I. Introduction
In the vast and intricate world of the oil and gas industry, the transport of fluids through pipelines is a fundamental component. Whether it’s crude oil, natural gas, or various other liquids and gases, the seamless and efficient flow of these substances is crucial. Piping systems play a pivotal role in facilitating this flow, and one essential aspect of these systems is branch connections.
Branch connections, or simply branch connections, are a vital element in the oil and gas sector, allowing for the distribution of fluids, control of flow, and integration with various equipment and structures. In this article, we will delve into the fascinating world of piping branch connections, exploring their history, functions, working principles, types, applications, advantages, disadvantages, and the associated codes and standards that govern their use.
Table of Contents
Don’t miss the Complete Course on Piping Engineering: Check Now
Enrollment Link
II. Brief History
The history of branch connections is closely intertwined with the development of piping systems and the industrial revolution. Piping has been used for centuries to transport water and other fluids, with early applications dating back to ancient civilizations. However, the modern use of branch connections in the oil and gas industry can be traced back to the 19th century when the world was in the midst of a significant transformation with the rise of the industrial era.
During this period, as demand for oil and gas exploration and transportation grew, the need for more sophisticated piping systems became evident. Branch connections emerged as a solution to facilitate the safe and efficient distribution of fluids in complex networks of pipelines, refineries, and petrochemical plants. Over the years, branch connections have evolved in design, materials, and manufacturing processes, ensuring they meet the rigorous demands of the oil and gas industry.
III. Basic Function and Working Principle
Branch connections serve a fundamental purpose within piping systems: they enable the connection of a smaller pipe or tubing to a larger main pipeline, allowing for the diversion of fluid flow. They can also connect two or more pipelines, serving as junction points in complex networks.
The working principle of branch connections is relatively straightforward. They are attached to the main pipeline through welding, threading, or other joining methods. This attachment creates a sealed connection that ensures the flow of fluids between the main pipeline and the branch. The design of branch connections incorporates features such as a reinforced pad or saddle to support the branch pipe, ensuring structural integrity and preventing leaks.
Branch connections can incorporate additional elements, such as valves, instrumentation, or control devices, depending on their specific application. These elements allow for the regulation of fluid flow and can be crucial in various oil and gas processes.
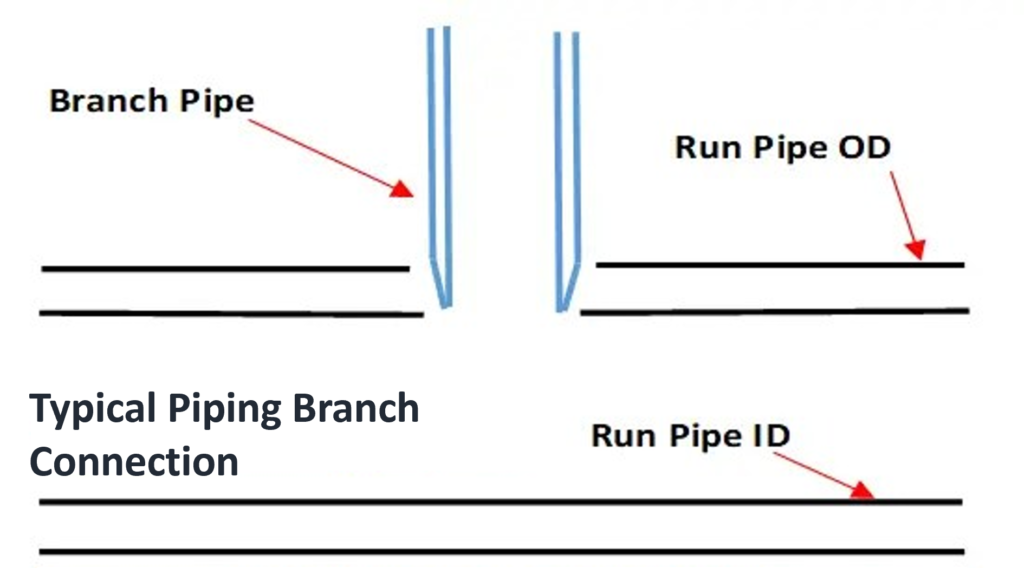
IV. Types of Piping Branch Connections
Branch connections come in a variety of types, each designed to serve specific purposes within the oil and gas industry. Some common types of branch connections include:
1. Weldolets
Description: Weldolets are a common type of branch connection that is welded onto the main pipeline. They are designed to provide a reinforced opening for attaching a smaller pipe or tube, diverting the flow of fluid from the main pipeline. The design typically includes a weldolet body with a connection for the branch pipe and a welded connection to the main pipeline.
