Carbon steel stands as a cornerstone material in various industries, known for its versatility, durability, and cost-effectiveness. With a wide range of applications across engineering, construction, manufacturing, and more, understanding carbon steel’s properties, types, and applications is crucial. In this comprehensive guide, we delve into the world of carbon steel, exploring its characteristics, variants, and its significance in modern-day industries.
Introduction to Carbon Steel
Carbon steel, as the name suggests, is primarily composed of carbon and iron, with trace amounts of other elements. Its composition gives rise to a broad spectrum of mechanical properties that make it suitable for an array of applications. Carbon steel finds its utility across various sectors due to its cost-effectiveness, ease of production, and exceptional mechanical performance.
Table of Contents
Don’t miss the Complete Course on Piping Engineering: Check Now
By EPCLand.com
Properties of Carbon Steel
Carbon Content and Alloying Elements
The defining characteristic of carbon steel is its carbon content, typically ranging from 0.05% to 2.0%. The carbon content influences the material’s hardness, strength, and overall performance. Additionally, small amounts of alloying elements such as manganese, silicon, and copper can be added to enhance specific properties.
Strength and Durability
Carbon steel exhibits impressive strength and durability, making it a preferred choice for load-bearing structures and components. The higher the carbon content, the greater the material’s hardness and strength. However, a delicate balance must be struck to prevent brittleness.
Machinability and Weldability
One of carbon steel’s notable features is its excellent machinability, allowing for ease of shaping, cutting, and drilling. Moreover, it possesses good weldability, making it feasible to create complex structures and components through various welding techniques.
Corrosion Resistance
While carbon steel is susceptible to corrosion, the addition of certain alloying elements, protective coatings, and proper maintenance can significantly enhance its corrosion resistance. Understanding the environmental conditions is crucial in selecting the appropriate type of carbon steel.
Types of Carbon Steel
Carbon Steel Type | Carbon Content (%) | Additional Elements | Strength | Ductility | Applications |
---|---|---|---|---|---|
Low-Carbon Steel | Below 0.25 | Limited | Weaker | High | Automobile components, pipes, construction |
Medium-Carbon Steel | 0.25 – 0.6 | 0.6 – 1.65 Manganese | Moderate | Moderate | Railway tracks, gears, machinery parts |
High-Carbon Steel | 0.6 – 1.25 | 0.3 – 0.9 Manganese | Strong | Low | Cutting tools, springs, high-strength wire |
Low Carbon Steel
Low carbon steel, also known as mild steel, contains a minimal carbon content. It offers exceptional ductility, making it suitable for forming and welding. Applications range from automotive panels to construction components.
Medium Carbon Steel
Medium carbon steel strikes a balance between strength and ductility. It is commonly used in machinery and automotive parts that require both resilience and load-bearing capacity.
High Carbon Steel
High carbon steel boasts increased hardness and strength due to its elevated carbon content. This type of carbon steel is utilized in applications such as cutting tools, springs, and high-strength wires.
Ultra-High Carbon Steel
With a carbon content approaching 2.0%, ultra-high carbon steel exhibits extreme hardness. It is predominantly used in applications demanding exceptional wear resistance, like cutting blades and specialized machinery.
Applications of Carbon Steel
Automotive Industry
Carbon steel finds extensive use in the automotive sector, from structural components to body panels. Its formability, strength, and cost-effectiveness contribute to its prevalence in manufacturing vehicles.
Construction and Infrastructure
In construction, carbon steel serves as a fundamental material for beams, columns, and reinforcing bars. Its robustness and availability make it indispensable in building sturdy and reliable structures.
Manufacturing and Machinery
Machinery manufacturing benefits from carbon steel’s versatility. It’s utilized in gears, shafts, bearings, and various machine components that require a combination of strength and machinability.
Oil and Gas Sector
Carbon steel pipes are vital components in the oil and gas industry. Their durability and corrosion resistance, especially when coated or lined, make them ideal for transporting oil and gas over long distances.
