I. Introduction
In the oil and gas industry, the efficient control of fluid flows is paramount to ensure the safe and productive operation of various processes. One critical component that plays a vital role in this regard is the Steam Manifold. This article delves into the world of Steam Manifolds, exploring their history, functions, types, applications, advantages, disadvantages, and the associated codes and standards that govern their usage in the oil and gas sector.
Table of Contents
Don’t miss the Complete Course on Piping Engineering: Check Now
Enrollment Link
II. Brief History
Steam Manifolds have a rich history that dates back to the early days of industrialization. The concept of manifolds, in general, can be traced to the need for efficient distribution of fluids and gases in industrial processes. Steam, being one of the earliest sources of power in the industry, necessitated the development of Steam Manifolds for its controlled distribution. Over time, these manifolds have evolved and adapted to meet the specific demands of the oil and gas sector, becoming an integral part of various projects.
III. Basic Function and Working Principle
The primary function of a Steam Manifold is to efficiently distribute steam from a single source to multiple locations or pieces of equipment within an oil and gas facility. Think of it as the central hub for steam distribution, much like a branching network of pipes that directs steam to where it’s needed. This centralization of steam distribution serves several crucial purposes:
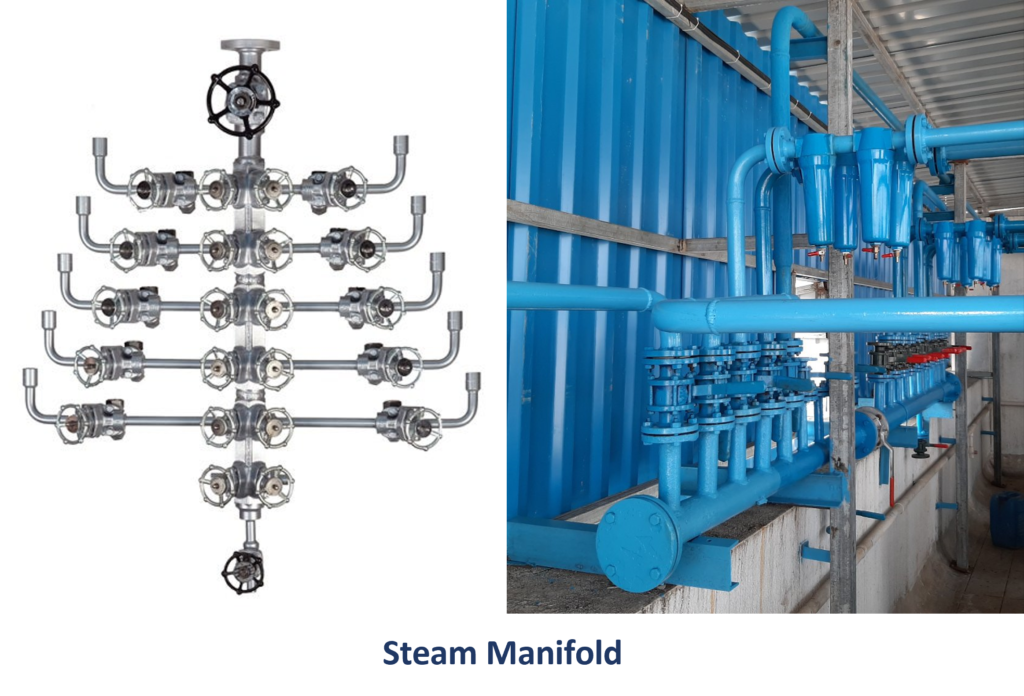
1. Controlled Steam Flow:
Steam Manifolds allow for precise control over the flow of steam. By adjusting the valves associated with each outlet or branch, operators can regulate the amount of steam sent to different processes or equipment. This level of control is essential to ensure that each part of the facility receives the exact amount of steam required for optimal performance.
2. Flexibility:
Steam Manifolds offer flexibility in managing steam distribution. They can redirect steam to different areas of the facility as needed, making them adaptable to changing operational requirements.
3. Safety:
Safety is a paramount concern in the oil and gas industry. Steam Manifolds help maintain safety by providing a centralized point of control. In case of emergencies or the need for rapid shutdowns, operators can quickly isolate specific sections of the facility by closing the relevant valves on the manifold.
4. Efficiency:
Efficiency is a key consideration in industrial processes. Steam Manifolds help optimize energy use by ensuring that steam is only delivered where and when it’s required. This prevents unnecessary steam wastage and reduces operational costs.
Working Principle of Steam Manifolds
To understand the working principle of Steam Manifolds, let’s break it down step by step:
1. Steam Generation:
The process begins with the generation of steam in a central boiler or steam generator. Steam is typically produced by heating water using combustion, electricity, or other heat sources. The steam generated in the boiler is then conveyed to the Steam Manifold.
