Introduction
Welded pipes play a pivotal role in the world of oil and gas industry projects. These pipes are the arteries that transport the lifeblood of our modern society—crude oil and natural gas. This comprehensive article explores the significance of welded pipes in the oil and gas sector. We’ll delve into their history, how they function, the various types available, their diverse applications, and the advantages and disadvantages associated with their use. Additionally, we’ll touch upon the codes and standards that regulate these vital components and address frequently asked questions for a complete understanding.
Table of Contents
Don’t miss the Complete Course on Piping Engineering: Check Now
Enrollment Link
Brief History
Origins of Welded Pipes
Welded pipes have a rich history dating back to ancient times when various civilizations used metal pipes for water supply and irrigation. However, it was during the Industrial Revolution that significant advancements in welding technology led to the mass production of welded steel pipes. This development transformed the way industries, including oil and gas, transported fluids over long distances.
Milestones in Welded Pipe Development
- Late 19th Century: The introduction of arc welding processes such as the Shielded Metal Arc Welding (SMAW) allowed for the creation of stronger and more durable welded pipes.
- Early 20th Century: Electric resistance welding (ERW) was developed, enabling the production of high-frequency, precision-welded pipes.
- Mid-20th Century: The advent of submerged arc welding (SAW) further improved pipe quality and efficiency.
- Modern Era: Welded pipes have become the industry standard for the transmission of oil and gas due to their durability and cost-effectiveness.
Basic Function and Working Principle
Welded pipes serve as conduits for the transportation of oil and gas from extraction sites to refineries and end-users. The fundamental working principle revolves around creating a continuous, strong, and leak-proof pipeline that can withstand high-pressure, harsh environments, and various corrosive elements. Here’s a closer look at how welded pipes achieve this:
How Welded Pipes Work
Welded pipes are made by joining two pipe sections together through a welding process. The most common methods are:
- Electric Resistance Welding (ERW): This process involves passing a high-frequency electric current through the edges of the steel strips to create a weld.
- Submerged Arc Welding (SAW): In this method, a consumable wire electrode is fed continuously, creating a submerged arc that melts the edges of the pipe sections and fuses them together.
- High-Frequency Induction (HFI) Welding: HFI welding uses electromagnetic induction to heat the edges of the pipe sections, forming a strong weld.
Key Features of Welded Pipe Material
- Steel: Welded pipes are primarily made of steel due to its strength, durability, and resistance to corrosion.
- Anti-Corrosion Coatings: To enhance longevity and corrosion resistance, welded pipes are often coated with materials such as epoxy or polyethylene.
Advantages of Using Welded Pipes
- Strength and Durability: Welded pipes can withstand extreme pressure and temperature conditions, making them ideal for oil and gas transport.
- Cost-Effective: They are more affordable than seamless pipes, offering a cost-effective solution for long-distance transportation.
- Customization: Welded pipes come in various sizes, grades, and coatings to suit specific project requirements.
- High Production Efficiency: The manufacturing process of welded pipes allows for high production rates, meeting the demands of the oil and gas industry.
Manufacturing Process of Welded Pipes
Welded pipes are a critical component in various industries, with a significant presence in the oil and gas, construction, and manufacturing sectors. Understanding the manufacturing process of welded pipes is essential for those involved in their production or utilization. This process involves several key steps that ensure the creation of durable and reliable pipes for various applications. In this article, we will delve into the detailed manufacturing process of welded pipes, considering various welding methods commonly used.
Step 1: Material Selection
The process begins with the selection of appropriate raw materials. Welded pipes are predominantly made from carbon steel due to its strength, durability, and suitability for welding. The choice of steel grade depends on the intended application and the environmental conditions the pipe will be exposed to.
Step 2: Coil Preparation
The selected steel coils are uncoiled and subjected to various preparatory steps. This includes straightening and leveling the coil to remove any deformities, ensuring a consistent and even feed into the pipe manufacturing process.