Carbon Steel vs Stainless Steel
In the vast realm of metals, the term “steel” unveils an entire family of versatile metal alloys. With an extensive array of applications and utilitarian roles, steel remains a ubiquitous material. Within this expansive category, two primary classifications stand out: carbon steels and stainless steels. This article delves into the realm of carbon steel, elucidating its intrinsic properties, diverse types, and broad applications.
Unveiling Carbon Steel’s Essence
Steel, a diverse alloy encompassing carbon and iron, showcases remarkable adaptability across industries. The distinction between carbon steel and stainless steel lies in their composition. While both are predominantly comprised of iron and carbon, the incorporation of varying alloying elements imparts distinctive properties to each.
The Carbon Content Distinction
Carbon steel’s unique character emanates from its carbon content, often falling below 10.5%. Notably, stainless steel necessitates a minimum of 10.5% chromium to gain its stainless attribute, setting a pivotal demarcation between the two.
Understanding Stainless Steel
Stainless Steel: A Guardian Against Oxidation
Stainless steel is synonymous with resilience, owing its distinctive qualities to the addition of chromium and other alloying components like nickel. Often referred to as “inox steel” due to its resistance against oxidation (inoxidation), stainless steel fends off rusting through the strategic application of chromium. Unlike iron that oxidizes in the presence of oxygen, chromium forms a protective layer, shielding the underlying iron from corrosive elements.
Various Types of Stainless Steel
Diverse chromium levels in stainless steel govern its properties, with lower chromium content often translating to lower cost but reduced durability. The realm of stainless steel includes:
- Austenitic Stainless Steel: With remarkable corrosion and heat resistance, this variant is extensively used in industrial piping, housewares, and architectural facades. It constitutes the majority of stainless steel production.
- Ferritic Stainless Steel: Exhibiting superior corrosion, heat, and cracking resistance, ferritic steel often lacks nickel. Its application spans washing machines, boilers, and indoor architecture.
- Martensitic Stainless Steel: Magnetic and robust, martensitic steel is used in knife and turbine blade production. Its lower chromium content slightly diminishes corrosion resistance.
- Duplex Stainless Steel: A fusion of austenitic and ferritic steel, duplex steel boasts strength and flexibility, rendering it suitable for paper, pulp, shipbuilding, and petrochemical industries.
- Precipitation Stainless Steel: Balancing corrosion resistance and strength, precipitation steel can be fortified with elements like aluminum, copper, and niobium for exceptional robustness.
Pros and Cons of Stainless Steel
Advantages:
- Corrosion-resistant
- Withstands high and low temperatures
- Diverse variety available
- Strong and durable
- Low maintenance and easy to clean
- Environmentally friendly and recyclable
Disadvantages:
- Initial high cost
- Handling challenges without advanced technology
- Potential waste and rework
Applications of Stainless Steel
Stainless steel’s influence spans diverse sectors. It has been a staple in the automotive industry for decades, employed in exhaust systems, grills, trims, and structural components. In aviation, stainless steel finds a home in airplane frames, jet engines, and landing gear due to its corrosion resistance and ease of maintenance. Its compatibility with chemicals makes it vital in transporting and handling chemicals. The medical field benefits from stainless steel’s hygiene-friendly nature.
Architecturally, stainless steel shines in projects like the Eurostar Terminal in London and the Helix Bridge in Singapore. Its presence is felt in everyday life too, from cookware and cutlery to appliances.
Carbon Steel: Sturdy Foundation
Contrasting stainless steel, carbon steel’s essence lies in its lower chromium levels. Essentially, carbon steel is a carbon-iron alloy with limited additional elements. This “low-alloy” steel’s defining aspect is its carbon content, typically ranging between 2-2.5%. The variance in carbon content dictates carbon steel’s mechanical traits.
Varieties of Carbon Steel
The defining feature of any carbon steel is its carbon content, demarcating the following categories:
- Low-Carbon Steel: With carbon content under 0.25%, this type is weaker yet ductile. It finds application in automobile components, pipes, and construction.
- Medium-Carbon Steel: Carrying 0.25-0.6% carbon and 0.6-1.65% manganese, this type gains strength through heat treatment. It suits railway tracks, gears, and machinery parts.
