Ultrasonic Testing (UT) is a widely used non-destructive testing method that utilizes high-frequency sound waves to detect flaws, defects, and irregularities in materials and structures. This technique has applications across various industries, including manufacturing, construction, aerospace, and more. In this article, we will delve into the details of Ultrasonic Testing, its benefits, limitations, and FAQs.
Table of Contents
Don’t miss the Complete Course on Piping Engineering: Check Now
By EPCLand.com
Understanding Ultrasonic Testing
Ultrasonic Testing employs ultrasonic waves that travel through a material, reflecting off its internal features and creating echoes. By analyzing these echoes, technicians can determine the material’s thickness, identify defects such as cracks or voids, and assess the overall structural integrity. This non-invasive method is particularly valuable for ensuring the reliability and safety of critical components.
The UT Process
- Generation of Ultrasonic Waves: In UT, a transducer generates ultrasonic waves that are transmitted into the material being tested.
- Propagation and Reflection: These waves propagate through the material until they encounter a boundary between different materials or an internal flaw. Upon encountering these boundaries, some of the waves are reflected back to the transducer.
- Echo Formation: The reflected waves create echoes that are received by the transducer.
- Signal Analysis: The time taken for the echoes to return and their amplitude provide information about the material’s characteristics, such as its thickness and the presence of defects.
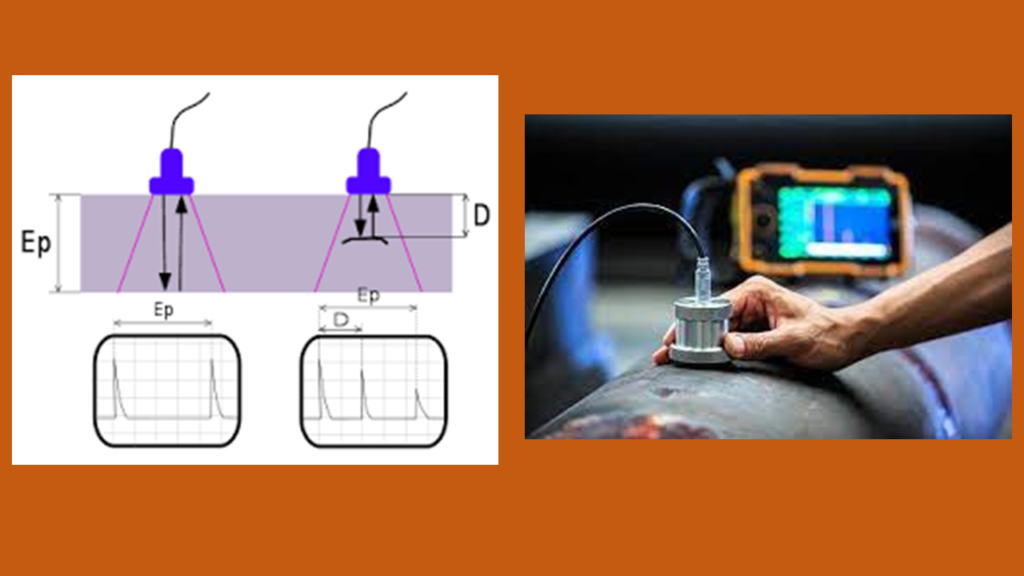
Benefits of Ultrasonic Testing
Ultrasonic Testing offers numerous advantages, making it a preferred choice for quality control and safety assessment:
- Accuracy: UT can detect small defects with high precision, ensuring thorough inspections.
- Depth Assessment: The technique allows for the measurement of flaw depth, helping technicians understand the severity of defects.
- Versatility: It can be used on a variety of materials, including metals, plastics, ceramics, and composites.
- Real-time Results: UT provides instant results, enabling quick decision-making in time-sensitive scenarios.
Limitations of Ultrasonic Testing
While Ultrasonic Testing is highly effective, there are certain limitations to consider:
- Surface Condition: UT may struggle to detect defects near rough surfaces or in materials with irregular grain structures.
- Operator Skill: Proper training is required to interpret results accurately and avoid false positives or negatives.
- Thickness Constraints: UT’s effectiveness can be limited by the material’s thickness, as very thick materials may attenuate the ultrasonic waves.
Applications of Ultrasonic Testing
Ultrasonic Testing finds applications in various industries:
Manufacturing
In manufacturing, UT is used to ensure the quality of products during production. It helps detect internal defects that could compromise the integrity of the final product.
Aerospace
Aerospace companies rely on UT to inspect critical components of aircraft, such as engine parts and structural elements. Ensuring the absence of defects is essential to guarantee passenger safety.
Oil and Gas
UT plays a crucial role in the oil and gas industry by inspecting pipelines and storage tanks for corrosion, cracks, and leaks. This prevents potential environmental disasters.
Construction
In the construction sector, UT is used to assess the structural integrity of buildings, bridges, and other infrastructure projects.
