Introduction
The oil and gas industry is a vast and complex sector that relies heavily on precise measurements and data analysis to ensure efficient operations and safety. One crucial component in this industry, often overlooked but essential, is the sample cooler. Sample coolers play a pivotal role in maintaining the integrity of fluid samples collected during various processes. In this article, we will delve into the world of sample coolers, exploring their history, functions, working principles, types, applications, advantages, disadvantages, and the relevant codes and standards that govern their use.
Table of Contents
Don’t miss the Complete Course on Piping Engineering: Check Now
Enrollment Link
Brief History
The concept of sample coolers traces its roots to the early days of the oil and gas industry when accurate measurement and analysis of fluid samples became crucial. Initially, these coolers were rudimentary, using basic heat exchange principles to cool down samples. Over time, with advancements in materials and engineering, sample coolers evolved into highly efficient and reliable devices. Today, they are indispensable in ensuring the quality and accuracy of data obtained from fluid samples.
Basic Function and Working Principle
The primary function of sample coolers is to precisely control and maintain the temperature of fluid samples collected during various processes within the oil and gas industry. These fluid samples can include crude oil, natural gas, water, and various petroleum products. Temperature control is crucial because many analytical instruments and laboratory procedures require samples to be within a specific temperature range for accurate and reliable results.
Sample coolers are designed to address the following key functions:
- Prevent Sample Degradation: By cooling down hot fluid samples to the desired temperature, sample coolers prevent sample degradation. High temperatures can alter the composition and properties of fluids, leading to inaccurate analysis and potentially compromising safety.
- Maintain Sample Integrity: Accurate analysis of fluid samples depends on maintaining the integrity of the sample. Rapid temperature changes can cause phase separation, vaporization, or chemical reactions. Sample coolers ensure that the composition and properties of the sample remain stable.
- Facilitate Precise Measurements: Many analytical instruments used in the oil and gas industry, such as gas chromatographs, spectrometers, and viscosity meters, require samples to be at a specific temperature. Sample coolers provide the controlled environment necessary for precise measurements.
- Enable Safe Handling: Some fluids in the oil and gas industry can be volatile or hazardous. Cooling samples can reduce the risk of accidents by minimizing the release of volatile compounds or preventing the buildup of pressure in closed sample containers.
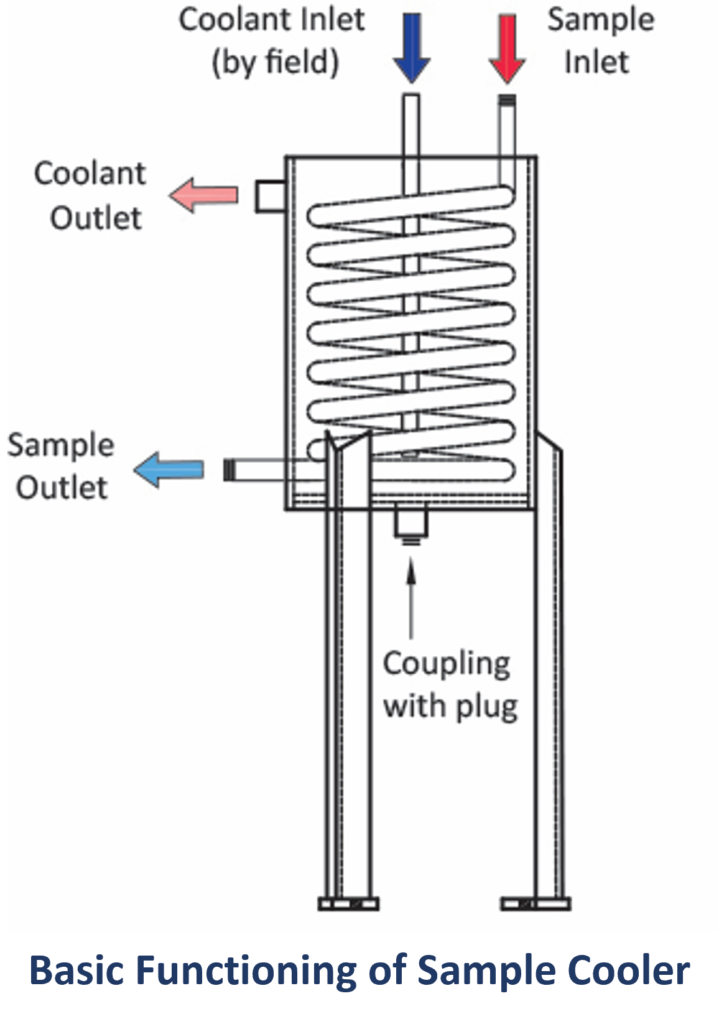
Working Principle of Sample Coolers
The working principle of a sample cooler is based on the fundamental concept of heat exchange. Sample coolers use a heat exchanger to transfer heat from the hot fluid sample to a cooling medium, typically water or air. The heat exchanger is the core component responsible for achieving controlled cooling. Here’s how the process works:
