Introduction
Piping fittings are a critical component of any oil and gas industry project. They play a vital role in connecting, terminating, and controlling the flow of various fluids within a complex network of pipelines. These fittings are essential for maintaining the integrity and efficiency of the system. In this article, we will delve into the world of piping fittings, exploring their history, basic functions, working principles, different types, and their diverse applications within the oil and gas industry.
Table of Contents
Don’t miss the Complete Course on Piping Engineering: Check Now
Enrollment Link
Brief History
Piping fittings have a rich history that dates back to the early days of industrialization. The first rudimentary fittings were primarily made of cast iron and used in steam-powered engines and early industrial processes. Over time, as technology advanced and industries expanded, the demand for more sophisticated and specialized fittings grew. In the oil and gas sector, the development of piping fittings paralleled the industry’s evolution. Today, these fittings are manufactured with precision and sophistication, making them a cornerstone of modern oil and gas projects.
Basic Function and Working Principle
Basic Functions
Piping fittings serve several fundamental functions within the oil and gas industry. These include:
- Connection: Fittings are used to connect pipes of different sizes, materials, or configurations. They ensure a secure and leak-free joint.
- Termination: They terminate the flow of fluid in specific areas, such as at the end of a pipeline or a branch line.
- Direction Control: Fittings help direct the flow of fluids by providing elbows, tees, and other directional components.
- Pressure Control: Some fittings, like valves and regulators, are designed to control the pressure within the pipeline.
Working Principles
The working principles of piping fittings vary depending on their type and purpose. For instance, a basic elbow fitting changes the direction of flow, while a valve fitting can control the flow by opening and closing. These principles are essential for ensuring the proper functioning of the oil and gas system.
Types of Piping Fittings
Piping fittings come in a wide range of types, each designed for specific applications and requirements. Understanding the different types is essential for choosing the right fitting to meet the demands of an oil and gas project. Here, we’ll explore each type in more detail:
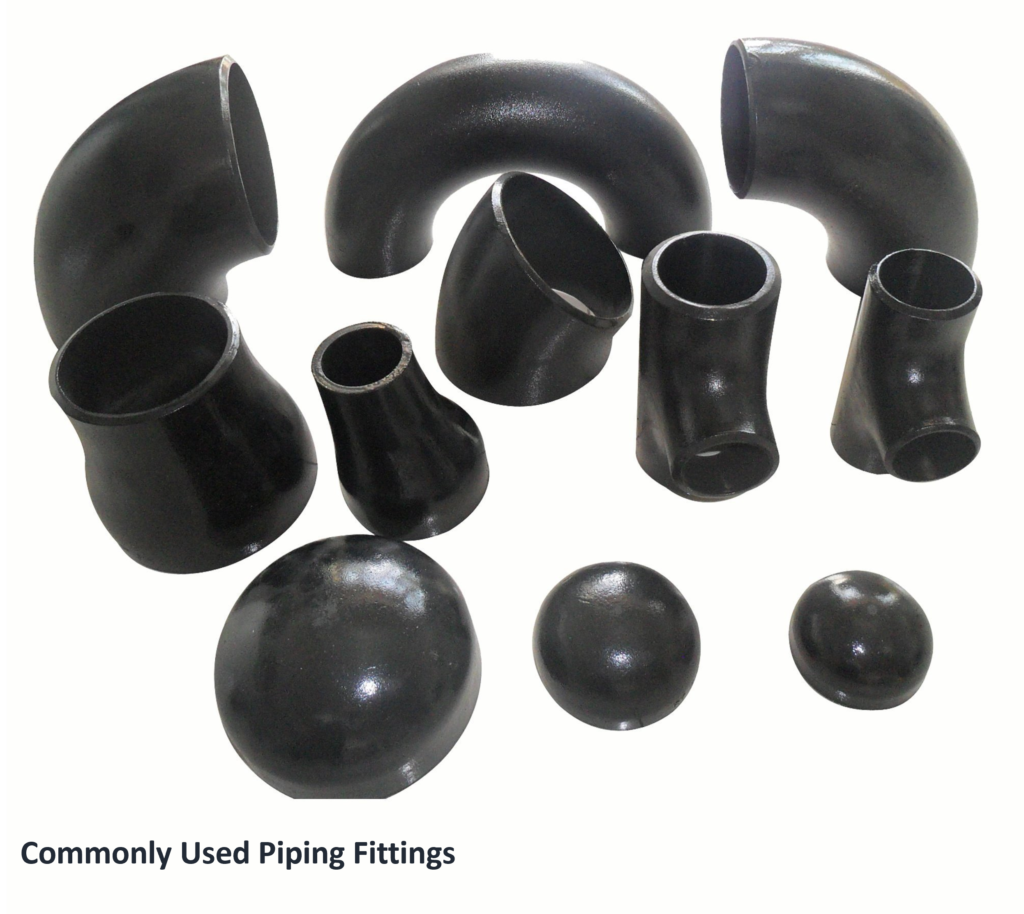
1. Elbow Fittings
Elbow fittings are one of the most common types of fittings used in the industry. They are designed to change the direction of the pipeline, allowing for smooth turns and transitions. Elbows are available in various angles, with 90 degrees and 45 degrees being the most common. These fittings are vital for navigating around obstacles, corners, and other changes in the pipeline’s direction.
- Applications: Elbow fittings are widely used in almost every aspect of the oil and gas industry, including upstream drilling, refining, and distribution.
2. Tee Fittings
