1. Introduction
In the intricate tapestry of the oil and gas industry, efficient steam management is paramount. Steam traps, often overlooked heroes in industrial settings, play a pivotal role in optimizing energy usage, ensuring safety, and enhancing productivity. Steam traps are indispensable devices designed to discharge condensate and non-condensable gases, ensuring the integrity and efficiency of steam systems. In this article, we delve into the depths of steam traps, exploring their history, intricate workings, types, applications, and the standards governing their usage.
Table of Contents
Don’t miss the Complete Course on Piping Engineering: Check Now
Enrollment Link
2. Brief History
Steam traps, humble yet vital, have a history that mirrors the industrial evolution. The first steam traps, rudimentary in design, emerged in the early 19th century alongside the steam engine. As industries burgeoned during the Industrial Revolution, the need for efficient steam utilization became evident. Inventors and engineers tirelessly worked to refine steam trap designs. In the late 19th century, the first mechanical steam traps made their appearance, heralding a new era of steam management. With time, thermodynamic and thermostatic steam traps were developed, each catering to specific industrial needs. Today, steam traps stand as a testament to human ingenuity and engineering excellence.
3. Basic Function and Working Principle
Steam traps operate on a deceptively simple principle yet have a profound impact on industrial processes. At their core, steam traps are automatic valves that release condensate and non-condensable gases from steam systems while preventing the escape of steam. The primary function of a steam trap is to conserve energy by recovering and reusing the latent heat of condensation. When steam loses its heat and condenses into water, a steam trap ensures the removal of this condensate, maintaining optimal steam quality. Mechanical steam traps employ floats and thermostatic elements, whereas thermodynamic traps rely on the fluid dynamics of steam and water to function. Thermostatic traps, sensitive to temperature changes, provide precise control over the discharge process.
4. Main Components & Their Functions
Steam traps used in the oil and gas industry consist of several essential components, each with specific functions crucial to the efficient operation of industrial processes.
1. Valve Mechanism: The valve mechanism is the heart of any steam trap. It controls the flow of steam and condensate within the system. There are various types of valve mechanisms, including float-operated, thermostatic, and thermodynamic. Float-operated traps use a float to open and close the valve based on the condensate level. Thermostatic traps use temperature-sensitive elements to modulate the valve, responding to the changes in temperature caused by condensate or steam. Thermodynamic traps use the dynamic effect of steam flow to open and close the valve. The choice of valve mechanism depends on the specific application and the characteristics of the steam system.
2. Control Devices: Control devices are responsible for regulating the operation of the steam trap. These devices ensure that the trap functions optimally under varying load and pressure conditions. Bimetallic elements, for instance, bend in response to temperature changes, allowing precise control of the trap’s valve. Expansion valves, another type of control device, modulate the trap’s operation based on the expansion and contraction of a material, typically wax, in response to temperature variations. By incorporating these control devices, steam traps can adapt to different operating conditions, making them versatile and reliable components in oil and gas facilities.
3. Discharge Orifice: The discharge orifice is a carefully designed opening through which the condensate is expelled from the steam trap. It plays a crucial role in maintaining the balance between discharging condensate and retaining steam within the system. Proper sizing of the discharge orifice is essential to prevent steam loss and ensure efficient condensate removal. The size of the orifice is determined by factors such as condensate load, system pressure, and the specific application requirements. By maintaining the correct balance, the discharge orifice ensures that only condensate is expelled, allowing steam to continue its journey through the industrial process without unnecessary wastage.
4. Body and Casing: The body and casing of a steam trap provide structural support and protection to the internal components. They are designed to withstand high pressures and temperatures prevalent in oil and gas applications. Additionally, the material of the body and casing is chosen to resist corrosion, ensuring the longevity of the steam trap. These components also house the valve mechanism, control devices, and discharge orifice, creating a sealed environment that prevents steam leakage and enhances the overall efficiency of the steam trap system.
In summary, the valve mechanism, control devices, discharge orifice, and the body/casing form the core components of steam traps in the oil and gas industry. Their synergy allows steam traps to efficiently remove condensate, prevent steam loss, adapt to changing operating conditions, and maintain the integrity of industrial processes. Understanding the functions of these components is essential for selecting, installing, and maintaining steam traps, ensuring the seamless operation of oil and gas facilities.
