Now
Enrollment Link
I. Introduction
The use of pipes in the oil and gas industry is nothing short of essential. They form the arteries through which vital resources flow, connecting drilling sites, refineries, and distribution centers. These pipes are designed to withstand extreme conditions and deliver these valuable resources safely and efficiently. The engineering and design of these pipelines have come a long way, and they continue to evolve with new technologies and materials.
II. Brief History
The history of pipes in the oil and gas industry can be traced back to the early days of the industry itself. In the 19th century, the discovery of oil and natural gas prompted the development of pipelines for their transportation. Initially, these pipelines were simple and made of materials like wood, but they were soon replaced by more durable materials like iron and steel.
As the industry expanded, so did the need for more sophisticated pipelines. The advent of welding techniques and the use of corrosion-resistant alloys revolutionized pipeline construction. In recent decades, innovations such as composite materials and advanced coatings have further improved pipeline durability and longevity.
III. Basic Function and Working Principle
Pipes in the oil and gas industry serve a basic yet crucial function: they transport hydrocarbons from production sites to processing and distribution facilities. These pipelines can cover vast distances, often crossing challenging terrains and bodies of water. The working principle of these pipes is relatively straightforward, with the primary goal being the safe and efficient transport of fluids.
Pipelines work on the principle of fluid flow driven by pressure differentials. Pumping stations are strategically placed along the pipeline to maintain the required pressure, ensuring that the oil or gas flows steadily to its destination. These pipelines may also incorporate safety features such as pressure relief valves and emergency shutdown systems.
IV. Types of Pipes
Pipes used in the oil and gas industry come in various types, each designed for specific purposes and operating conditions. The choice of pipe type is influenced by factors like the type of hydrocarbons being transported, pressure, temperature, and environmental conditions. Common types of pipes include:
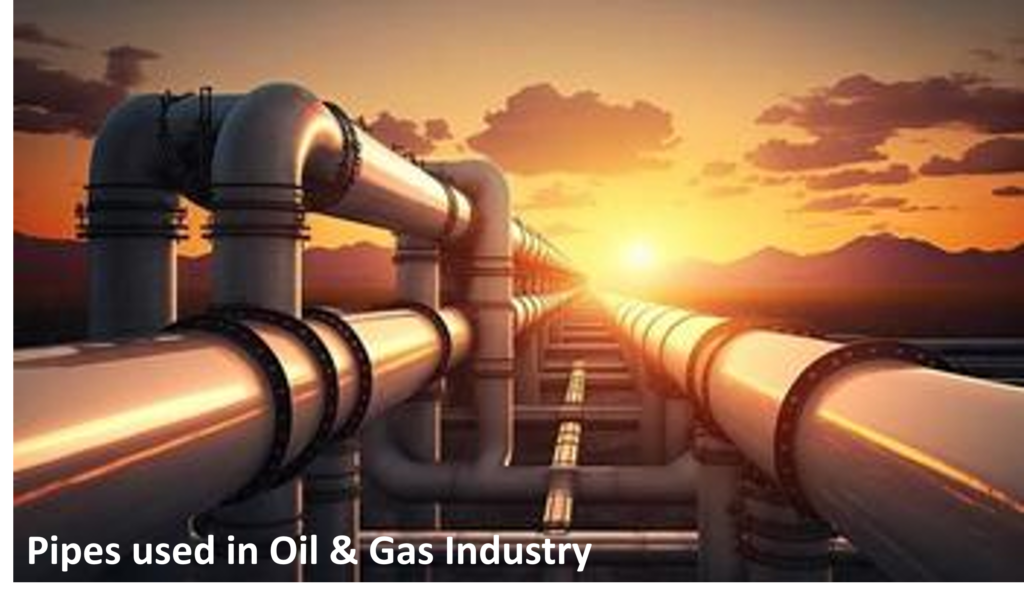
1. Steel Pipes
Description: Steel pipes are the workhorses of the oil and gas industry. They are renowned for their strength, durability, and versatility. Steel pipes are the go-to choice for high-pressure and high-temperature applications.