- High-Carbon Steel: With carbon content ranging from 0.6-1.25% and manganese from 0.3-0.9%, this type boasts extreme hardness, resilience, and wear resistance. It serves in cutting tools and springs.
Pros and Cons of Carbon Steel
Advantages:
- Increased strength
- Cost-effective compared to stainless steel
- Wear-resistant
- Durable and shock-resistant
- Environmentally friendly and recyclable
Disadvantages:
- Prone to rust and corrosion
- Brittle and difficult to mold
- Less attractive appearance
Applications of Carbon Steel
Low-carbon steel’s malleability suits automobile bodies and construction. Medium-carbon steel finds its place in railway tracks, gears, and machinery parts, while high-carbon steel’s robustness serves cutting tools and springs.
Comparing Stainless Steel and Carbon Steel: Mechanical Properties
Ductility: Austenitic Stainless Steel grades exhibit greater ductility compared to Carbon Steel. However, Martensitic stainless steel grades can be more brittle than carbon steel.
Mechanical Strength: Generally, Stainless steel is softer and exhibits lower strength due to its lower carbon content. The mechanical properties of carbon steel versus stainless steel are outlined in Table 2 below:
Mechanical Properties | Carbon Steel | Stainless Steel |
---|---|---|
Yield Strength | Low Carbon Steel: 180 to 260 MPa; High carbon Steel: 325 to 440 Mpa. | Ferritic Steel: 280 Mpa; Austenitic Steel: 230 MPA; Martensitic Steel: 480 MPA |
Tensile Strength | Low Carbon Steel: 325 to 485 MPa; High carbon Steel: 460 to 924 Mpa. | Ferritic Steel: 450 Mpa; Austenitic Steel: 540 MPA; Martensitic Steel: 660 MPA |
Elastic Modulus | 2100000 Mpa | 1900000 MPa |
Shear Modulus | 81000 Mpa | 740000 MPa |
Poisson’s Ratio | 0.3 | 0.27 |
Comparing Carbon Steel and Stainless Steel: Temperature Tolerance
Stainless steel can handle fluids at temperatures above 426 degrees C, while carbon steel starts graphitization after 426 degrees C, limiting its application to temperatures of 426 degrees C. Stainless steel is renowned for its exceptional heat resistance capabilities.
Normal carbon steel isn’t suitable for temperatures below -460 degrees C. Special LTCS material is used for temperatures below this mark. In contrast, stainless steel can endure much lower temperatures.
Comparing Stainless Steel and Carbon Steel: Appearance
For aesthetic appeal, stainless steel takes the lead over carbon steel. Stainless steel’s natural appearance is striking, whereas carbon steel requires surface painting to prevent rusting.
Comparing Stainless Steel and Carbon Steel: Cost
Economic factors are crucial when comparing carbon steel and stainless steel. In general, stainless steel is pricier than carbon steel. However, costs vary based on the material grades. The addition of special alloys like chromium, nickel, and manufacturing processes contribute to the increased cost of stainless steel.
Comparing Stainless Steel and Carbon Steel: Machinability and Weldability
Carbon steel is easy to machine and possesses good welding characteristics. In contrast, stainless steel demands specialized techniques for welding and machining. Stainless steel is harder than carbon steel, making it more challenging for machine tools.
Comparing Stainless Steel and Carbon Steel: Other Distinctions
Stainless Steel | Carbon Steel | |
---|---|---|
Thermal Conductivity | Comparatively lower | Higher thermal conductivity |
Wear Resistance | Excellent wear resistance | Poor wear resistance |
Heat Treatment | Difficult to heat treat | Easily undergoes heat treatment |
Cleanability | Easily cleanable | Carbon steel has lower cleanability |
In conclusion, understanding the differences between stainless steel and carbon steel’s mechanical properties, temperature tolerances, appearance, cost, machinability, and other characteristics is vital when selecting the appropriate material for various applications.
Can Stainless Steel Weld to Carbon Steel?
Welding these distinct metals is feasible but not generally recommended due to their differing electrical conductivity. Carbon steel’s higher electrical conductivity requires preheating during resistance welding, complicating achieving the right weld temperature.