- Heat Exchanger Design: Sample coolers are equipped with a heat exchanger, which consists of a network of tubes or plates. These tubes or plates are in direct contact with the hot fluid sample.
- Hot Sample Flow: The hot fluid sample, which may be at an elevated temperature due to the process it has undergone, flows through the tubes or channels of the heat exchanger.
- Cooling Medium: Simultaneously, a cooling medium, often water, circulates around the outside of the tubes or plates. The cooling medium is at a lower temperature compared to the sample.
- Heat Transfer: Heat transfer occurs through the walls of the tubes or plates. The heat from the hot sample is conducted through the tube or plate walls and into the cooling medium.
- Temperature Control: The rate of heat transfer is controlled to achieve the desired temperature for the sample. This control can be achieved by adjusting the flow rate of the cooling medium, the surface area of the heat exchanger, or a combination of both.
- Cooled Sample Outlet: The sample, after passing through the heat exchanger, exits the cooler at the desired, controlled temperature. This cooled sample is then ready for analysis or further processing.
- Monitoring and Control: Sample coolers often include temperature sensors and control systems that continuously monitor and regulate the cooling process to maintain the sample at the desired temperature. This ensures that the sample remains within the specified range throughout the cooling process.
Don’t miss the Complete Course on Piping Engineering: Check Now
Enrollment Link
Types of Sample Coolers
Sample coolers come in various types, each designed to meet specific requirements and operating conditions. Understanding these types is crucial for selecting the right cooler for a particular application. Here’s an in-depth look at each type:
1. Shell and Tube Sample Cooler
Design: A shell and tube sample cooler consists of a bundle of tubes enclosed within a larger cylindrical shell. The tubes are typically arranged in parallel inside the shell.
Operation: Hot fluid samples flow through the tubes, while a cooling medium, often water, circulates around the outside of the tubes within the shell. Heat exchange occurs through the tube walls, cooling the sample to the desired temperature.
Advantages:
- Versatility: Shell and tube coolers are highly versatile and can handle a wide range of flow rates, temperatures, and pressures.
- Efficient Heat Transfer: This design allows for efficient heat transfer, making it suitable for applications with varying cooling requirements.
- Durability: They are robust and durable, making them suitable for harsh environments.
Applications: Shell and tube sample coolers find use in a variety of applications, including cooling samples of crude oil, natural gas, and produced water in upstream operations, as well as cooling hydrocarbon products in refineries.
2. Plate Heat Exchanger Sample Cooler
Design: Plate heat exchanger sample coolers consist of a stack of thin, corrugated metal plates. These plates have alternating hot and cold channels formed between them.
Operation: Hot fluid samples flow through one set of channels, while the cooling medium (usually water) flows through the adjacent channels. Heat transfer occurs across the thin plates, rapidly cooling the sample.
