Introduction
Plug valves are indispensable components in various industrial applications, playing a pivotal role in regulating the flow of fluids. They are integral parts of pipelines and are utilized in diverse sectors, including oil and gas, water treatment, chemical processing, and more. This article delves into the intricate world of plug valves, exploring their origins, mechanisms, types, applications, and the associated standards and codes governing their use.
Table of Contents
Don’t miss the Complete Course on Piping Engineering: Check Now
Enrollment Link
Brief History
Plug valves have a rich history that dates back centuries. The earliest versions of plug valves were simple devices made from wood, used to control the flow of water in ancient civilizations. Over the years, these valves evolved, with innovations in materials and design, leading to the sophisticated plug valves we see today. Notable advancements include the introduction of metal plug valves in the industrial revolution era, marking a significant leap in their durability and functionality.
Basic Function and Working Principle
At its core, a plug valve consists of a cylindrical or tapered plug with a hollow passageway. The valve is positioned to control the flow of fluid by rotating the plug within the valve body. In the closed position, the plug blocks the flow path, and by turning the plug, the passage is opened, allowing the fluid to flow through. This fundamental principle of rotation to control the flow makes plug valves efficient and reliable in various applications.
Main Components
1. Body: The body of a plug valve provides the structure and housing for the internal components. It is designed to withstand high pressures and temperatures, making it a critical element for the valve’s functionality.
2. Plug: The plug, usually made of metal, fits into the body and is responsible for controlling the flow. Its shape and design vary based on the specific type of plug valve, determining its efficiency and applicability.
3. Stem: The stem connects the actuator (the mechanism for controlling the valve) to the plug. When the actuator is engaged, it rotates the stem, which, in turn, rotates the plug to open or close the valve.
4. Actuator: The actuator can be manual (handwheel or lever), electric, or pneumatic. Manual actuators require human intervention, while electric and pneumatic actuators allow for remote or automated operation.
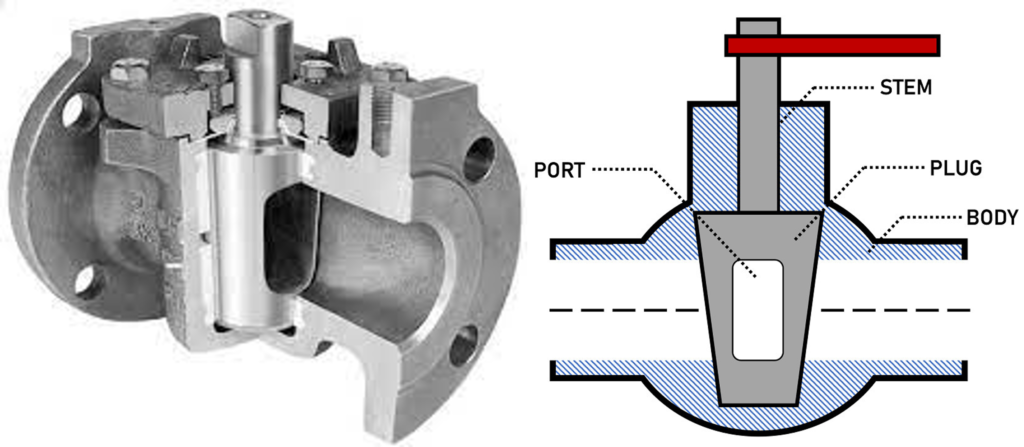
Types of Plug Valves
Plug valves come in several types, each tailored to specific applications and operational requirements.
1. Lubricated Plug Valves: These valves use a lubricant, typically a grease-like substance, to reduce friction between the plug and the body. Lubricated plug valves are suitable for applications where a tight seal is crucial.
2. Non-Lubricated Plug Valves: Non-lubricated plug valves are designed to operate without the need for external lubrication. They often feature self-lubricating components, reducing maintenance needs and making them ideal for certain industrial environments.
3. Eccentric Plug Valves: Eccentric plug valves have an offset plug, which means the plug’s axis is located away from the centerline of the pipe. This design enables a more effective seal and reduces wear, making them suitable for applications with abrasive fluids.
4. Sleeved Plug Valves: Sleeved plug valves have a flexible sleeve or lining inside the valve body. The plug moves within this sleeve, ensuring a tight seal. Sleeved plug valves are excellent for handling corrosive or abrasive fluids, providing enhanced durability and longevity.
Don’t miss the Complete Course on Piping Engineering: Check Now
Enrollment Link
Applications of Plug Valves
Plug valves find widespread use in various industries due to their versatility and reliability.
1. Oil and Gas Industry: In the oil and gas sector, plug valves are employed in pipelines and refineries to control the flow of crude oil, natural gas, and other hydrocarbons. Their robust design makes them suitable for high-pressure and high-temperature applications.
2. Water Treatment Plants: Plug valves play a vital role in water treatment plants, regulating the flow of water, chemicals, and other fluids. Their precise control capabilities contribute to the efficiency of water purification processes.
3. Chemical Processing: Chemical manufacturing facilities utilize plug valves to handle a wide range of chemicals. The valves’ resistance to corrosion and ability to handle aggressive substances make them invaluable in chemical processing operations.
4. Pulp and Paper Industry: In paper mills, plug valves are utilized for controlling the flow of pulp, chemicals, and water. Their durability and resistance to wear ensure reliable performance in the challenging environment of pulp and paper production.