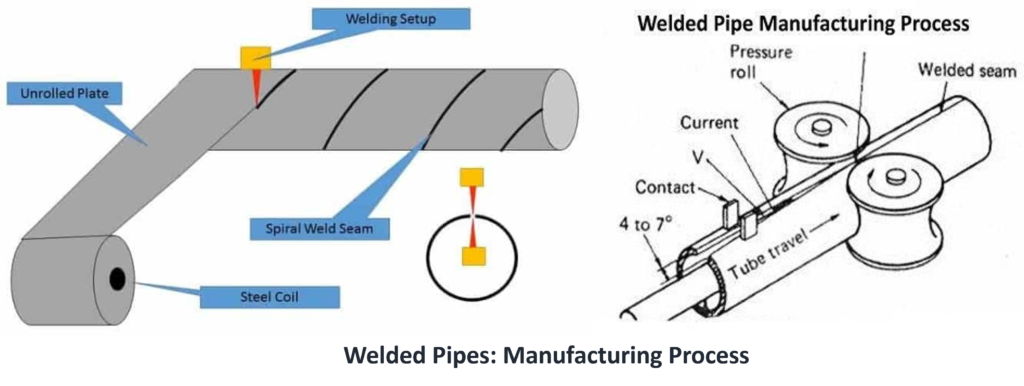
Step 3: Edge Milling
In this step, the edges of the steel strip are milled to form a precise, smooth edge. The quality of the edge is critical, as it significantly impacts the quality of the weld. Proper edge milling ensures a strong and leak-proof seam.
Step 4: Skelp Formation
The milled steel strip, now known as skelp, is shaped into a cylindrical form. This is achieved by passing the skelp through a series of rollers to bend it into the desired shape. The edges of the skelp are brought together, ready for welding.
Don’t miss the Complete Course on Piping Engineering: Check Now
Enrollment Link
Step 5: Welding
Welding is the central step in the manufacturing process of welded pipes. There are several methods for welding, each with its advantages and ideal applications:
a. Electric Resistance Welding (ERW)
ERW welding involves passing a high-frequency electric current through the edges of the steel skelp. This creates the necessary heat for fusion, resulting in a strong and continuous weld. ERW is commonly used for pipes that will transport low to medium pressure fluids.
b. Submerged Arc Welding (SAW)
SAW is employed for welding thick-walled pipes and for high-pressure applications. In this method, a consumable wire electrode is continuously fed into the weld zone. A granular flux shields the weld, creating a submerged arc that melts the edges of the skelp and forms a robust weld.
c. High-Frequency Induction (HFI) Welding
HFI welding uses electromagnetic induction to heat the edges of the skelp. This process produces a high-quality weld and is commonly used for pipes that require superior weld integrity.
d. Electric Fusion Welding
Electric fusion welding is a process used for joining the ends of the skelp through electric fusion. This method is often employed for large-diameter pipes and pipes with thicker walls.
e. Spiral Welding
Spiral welding involves continuously forming and welding a helical seam along the length of the pipe. This method is commonly used for the production of large-diameter pipes, especially in water and gas transmission.
f. Longitudinal Submerged Arc Welding (LSAW)
LSAW involves welding along the length of the pipe, typically in a straight line. This method is preferred for pipes that require precise dimensions and high-quality welds.
Step 6: Weld Inspection
After welding, the pipes undergo rigorous inspection to detect any defects or irregularities in the weld. Non-destructive testing methods, such as ultrasonic testing or X-ray examination, are used to ensure the integrity of the weld seam. Any defects are marked for correction.
Step 7: Sizing and Shaping
The welded pipe is passed through a series of sizing and shaping rolls to achieve the desired diameter and wall thickness. This process is crucial for meeting the specified dimensions and ensuring the pipe’s structural integrity.