Don’t miss the Complete Course on Piping Engineering: Check Now
By EPCLand.com
Pros and cons of Ultrasonic Testing (UT):
Pros of Ultrasonic Testing (UT) | Cons of Ultrasonic Testing (UT) |
---|---|
Accurate Detection: Can detect small defects with high precision. | Surface Condition: Struggles to detect defects near rough surfaces or irregular grain structures. |
Depth Assessment: Provides information about flaw depth, aiding in defect severity evaluation. | Operator Skill: Requires trained technicians to interpret results accurately and avoid false positives/negatives. |
Versatility: Applicable to various materials such as metals, plastics, ceramics, and composites. | Thickness Constraints: Effectiveness limited by material thickness; ultrasonic waves may attenuate in very thick materials. |
Real-time Results: Offers instant feedback, enabling quick decision-making in time-sensitive scenarios. | Equipment Cost: Initial investment in equipment and training can be significant. |
Non-Destructive: Does not cause damage to the tested material, making it suitable for critical components. | Surface Preparation: Requires adequate surface preparation for reliable results, which can be time-consuming. |
Depth Measurement: Can measure the depth of flaws, aiding in assessing structural integrity. | Limited to Access: Challenging to inspect components with limited access points. |
Subsurface Defects: Capable of detecting defects both at the surface and within the material. | Material Properties: Effectiveness can vary based on material properties like density and sound velocity. |
Application Range: Widely used in industries like manufacturing, aerospace, construction, and more. | Calibration: Regular calibration of equipment is necessary for accurate results. |
Safety: Non-hazardous to operators, making it a safer testing method. | Environmental Conditions: Results may be affected by temperature, humidity, and other environmental factors. |
It’s important to note that the pros and cons mentioned here are general and may vary based on specific testing scenarios and equipment used.
Conclusion
Ultrasonic Testing is a versatile and powerful non-destructive testing technique that plays a crucial role in ensuring the quality, safety, and reliability of materials and structures across various industries. Its ability to accurately detect defects and flaws, coupled with its real-time results, makes it an indispensable tool for modern quality control and inspection processes. Understanding the principles, benefits, and limitations of Ultrasonic Testing is essential for professionals in fields where materials’ integrity is of utmost importance.
FAQs about Ultrasonic Testing
Q1: What is the primary principle behind Ultrasonic Testing?
A1: Ultrasonic Testing (UT) operates on the principle of sound wave propagation. High-frequency sound waves are introduced into a material, and these waves travel through the material until they encounter a boundary between materials or an internal flaw. When the waves encounter these boundaries or defects, they reflect back to the transducer, creating echoes. By analyzing the time it takes for these echoes to return and their amplitude, technicians can assess the material’s characteristics, such as thickness and the presence of defects.
Q2: Is UT suitable for all types of materials?
A2: Yes, Ultrasonic Testing is suitable for a wide range of materials, including metals, plastics, ceramics, and composites. It can be applied to both conductive and non-conductive materials, making it a versatile testing method for various industries.
Q3: Can UT detect both surface and subsurface defects?
A3: Absolutely. Ultrasonic Testing is capable of detecting defects both at the surface and within the material. This ability to assess both surface and subsurface conditions makes UT particularly valuable for identifying hidden flaws that might compromise the structural integrity of materials or components.
Q4: Is UT a time-consuming process?
A4: No, Ultrasonic Testing provides real-time results, making it an efficient and rapid testing method. The echoes generated by the ultrasonic waves are analyzed in real-time, allowing technicians to quickly assess the condition of the material being tested. This speed is advantageous, especially in industries where timely assessments are critical.
Q5: How is UT different from Radiographic Testing (RT)?
A5: While both Ultrasonic Testing (UT) and Radiographic Testing (RT) are non-destructive testing methods, they use different principles and techniques. UT relies on sound waves that travel through the material and create echoes at boundaries or defects. On the other hand, RT employs X-rays or gamma rays to penetrate materials, creating a shadow image on a radiographic film or detector. RT is more suitable for thicker materials and provides a 2D image of the internal structure, while UT offers real-time results and can assess both surface and subsurface conditions.
Recommended courses (Published on EPCLand)
- Basics of Piping Engineering
- Piping Layout Engineering
- Piping Material Engineering
- Piping Stress Analysis
- Complete Course on Piping Engineering
- Material Requisitions
- Piping Material Specifications
- Valve Material Specifications
Don’t miss the published articles on following:
Related Video
Attempt Quiz
Question 1:
What is Ultrasonic Testing (UT) in Non-Destructive Testing (NDT)?
Explanation: Ultrasonic Testing (UT) is a non-destructive testing method that uses high-frequency sound waves to detect and characterize flaws, thickness variations, and other internal features in materials without causing damage.
Question 2:
How does Ultrasonic Testing work?
Explanation: Ultrasonic Testing works by transmitting high-frequency sound waves into the material. These waves travel through the material and bounce back (reflect) when they encounter changes in acoustic impedance, such as the presence of defects or boundaries. The reflected waves are then analyzed to identify and characterize flaws.
Question 3:
What type of defects can Ultrasonic Testing detect?
Explanation: Ultrasonic Testing can detect a variety of defects, including both surface and subsurface defects such as cracks, voids, inclusions, and discontinuities.
Question 4:
What is the advantage of using Ultrasonic Testing over other NDT methods?
Explanation: Ultrasonic Testing offers the advantage of providing precise depth measurements of defects, allowing inspectors to assess not only the presence of defects but also their location within the material.
Question 5:
What is the term used for the instrument that generates and receives ultrasonic waves in UT?
Explanation: The instrument that generates and receives ultrasonic waves in Ultrasonic Testing is called an “Ultrasonic Transducer.” It converts electrical energy into mechanical vibrations and vice versa to send and receive sound waves in the material.