Applications: Weldolets are widely used in various applications, especially in situations where a strong and leak-resistant connection is essential. They are often preferred in high-pressure and high-temperature environments. Weldolets are suitable for both liquid and gas applications, including in refineries, petrochemical plants, and offshore platforms.
Advantages:
- Weldolets provide a strong and reliable connection, minimizing stress on the main pipeline.
- They are available in various configurations, including sockolets, threadolets, and elbolets, allowing for flexibility in design.
- Well-suited for high-pressure and high-temperature applications.
Disadvantages:
- Requires skilled welders for installation to ensure a leak-free connection.
- The initial cost of materials and welding may be relatively high, especially for large-diameter branches.
2. Threaded Connections
Description: Threaded branch connections are screwed into the main pipeline. They have threads on the branch end, allowing them to be easily connected or disconnected from the main pipeline using threaded fittings. Threaded connections are commonly used for small-diameter branches and offer ease of installation and maintenance.
Applications: Threaded connections are typically used in low-pressure and low-temperature applications. They are commonly employed in situations where frequent disassembly and reassembly are required, such as for maintenance and modifications.
Advantages:
- Quick and easy installation without the need for welding.
- Suitable for small-diameter branch pipes.
- Allows for easy disconnection and reconnection, making them ideal for situations requiring maintenance.
Disadvantages:
- Limited to low-pressure and low-temperature applications due to the threaded connection.
- Not suitable for high-pressure or high-temperature environments.
3. Socket Weld Connections
Description: Socket weld connections involve welding the branch connection into the main pipeline through a socket. This type of connection is used in applications that require a strong, high-integrity joint. Socket weld branch connections have a socket-like design, where the branch pipe is inserted and then welded in place.
Applications: Socket weld connections are commonly used in high-pressure applications. They are well-suited for situations where leak-tightness and structural integrity are crucial, such as in high-pressure gas or steam systems.
Advantages:
- Provides a strong and leak-resistant connection.
- Suitable for high-pressure and high-temperature applications.
- Relatively easy to install and disassemble for maintenance.
Disadvantages:
- Requires skilled welders for installation.
- Welding adds complexity and cost to the installation process.
4. Flanged Connections
Description: Flanged branch connections are connected using flanges and bolts. They feature a branch connection with a flange, which is bolted to a matching flange on the main pipeline. The flanges create a secure and sealed connection.
Applications: Flanged connections are versatile and are commonly used in applications where frequent disconnection and reconnection are necessary, such as in pump stations, measurement points, and flow control systems. They are also suitable for both high and low-pressure applications.
Advantages:
- Versatile and adaptable for various applications.
- Easy to disconnect and reassemble, making them ideal for maintenance or modifications.
- Suitable for both high and low-pressure systems.
Disadvantages:
- The cost of flanges and bolts can be significant, especially in large-scale projects.
- Requires more space for the installation of flanges, which may not be feasible in some layouts.
5. Butt Weld Connections
Description: Butt weld connections involve welding the branch directly to the main pipeline. This creates a strong, seamless, and leak-proof connection. The branch pipe and main pipeline have matching ends that are welded together, ensuring structural integrity and fluid-tightness.
Applications: Butt weld connections are commonly used in high-pressure and high-temperature applications where structural integrity and leak resistance are paramount. They are widely employed in critical systems, including those found in petrochemical plants and power generation facilities.
Advantages:
- Provides a highly robust and leak-resistant connection.
- Suitable for high-pressure and high-temperature applications.
- Maintains the full structural integrity of the pipeline.
Disadvantages:
- Requires skilled welders and rigorous quality control to ensure a reliable connection.
- Welding adds complexity and cost to the installation process.
Don’t miss the Complete Course on Piping Engineering: Check Now
Enrollment Link
V. Applications of Piping Branch Connections
Piping branch connections find extensive use in a wide range of applications within the oil and gas industry. Some of the primary applications include:
1. Distribution Networks
In the oil and gas industry, the efficient distribution of hydrocarbons is paramount. This includes the transportation of crude oil from wells to refineries, the distribution of refined products to storage tanks or delivery points, and the movement of natural gas from production facilities to end-users. Piping branch connections play a crucial role in creating distribution networks that branch off from main pipelines.
These branch connections enable the transfer of fluids to various destinations, such as storage tanks, loading facilities, or distribution centers. They can be used to divert flows based on demand or to isolate specific sections of the network for maintenance or repairs. In distribution networks, the flexibility of branch connections allows for the optimization of fluid transport and ensures a constant supply of oil and gas products.