Step 8: Cooling and Cutting
Once the pipe is sized, it is cooled using a water spray or air to facilitate handling and prevent deformation. After cooling, the pipe is cut to the required lengths. Precision cutting ensures the pipes are uniform and ready for further processing or transport.
Step 9: End Facing and Beveling
The cut ends of the pipes are then faced and beveled to ensure they are square and free from any burrs or irregularities. This is essential for proper fitting and welding when the pipes are joined together in a pipeline.
Step 10: Coating and Surface Treatment
To enhance the pipes’ corrosion resistance and longevity, they may be coated with various materials, including epoxy, polyethylene, or zinc. This protective coating shields the pipe from environmental factors and corrosive substances.
Step 11: Final Inspection
Before the pipes are ready for distribution and installation, they undergo a final inspection. This inspection verifies that all specifications, including size, thickness, and weld quality, meet the required standards and project specifications.
Step 12: Marking and Packaging
Each pipe is marked with essential information, including its size, grade, manufacturing date, and relevant codes. The pipes are then packaged and prepared for shipment to their intended destination.
Types of Welded Pipes
Welded pipes are the workhorses of the oil and gas industry, serving various applications with different requirements. Understanding the types of welded pipes available is crucial for selecting the right pipe for a specific project. In this section, we will delve deeper into the common types of welded pipes used in the oil and gas sector and explore specialty pipes designed for specific applications.
Common Types of Welded Pipes
Electric Resistance Welded (ERW) Pipes
ERW pipes are among the most commonly used welded pipes in the oil and gas industry. They are known for their versatility and cost-effectiveness, making them suitable for a wide range of applications. The ERW welding process involves passing a high-frequency electric current through the edges of steel strips to create a weld.
Applications:
- ERW pipes are often used for low and medium-pressure applications, such as pipelines, distribution networks, and structural components.
- They find extensive use in water and gas pipelines.
Advantages:
- ERW pipes are economical due to their efficient manufacturing process.
- They come in various sizes, making them suitable for different project requirements.
Electric Fusion Welded (EFW) Pipes
Electric Fusion Welded (EFW) pipes are another important category of welded pipes used in the oil and gas industry. EFW pipes are created by applying an electrical charge to melt the edges of two pipe sections, fusing them together. This process offers several advantages, including the ability to produce large-diameter pipes with excellent quality and a smooth internal finish.
Applications:
- EFW pipes are suitable for various applications, including transportation of oil, gas, and petrochemical products.
- They are often used in high-pressure and high-temperature environments.
Advantages:
- EFW pipes can be produced in large diameters, making them ideal for oil and gas transmission.
- The process results in a smooth internal surface, reducing friction and improving flow characteristics.
EFW pipes are particularly valuable when large volumes of oil and gas need to be transported efficiently and reliably over long distances.
Submerged Arc Welded (SAW) Pipes
SAW pipes are preferred for transporting heavy and high-pressure fluids, particularly crude oil. The submerged arc welding process involves feeding a consumable wire electrode continuously, creating a submerged arc that melts the edges of the pipe sections and fuses them together.
Applications:
- SAW pipes are commonly used in the transmission of crude oil, natural gas, and other heavy hydrocarbons.
- They are suitable for onshore and offshore pipelines, including those operating in corrosive environments.
Advantages:
- SAW pipes offer excellent weld quality, ensuring structural integrity and leak resistance.
- They are known for their ability to withstand high pressure and stress.
High-Frequency Induction (HFI) Welded Pipes
HFI welded pipes are recognized for their superior weld quality and precision. This method uses electromagnetic induction to heat the edges of the pipe sections, creating a strong weld.
Applications:
- HFI welded pipes are often chosen for critical applications that demand high precision and consistent weld quality.
- They are used in industries where reliability and performance are paramount.
Advantages:
- HFI welding ensures excellent weld quality, making the pipes suitable for critical applications.
- These pipes are adaptable and can be customized to meet specific project requirements.