Tee fittings are used to create a branch in the pipeline. They have a T-shaped design, with one inlet and two outlets (or vice versa), allowing the distribution of fluids to multiple directions from a single pipeline. Tees are crucial for managing the flow of liquids or gases to various equipment or processes.
- Applications: Tees are used in distribution systems, where fluid flow needs to be divided into multiple directions, such as supplying different sections of a plant or equipment.
3. Cross Fittings
Cross fittings are similar to tee fittings but with four openings arranged in a cross configuration. They are less common than tees but essential for specific applications where a pipeline needs to split into four different directions. Cross fittings are typically used when multiple branch lines are required.
- Applications: Cross fittings find use in specialized processes where fluids need to be directed to four different components or systems.
4. Reducer Fittings
Reducer fittings are employed when there is a need to transition between pipes of different sizes. These fittings come in two types: concentric and eccentric reducers. Concentric reducers have a symmetrical design, gradually reducing the pipe’s diameter, while eccentric reducers are used when a reduction in diameter is required but not necessarily in a centered fashion. These fittings ensure a balanced flow in the pipeline.
- Applications: Reducer fittings are commonly used in industries where the flow rate and diameter of pipes change, such as in petrochemical plants and refineries.
5. Coupling Fittings
Coupling fittings are used to connect two pipes of the same size. They provide a secure, leak-free connection and are often threaded or welded in place. Couplings are straightforward but essential components for joining two pipes to create a continuous, unbroken pipeline.
- Applications: Couplings are used in various applications where pipe segments need to be connected, ensuring a continuous flow of fluids.
6. Union Fittings
Union fittings serve a purpose similar to that of couplings, but they allow for easy disconnection and reconnection of pipes. Unions consist of three parts: a male end, a female end, and a nut. This design allows for the quick and convenient disassembly of pipes for maintenance or repairs without cutting or welding.
- Applications: Unions are commonly used in applications where periodic access to pipes is required, such as in maintenance and repair work.
7. Valve Fittings
Valve fittings encompass a broad category of fittings used for controlling the flow of fluids within the pipeline. Different types of valves are employed to start, stop, or regulate the flow as needed. Some common types of valve fittings include gate valves, ball valves, globe valves, and check valves.
- Applications: Valve fittings are crucial in processes that require precise control over fluid flow, safety shutdown systems, and regulation of pressure.
8. Flange Fittings
Flange fittings are essential for connecting pipes to various components like pumps, valves, tanks, or other equipment. They consist of flat, circular discs with holes for bolts, providing a secure and leak-proof connection. Flanges are commonly used in high-pressure and high-temperature applications.