Advantages:
- Strength: Steel pipes can withstand immense pressure and are resistant to deformation.
- Durability: They have a long service life and can endure harsh conditions.
- Versatility: Steel pipes are suitable for both onshore and offshore applications.
- Corrosion Resistance: With proper coatings, they can be made corrosion-resistant.
Disadvantages:
- Cost: Steel pipes can be more expensive than some alternative materials.
- Weight: They are heavier than plastic or composite pipes, which can complicate transportation and installation.
2. Carbon Steel Pipes
Description: Carbon steel pipes are a subset of steel pipes known for their carbon content. These pipes are ideal for both onshore and offshore projects, where they are used for transporting crude oil, natural gas, and other hydrocarbons.
Advantages:
- Cost-Effective: Carbon steel pipes are relatively affordable.
- Resistance to Corrosion: Their natural composition provides good corrosion resistance.
- Strength: They can withstand high pressure and temperature conditions.
Disadvantages:
- Susceptible to Corrosion: Without proper coatings, carbon steel pipes can corrode.
- Maintenance: They require regular maintenance to prevent corrosion.
3. Stainless Steel Pipes
Description: Stainless steel pipes are the choice when corrosion resistance is critical. They are often used in transporting corrosive substances and in environments where traditional steel might corrode.
Advantages:
- Corrosion Resistance: Stainless steel pipes are highly resistant to corrosion.
- Longevity: They have a long service life and require minimal maintenance.
- Strength: They can handle high-pressure and high-temperature conditions.
Disadvantages:
- Cost: Stainless steel pipes can be more expensive than carbon steel.
- Environmental Impact: Manufacturing stainless steel can be more energy-intensive than other materials.
4. Ductile Iron Pipes
Description: Ductile iron pipes are commonly used in lower-pressure applications, such as water injection systems in the oil and gas industry. They are valued for their flexibility and ease of installation.
Advantages:
- Flexibility: Ductile iron pipes can withstand minor bending and flexing.
- Easy Installation: They are relatively easy to install compared to steel pipes.
- Resistance to Fracture: They are less prone to fracturing compared to traditional cast iron pipes.
Disadvantages:
- Limited Pressure and Temperature: Ductile iron pipes are not suitable for high-pressure or high-temperature applications.
- Corrosion Vulnerability: Without proper coatings, they can be susceptible to corrosion.
5. Plastic Pipes
Description: Plastic pipes, such as polyethylene and PVC, are lightweight and often used in low-pressure and lower-temperature applications. They are commonly employed in gas distribution systems.
Advantages:
- Lightweight: Plastic pipes are easy to transport and install.
- Corrosion Resistance: They are naturally corrosion-resistant.
- Low Cost: They are generally cost-effective.
Disadvantages:
- Limited Strength: Plastic pipes cannot withstand high pressures or temperatures.
- Environmental Impact: Some plastic materials can have environmental concerns, especially when not disposed of properly.
6. Composite Pipes
Description: Composite pipes are a blend of different materials, designed for specific applications. They aim to harness the advantages of each material used in their construction.
Advantages:
- Balanced Properties: Composite pipes combine materials to achieve a balance between strength, corrosion resistance, and weight.
- Specialized Use: They are ideal for specialized applications, such as offshore projects.
- Customizable: The composition can be tailored to meet specific project needs.
Disadvantages:
- Complex Manufacturing: The production of composite pipes can be more intricate than single-material pipes.
- Cost: Customization and the use of multiple materials can make composite pipes relatively expensive.