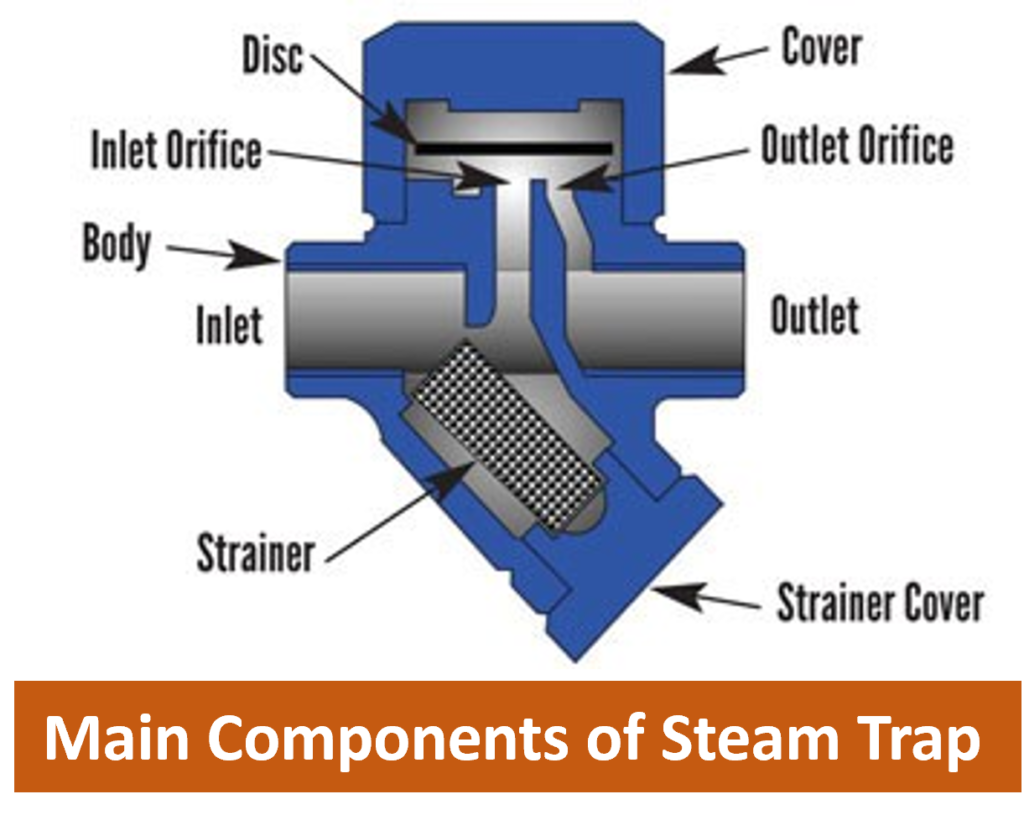
5. Types of Steam Traps
Steam traps come in various types, each tailored to specific applications and operating conditions. Mechanical steam traps, the simplest in design, utilize floats to open and close the valve. Thermodynamic steam traps employ the dynamic properties of steam and water to function, making them suitable for high-pressure applications. Thermostatic steam traps, sensitive to temperature changes, are ideal for low-load conditions. Selecting the appropriate type of steam trap is crucial, as it directly impacts the efficiency and longevity of industrial processes. Proper selection ensures optimal condensate removal and prevents steam wastage, leading to significant energy savings.