2. Refineries and Petrochemical Plants
Refineries and petrochemical plants are complex facilities with an intricate network of pipes carrying various products and intermediates. Branch connections are essential for these plants to connect different process units, instruments, and control devices. They facilitate the distribution of feedstock, intermediate products, and finished products within the plant.
In a refinery, for example, branch connections can be found connecting distillation columns, heat exchangers, reactors, and various processing units. They allow for the integration of these units into a cohesive production system. Additionally, they are used to connect pipelines to control devices, valves, and instrumentation, ensuring precise process control and monitoring.
3. Offshore Platforms
Offshore oil and gas production presents unique challenges due to the harsh marine environment. Branch connections are used in offshore platforms to connect pipelines to wellheads, subsea infrastructure, and processing equipment on the seabed. The design of these branch connections must account for factors like extreme pressures, corrosive seawater, and the need for durability in a submerged environment.
Branch connections in offshore applications play a critical role in transporting hydrocarbons from the wellhead to the production platform. They also allow for the integration of safety systems, control devices, and instrumentation to monitor and manage the flow of oil and gas. The ability to access and service these connections is vital for maintaining offshore operations.
4. Gas Compression Stations
In gas compression stations, branch connections are used to connect pipelines to compressors and other equipment. Gas compression stations are essential in the oil and gas industry for increasing the pressure of natural gas to facilitate its transportation over long distances. Branch connections allow for the seamless integration of compressors into the gas transmission system.
The correct selection of branch connections in these applications is critical because they must withstand the high pressures associated with gas compression. They also need to accommodate the various control and monitoring systems that are essential for regulating gas flow and ensuring the safety of the compression process.
5. Cross-Country Pipelines
Cross-country pipelines are vast networks of pipelines that transport oil and gas over long distances, often spanning hundreds of miles or more. Branch connections are used to create access points along these pipelines, which are necessary for maintenance, inspection, and the integration of measurement and control devices.
Branch connections in cross-country pipelines enable technicians to access specific segments of the pipeline without disrupting the entire flow. This is essential for routine maintenance, inspection of the pipeline’s integrity, and the installation of sensors or measurement devices to monitor flow rates, pressure, and other critical parameters.
VI. Advantages & Disadvantages
To provide a comprehensive understanding of piping branch connections, it is essential to consider their advantages and disadvantages:
Advantages
1. Efficient Fluid Distribution
Piping branch connections enable the efficient distribution of fluids, ensuring they reach their intended destinations without disruptions or pressure losses.
2. Structural Integrity
Properly designed and installed branch connections offer structural integrity, preventing leaks and ensuring the overall safety of the system.
3. Versatility
The availability of various types of branch connections allows for flexibility in design and adaptation to different project requirements.
4. Integration of Instruments
Branch connections can incorporate valves, gauges, and other instruments, facilitating control and monitoring of fluid flow.
5. Maintenance and Repairs
Certain types of branch connections, such as flanged connections, make it easier to disassemble and reassemble sections of pipelines for maintenance and repairs.
Disadvantages
1. Cost
The initial cost of materials and installation for branch connections can be relatively high, especially in projects with numerous connections.
2. Potential Leakage
Improper installation or maintenance can lead to leakage, which can be costly and detrimental to the environment.
3. Space Requirements
Some types of branch connections, like weldolets, require additional space for installation, which may not always be available in tight layouts.
4. Welding Expertise
Welding-based branch connections require skilled welders and stringent quality control to ensure their reliability.
Don’t miss the Complete Course on Piping Engineering: Check Now
Enrollment Link
VII. Associated Codes & Standards
To maintain safety and quality standards in the oil and gas industry, numerous codes and standards are established to govern the use of branch connections. These include:
1. ASME B31.3 – Process Piping
This code sets the requirements for the design, construction, and inspection of process piping systems, including branch connections. It provides guidelines for materials, fabrication, and testing.
2. API 570 – Piping Inspection Code
API 570 focuses on the inspection, repair, alteration, and rerating of in-service piping systems. It outlines procedures for assessing the condition of branch connections and the entire piping system.
3. ASME BPVC – Boiler and Pressure Vessel Code
This code contains regulations for the design and construction of pressure vessels, including the standards for branch connections in high-pressure applications.
4. NACE MR0175/ISO 15156 – Sulfide Stress Cracking Resistant Metallic Materials
This standard specifies the requirements for materials that are resistant to sulfide stress cracking in oil and gas production environments. It is crucial for selecting suitable materials for branch connections.
VIII. Conclusion
Piping branch connections are the unsung heroes of the oil and gas industry, ensuring the seamless flow of fluids and the integrity of piping systems. As this article has highlighted, their history, functions, working principles, types, applications, advantages, disadvantages, and the importance of adhering to industry codes and standards all contribute to their significance.