Advantages and Disadvantages
Advantages | Disadvantages |
---|---|
High Sealing Capability | Limited Flow Control |
Simple Design | Prone to Wear and Tear |
Wide Range of Applications | Challenges in Maintenance |
Durability and Longevity |
Plug valves offer several advantages. Their high sealing capability ensures minimal leakage, making them ideal for applications where fluid containment is critical. Additionally, their simple design results in easy operation and maintenance. Plug valves are versatile, finding applications in various industries, and their durability and longevity contribute to their popularity.
However, plug valves also have limitations. They offer limited flow control compared to other types of valves, which may be a drawback in certain applications. They are also prone to wear and tear, especially in high-usage scenarios, necessitating regular maintenance. Overcoming these challenges requires careful consideration of the valve’s design, material, and operating conditions.
Don’t miss the Complete Course on Piping Engineering: Check Now
Enrollment Link
Associated Codes and Standards
Standards Organization | Relevant Codes and Standards |
---|---|
API (American Petroleum Institute) | API 6D: Specification for Pipeline Valves |
ASME (American Society of Mechanical Engineers) | ASME B16.34: Valves – Flanged, Threaded, and Welding End |
ISO (International Organization for Standardization) | ISO 9001: Quality management systems – Requirements |
Compliance with industry standards and codes is essential to ensure the reliability and safety of plug valves. Organizations like the American Petroleum Institute (API), the American Society of Mechanical Engineers (ASME), and the International Organization for Standardization (ISO) establish guidelines that manufacturers adhere to during the design, production, and testing of plug valves. These standards ensure consistency in quality and performance across different products and manufacturers.
Conclusion
In conclusion, plug valves are indispensable components in the world of industrial fluid control. Their evolution from simple wooden devices to sophisticated metal valves showcases the continuous advancements in engineering and materials science. Understanding the different types of plug valves and their applications is crucial for selecting the right valve for specific industrial needs.
As technology continues to advance, plug valves are likely to undergo further improvements, addressing their limitations and enhancing their efficiency. Industries will benefit from these advancements, enjoying more reliable and durable plug valves for their operations. Adherence to established standards and codes will remain pivotal, ensuring the highest quality and safety standards are met in the manufacturing and application of plug valves. As a result, these valves will continue to play a vital role in shaping various industrial processes, contributing to the global economy and technological progress.
FAQs
1. What is a plug valve and how does it work?
A plug valve is a type of quarter-turn valve that uses a cylindrical or tapered plug to control the flow of fluids. By rotating the plug within the valve body, the passage is either opened or closed, allowing or stopping the flow of the fluid.
2. What are the main applications of plug valves?
Plug valves are widely used in various industries, including oil and gas, water treatment, chemical processing, and pulp and paper production. They are employed to regulate the flow of liquids and gases in pipelines and other industrial processes.
3. What are the advantages of plug valves compared to other types of valves?
Plug valves offer high sealing capability, a simple design for easy operation, and a wide range of applications. They are durable and long-lasting, making them suitable for harsh industrial environments. However, they do have limitations in terms of flow control and may require regular maintenance.
4. How do lubricated and non-lubricated plug valves differ?
Lubricated plug valves require external lubrication, usually in the form of grease, to reduce friction between the plug and the valve body. Non-lubricated plug valves, on the other hand, are designed to operate without external lubrication, often featuring self-lubricating components for reduced maintenance needs.
5. What standards and codes govern the manufacturing and use of plug valves?
Plug valves are regulated by standards and codes established by organizations such as the American Petroleum Institute (API), the American Society of Mechanical Engineers (ASME), and the International Organization for Standardization (ISO). These standards ensure the quality, safety, and performance of plug valves in various industrial applications.
Recommended courses (Published on EPCLand)
- Basics of Piping Engineering
- Piping Layout Engineering
- Piping Material Engineering
- Piping Stress Analysis
- Complete Course on Piping Engineering
- Material Requisitions
- Piping Material Specifications
- Valve Material Specifications
Don’t miss the published articles on following:
Don’t miss the Complete Course on Piping Engineering: Check Now
Enrollment Link
Attempt Quiz
Question 1:
What is the primary function of a plug valve?
Explanation: Plug valves are primarily used to start, stop, or regulate fluid flow in pipelines.
Question 2:
What is the typical configuration of a plug valve?
Explanation: Plug valves belong to the rotary valve family and have a cylindrical or conical “plug” inside.
Question 3:
Which industry commonly uses plug valves for controlling fluid flow?
Explanation: Plug valves are commonly used in the oil and gas industry for controlling fluid flow.
Question 4:
What material is often used for the plug in plug valves?
Explanation: The plug in plug valves is often made of materials like stainless steel.
Question 5:
What is the advantage of a lubricated plug valve?
Explanation: Lubricated plug valves require less maintenance due to the lubrication applied to reduce friction and wear.
Question 6:
What is the primary sealing mechanism in a plug valve?
Explanation: The primary sealing mechanism in a plug valve is the plug, which fits into the body to stop or regulate the flow.
Question 7:
Where are lubricated plug valves commonly used?
Explanation: Lubricated plug valves are commonly used in corrosive environments due to their resistance to corrosion.
Question 8:
What is the handle rotation for a typical plug valve?
Explanation: A typical plug valve rotates 90 degrees to control the flow.
Question 9:
What type of flow is a plug valve best suited for?
Explanation: Plug valves are best suited for steady flow applications.
Question 10:
What is the disadvantage of lubricated plug valves?
Explanation: Lubricated plug valves require regular maintenance, which can be a disadvantage in certain applications.