Introduction
Needle valves, a fundamental component in various industrial applications, play a pivotal role in controlling the flow of fluids within a system. Their precision and reliability make them indispensable in sectors such as oil and gas, aerospace, and manufacturing. Understanding their intricate design, history, types, and applications is essential for engineers and professionals working in these fields.
Table of Contents
Brief History
Needle valves have a rich history that dates back to the early days of the Industrial Revolution. In the 19th century, as industries began to flourish, the need for precise control over fluid flow became evident. The first needle valves were rudimentary, but they laid the foundation for more sophisticated designs.
In the late 1800s, with advancements in metallurgy and machining, needle valves evolved significantly. Engineers started experimenting with various materials and designs, leading to the development of more durable and efficient valves. The invention of the hydraulic press and the growth of the oil and gas industry further propelled the refinement of needle valve technology.
Basic Function and Working Principle
Needle valves operate on a simple yet ingenious principle. They consist of a slender, tapered needle-like stem, which, when rotated, gradually raises or lowers to regulate the flow of fluid. This fine adjustment capability makes them ideal for applications where precise control is critical.
The key function of a needle valve is to control the flow rate and pressure of a fluid within a system. By adjusting the position of the needle, operators can achieve accurate and stable flow control. Needle valves are especially useful in situations where sudden surges or drops in pressure can damage the system.
Main Components
Needle valves comprise several essential components that ensure their proper functioning. The main parts of a typical needle valve include the body, bonnet, stem, seat, and handle. The body provides the housing for the internal components and serves as the primary structural element. The bonnet encloses the stem and other moving parts, protecting them from external factors.
The stem, a slender rod with a tapered end, is the central component responsible for regulating the flow. The seat, usually made of resilient materials like Teflon or graphite, forms a seal around the needle to prevent leakage. The handle, attached to the stem, allows operators to rotate the needle, adjusting the flow as needed.
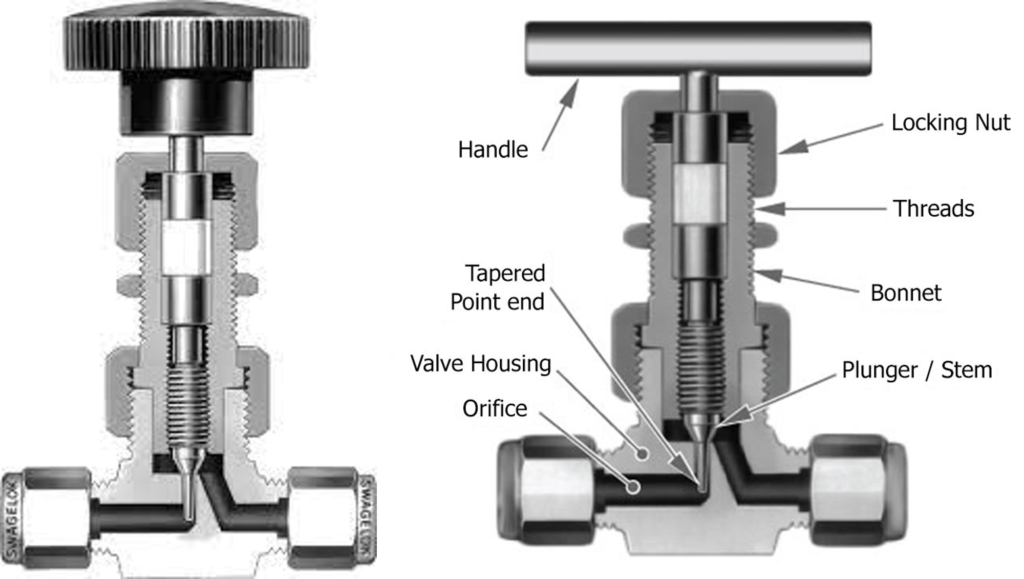
Types of Needle Valves
Needle valves come in various types, each tailored to specific applications. The classification is based on factors such as design, materials, and usage. The common types include screw-in needle valves, integral bonnet needle valves, and union-bonnet needle valves.