2. Steam Manifold Configuration:
The Steam Manifold is a complex arrangement of pipes, valves, and outlets. It is designed to receive high-pressure steam from the boiler and distribute it to various sections of the facility. The configuration of the manifold may vary depending on the specific requirements of the project. Key components of the manifold include:
- Inlet Connection: This is where high-pressure steam enters the manifold from the boiler.
- Outlet Connections: These are the branches or outlets through which steam is distributed to different parts of the facility. Each outlet is equipped with a valve to control the flow of steam.
- Valves: Valves within the manifold are crucial for regulating steam flow. Motor-operated valves (MOVs) are often used for precise control. These valves can be remotely operated to adjust steam flow rates.
3. Steam Distribution:
As steam enters the manifold from the inlet connection, it is directed through the appropriate outlet(s) based on the operational requirements. The valves associated with each outlet can be adjusted to control the volume of steam flowing to that particular location.
4. Steam Utilization:
The steam distributed through the outlets is utilized for various processes and functions within the oil and gas facility. This can include steam injection for enhanced oil recovery, steam heating, steam tracing to maintain pipeline temperatures, and more.
5. Monitoring and Control:
Modern Steam Manifolds are often equipped with instrumentation and control systems that allow operators to monitor and adjust steam flow remotely. These systems may include sensors to measure temperature, pressure, and flow rates, providing real-time data for decision-making.
6. Safety Considerations:
Safety is paramount in steam distribution systems. Steam Manifolds are designed with safety features, including pressure relief valves and emergency shutdown mechanisms. In case of abnormal conditions, these safety measures can be activated to protect equipment and personnel.
IV. Types of Steam Manifolds
Steam Manifolds come in various configurations, each designed to suit specific applications within the oil and gas industry. Understanding these types is crucial for selecting the appropriate manifold for a given project. Below, we’ll explore the key types of Steam Manifolds in more detail:
1. Main Steam Manifold
Main Function: The primary role of the Main Steam Manifold is to distribute high-pressure steam from a central boiler or steam generator to various sections of an oil and gas facility. It serves as the initial point of distribution, splitting the steam into multiple branches for further delivery.
Design and Features:
- Typically located near the boiler or steam generator.
- Equipped with a large number of outlets, each connected to different sections or units within the facility.
- Valves, such as gate valves or motor-operated valves (MOVs), control the flow of steam to individual branches.
Applications:
- Main Steam Manifolds are vital in power generation facilities where steam turbines are used to generate electricity.
- They are also utilized in various heating processes, ensuring a steady supply of steam to meet the facility’s heating requirements.
2. Branch Steam Manifold
Main Function: Branch Steam Manifolds are secondary distribution points that receive steam from the Main Steam Manifold. They play a crucial role in delivering steam to localized areas or specific equipment within a facility.
Design and Features:
- Connected to the Main Steam Manifold through inlet connections.
- Equipped with multiple outlets to distribute steam to different sections or equipment.
- Valves are used to control steam flow to individual branches, allowing for precise regulation.
Applications:
- Branch Steam Manifolds are commonly found in refineries, petrochemical plants, and industrial facilities where steam is required for various processes.
- They are used to provide steam to equipment like heat exchangers, reactors, and distillation columns.
3. Process-specific Steam Manifold
Main Function: Process-specific Steam Manifolds are customized to meet the unique requirements of specific applications or equipment within the oil and gas industry. Unlike Main and Branch Steam Manifolds, which serve general distribution purposes, process-specific manifolds are tailored to provide precise control and efficiency for specialized processes.
Design and Features:
- Custom-engineered to meet the specific needs of the process or equipment.
- May have unique configurations, valve types, and materials based on the application.
- Designed for optimized performance, energy efficiency, and safety within the defined process.
Applications:
- Process-specific Steam Manifolds are used in a wide range of applications, including steam injection for enhanced oil recovery (EOR), process heating in chemical plants, and sterilization processes in pharmaceutical manufacturing.
- They are critical for ensuring that steam is delivered accurately, at the right temperature, and under the necessary pressure for the intended process.
4. Instrument Steam Manifold
Main Function: Instrument Steam Manifolds are designed specifically for the control and measurement of steam flow to instrumentation and devices within the oil and gas industry. They are essential for maintaining precision in measuring and controlling steam-related variables.
Design and Features:
- Compact and often modular in design to accommodate various instruments.
- Equipped with numerous outlets and connections for instrument tubing and fittings.
- Valves and other control devices are integrated to ensure precise regulation of steam flow to instruments.
Applications:
- Instrument Steam Manifolds are primarily used in applications where accurate measurements of temperature, pressure, or flow are critical, such as control loops, analytical instrumentation, and safety systems.