In conclusion, carbon steel and stainless steel’s unique properties grant them diverse roles across industries. While stainless steel triumphs in durability and hygiene, carbon steel offers economic strength and resilience. The intricacies of these materials provide the foundation for innovation, construction, and progress across various sectors.
Aspect | Carbon Steel | Stainless Steel |
---|---|---|
Composition | Primarily carbon and iron, with limited alloys | Iron, carbon, chromium, and other alloys |
Corrosion Resistance | Prone to rust and corrosion | Resistant to corrosion and rust |
Strength | Varies based on carbon content | Strong and durable |
Ductility | Varies based on carbon content | Varies based on alloy composition |
Cost | Generally lower cost | Higher initial cost, but often cost-effective over time |
Weldability | Can be welded with appropriate techniques | Requires special techniques due to varied electrical conductivity |
Applications | Construction, machinery parts, cutting tools | Automotive, aviation, medical, architecture, cookware, appliances |
Manufacturing of Carbon Steel
Carbon steel and mild steel undergo manufacturing through a series of stages that shape their properties and characteristics. The production process involves three main phases: primary steelmaking, secondary steelmaking, and casting. These stages are followed by various finishing techniques that directly influence the final product’s attributes.
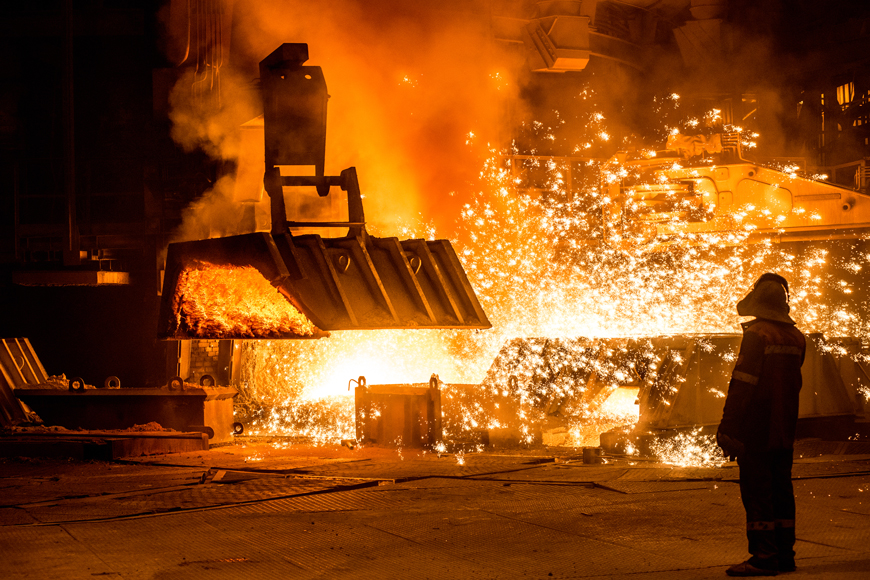
Primary Steelmaking
The creation of steel begins with primary steelmaking, which can occur through two approaches: using 100% recycled material or combining recycled material with virgin steel. Virgin steel is crafted in a blast furnace, employing iron ore, coke derived from coal, and lime. These raw materials are introduced to the furnace’s top, operating at extremely high temperatures. As the iron ore fuses with burning coke, carbon is released into the molten mixture. Lime absorbs impurities, creating a slag that is removed from the liquid steel’s surface. At this point, the product contains about 4% carbon along with certain impurities.
The molten virgin steel is then moved to a basic oxygen furnace (BOF) containing recycled scrap metal. Oxygen is blown through the liquid steel in the BOF to oxidize excess carbon, resulting in a finished product with carbon content up to 1.5%.
Recycled scrap steel, on the other hand, is processed without the addition of virgin steel in an electric arc furnace. This furnace employs high-power electric arcs to melt the metal at extremely high temperatures. The molten scrap steel can accommodate further batches of scrap until it reaches capacity. Subsequently, oxygen is blown through the molten metal in a manner similar to the BOF process. In both scenarios, the molten steel is tapped into ladles or steel baths for further processing, while the impurity-laden slag is removed from the surface.