- Applications: Flange fittings are found in petrochemical plants, refineries, and offshore drilling platforms where secure connections between pipes and equipment are vital.
9. Cap and Plug Fittings
Cap and plug fittings are used to close the ends of pipes securely. Caps are used when permanent closure is required, while plugs are employed when periodic access to the pipe is necessary. These fittings ensure that the ends of pipes remain sealed, preventing the entry of contaminants and maintaining pipeline integrity.
- Applications: Cap and plug fittings are used in various applications, from capping unused pipes to sealing off pipes temporarily during maintenance or when not in use.
Don’t miss the Complete Course on Piping Engineering: Check Now
Enrollment Link
Applications of Piping Fittings
Piping fittings find a wide range of applications within the oil and gas industry, contributing to the overall functionality and safety of the system. Some notable applications include:
1. Transporting Hydrocarbons
In the upstream sector, piping fittings play a crucial role in the transportation of crude oil and natural gas from the wellhead to processing facilities. Here are some specific applications within this context:
a. Elbows and Reducers
Elbow fittings are used to navigate around obstacles and corners in oil fields. They facilitate the seamless flow of hydrocarbons from the wellhead to the initial processing points. Reducer fittings are employed to transition between pipes of different sizes, ensuring the smooth transfer of fluids.
b. Valves
Valve fittings, such as ball valves and gate valves, provide control over the flow of hydrocarbons. They can be used to start, stop, or regulate the flow of crude oil or natural gas, ensuring safe and efficient transport.
2. Refining Processes
In refining and petrochemical plants, where crude oil is processed into various products like gasoline, diesel, and petrochemicals, piping fittings are used extensively. Some applications include:
a. Flange Fittings
Flange fittings are employed to connect pipes to various components like pumps, heat exchangers, and distillation columns. These fittings ensure a reliable and leak-proof connection, critical in preventing product contamination and safety hazards.
b. Valve Fittings
Valve fittings are used to control the flow of various chemicals and fluids throughout the refining process. For example, they regulate the flow of crude oil through different processing units, allowing for efficient separation and purification.
3. Distribution and Storage
For the distribution and storage of petroleum products, such as gasoline, diesel, and aviation fuel, piping fittings are indispensable. Here are a few applications in this regard:
a. Coupling and Union Fittings
Coupling fittings are used to connect pipes within storage tanks and distribution systems, ensuring a secure and leak-free connection. Union fittings are employed when there’s a need for easy disconnection and reconnection, which can be particularly useful during maintenance and repairs.
b. Cap and Plug Fittings
In storage tank applications, cap and plug fittings are essential for closing the ends of pipes securely, preventing spills or contamination. Caps are used for permanent closure, while plugs allow for periodic access when needed.
4. Offshore Drilling
In offshore drilling platforms, where oil and gas extraction takes place in challenging marine environments, piping fittings are vital. Specific applications include:
a. Flange Fittings
Flange fittings are used extensively to connect pipes to various equipment on offshore platforms, such as pumps, compressors, and risers. They provide a reliable and robust connection that can withstand the harsh conditions of the sea.
b. Elbow Fittings
Elbow fittings are employed to navigate complex pipe routing on offshore platforms, allowing the flow of extracted oil and gas from the ocean floor to the surface.
5. Gas Transmission
In the midstream sector, where natural gas is transported over long distances, piping fittings have critical roles to play. Applications include:
a. Valve Fittings
Valve fittings, such as ball valves and check valves, are used in compressor stations, metering stations, and regulating stations. They control the flow and pressure of natural gas as it travels through pipelines, ensuring efficient transmission.
b. Flange Fittings
Flange fittings are used to connect pipes to various components within the transmission network, including compressors and storage facilities. These fittings provide secure connections to withstand the high pressures involved.
6. LNG Processing
Liquefied Natural Gas (LNG) is an integral part of the natural gas industry. Piping fittings are used in LNG processing facilities for applications like:
a. Cryogenic Fittings
Piping fittings in LNG facilities must be able to withstand extreme cold and high-pressure conditions. Specialized fittings are employed to handle these challenges, ensuring the safe processing and transport of LNG.