Advantages:
- Compact Design: Plate heat exchangers are known for their compact size, making them ideal for installations with limited space.
- Efficiency: They offer excellent heat transfer efficiency due to the large surface area provided by the stacked plates.
- Easy Maintenance: Plate heat exchangers are relatively easy to clean and maintain.
Applications: Plate heat exchanger sample coolers are commonly used in midstream operations to cool samples taken from pipelines, storage tanks, and terminals. Their compact design and efficiency make them suitable for these applications.
3. Finned Tube Sample Cooler
Design: Finned tube sample coolers consist of a tube with extended fins attached to the outer surface of the tube. These fins increase the heat transfer surface area.
Operation: Hot fluid samples flow through the tube, while the cooling medium circulates around the finned exterior surface. The increased surface area enhances heat transfer, facilitating rapid cooling.
Advantages:
- Enhanced Heat Transfer: The finned surface design significantly improves heat transfer, making finned tube coolers suitable for samples with high viscosity or fouling tendencies.
- Resistance to Fouling: The fins help resist fouling and scaling, prolonging the cooler’s efficiency.
- Robust Construction: They are robust and can withstand challenging operating conditions.
Applications: Finned tube sample coolers are often used in applications where the fluid samples have high viscosity or are prone to fouling. They are commonly employed in downstream operations, particularly in refineries and petrochemical plants.
4. Coiled Tube Sample Cooler
Design: Coiled tube sample coolers feature a single, continuous coil of tubing. The coiled design increases the surface area for heat transfer.
Operation: Hot fluid samples flow through the coiled tube, while the cooling medium circulates around the coil. Heat exchange occurs through the tube wall, cooling the sample.
Advantages:
- Compact and Space-Efficient: Coiled tube coolers are compact and take up minimal space, making them suitable for installations with space constraints.
- Efficient Cooling: They offer efficient cooling due to the extended surface area created by the coiled design.
- Simple Installation: Coiled tube coolers are relatively easy to install and maintain.
Applications: Coiled tube sample coolers are often used in applications where space is limited, such as offshore platforms or compact process units in refineries.
Each type of sample cooler offers distinct advantages and is chosen based on the specific requirements of the application. The selection process involves considering factors such as fluid properties, flow rates, temperature ranges, and space constraints to ensure that the sample cooler effectively fulfills its role in maintaining the integrity of fluid samples in the oil and gas industry.
Application of Sample Coolers
Sample coolers are versatile devices that find widespread use in various aspects of the oil and gas industry. They play a critical role in ensuring the accuracy of analytical data obtained from fluid samples. Here, we explore their applications in different sectors of the industry:
1. Upstream Operations
In the upstream segment of the oil and gas industry, which encompasses exploration and production, sample coolers are essential for several purposes:
a. Well Testing: During well testing operations, fluid samples are collected from production wells to assess reservoir characteristics, such as pressure, temperature, and fluid composition. These samples often come out at elevated temperatures due to the reservoir’s geothermal heat. Sample coolers rapidly lower the temperature of these samples to preserve their integrity for subsequent laboratory analysis. Accurate data from well tests is vital for reservoir management and production optimization.
b. Separator and Pipeline Sampling: Fluid samples are routinely collected from production separators, pipelines, and wellheads to monitor the quality and composition of produced fluids. Sample coolers ensure that these samples remain within specified temperature ranges, preventing phase changes or component separation that could skew analytical results.
c. Downhole Sampling: In some cases, downhole sampling tools are used to collect samples directly from the reservoir. These samples can be at extremely high temperatures and pressures. Sample coolers are employed to quickly and safely cool these samples for analysis, ensuring that the reservoir’s conditions are accurately captured.