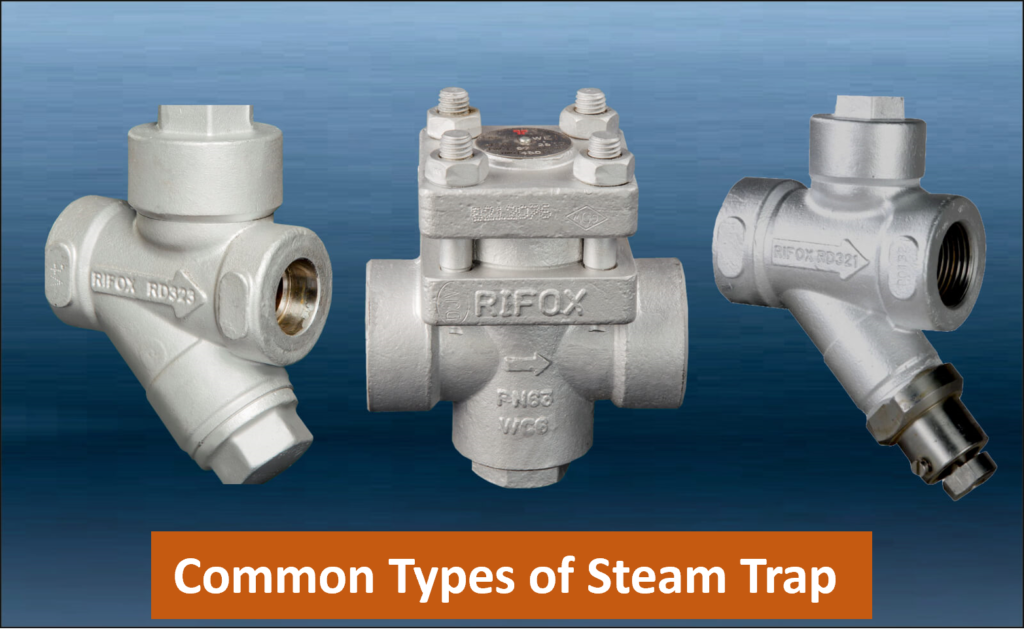
Don’t miss the Complete Course on Piping Engineering: Check Now
Enrollment Link
6. Applications of Steam Traps in Oil & Gas Industry
Steam Traps in Oil Refineries
In oil refineries, steam traps are deployed in various units, including distillation columns, heat exchangers, and reactors. By efficiently removing condensate, steam traps maintain the desired temperature and pressure, ensuring the smooth operation of refining processes. Properly functioning steam traps also prevent water hammer, a phenomenon that can cause significant damage to pipelines and equipment.
Steam Traps in Gas Processing Plants
Gas processing plants rely on steam traps to maintain the temperature of natural gas and its by-products. Condensate removal is crucial to prevent the formation of hydrates and ensure the quality of processed gases. Steam traps in these plants are strategically placed in dehydration units, compressors, and fractionation columns to enhance operational efficiency and minimize downtime.
Steam Traps in Petrochemical Manufacturing
Petrochemical manufacturing involves complex processes that demand precise temperature control. Steam traps play a vital role in maintaining optimal conditions within reactors, distillation units, and heat exchangers. By removing condensate promptly, steam traps prevent heat loss and enable the production of high-quality chemicals and polymers.
7. Advantages and Disadvantages
Advantages:
Advantages | Description |
Energy Conservation | Efficient condensate removal conserves energy, reducing fuel consumption and operational costs. |
Equipment Longevity | Proper steam trapping prevents water hammer and corrosion, extending the lifespan of equipment and pipes. |
Environmental Sustainability | Reduced steam wastage contributes to environmental conservation by lowering greenhouse gas emissions. |
Enhanced Productivity | Maintaining optimal steam quality ensures consistent process temperatures, enhancing overall productivity. |
Operational Cost Savings | Energy savings and reduced maintenance costs translate to significant operational cost reductions. |
Disadvantages:
Disadvantages | Description |
Initial Investment | High-quality steam traps may have a significant upfront cost, although they offer long-term savings. |
Maintenance Complexity | Improper maintenance can lead to steam leakage or blockages, necessitating skilled personnel. |
Compatibility Issues | Selecting the wrong steam trap type for specific applications can lead to inefficiencies. |
Limited Efficiency Under Load | Certain steam traps may have limitations under low-load conditions, affecting their efficiency. |
Risk of Steam Loss | Malfunctioning traps can lead to steam wastage, impacting both energy efficiency and operational costs. |
8. Codes and Standards
The usage of steam traps in the oil and gas industry is governed by stringent codes and standards to ensure safety, efficiency, and compliance. Industry-specific standards, such as API 526 for pressure relief valves and API 14C for safety analysis, establish guidelines for steam trap selection, installation, and maintenance. Adhering to these standards not only guarantees operational reliability but also mitigates risks associated with steam system failures. Compliance with codes and standards is paramount in ensuring the seamless integration of steam traps into oil and gas processes, safeguarding both personnel and assets.
9. Conclusion
In the ever-evolving landscape of the oil and gas industry, the role of steam traps remains indispensable. These unassuming devices, with their intricate mechanisms, are the guardians of energy efficiency and operational integrity. From historical innovations to modern applications, steam traps have stood the test of time, shaping the industrial world as we know it. As we move forward, embracing sustainable practices and maximizing energy efficiency, steam traps will continue to be the unsung heroes, ensuring the seamless flow of energy in the heart of oil and gas processes. Understanding their significance, selecting the right type, and adhering to industry standards are pivotal steps in harnessing the full potential of steam traps, paving the way for a greener, more efficient future in the oil and gas industry.