In all of these applications, the choice of piping fittings is critical to the efficiency, safety, and reliability of the oil and gas system. Different fittings are selected based on the specific requirements of the project, the nature of the fluids being transported, and the environmental conditions in which they are used.
Advantages & Disadvantages of Piping Fittings
Advantages
Advantage | Description |
---|---|
1. Versatility | Piping fittings are available in various types and materials, allowing for customization to suit specific needs. |
2. Reliability | When installed and maintained correctly, piping fittings offer a reliable and long-lasting solution for fluid transport. |
3. Control | Fittings like valves provide precise control over fluid flow, which is crucial in many oil and gas processes. |
4. Safety | Well-designed and maintained fittings enhance safety by preventing leaks, pressure imbalances, and accidents. |
5. Ease of Maintenance | Many fittings are designed for easy maintenance and replacement, reducing downtime during repairs. |
Disadvantages
Disadvantage | Description |
---|---|
1. Cost | High-quality fittings and their installation can be costly, particularly for large-scale projects. |
2. Complexity | The vast array of fitting types and sizes can lead to complexity in design and selection. |
3. Maintenance Challenges | Over time, fittings may require maintenance, which can be a challenge, especially in remote or harsh environments. |
4. Environmental Impact | Improperly managed fittings can contribute to environmental pollution, particularly in cases of leaks or failures. |
5. Compatibility | Ensuring compatibility between different fitting types and materials can be a concern in some applications. |
Don’t miss the Complete Course on Piping Engineering: Check Now
Enrollment Link
Associated Codes & Standards
To ensure the safety, reliability, and quality of piping fittings in the oil and gas industry, various codes and standards have been developed and implemented. These codes and standards provide guidelines for the design, fabrication, inspection, and maintenance of piping fittings. Some of the most significant ones include:
1. ASME B16 Series
The American Society of Mechanical Engineers (ASME) publishes the B16 series of standards, which covers a wide range of piping components, including flanges, valves, and fittings. These standards provide guidelines for material specifications, dimensions, and testing requirements.
2. API Standards
The American Petroleum Institute (API) produces a range of standards that are specifically tailored to the oil and gas industry. These standards cover various aspects of the industry, including the design and manufacturing of piping fittings.
3. ASTM International
ASTM International develops and publishes standards for materials, products, systems, and services. Many piping fittings are subject to ASTM standards, ensuring the quality and performance of the materials used in their construction.
4. ANSI/ASME B31.3
The ANSI/ASME B31.3 standard focuses on process piping in the oil and gas industry. It provides guidelines for design, materials, fabrication, inspection, testing, and safety in the design and operation of piping systems.
5. ASME Boiler and Pressure Vessel Code
For fittings that handle high-pressure and high-temperature applications, the ASME Boiler and Pressure Vessel Code is a crucial standard. It sets forth rules for the design, fabrication, and inspection of pressure vessels, including some types of piping fittings.
Conclusion
Piping fittings are the unsung heroes of the oil and gas industry, connecting the dots in a complex network of pipelines that span continents and oceans. Their history, functionality, and applications are deeply intertwined with the evolution of the industry itself. While they may not always be in the spotlight, their role in ensuring the safe and efficient transport of oil and gas is undeniable. The variety of fittings available, their advantages, and their adherence to industry standards all contribute to the success of oil and gas projects worldwide.
As the industry continues to evolve and embrace new technologies, the importance of piping fittings remains constant. Whether it’s the precision control of a valve, the distribution capability of a tee, or the robustness of a flange, these fittings will continue to be the backbone of the oil and gas industry for years to come.
FAQs
1. What are piping fittings, and why are they essential in the oil and gas industry?
Piping fittings are components used to connect, control, and terminate pipelines in the oil and gas industry. They are essential for maintaining the integrity and efficiency of the system, ensuring the safe transport of fluids, and allowing for precise control of flow and pressure.