Don’t miss the Complete Course on Piping Engineering: Check Now
Enrollment Link
Specialty Welded Pipes
Corrosion-Resistant Alloy (CRA) Welded Pipes
In environments where standard steel pipes may corrode, corrosion-resistant alloy (CRA) welded pipes are employed. These pipes are made from alloys such as Inconel, Hastelloy, or other corrosion-resistant materials.
Applications:
- CRA pipes are used in corrosive environments where standard steel pipes are not suitable.
- They find applications in oil and gas production facilities, offshore drilling, and processing plants.
Advantages:
- CRA welded pipes offer exceptional resistance to corrosion and wear.
- They are crucial for ensuring the longevity of pipelines in harsh environments.
Lined Pipes
Lined pipes consist of a carbon steel pipe lined with materials like PTFE (Polytetrafluoroethylene). The lining material provides protection against the transport of aggressive or corrosive fluids.
Applications:
- Lined pipes are used when the transported fluids are highly corrosive and could damage standard steel pipes.
- They are common in industries where chemical resistance is essential, such as chemical processing and wastewater treatment.
Advantages:
- Lined pipes combine the strength of steel with the chemical resistance of the lining material.
- They ensure the safe and efficient transportation of aggressive fluids.
Choosing the Right Welded Pipe
Selecting the right type of welded pipe for an oil and gas industry project is crucial to ensure the success and longevity of the pipeline. The choice of pipe type should be based on factors such as the type of fluid being transported, the operating environment, pressure and temperature requirements, and budget constraints. Each type of welded pipe has its strengths and limitations, making it essential to match the pipe to the specific needs of the project.
Application of Welded Pipes
Welded pipes are the vital conduits that enable the oil and gas industry to transport its most precious resources over long distances. These pipes play a pivotal role in various applications, ensuring the safe and efficient flow of crude oil, natural gas, and other hydrocarbons from extraction sites to refineries, distribution networks, and ultimately, to consumers. Understanding the diverse applications of welded pipes in the oil and gas sector is essential for appreciating their significance and reliability.
Oil Transportation
One of the primary and most critical applications of welded pipes in the oil and gas industry is the transportation of crude oil from its source to refineries. These pipelines are the arteries of the industry, facilitating the movement of this valuable resource to locations where it is processed and transformed into the products we rely on daily.
Key Points:
- Crude oil pipelines are designed to transport the unrefined petroleum from oil fields, whether onshore or offshore, to the refining facilities.
- These pipelines can extend over thousands of miles, crossing varied terrains and climatic conditions.
- Their efficiency is paramount to ensure a steady supply of crude oil for processing.
Natural Gas Transmission
Welded pipes are also instrumental in the transportation of natural gas, which plays a central role in powering homes, industries, and electric power plants. These pipelines carry the gas from production fields to distribution networks, ensuring a continuous and reliable supply.
Key Points:
- Natural gas pipelines are responsible for transporting gas from wells to storage facilities, processing plants, and eventually, to end-users.
- The gas can travel vast distances before reaching its destination, often requiring an extensive network of pipelines.
- Efficiency and safety are paramount to prevent leaks and ensure the uninterrupted supply of natural gas.
Water Injection
In enhanced oil recovery (EOR) projects, water injection is used to increase the productivity of oil wells. Welded pipes are employed to transport and inject water into oil reservoirs, enhancing oil recovery rates.
Key Points:
- Water injection pipelines transport water from source locations to injection wells.
- The injected water helps maintain reservoir pressure and displaces oil, making it easier to extract.
- Welded pipes are crucial in the efficient delivery of water for this enhanced oil recovery technique.
Offshore Drilling
Offshore drilling in the oil and gas industry involves extracting hydrocarbons from beneath the seabed. The pipes used for offshore drilling must be durable and reliable, as they transport oil and gas from underwater wells to processing facilities on the surface.
Key Points:
- Offshore pipelines are subject to harsh conditions, including saltwater corrosion and extreme pressure.