Table 1: Types of Needle Valves
Type | Description |
---|---|
Screw-In Needle Valves | Compact design, ideal for limited space applications. |
Integral Bonnet Needle Valves | Robust construction, suitable for high-pressure environments. |
Union-Bonnet Needle Valves | Easy to disassemble and maintain, popular in various industries. |
Application of Needle Valves
Needle valves find extensive application in diverse industrial sectors due to their precision and reliability. In the oil and gas industry, they are utilized in wellhead control panels, providing accurate control over the flow of oil and gas from wells. In aerospace, needle valves play a crucial role in hydraulic systems, ensuring precise control of landing gear and flight control surfaces.
In manufacturing, these valves are integrated into equipment used for processing chemicals, pharmaceuticals, and food products. Their ability to handle corrosive substances and maintain a stable flow rate makes them invaluable in such environments. Additionally, needle valves are employed in laboratories for precise control of gases and liquids in experiments and research.
Advantages and Disadvantages
Table 2: Advantages and Disadvantages of Needle Valves
Advantages | Disadvantages |
---|---|
Precise Flow Control | Limited Flow Capacity |
Tight Shut-Off Capability | Sensitivity to Contaminants |
Compact Design | Prone to Wear and Tear |
Versatility in Applications | Higher Cost Compared to Others |
Easy Installation | Requires Skilled Maintenance |
Needle valves offer precise flow control, allowing operators to fine-tune the flow rate according to specific requirements. Their tight shut-off capability ensures that there is minimal or no leakage, enhancing the safety and efficiency of the system. The compact design of needle valves makes them suitable for applications where space is limited. They are versatile and can handle a wide range of fluids, from gases to highly viscous liquids. Installation is relatively easy, although proper maintenance by skilled professionals is essential to ensure longevity.
However, needle valves also have their limitations. Their flow capacity is limited, making them unsuitable for high-flow applications. They are sensitive to contaminants, which can affect their performance. Like all mechanical components, needle valves are prone to wear and tear over time, necessitating periodic maintenance and potential replacements. Additionally, their precision and specialized design contribute to a higher cost compared to other types of valves.
Associated Codes & Standards
Table 3: Associated Codes & Standards for Needle Valves
Standards | Applicability |
---|---|
ASME B16.34 | General Valve Design and Manufacturing |
API 602 | Compact Steel Gate, Globe, and Check Valves |
ANSI B1.20.1 | Pipe Threads, General Purpose |
ISO 9001 | Quality Management Systems |
ASTM A105/A182 | Standard Specifications for Forged or Rolled Alloy and Stainless Steel Pipe Flanges, Forged Fittings, and Valves and Parts for High-Temperature Service |
API 6D | Pipeline Valves |
Needle valves are subject to various industry standards and codes to ensure their quality, safety, and performance. ASME B16.34 provides guidelines for the general design and manufacturing of valves, including needle valves. API 602 specifically addresses compact steel gate, globe, and check valves, which includes certain types of needle valves. ANSI B1.20.1 establishes standards for pipe threads, ensuring compatibility and proper sealing. ISO 9001 sets the criteria for quality management systems, emphasizing consistent quality in manufacturing processes.
ASTM A105/A182 outlines specifications for forged or rolled alloy and stainless steel pipe flanges, forged fittings, and valves and parts for high-temperature service, including needle valves. API 6D focuses on pipeline valves, including needle valves used in pipelines.
Conclusion
In conclusion, needle valves play a critical role in various industries, offering precise flow control and ensuring the safety and efficiency of fluid systems. Their evolution over the years has led to the development of specialized designs catering to specific applications. While they have distinct advantages, such as precise control and tight shut-off capability, they also have limitations, including limited flow capacity and sensitivity to contaminants.
