1. Proximity to Associated Equipment while Fixing Location of Heat Exchangers
Fixing Location of Heat Exchangers concerning major equipment they are associated with?
Explanation: Heat exchangers should be placed close to major equipment they are associated with, enhancing operational efficiency and minimizing piping runs.
2. Optimal Placement Between Distant Equipment
What is the recommended consideration when locating heat exchangers connecting two distant process units?
Explanation: Heat exchangers connecting distant process units should be located at optimal points in relation to piperacks to minimize piping runs.
3. Grade-Level Placement
What is the recommended position for most heat exchangers concerning elevation?
Explanation: Most heat exchangers should be positioned at grade level, ensuring a minimum clearance of 1 meter above Finished Ground Level (FGL).
4. Elevated Exchangers for NPSH Requirements
Under what conditions should heat exchangers be elevated?
Explanation: Heat exchangers should be elevated to meet the NPSH (Net Positive Suction Head) requirement of downstream centrifugal pumps when necessary.
5. Grouping Heat Exchangers
What is the purpose of grouping heat exchangers into categories?
Explanation: Grouping heat exchangers into categories helps save on piping, structural work, lifting, and maintenance facilities, as well as platform requirements.
6. Spacing Between Paired or Grouped Exchangers
What is the recommended minimum spacing between the outside of adjacent channel or bonnet flanges on paired or grouped exchangers?
Explanation: The recommended minimum spacing between the outside of adjacent channel or bonnet flanges on paired or grouped exchangers is 450mm, preferably 600mm.
7. Adequate Access for Control and Operator Maintenance
Why is it important to provide adequate space on either side of paired exchangers and at both ends of grouped exchangers?
Explanation: Providing adequate space on either side of paired exchangers and at both ends of grouped exchangers is essential for control and operator access during maintenance.
Short Article on Fixing Location of Heat Exchangers
Location Considerations for Heat Exchangers
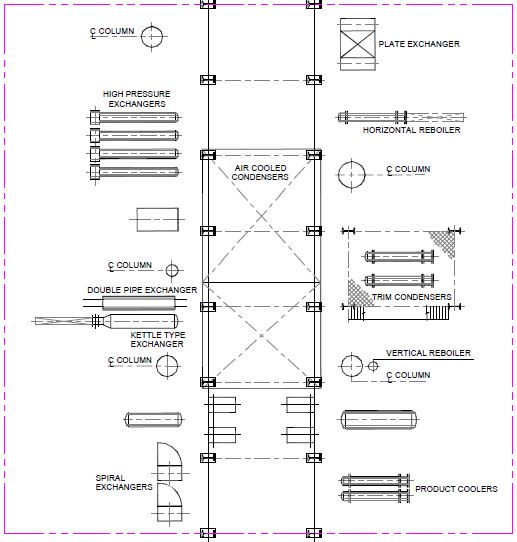
- Proximity to associated equipment: Place heat exchangers close to the major equipment they are associated with, such as reboilers near their respective towers and condensers over reflux drums.
- Optimal placement between distant equipment: For heat exchangers connecting two distant process units, locate them at optimal points in relation to piperacks to minimize piping runs.
- Grade-level placement: Position most exchangers at grade level, ensuring a minimum clearance of 1 meter above Finished Ground Level (FGL).
- Elevated exchangers for NPSH requirements: When necessary, elevate heat exchangers to meet the NPSH (Net Positive Suction Head) requirement of downstream centrifugal pumps.
- Grouping heat exchangers: Group heat exchangers into categories to save on piping, structural work, lifting and maintenance facilities, and platform requirements.
- Spacing between paired or grouped exchangers: Maintain a minimum spacing of 450mm, preferably 600mm, between the outside of adjacent channel or bonnet flanges on paired or grouped exchangers to facilitate access during maintenance.
- Adequate access for control and operator maintenance: Provide adequate space on either side of paired exchangers and at both ends of grouped exchangers for control and operator access.
- Aligning channel nozzles in vertical planes: When grouping heat exchangers, align channel nozzles vertically to create an aesthetically pleasing arrangement.
- Support saddle location for thermal expansion: Position the support saddle with oblong holes for thermal expansion on the saddle farthest from the channel end. The final location may vary depending on plant layout and connected piping stress analysis.
- Direct and simple piping: Design exchanger piping as direct and simple as possible. Consider alternatives like arranging exchangers side-by-side or stacking them for reversing flows.
- Mounting on structures or equipment: When mounting heat exchangers on structures, process columns, or other equipment, provide special arrangements for maintenance and tube cleaning.
Table of Contents
Don’t miss the Course on Effective Isometrics Management: Check Now
Enrollment Link
Recommended courses (Published on EPCLand)
- Complete Course on Piping Engineering
- Basics of Piping Engineering
- Piping Layout Engineering
- Piping Material Engineering
- Piping Stress Analysis
- Material Requisitions
- Piping Material Specifications
- Valve Material Specifications
- Plant Design & Layouts-OISD 118
- Isometric Management
Library of Technical Articles
Don’t miss out the collection of 15+ articles on following topics:
- Basics of Oil and Gas Industry
- Valves
- Testing
- Tank
- Piping Bulk Items
- Pipe
- Metallurgy
- Piping Materials
- Layout
- Instrumentation
- Heat Exchanger
- Type of Contracts
- Codes and Standards
- ASTM Standards
- Articles on Piping Specialty Items
Video details of Complete Course on Piping Engineering
Why Enroll in the EPCLand
Proven Track Record– PTR
Activities & Achievements before launching EPCLand
- Published more than 50+ short courses
- 3000+ Enrolments
- More than 3,500,00 Minutes of watch hours in the last 2 years
- 4000+ Students in 100+ Countries
- Rating of 4+ out of 5
- 1000+ YouTube Videos
- 8K+ Subscribers
What Students will Learn
- Codes & Standards of the Energy Sector
- Piping Material Engineering
- Piping Layout Engineering
- Stress Analysis
Interesting facts
- All the published courses have been developed by Industry Experts with more than 2 decades of experience
- Content is based on Practical experience and real-time problems.
- Content is designed and organized in such a manner that it can be easily grabbed.
- Complete website, Blogs and Quiz sections are Planned, Designed and published by myself (About me: Atul Singla)
- Complete flexibility of Time & Location, Students can access the content from anywhere & anytime
- Moreover, once enrolled, the content can be access as many times as you want, which helps in understand the fundamentals in a better way.
Conclusion
In conclusion, our courses are meticulously crafted by industry experts with over two decades of hands-on experience. The content is rooted in practical knowledge, addressing real-time problems. The material is thoughtfully designed and organized for easy comprehension. Every aspect, from the website to blogs and quizzes, has been planned, designed, and executed by Atul Singla, ensuring a comprehensive and seamless learning experience. With the flexibility of accessing the content at any time and from any location, students have the freedom to learn on their terms. Furthermore, enrollment grants unlimited access, allowing learners to revisit the material as often as needed, fostering a deep understanding of the fundamentals.