Don’t miss the Complete Course on Piping Engineering: Check Now
Enrollment Link
V. Applications of Pipes in the Oil & Gas Industry
Pipes play a crucial role in various facets of the oil and gas industry. Their applications are diverse, and they are used in different phases of hydrocarbon production, processing, and distribution. Here are some key applications:
1. Exploration and Drilling
In the upstream sector of the oil and gas industry, pipes are essential for drilling and wellbore construction. These pipes are referred to as drill pipes, and they serve several important purposes:
- Conduit for Drilling Fluids: Drill pipes are used to deliver drilling fluids to the drilling bit, ensuring efficient drilling operations. These fluids help cool the drill bit, lift cuttings to the surface, and stabilize the wellbore.
- Transmitting Torque: Drill pipes transmit torque from the surface to the drilling bit, allowing for the rotation and penetration of the wellbore.
- Protection of the Drill String: Drill pipes protect the drilling assembly, which includes the drill bit, from damage and corrosion as it moves through different geological formations.
- Transport of Core Samples: In certain drilling operations, drill pipes are used to transport core samples from the wellbore to the surface for analysis.
2. Transport
One of the most prominent and crucial applications of pipes in the oil and gas industry is the transportation of crude oil and natural gas from production facilities to refineries and distribution centers. These pipelines often span vast distances, connecting production sites in remote locations to urban areas. Key aspects of this application include:
- Crossing Diverse Terrains: Oil and gas pipelines can traverse various terrains, including deserts, mountains, and bodies of water. Specialized engineering techniques and materials are employed to overcome these challenges.
- Compressor and Pump Stations: Along the pipeline route, compressor and pump stations are strategically placed to maintain the necessary pressure for efficient transportation. These stations play a critical role in ensuring the flow of hydrocarbons over long distances.
- Interconnectivity: The pipeline network in the oil and gas industry is extensive, with various pipelines interconnected to transport different grades of oil and gas and to serve different regions.
3. Refining
Pipes are vital components within refineries, where they are used to transport various petroleum products between different processing units. The applications within a refinery are diverse, and pipes are designed to handle a wide range of temperatures and chemical compositions. Some specific applications include:
- Feedstock Transportation: Pipes carry raw crude oil from storage tanks to the refining units, where it undergoes various processes such as distillation, cracking, and reforming.
- Product Distribution: After refining, pipes are employed to distribute the different petroleum products, including gasoline, diesel, jet fuel, and petrochemical feedstocks, to storage tanks and terminals for subsequent distribution.
- Heat Exchangers: Pipes are integral to heat exchangers, which play a role in the refining process by transferring heat between process streams.
- Instrumentation and Control Lines: Small-diameter pipes, often referred to as tubing, are used for instrument lines and control systems throughout the refinery to monitor and control various processes.
4. Distribution
Once refined, petroleum products are transported from refineries to end-users through distribution pipelines. These pipelines connect to storage tanks and terminals before reaching the consumer, and their functions include:
- Storage Tank Connections: Distribution pipelines are connected to storage tanks where petroleum products are held until they are ready for transportation to consumers.
- Terminal Connections: Distribution pipelines are also connected to terminals where bulk loading and unloading of products occur.
- Local and Regional Distribution: These pipelines distribute products to local markets, industrial facilities, and regional distribution centers.
- Gas Distribution: In addition to liquid petroleum products, pipelines are used to distribute natural gas to residential, commercial, and industrial customers. Gas distribution pipelines are a crucial part of natural gas utility systems.
5. Offshore
In the offshore oil and gas sector, specialized pipelines are used to transport oil and gas from beneath the seabed to the surface. These subsea pipelines are engineered to withstand harsh ocean conditions and unique challenges:
- Subsea Production Systems: Subsea pipelines are an integral part of subsea production systems, connecting underwater wellheads to production platforms or floating production, storage, and offloading (FPSO) vessels.
- Corrosion Resistance: Subsea pipelines are constructed with materials that resist corrosion from saltwater and provide long-term durability in a harsh marine environment.
- Maintenance and Inspection: The maintenance of subsea pipelines often involves remotely operated vehicles (ROVs) and underwater inspection techniques to ensure their integrity.