- Welded pipes used in offshore drilling must meet stringent safety and quality standards.
- These pipes are essential for maintaining the integrity of subsea well systems.
Refinery Piping
Within refineries, welded pipes serve various purposes, including the transport of refined products, chemicals, and feedstocks between different processing units. The efficiency and reliability of these pipes are crucial for the smooth operation of the entire refinery.
Key Points:
- Refinery piping systems often handle a wide range of products, from gasoline and diesel to petrochemicals.
- The pipes must be designed to withstand the specific pressures, temperatures, and corrosive elements associated with different refinery processes.
- Efficiency and safety are paramount within this complex and highly regulated environment.
High-Pressure Applications
Welded pipes are ideal for high-pressure applications, such as hydraulic systems and wellheads in oil and gas fields. These pipes are designed to withstand extreme pressure and provide a reliable conduit for hydraulic fluids or hydrocarbons.
Key Points:
- High-pressure pipelines are used in situations where the flow of fluids at elevated pressures is necessary.
- They can be found in hydraulic fracking systems, drilling equipment, and pressure vessels.
- The integrity of welded pipes in high-pressure applications is critical to prevent leaks and ensure operational safety.
Environmental Remediation
In environmental remediation projects, welded pipes may be used to transport contaminated fluids or gases for treatment and disposal. These pipes are crucial for handling hazardous materials safely and efficiently.
Key Points:
- Environmental remediation involves the cleanup and disposal of hazardous waste, contaminated water, or gases.
- Welded pipes in these applications must meet specific safety and environmental standards.
- Their use ensures the controlled and secure transport of pollutants to treatment or disposal facilities.
Don’t miss the Complete Course on Piping Engineering: Check Now
Enrollment Link
Advantages & Disadvantages
To make informed decisions about the use of welded pipes in oil and gas industry projects, it’s essential to consider their advantages and disadvantages.
Table: Advantages of Welded Pipes
Advantages | Explanation |
---|---|
Strength and Durability | Welded pipes can withstand high pressure and stress. |
Cost-Effective | They are more affordable than seamless pipes. |
Customization | Available in various sizes and coatings for versatility. |
High Production Efficiency | Rapid manufacturing meets industry demand. |
Resistance to Corrosion | Corrosion-resistant coatings extend lifespan. |
Table: Disadvantages of Welded Pipes
Disadvantages | Explanation |
---|---|
Potential for Weld Defects | Welded seams may have defects that need inspection. |
Vulnerable to Corrosion | Uncoated surfaces are susceptible to corrosion. |
Limited Temperature Range | May not be suitable for extremely high temperatures. |
Installation Challenges | May require skilled labor for proper installation. |
Environmental Impact | Coatings and materials used can have environmental impacts. |
Associated Codes & Standards
In the oil and gas industry, the utilization of welded pipes is governed by a comprehensive set of codes and standards. These regulations are essential to guarantee the safety, reliability, and performance of welded pipes in various applications. In addition to the previously mentioned standards, several others play a crucial role in the industry. Let’s explore these in more detail:
1. API 5L
API 5L stands as one of the most pivotal standards for welded and seamless steel line pipes. It is published by the American Petroleum Institute (API) and encompasses a wide range of steel pipe grades. These pipes find application in conveying natural gas, crude oil, and water. The API 5L standard ensures that these pipes meet stringent quality and performance requirements, making them suitable for the transportation of hydrocarbons over long distances.
2. ASME B31.4 & B31.8
The ASME B31.4 and ASME B31.8 codes, issued by the American Society of Mechanical Engineers (ASME), offer guidelines for the design, construction, operation, and maintenance of pipeline transportation systems. These standards are specific to liquid hydrocarbons (B31.4) and gas (B31.8) transmission. They address various aspects of pipeline systems, including materials, design, testing, safety, and maintenance. Complying with these codes is imperative for ensuring the integrity and safety of oil and gas pipelines.