In an industry where safety and efficiency are paramount, understanding and properly implementing branch connections is essential. Their versatility and adaptability make them a critical element in a wide range of applications, from distribution networks to refineries and offshore platforms.
The oil and gas industry continually evolves, and branch connections continue to advance in design and materials to meet the ever-increasing demands. They remain essential components in the complex web of pipes that crisscross the globe, enabling the energy resources that power our world.
FAQs
1. What is the primary purpose of piping branch connections in the oil and gas industry?
Piping branch connections primarily serve to connect smaller pipes or tubing to larger main pipelines, allowing for the diversion of fluid flow. They are used to distribute fluids efficiently, control flow, and integrate with various equipment and structures.
2. What are the main types of branch connections used in the oil and gas industry, and how do they differ?
Common types of branch connections include Weldolets, threaded connections, socket weld connections, flanged connections, and butt weld connections. They differ in terms of their installation methods, application suitability, and structural design. The choice of type depends on factors like the fluid being transported and the specific project requirements.
3. What are the advantages of using piping branch connections in oil and gas projects?
Branch connections offer advantages such as efficient fluid distribution, structural integrity, versatility in design, integration of instruments, and the ability to facilitate maintenance and repairs. They play a crucial role in ensuring the seamless operation of various processes within the industry.
4. What are the common industry codes and standards that govern the use of branch connections in the oil and gas sector?
Key industry codes and standards include ASME B31.3 (Process Piping), API 570 (Piping Inspection Code), ASME BPVC (Boiler and Pressure Vessel Code), and NACE MR0175/ISO 15156 (Sulfide Stress Cracking Resistant Metallic Materials). These standards provide guidelines for the design, construction, inspection, and materials used in branch connections.
5. What are the potential disadvantages or challenges associated with using branch connections in oil and gas projects?
Disadvantages of branch connections may include initial cost considerations, potential for leakage if not installed or maintained properly, space requirements for certain types, and the need for skilled welding expertise in specific applications. Careful planning and adherence to industry standards can help mitigate these challenges.
Recommended courses (Published on EPCLand)
- Complete Course on Piping Engineering
- Basics of Piping Engineering
- Piping Layout Engineering
- Piping Material Engineering
- Piping Stress Analysis
- Material Requisitions
- Piping Material Specifications
- Valve Material Specifications
- Plant Design & Layouts-OISD 118
- Isometric Management
Library of Technical Articles
Don’t miss out the collection of 15+ articles on following topics:
- Basics of Oil and Gas Industry
- Valves
- Testing
- Tank
- Piping Bulk Items
- Pipe
- Metallurgy
- Piping Materials
- Layout
- Instrumentation
- Heat Exchanger
- Type of Contracts
- Codes and Standards
- ASTM Standards
- Articles on Piping Specialty Items
Video details of Complete Course on Piping Engineering
Don’t miss the Complete Course on Piping Engineering: Check Now
Enrollment Link
Attempt Quiz
Question 1:
What is the purpose of a weldolet in piping branch connections?
Explanation: A weldolet is used to create a branch connection for smaller pipes in a larger pipeline.
Question 2:
Which material is commonly used for manufacturing branch connections in corrosive environments?
Explanation: Stainless Steel is commonly used for branch connections in corrosive environments due to its corrosion resistance.
Question 3:
What is the function of a threadolet in branch connections?
Explanation: A threadolet is used to create a threaded branch connection in a pipeline.
Question 4:
Which type of branch connection is suitable for high-pressure applications?
Explanation: A Sockolet is a branch connection suitable for high-pressure applications.
Question 5:
What is the primary difference between a weldolet and a sockolet?
Explanation: The primary difference between a weldolet and a sockolet is the type of connection they create in the pipe.
Question 6:
Which branch connection type is commonly used for connecting small instrumentation lines?
Explanation: Nipolet is commonly used for connecting small instrumentation lines in branch connections.
Question 7:
What is the function of a latrolet in a branch connection?
Explanation: A latrolet is used to create a lateral branch in a pipeline.
Question 8:
Which type of branch connection is used for changing the pipe’s direction by 45 degrees?
Explanation: Elbolet is used for changing the pipe’s direction by 45 degrees in a branch connection.
Question 9:
What is the purpose of an elbolet in a branch connection?
Explanation: An elbolet is used to connect pipes at a 90-degree angle in a branch connection.
Question 10:
What is the main advantage of using branch connections in piping systems?
Explanation: Branch connections in piping systems allow for the addition of new pipelines without major modifications, reducing system complexity.