- They are commonly found in oil refineries, natural gas processing plants, and other facilities where instrumentation is vital for process control and safety.
Each type of Steam Manifold serves a unique purpose in the oil and gas industry, ensuring that steam is efficiently distributed to meet the specific requirements of various processes and equipment. Selecting the right type of manifold is essential for optimizing operational efficiency, energy conservation, and safety within a facility.
Don’t miss the Complete Course on Piping Engineering: Check Now
Enrollment Link
V. Applications of Steam Manifolds
Steam Manifolds serve a wide range of critical applications in the oil and gas sector. These applications are essential for various processes and operations, and Steam Manifolds play a pivotal role in ensuring their efficiency and reliability.
1. Steam Injection for Enhanced Oil Recovery (EOR)
In the upstream sector of the oil and gas industry, one of the most vital applications of Steam Manifolds is in Enhanced Oil Recovery (EOR). Many oil reservoirs contain heavy or viscous crude oil that is challenging to extract using traditional methods. Steam Manifolds are used to inject high-pressure steam directly into the reservoir. This injected steam heats the oil, reducing its viscosity and making it easier to flow and extract. This process significantly enhances the recovery rate of oil from the reservoir, increasing production and extending the life of oil fields.
2. Steam Heating and Condensation
In the downstream sector, particularly in refineries and petrochemical plants, Steam Manifolds are employed for steam heating and condensation processes. These processes involve the use of steam to maintain or raise the temperature of various fluids and substances. Steam Manifolds ensure that steam is distributed precisely to the equipment and pipelines that require heating. For example, they play a crucial role in maintaining the temperature of crude oil during transportation through pipelines, preventing it from solidifying and causing blockages.
Additionally, in distillation and separation processes within refineries, Steam Manifolds are used for precise control over the temperature of distillation columns, condensers, and other equipment. This control is essential for separating crude oil into its various components, such as gasoline, diesel, and jet fuel.
3. Steam Turbine Drives
In power generation facilities associated with oil and gas projects, Steam Manifolds supply steam to steam turbines used for electricity generation. Steam turbines are commonly employed in combined-cycle power plants, where they complement gas turbines to maximize energy efficiency. Steam Manifolds ensure that the right amount of high-pressure steam is delivered to the turbines, enabling them to produce electricity by turning generators. This application highlights the versatility of Steam Manifolds, which are not limited to the oil and gas processing itself but are also integral to power generation.
4. Process Sterilization
In the pharmaceutical and chemical industries, maintaining strict sterility is crucial. Steam is widely used for sterilizing equipment, vessels, and pharmaceutical products. Steam Manifolds play a vital role in this context by delivering steam to autoclaves and sterilization chambers. Precise control over steam pressure and temperature is essential to ensure the effectiveness of the sterilization process and the safety of the products.
5. Steam Tracing
In the oil and gas industry, pipelines and equipment are often exposed to extreme temperatures, including freezing conditions. Steam tracing is the practice of running steam lines alongside pipes or equipment to maintain their temperature and prevent the freezing of fluids within them. Steam Manifolds provide the necessary steam for tracing systems, ensuring that critical pipelines and equipment remain operational in cold climates. This application is particularly important in regions with harsh weather conditions, such as those found in many oil and gas production areas.
VI. Advantages & Disadvantages
Advantages of Using Steam Manifolds
Steam Manifolds offer several advantages in oil and gas projects:
1. Precise Control
Steam Manifolds allow for precise control over steam flow, ensuring that each process or piece of equipment receives the required amount of steam.
2. Energy Efficiency
They contribute to energy efficiency by preventing steam wastage and optimizing the use of steam for heating and other purposes.
3. Safety
Properly designed and maintained Steam Manifolds enhance safety by minimizing the risk of steam-related accidents or leaks.
Disadvantages and Challenges
1. Maintenance
Steam Manifolds require regular maintenance to ensure they function correctly. This can add to operational costs.
2. Initial Investment
The installation of Steam Manifolds involves a significant initial investment in terms of equipment and engineering.
3. Complexity
Complex systems with numerous valves and controls can be challenging to operate and maintain.
VII. Associated Codes & Standards
The use of Steam Manifolds in the oil and gas industry is governed by a set of codes and standards to ensure safety, reliability, and compliance with industry best practices. Some of the key codes and standards include:
1. ASME B31.1
The ASME B31.1 code covers the design and construction of power piping systems, which may include Steam Manifolds.
2. API 520
API 520 provides guidelines for the sizing and selection of pressure-relief devices, including those used in Steam Manifolds to ensure overpressure protection.
3. ISA-75.19.01
ISA-75.19.01 standardizes the design and installation of instrument tubing and fittings, which are integral components of Steam Manifolds for control and measurement.