3. ASME B31.3
In addition to B31.4 and B31.8, the ASME B31.3 code is of great importance in the oil and gas industry. Although it primarily pertains to process piping systems within facilities, it is highly relevant to projects where welded pipes are extensively used. ASME B31.3 provides comprehensive guidance for the design, construction, inspection, and maintenance of process piping systems that carry various fluids, including hazardous materials. Adherence to this code is crucial for maintaining the safety and reliability of process piping systems, which often incorporate welded pipes.
4. ISO 3183
The ISO 3183 standard, developed by the International Organization for Standardization (ISO), outlines requirements for pipelines used in the transportation of hydrocarbons. It addresses aspects such as pipe manufacturing, testing, and quality control. ISO 3183 harmonizes international practices and ensures consistency in the design, construction, and operation of pipelines across different regions.
5. NACE MR0175/ISO 15156
NACE MR0175/ISO 15156 is a standard that specifically deals with materials used in environments where there is a risk of sulfide stress cracking, a significant concern in the oil and gas industry. It provides guidelines for selecting materials that are resistant to such cracking in environments containing hydrogen sulfide (H2S).
6. ASTM Standards
The American Society for Testing and Materials (ASTM) issues numerous standards related to welded pipes, including specifications for specific pipe grades and types, testing methods, and procedures. These standards ensure that the material properties and quality of welded pipes meet industry requirements.
7. DNV-OS-F101
DNV-OS-F101 is a widely recognized standard from the Det Norske Veritas (DNV) for submarine pipeline systems. It provides guidelines for the design, construction, and operation of offshore pipelines. This standard is particularly relevant in offshore oil and gas projects where welded pipes are extensively employed.
8. CSA Z245
The CSA Z245 series of standards are published by the Canadian Standards Association (CSA) and pertain to steel pipe, valves, and fittings used in Canada’s oil and gas industry. These standards cover various aspects, including material specifications and requirements for steel pipes used in different service conditions.
9. EN Standards
The European Norm (EN) standards cover various aspects of welded steel pipes used in Europe. They address material properties, dimensions, and testing procedures to ensure the quality and reliability of pipes used in oil and gas projects within the European Union.
Conclusion
In conclusion, welded pipes are the backbone of the oil and gas industry, enabling the efficient and reliable transportation of vital resources. Understanding their history, functions, types, applications, advantages, and disadvantages, as well as adhering to strict industry standards, is essential for the successful execution of oil and gas projects.
The rich history of welded pipes, coupled with continuous technological advancements, has allowed the industry to depend on them for the transportation of oil and gas. The welding methods, such as Electric Resistance Welding (ERW), Submerged Arc Welding (SAW), and High-Frequency Induction (HFI) Welding, have evolved to create stronger, more durable, and cost-effective pipes.
These pipes serve a multitude of applications, including the transportation of crude oil, natural gas, water injection in enhanced oil recovery, offshore drilling in challenging environments, and within refineries. They are ideal for high-pressure applications and even environmental remediation projects, showcasing their versatility.
Despite their many advantages, such as strength, durability, and cost-effectiveness, welded pipes do have their limitations, including potential weld defects, susceptibility to corrosion, and limited temperature ranges. However, the industry addresses these challenges through strict adherence to codes and standards, such as API 5L, ASME B31.3, ASME B31.4, ASME B31.8, and ISO 3183.
In the dynamic world of the oil and gas industry, welded pipes remain an essential component, continually evolving to meet the ever-increasing demands of energy production and transportation. Their reliability and adaptability ensure that they will continue to be at the forefront of oil and gas projects, providing the infrastructure necessary for the modern world’s energy needs.
Frequently Asked Questions (FAQs)
FAQ 1: What are welded pipes, and why are they used in the oil and gas industry?
Welded pipes are steel pipes manufactured by joining two pipe sections through welding processes like ERW, SAW, or HFI. They are used in the oil and gas industry because of their strength, durability, and cost-effectiveness for transporting fluids over long distances.