2. Midstream Operations
In midstream operations, which involve the transportation and storage of hydrocarbons, sample coolers play a crucial role in quality control, custody transfer, and safety:
a. Pipeline Monitoring: Pipelines used to transport crude oil, natural gas, and refined products cover vast distances and are subject to varying environmental conditions. Sample coolers at key points along these pipelines help maintain sample integrity during transportation. This is vital for assessing product quality and ensuring compliance with regulatory standards.
b. Tank Farm and Terminal Sampling: At storage terminals and tank farms, sample coolers are used to collect representative samples from storage tanks. These samples are analyzed to verify product quality and consistency before transferring the product to customers or distribution pipelines.
c. Custody Transfer: During custody transfer operations, where ownership of hydrocarbons changes hands, accurate measurement of the transferred product is crucial. Sample coolers ensure that samples taken during custody transfer remain at specified temperatures, allowing for precise measurement and fair compensation between parties involved.
3. Downstream Operations
In downstream operations, which include refining and processing, sample coolers serve several important functions:
a. Refinery Processes: Refineries require precise analytical data to optimize their processes and ensure product quality. Sample coolers are used to cool samples taken from various points in the refining process, including distillation columns, reactors, and product streams. Accurate measurements help refine processes, reduce energy consumption, and meet product specifications.
b. Petrochemical Plants: Petrochemical plants produce a wide range of chemical products derived from hydrocarbons. Sample coolers are employed to cool samples from these processes, ensuring that the chemical composition and properties of the products are within specified limits. This is critical for quality control and meeting customer requirements.
c. Product Blending: In some cases, sample coolers are used to cool samples of different product streams before blending them to achieve the desired product specifications. Temperature control is vital to achieving consistent and marketable products.
Don’t miss the Complete Course on Piping Engineering: Check Now
Enrollment Link
Advantages & Disadvantages
A comprehensive evaluation of sample coolers must consider both their advantages and disadvantages:
Advantages
Advantage | Explanation |
---|---|
1. Accurate Measurements | Sample coolers ensure precise temperature control, leading to reliable analytical results. |
2. Sample Preservation | By preventing sample degradation due to temperature fluctuations, sample coolers maintain sample integrity. |
3. Versatility | Different types of sample coolers cater to a wide range of applications and fluid types. |
4. Compliance with Standards | Using sample coolers helps meet industry standards and regulations for sample handling and analysis. |
Disadvantages
Disadvantage | Explanation |
---|---|
1. Maintenance Requirements | Sample coolers require regular maintenance to ensure optimal performance. |
2. Initial Cost | The initial investment in sample coolers can be significant, especially for specialized units. |
3. Space Considerations | Some coolers may require ample space, which can be a limitation in certain installations. |
Associated Codes & Standards
To ensure the proper design, installation, and operation of sample coolers in the oil and gas industry, adherence to relevant codes and standards is essential. Some of the key standards include:
1. API RP 14J – Recommended Practice for Design and Hazards Analysis for Offshore Production Facilities
This API (American Petroleum Institute) recommended practice provides guidelines for designing and analyzing hazards associated with offshore production facilities, including recommendations for sample cooler installations.
2. ASTM D3700 – Standard Practice for Obtaining LPG Samples Using a Floating Piston Cylinder
ASTM D3700 outlines procedures for obtaining liquid petroleum gas (LPG) samples, including the use of sample coolers to maintain sample integrity during collection.
3. ISO 3171 – Petroleum liquids – Automatic pipeline sampling
ISO 3171 specifies requirements for automatic pipeline sampling, including the use of sample coolers to control sample temperature and prevent evaporation.
Conclusion
Sample coolers may seem like a minor component in the vast landscape of the oil and gas industry, but their role in ensuring accurate measurements and maintaining sample integrity is indispensable. From their historical evolution to their diverse applications and adherence to industry standards, sample coolers play a vital part in optimizing operations and ensuring the quality of hydrocarbon products. As technology continues to advance, these unassuming devices will continue to evolve, contributing to the industry’s efficiency and safety.