Compliance with industry standards and codes is essential to guarantee the quality and performance of needle valves. As technology continues to advance, we can expect further innovations in needle valve design, addressing current limitations and expanding their applicability in different sectors. Understanding the nuances of needle valves is vital for engineers and professionals working in fields where fluid control is paramount, ensuring the seamless operation of various industrial processes.
FAQs
1. What is a needle valve and how does it differ from other types of valves?
A needle valve is a type of valve with a slender, tapered needle-like stem that controls the flow of fluids within a system. Unlike other valves, needle valves provide precise flow control, making them ideal for applications where accuracy is crucial. Their unique design allows for fine adjustments, setting them apart from traditional valves.
2. What are the primary applications of needle valves in industrial settings?
Needle valves find extensive use in various industries, including oil and gas, aerospace, manufacturing, and laboratories. They are employed in wellhead control panels, hydraulic systems, chemical processing equipment, and research experiments. Their ability to handle different fluids and offer accurate flow control makes them indispensable in these applications.
3. What are the key advantages of using needle valves in fluid control systems?
Needle valves offer several advantages, including precise flow control, tight shut-off capability, compact design, versatility in applications, and easy installation. Their ability to provide accurate and stable flow rates, along with their compact size, makes them valuable in situations where space is limited. Additionally, they ensure minimal or no leakage, enhancing the safety and efficiency of fluid systems.
4. What are the limitations and potential challenges associated with needle valves?
Despite their precision and reliability, needle valves have limitations. They have limited flow capacity, making them unsuitable for high-flow applications. Needle valves are also sensitive to contaminants, which can affect their performance. Over time, wear and tear can occur, requiring regular maintenance and potential replacements. Additionally, their specialized design contributes to a higher cost compared to other types of valves.
5. How important is compliance with industry standards and codes when it comes to needle valves?
Compliance with industry standards and codes is crucial for ensuring the quality, safety, and performance of needle valves. Standards such as ASME B16.34, API 602, and ANSI B1.20.1 provide guidelines for the design, manufacturing, and threading of needle valves. Adhering to these standards helps manufacturers produce high-quality valves that meet the requirements of various industrial applications, enhancing reliability and user confidence.
Recommended courses (Published on EPCLand)
- Basics of Piping Engineering
- Piping Layout Engineering
- Piping Material Engineering
- Piping Stress Analysis
- Complete Course on Piping Engineering
- Material Requisitions
- Piping Material Specifications
- Valve Material Specifications
Don’t miss the published articles on following:
Attempt Quiz
Question 1:
What is the primary function of a needle valve?
Explanation: A needle valve is used to control the flow rate of fluids in small pipes with precision.
Question 2:
What is the typical shape of the controlling element in a needle valve?
Explanation: The controlling element in a needle valve is typically needle-shaped, hence the name.
Question 3:
Which industry commonly uses needle valves for precision flow control?
Explanation: The aerospace industry commonly uses needle valves for precision flow control of fluids and gases.
Question 4:
What material is commonly used for the construction of needle valves?
Explanation: Brass is a common material used for the construction of needle valves due to its durability and resistance to corrosion.
Question 5:
Which of the following best describes the flow regulation mechanism of needle valves?
Explanation: Needle valves provide precise control over flow rates through a fine-threaded screw mechanism.
Question 6:
Which industry requires needle valves to handle corrosive substances?
Explanation: The chemical industry often uses needle valves to handle corrosive substances due to their resistant materials and precise control.
Question 7:
What is the purpose of the fine adjustment feature in needle valves?
Explanation: The fine adjustment feature in needle valves allows for precise control over the flow rate of fluids.
Question 8:
What is the advantage of using needle valves in high-pressure systems?
Explanation: Needle valves can handle high pressures and provide precise control over the flow rate in high-pressure systems.
Question 9:
Which of the following is NOT a common application of needle valves?
Explanation: Needle valves are not commonly used in automotive engines.
Question 10:
Which part of a needle valve is responsible for controlling the flow rate?
Explanation: The needle, a fine-threaded screw-like component, is responsible for controlling the flow rate in a needle valve.