4. National Fire Protection Association (NFPA) Codes
Various NFPA codes, such as NFPA 85 (Boiler and Combustion Systems Hazards Code), contain requirements related to the safe operation of boilers and steam systems.
VIII. Conclusion
Steam Manifolds are indispensable components in the oil and gas industry, facilitating the controlled distribution of steam for various applications. Their history, working principles, types, applications, advantages, disadvantages, and the importance of adhering to industry codes and standards highlight their critical role in ensuring safe and efficient operations within the sector. As technology continues to evolve, Steam Manifolds will likely see further advancements, further enhancing their contribution to the industry’s success.
In conclusion, understanding the functions and significance of Steam Manifolds is essential for professionals involved in oil and gas projects, as they are the backbone of steam distribution in these operations, impacting everything from production to safety and environmental compliance.
FAQs
1. What is a Steam Manifold, and how does it differ from a regular pipe distribution system?
- A Steam Manifold is a specialized system used in the oil and gas industry to distribute steam from a single source to multiple locations or equipment. It differs from a regular pipe distribution system by offering precise control over steam flow, making it ideal for various applications that require accurate temperature and pressure regulation.
2. What are the primary applications of Steam Manifolds in the oil and gas sector?
- Steam Manifolds have diverse applications, including steam injection for enhanced oil recovery, steam heating and condensation in refineries, powering steam turbines for electricity generation, sterilization in pharmaceutical and chemical industries, and steam tracing to prevent pipeline freezing.
3. Are there specific safety considerations when using Steam Manifolds in oil and gas projects?
- Yes, safety is paramount. Regular maintenance and adherence to safety standards are crucial. Steam Manifolds should be designed and operated to prevent steam-related accidents, leaks, and overpressure situations. Compliance with industry-specific codes and standards, such as NFPA and ASME, is essential for safety.
4. What types of Steam Manifolds are commonly used, and how do they differ?
- Common types of Steam Manifolds include main steam manifolds, branch steam manifolds, and process-specific steam manifolds. Main steam manifolds distribute high-pressure steam from a central source, while branch manifolds distribute it to different sections. Process-specific manifolds are tailored to specific applications, offering precise control over steam distribution.
5. What are the advantages and disadvantages of using Steam Manifolds in oil and gas projects?
- The advantages of Steam Manifolds include precise control over steam flow, energy efficiency, and enhanced safety. However, they require regular maintenance, involve a significant initial investment, and can become complex in systems with numerous controls and valves. Proper planning and maintenance are essential to reap the benefits while managing the challenges.
Recommended courses (Published on EPCLand)
- Basics of Piping Engineering
- Piping Layout Engineering
- Piping Material Engineering
- Piping Stress Analysis
- Complete Course on Piping Engineering
- Material Requisitions
- Piping Material Specifications
- Valve Material Specifications
Don’t miss the published articles on following:
Don’t miss the Complete Course on Piping Engineering: Check Now
Enrollment Link
Attempt Quiz
Question 1:
What is the primary purpose of a Steam Manifold in an oil & gas industry project?
Explanation: A Steam Manifold is primarily used to regulate the flow of steam in oil & gas industry projects.
Question 2:
What material is commonly used to construct Steam Manifolds for high-temperature applications?
Explanation: Stainless Steel is commonly used in the construction of Steam Manifolds for high-temperature applications due to its strength and corrosion resistance.
Question 3:
What function does insulation serve in Steam Manifolds?
Explanation: Insulation in Steam Manifolds helps maintain steam temperature and prevent heat loss.
Question 4:
What is the purpose of steam traps in a Steam Manifold system?
Explanation: Steam traps in a Steam Manifold system are used to remove condensate and prevent steam loss.
Question 5:
What is the typical temperature range that Steam Manifolds are designed to handle?
Explanation: Steam Manifolds are designed to handle high-temperature steam, typically above 100°C.
Question 6:
What is the main advantage of using Steam Manifolds in oil & gas industry projects?
Explanation: The main advantage of using Steam Manifolds is efficient distribution and control of steam in oil & gas industry projects.
Question 7:
What industry standards are commonly followed in the construction of Steam Manifolds?
Explanation: Common industry standards for the construction of Steam Manifolds include ASME B31.1 and ASME B31.3.
Question 8:
What role do pressure relief valves play in a Steam Manifold system?
Explanation: Pressure relief valves in a Steam Manifold system ensure safety by preventing overpressure.
Question 9:
What is the purpose of steam tracing in Steam Manifold systems?
Explanation: Steam tracing in Steam Manifold systems is used to maintain steam temperature in pipelines.
Question 10:
What is the typical lifespan of well-maintained Steam Manifolds in oil & gas industry projects?
Explanation: Well-maintained Steam Manifolds in oil & gas industry projects typically have a lifespan ranging from 15 to 20 years.