In an industry where precision is paramount, sample coolers stand as silent sentinels, ensuring that the data collected today paves the way for a more efficient and sustainable future in the world of oil and gas.
FAQs
- What is the primary purpose of a sample cooler in the oil and gas industry?
- A sample cooler’s primary purpose in the oil and gas industry is to maintain the temperature of fluid samples at a specific, controlled level. This temperature control is crucial for accurate measurements and data analysis.
- What types of sample coolers are commonly used in the industry, and how do they differ from each other?
- There are several types of sample coolers used in the industry, including shell and tube sample coolers, plate heat exchanger sample coolers, and finned tube sample coolers. They differ in design and are chosen based on factors such as application, fluid type, and operating conditions.
- Where are sample coolers typically employed within the oil and gas industry’s various sectors?
- Sample coolers find applications in all three major sectors of the oil and gas industry—upstream, midstream, and downstream. They are used to cool samples collected from wellheads, pipelines, storage tanks, refineries, and petrochemical plants to ensure accurate analysis and quality control.
- What are the advantages of using sample coolers in oil and gas operations?
- Sample coolers offer several advantages, including precise temperature control, preservation of sample integrity, versatility for various applications, and compliance with industry standards and regulations. They contribute to more accurate data analysis and process optimization.
- What are the key industry standards and codes that govern the use of sample coolers in the oil and gas sector?
- Industry standards and codes, such as API RP 14J, ASTM D3700, and ISO 3171, provide guidelines for the proper design, installation, and operation of sample coolers. Adherence to these standards is essential to ensure the reliability and safety of sample collection and analysis.
Recommended courses (Published on EPCLand)
- Basics of Piping Engineering
- Piping Layout Engineering
- Piping Material Engineering
- Piping Stress Analysis
- Complete Course on Piping Engineering
- Material Requisitions
- Piping Material Specifications
- Valve Material Specifications
Don’t miss the published articles on following:
Don’t miss the Complete Course on Piping Engineering: Check Now
Enrollment Link
Attempt Quiz
Question 1:
What is the primary purpose of a Sample Cooler in the Oil & Gas Industry?
Explanation: A Sample Cooler is primarily used to cool and condition process samples in the Oil & Gas Industry.
Question 2:
Which type of fluids are typically processed by Sample Coolers?
Explanation: Sample Coolers are used to process both gases and liquids in the Oil & Gas Industry.
Question 3:
What is the purpose of temperature control in a Sample Cooler?
Explanation: Temperature control in a Sample Cooler is used to maintain sample temperature within a specific range for accurate analysis.
Question 4:
Which material is commonly used for the heat exchange surfaces of Sample Coolers?
Explanation: Stainless Steel is commonly used for the heat exchange surfaces of Sample Coolers due to its corrosion resistance and durability.
Question 5:
What is the purpose of a Sample Cooler’s insulation?
Explanation: Insulation in a Sample Cooler is used to maintain sample temperature and reduce heat loss.
Question 6:
Which industry standards are relevant for the design and manufacturing of Sample Coolers?
Explanation: ASME B&PV Code is relevant for the design and manufacturing of Sample Coolers.
Question 7:
What is the typical flow rate range for Sample Coolers in the Oil & Gas Industry?
Explanation: The typical flow rate range for Sample Coolers in the Oil & Gas Industry is 1-50 liters per minute.
Question 8:
What is the main advantage of using Sample Coolers in oil and gas projects?
Explanation: The main advantage of using Sample Coolers in oil and gas projects is improved safety by cooling and conditioning process samples.
Question 9:
Which component in a Sample Cooler is responsible for cooling the sample?
Explanation: The heat exchange surface in a Sample Cooler is responsible for cooling the sample.
Question 10:
What is the typical installation location of a Sample Cooler in an oil and gas facility?
Explanation: A Sample Cooler is typically installed near the wellhead or processing equipment in an oil and gas facility.