FAQ 2: What are the different types of welded pipes used in the industry?
Common types of welded pipes include ERW, SAW, and HFI pipes, while specialty options like CRA and lined pipes are used for specific applications.
FAQ 3: How are welded pipes installed and maintained in oil and gas projects?
Installation requires skilled labor to ensure proper welding and connection. Maintenance involves inspections for defects and corrosion, with repairs or replacements as necessary.
FAQ 4: Are there environmental concerns associated with welded pipes in the oil and gas industry?
The coatings and materials used in welded pipes can have environmental impacts, and there is a need for proper disposal and management of such materials.
FAQ 5: How do welded pipes compare to other pipe materials in the oil and gas industry?
Welded pipes are preferred for their strength and cost-effectiveness. They are often chosen over alternatives like seamless pipes for their suitability in a wide range of applications.
Don’t miss the Complete Course on Piping Engineering: Check Now
Enrollment Link
Recommended courses (Published on EPCLand)
- Complete Course on Piping Engineering
- Basics of Piping Engineering
- Piping Layout Engineering
- Piping Material Engineering
- Piping Stress Analysis
- Material Requisitions
- Piping Material Specifications
- Valve Material Specifications
- Plant Design & Layouts-OISD 118
- Isometric Management
Library of Technical Articles
Don’t miss out the collection of 15+ articles on following topics:
- Basics of Oil and Gas Industry
- Valves
- Testing
- Tank
- Piping Bulk Items
- Pipe
- Metallurgy
- Piping Materials
- Layout
- Instrumentation
- Heat Exchanger
- Type of Contracts
- Codes and Standards
- ASTM Standards
- Articles on Piping Specialty Items
Video details of Complete Course on Piping Engineering
Attempt Quiz
Question 1:
What is the primary purpose of welded pipes in Oil & Gas projects?
Explanation: Welded pipes in Oil & Gas projects are primarily used to transport oil and gas.
Question 2:
Which material is commonly used in the manufacturing of welded pipes for Oil & Gas applications?
Explanation: Steel is commonly used in the manufacturing of welded pipes for Oil & Gas applications due to its strength and durability.
Question 3:
What welding technique is commonly used in the production of welded pipes for Oil & Gas projects?
Explanation: Electric resistance welding is a common technique used in the production of welded pipes for Oil & Gas projects.
Question 4:
What is the purpose of the internal coating in welded pipes used in Oil & Gas applications?
Explanation: The internal coating in welded pipes used in Oil & Gas applications is to prevent corrosion and improve fluid flow within the pipe.
Question 5:
Which of the following factors affects the selection of welded pipe thickness in Oil & Gas projects?
Explanation: The thickness of welded pipes in Oil & Gas projects is influenced by fluid temperature and pressure to ensure safe transport.
Question 6:
What is the primary advantage of using welded pipes over seamless pipes in Oil & Gas applications?
Explanation: The primary advantage of using welded pipes over seamless pipes in Oil & Gas applications is lower cost.
Question 7:
Which organization sets industry standards for the manufacturing and testing of welded pipes in the Oil & Gas sector?
Explanation: The American Petroleum Institute (API) sets industry standards for the manufacturing and testing of welded pipes in the Oil & Gas sector.
Question 8:
What is the purpose of X-ray and ultrasonic testing in the quality control of welded pipes?
Explanation: X-ray and ultrasonic testing are used to detect structural defects and ensure the integrity of welded pipes.
Question 9:
Which factor can lead to the failure of welded pipes in Oil & Gas projects?
Explanation: Corrosion and stress-related factors can lead to the failure of welded pipes in Oil & Gas projects.
Question 10:
What is the expected service life of high-quality welded pipes in Oil & Gas applications?
Explanation: High-quality welded pipes in Oil & Gas applications can have an expected service life of 20 to 30 years when properly maintained.