Don’t miss the Complete Course on Piping Engineering: Check Now
Enrollment Link
FAQs
1. FAQ: What is the primary function of a steam trap in the oil and gas industry?
Answer: Steam traps in the oil and gas industry are designed to remove condensate and non-condensable gases from steam systems while ensuring minimal steam loss. They play a critical role in maintaining energy efficiency, preventing equipment damage, and optimizing industrial processes.
2. FAQ: How do I choose the right type of steam trap for my specific oil and gas application?
Answer: The selection of a steam trap depends on factors such as operating pressure, load variation, and condensate flow rate. Mechanical steam traps are suitable for high-pressure environments, thermodynamic traps are versatile for various pressures, and thermostatic traps are ideal for low-load applications. Consulting with a steam system engineer or specialist can help determine the most suitable type for your specific needs.
3. FAQ: What are the common signs of a malfunctioning steam trap in an oil refinery?
Answer: Malfunctioning steam traps can lead to issues such as water hammer, fluctuating temperatures, and inefficient heating processes. Visual indicators include steam leakage around the trap, unusual noises, or visible condensate accumulation. Regular inspection and maintenance are essential to identify and address these problems promptly.
4. FAQ: How can steam traps contribute to energy conservation in the oil and gas industry?
Answer: Efficient steam traps prevent steam loss by removing condensate promptly. By conserving steam, industries reduce the fuel needed to generate steam, leading to significant energy savings. Properly functioning steam traps also maintain consistent temperatures, optimizing overall energy use in various processes.
5. FAQ: Are there specific regulations or standards governing the installation and maintenance of steam traps in the oil and gas sector?
Answer: Yes, there are industry standards and codes, such as ASME PTC 39.1 and ISO 6552, that provide guidelines for the testing, evaluation, and classification of steam traps. Adhering to these standards ensures the reliability and safety of steam trap systems in the oil and gas industry. Compliance with local regulations and facility-specific protocols is also crucial.
Recommended courses (Published on EPCLand)
- Basics of Piping Engineering
- Piping Layout Engineering
- Piping Material Engineering
- Piping Stress Analysis
- Complete Course on Piping Engineering
- Material Requisitions
- Piping Material Specifications
- Valve Material Specifications
Don’t miss the published articles on following:
Attempt Quiz
Question 1:
What is the primary function of a steam trap in the Oil & Gas Industry?
Explanation: Steam traps in the Oil & Gas Industry are used to trap and remove condensate from steam lines, ensuring efficient steam distribution.
Question 2:
Which type of steam trap operates based on the difference in density between steam and condensate?
Explanation: Inverted Bucket Steam Traps operate based on the difference in density between steam and condensate.
Question 3:
Which component of a steam trap opens and closes based on the level of condensate?
Explanation: The Float in a steam trap opens and closes based on the level of condensate, allowing the trap to discharge condensate while retaining steam.
Question 4:
Which type of steam trap is suitable for high-pressure steam systems?
Explanation: Inverted Bucket Steam Traps are suitable for high-pressure steam systems due to their robust design and ability to handle high pressures.
Question 5:
What is the purpose of a bypass valve in a steam trap?
Explanation: A bypass valve in a steam trap allows steam to bypass the trap, ensuring continuous steam flow even during trap maintenance or failure.
Question 6:
What is the purpose of air vents in steam traps?
Explanation: Air vents in steam traps allow air to enter the trap, ensuring efficient condensate drainage and preventing steam locking.
Question 7:
What is the function of a thermodynamic disc in a steam trap?
Explanation: The thermodynamic disc in a steam trap senses temperature changes and closes the trap to prevent steam loss.
Question 8:
Which steam trap type is best suited for applications with varying loads and pressures?
Explanation: Float and Thermostatic Steam Traps are versatile and suitable for applications with varying loads and pressures.
Question 9:
What is the purpose of a sight glass on a steam trap?
Explanation: A sight glass on a steam trap is used to monitor the condensate level and ensure proper drainage.
Question 10:
What can happen if a steam trap fails to operate efficiently?
Explanation: If a steam trap fails to operate efficiently, it can lead to reduced equipment lifespan due to water hammer, energy wastage, and decreased steam quality.