Secondary Steelmaking
Growing demands for higher-quality steel products and consistent properties have driven the development of secondary steelmaking techniques.
- Electric Arc Furnace: Steel composition is modified in an electric arc furnace by adding or removing specific components or manipulating temperature.
- Stirring: Electromagnetic fields generate turbulent currents in the ladle, separating non-metallic inclusions and ensuring homogenous steel composition.
- Ladle Furnace: The ladle acts as a secondary electrode furnace, enabling precise temperature control and controlled alloy component injection.
- Ladle Injection: Inert gas injected into the steel bath’s bottom generates a stirring effect as it rises through the molten metal.
- Degassing: Techniques like vacuum treatment, inert gas injection, and temperature control are employed to remove hydrogen, oxygen, nitrogen, and reduce sulfur content.
- Composition Adjustment (CAS-OB): Injecting argon gas into the sealed steel bath initiates stirring. Oxygen is fed to the bath through a lance, and aluminum is added through a snorkel, providing enhanced temperature control and accurate composition.
- Deoxidizing Steel: Deoxidation is crucial in altering steel characteristics, affecting its suitability for various applications. Rimming, capped, semi-killed, and killed steels are categories based on deoxidation levels.
Casting
Traditional casting involves pouring molten steel from a ladle into molds on rail cars. Ingots are then reheated for hot rolling. Continuous casting machines are used to cast molten steel into shapes suitable for downstream processing. This involves feeding molten steel from a tundish to a water-cooled mold. As the steel solidifies, it’s formed into slabs, blooms, or billets, and the process continues seamlessly.
Conclusion
The manufacturing process of carbon steel undergoes primary and secondary steelmaking followed by casting. Each stage contributes to the steel’s final properties, making it a versatile and widely used material across various industries.
Finishing Processes for Carbon Steel
Once the manufacturing of carbon steel is completed, it undergoes a series of finishing processes, including rolling, heat treatment, surface treatment, and downstream secondary processing, to enhance its properties and suitability for various applications.
Continuous Casting and Product Rolling
The journey of carbon steel continues with the solidification of steel into slabs, blooms, or billets using a continuous casting machine. These raw forms must then be transformed into more practical shapes and sizes through product rolling. In this crucial step, steel ingots are subjected to compression and elongation by rotating rolls. The rolls rotate at a faster rate than the steel’s movement, propelling it forward and compressing it simultaneously.
Hot Forming
To optimize the microstructure of the as-cast steel, hot forming is employed. Carbon steel is heated beyond the recrystallization temperature, effectively breaking down the initial microstructure. This results in a more consistent grain size and a uniform distribution of carbon throughout the steel. The hot forming process significantly improves the steel’s overall quality.
Cold Forming
Cold forming takes place below the recrystallization temperature, boosting the steel’s strength through a process known as strain hardening, which can increase its strength by up to 20%. This technique not only enhances the steel’s structural integrity but also refines its finish and allows for tighter tolerances. As a result of the cold forming process, semi-finished products emerge, taking the shape of blooms, billets, or slabs, depending on the required final dimensions. Blooms are robust rectangular slabs, billets share similar thickness but with a narrower width, while slabs are thinner and wider.
Further Processing for Intermediate Products
These semi-finished products then proceed to a rolling mill for further processing into intermediate forms. The objective is to prepare them for subsequent manufacturing steps and final processing performed by downstream companies. This integral part of the process refines the carbon steel and readies it for its intended applications.
Choosing Between Carbon Steel and Stainless Steel for Your Application
The decision to use either carbon steel or stainless steel comes down to a careful consideration of their respective advantages, disadvantages, properties, and budget implications. Therefore, the selection process between these two materials should primarily revolve around the specific application at hand. Here’s a guideline on when to opt for carbon steel or stainless steel:
Stainless Steel or Carbon Steel: The Decision Factors
Application: The foremost factor in the decision-making process is the intended application. Each material has its unique set of characteristics that can cater to specific requirements. Thus, the nature of the application should be the driving force behind your choice.