2. What types of piping fittings are commonly used in the oil and gas industry, and how do they differ?
Common types of piping fittings in the industry include elbows, tees, reducers, valves, flanges, and more. These fittings serve various purposes, such as changing direction, branching, reducing pipe size, controlling flow, and ensuring leak-free connections.
3. How do piping fittings contribute to safety in oil and gas projects?
Properly selected, installed, and maintained piping fittings play a vital role in ensuring safety. They prevent leaks, maintain pressure control, and allow for emergency shutdowns when necessary, reducing the risk of accidents and environmental hazards.
4. What are the challenges associated with using piping fittings in oil and gas projects?
Challenges can include the cost of high-quality fittings, the complexity of selecting the right type for specific applications, maintenance in remote or harsh environments, environmental impact if not managed correctly, and ensuring compatibility between different fittings and materials.
5. Are there specific industry standards and codes that govern the use of piping fittings in the oil and gas sector?
Yes, various standards and codes, such as the ASME B16 Series, API standards, ASTM standards, ANSI/ASME B31.3, and the ASME Boiler and Pressure Vessel Code, provide guidelines for the design, fabrication, inspection, and maintenance of piping fittings in the oil and gas industry. Adherence to these standards is crucial for safety and reliability.
Recommended courses (Published on EPCLand)
- Complete Course on Piping Engineering
- Basics of Piping Engineering
- Piping Layout Engineering
- Piping Material Engineering
- Piping Stress Analysis
- Material Requisitions
- Piping Material Specifications
- Valve Material Specifications
- Plant Design & Layouts-OISD 118
- Isometric Management
Library of Technical Articles
Don’t miss out the collection of 15+ articles on following topics:
- Basics of Oil and Gas Industry
- Valves
- Testing
- Tank
- Piping Bulk Items
- Pipe
- Metallurgy
- Piping Materials
- Layout
- Instrumentation
- Heat Exchanger
- Type of Contracts
- Codes and Standards
- ASTM Standards
- Articles on Piping Specialty Items
Video details of Complete Course on Piping Engineering
Don’t miss the Complete Course on Piping Engineering: Check Now
Enrollment Link
Attempt Quiz
Question 1:
What is the purpose of a pipe elbow in the Oil & Gas Industry?
Explanation: A pipe elbow is used to change the direction of flow in the Oil & Gas Industry.
Question 2:
Which piping fitting is used to combine two pipes of different sizes in the Oil & Gas Industry?
Explanation: A reducer is used to combine two pipes of different sizes in the Oil & Gas Industry.
Question 3:
Which type of fitting is typically used to allow branching of pipelines into two directions?
Explanation: A cross fitting is used to allow branching of pipelines into two directions in the Oil & Gas Industry.
Question 4:
Which fitting is commonly used to connect pipes to various equipment or instruments in the Oil & Gas Industry?
Explanation: A flange fitting is commonly used to connect pipes to various equipment or instruments in the Oil & Gas Industry.
Question 5:
What is the primary purpose of a valve in the Oil & Gas Industry?
Explanation: The primary purpose of a valve in the Oil & Gas Industry is to control or regulate the flow of fluids.
Question 6:
What is the function of a flange gasket in piping connections?
Explanation: A flange gasket is used to provide a leak-tight seal between flanges in piping connections.
Question 7:
Which type of fitting is used to terminate the end of a pipe in the Oil & Gas Industry?
Explanation: A cap fitting is used to terminate the end of a pipe in the Oil & Gas Industry.
Question 8:
What type of fitting is commonly used to join two pipes of the same diameter in a straight line?
Explanation: A coupling fitting is commonly used to join two pipes of the same diameter in a straight line.
Question 9:
Which piping fitting is used to provide a temporary connection for pressure testing or maintenance purposes?
Explanation: A plug fitting is used to provide a temporary connection for pressure testing or maintenance purposes.
Question 10:
What is the primary purpose of a union fitting in the Oil & Gas Industry?
Explanation: The primary purpose of a union fitting is to provide a leak-tight connection in the Oil & Gas Industry.