- Deepwater and Ultra-Deepwater Pipelines: Offshore pipelines are used in various water depths, from shallow to ultra-deepwater, depending on the location of oil and gas reserves.
These applications of pipes in the oil and gas industry underscore their multifaceted role in ensuring the reliable and efficient transportation of hydrocarbons from their sources to consumers, while also addressing the challenges associated with different operating environments and conditions. Moreover, these applications highlight the importance of maintaining the integrity of pipelines to prevent leaks and ensure the safety and sustainability of the oil and gas infrastructure.
VI. Advantages & Disadvantages
The use of pipes in the oil and gas industry brings both advantages and disadvantages. Understanding these factors is essential for making informed decisions about pipeline design and maintenance.
Advantages of Using Pipes in Oil & Gas Projects
Advantage | Explanation |
---|---|
Efficient Transport | Pipes enable the efficient and continuous flow of hydrocarbons, reducing the need for other forms of transportation. |
Environmental Impact | Pipelines can be more environmentally friendly than other modes of transport, such as shipping or trucking. |
Cost-Effective | Pipelines are often a cost-effective means of transportation over long distances. |
Safety and Reliability | Properly designed and maintained pipelines are known for their safety and reliability in transporting hazardous materials. |
Longevity | High-quality pipelines can have a long service life, providing a sustainable means of transportation. |
Disadvantages of Using Pipes in Oil & Gas Projects
Disadvantage | Explanation |
---|---|
Initial Investment | The construction of pipelines requires a significant upfront investment in materials and infrastructure. |
Maintenance Costs | Pipelines require regular maintenance to prevent leaks, corrosion, and other issues, incurring ongoing costs. |
Environmental Concerns | Pipeline spills and leaks can have a significant environmental impact, leading to public and regulatory scrutiny. |
Limited Flexibility | Once a pipeline is in place, it is challenging to adapt to changing transportation needs or routes. |
Regulatory Challenges | Pipelines are subject to stringent regulations, and obtaining permits and complying with standards can be complex. |
VII. Associated Codes & Standards
To ensure the safe and efficient operation of pipelines in the oil and gas industry, various codes and standards have been established. These standards dictate everything from the materials used in construction to safety features and inspection protocols. Compliance with these regulations is paramount to prevent accidents and environmental damage.
1. API Standards
- The American Petroleum Institute (API) is a primary source of standards and guidelines for the oil and gas industry. API standards cover various aspects of pipeline design, construction, and maintenance.
2. ASME B31 Codes
- The American Society of Mechanical Engineers (ASME) issues the B31 series of codes, which provide guidelines for pressure piping, including those used in the oil and gas industry.
3. International Standards
- Depending on the location and international agreements, pipelines may need to adhere to specific international standards and regulations, such as those set by the ISO (International Organization for Standardization).
4. National Regulations
- Each country may have its own set of regulations governing pipeline construction and operation. These regulations may vary in terms of safety requirements and environmental standards.
VIII. Conclusion
In conclusion, pipes are the unsung heroes of the oil and gas industry, enabling the safe and efficient transportation of vital resources. They have come a long way from their humble beginnings, evolving in material, design, and application. As the industry continues to grow and innovate, pipes will remain an indispensable component of the global energy infrastructure. It is essential to recognize their advantages and disadvantages, and to adhere to strict codes and standards to ensure the safety and sustainability of our pipelines.
In the coming years, we can expect further advancements in pipeline technology, with a focus on enhancing safety, environmental responsibility, and the longevity of these crucial conduits. As we move towards a more sustainable and efficient energy future, the role of pipes in the oil and gas industry will continue to be pivotal.
FAQs
1. Why are steel pipes commonly used in the oil and gas industry?
- Steel pipes are preferred due to their high strength and durability, which is essential for transporting oil and gas at high pressures and temperatures. They also offer resistance to corrosion, making them suitable for the harsh conditions of the industry.