Properties Needed: Different scenarios demand different properties. Stainless steel offers excellent corrosion resistance, making it ideal for environments with exposure to harsh chemicals or elements. Carbon steel, on the other hand, might be preferred for its robustness and strength in non-corrosive settings.
Budget Considerations: Budget is always a significant factor. Stainless steel tends to be pricier due to its specialized properties and alloy composition. If your budget is flexible, you might lean towards stainless steel. However, in cases where budget constraints exist, carbon steel can provide a more cost-effective solution.
Temperature Extremes: For applications requiring high-temperature resistance or dealing with cryogenic temperatures, stainless steel’s exceptional properties shine. Its ability to withstand extreme temperatures without compromising its integrity makes it the clear choice in such scenarios.
Corrosion Resistance: If your application involves exposure to corrosive agents, stainless steel’s corrosion-resistant nature makes it an obvious contender. On the other hand, if corrosion isn’t a primary concern, carbon steel could serve well in non-corrosive environments.
Making the Final Call
In summary, the decision between carbon steel and stainless steel should be rooted in a comprehensive understanding of the specific needs of your application. If budget is of minimal concern and corrosion resistance, high temperatures, or extreme temperature fluctuations are essential, stainless steel is likely the better option. However, when facing normal, non-corroding environments, carbon steel can offer a reliable and cost-effective solution.
Ultimately, a well-informed choice that aligns with your application’s requirements and budgetary considerations will ensure that you make the most suitable selection between these two versatile materials.
FAQs About Carbon Steel
Q1: What is carbon steel’s main component? A1: Carbon steel primarily consists of iron and carbon, with trace amounts of other elements.
Q2: What is the difference between mild steel and high carbon steel? A2: Mild steel (low carbon steel) has a lower carbon content and is more ductile, while high carbon steel has greater hardness due to its higher carbon content.
Q3: Is carbon steel prone to corrosion? A3: Yes, carbon steel can corrode, but its corrosion resistance can be improved through protective coatings and proper maintenance.
Q4: What are the applications of ultra-high carbon steel? A4: Ultra-high carbon steel is used in applications requiring extreme wear resistance, such as cutting tools and specialized machinery.
Q5: Can carbon steel be welded easily? A5: Yes, carbon steel generally has good weldability, making it suitable for various welding techniques.
Conclusion
Carbon steel’s versatility, coupled with its remarkable properties, renders it an invaluable asset across diverse industries. From automotive manufacturing to infrastructure development and machinery production, carbon steel underpins the foundation of modern civilization. Understanding the different types of carbon steel and their applications empowers industries to leverage its strengths effectively, ensuring enhanced performance and longevity in various applications.
By comprehending the nuances of carbon steel, we can harness its potential to drive innovation, construct robust structures, and propel industries forward, standing as a testament to human ingenuity and engineering prowess.
Recommended courses (Published on EPCLand)
- Basics of Piping Engineering
- Piping Layout Engineering
- Piping Material Engineering
- Piping Stress Analysis
- Complete Course on Piping Engineering
- Material Requisitions
- Piping Material Specifications
- Valve Material Specifications
Don’t miss the published articles on following:
Related Video
Attempt Quiz
Question 1:
What is carbon steel primarily composed of?
Explanation: Carbon steel is primarily composed of iron and carbon, with carbon content influencing its properties and characteristics.
Question 2:
Which of the following is a common classification of carbon steel based on carbon content?
Explanation: Carbon steel is commonly classified based on carbon content. Low-Carbon Steel, for example, has a low carbon content and is often referred to as mild steel.
Question 3:
Which of the following properties does carbon steel generally exhibit?
Explanation: Carbon steel generally exhibits good machinability, making it relatively easy to cut, shape, and process. It may have varying degrees of tensile strength depending on its carbon content.
Question 4:
Which carbon steel classification is commonly used for structural applications?
Explanation: Low-Carbon Steel and Medium-Carbon Steel are commonly used for structural applications due to their balance of strength, ductility, and weldability.
Question 5:
Which factor determines the hardness and strength of carbon steel?
Explanation: The carbon content in carbon steel primarily determines its hardness and strength. Higher carbon content generally results in higher hardness and strength.