2. What are the environmental concerns associated with pipelines in the oil and gas sector?
- Pipelines can pose environmental risks, primarily due to potential leaks or spills. These incidents can harm ecosystems, contaminate water sources, and have long-term environmental consequences. Pipeline safety and preventive measures are crucial to mitigate these concerns.
3. How do regulations and standards differ for pipelines in different countries?
- Regulations and standards for pipelines can vary significantly from one country to another. Each nation may have its own set of requirements, safety standards, and environmental regulations that pipelines must adhere to. International pipelines may need to meet multiple sets of standards to ensure compliance.
4. What role do composite pipes play in the oil and gas industry, and where are they typically used?
- Composite pipes combine different materials to leverage their unique strengths. They are often used in offshore projects, where they need to withstand both the corrosive marine environment and the high pressures of deep-sea drilling.
5. How are pipelines inspected and maintained to ensure their safety and integrity?
- Pipelines undergo regular inspections using techniques such as smart pigs (pipeline inspection gauges) and ultrasonic testing. Maintenance includes activities like cleaning, corrosion protection, and repairing any damaged sections to ensure safe and efficient operation.
Don’t miss the Complete Course on Piping Engineering: Check Now
Enrollment Link
Recommended courses (Published on EPCLand)
- Complete Course on Piping Engineering
- Basics of Piping Engineering
- Piping Layout Engineering
- Piping Material Engineering
- Piping Stress Analysis
- Material Requisitions
- Piping Material Specifications
- Valve Material Specifications
- Plant Design & Layouts-OISD 118
- Isometric Management
Library of Technical Articles
Don’t miss out the collection of 15+ articles on following topics:
- Basics of Oil and Gas Industry
- Valves
- Testing
- Tank
- Piping Bulk Items
- Pipe
- Metallurgy
- Piping Materials
- Layout
- Instrumentation
- Heat Exchanger
- Type of Contracts
- Codes and Standards
- ASTM Standards
- Articles on Piping Specialty Items
Video details of Complete Course on Piping Engineering
Attempt Quiz
Question 1:
What is the primary purpose of pipes in the Oil & Gas Industry?
Explanation: The primary purpose of pipes in the Oil & Gas Industry is to transport oil and gas fluids.
Question 2:
Which material is commonly used for constructing pipes in the Oil & Gas Industry?
Explanation: Steel is commonly used for constructing pipes in the Oil & Gas Industry due to its strength and durability.
Question 3:
What is the purpose of pipeline coatings in the Oil & Gas Industry?
Explanation: Pipeline coatings are used to protect pipes from corrosion and external factors in the Oil & Gas Industry.
Question 4:
What is the primary function of flanges in pipeline systems?
Explanation: Flanges in pipeline systems are used to connect and secure pipe sections in the Oil & Gas Industry.
Question 5:
Which type of pipeline is used to transport natural gas over long distances?
Explanation: Transmission pipelines are used to transport natural gas over long distances in the Oil & Gas Industry.
Question 6:
What is the typical diameter range of pipes used in the Oil & Gas Industry?
Explanation: Pipes used in the Oil & Gas Industry can have a typical diameter range of 10-48 inches, depending on the specific application.
Question 7:
Which method is commonly used to transport oil and gas through pipelines?
Explanation: Pumping is commonly used to transport oil and gas through pipelines in the Oil & Gas Industry.
Question 8:
What is the primary factor affecting the thickness of pipeline walls?
Explanation: The primary factor affecting the thickness of pipeline walls is the operating pressure and the contents they carry.
Question 9:
What is the function of a pig in pipeline maintenance?
Explanation: Pigs in pipeline maintenance are used to inspect, clean, or separate pipelines as needed.
Question 10:
What is the typical color coding for pipes used in natural gas transmission?
Explanation: Pipes used in natural gas transmission are typically color-coded in yellow.