Introduction
Regulation valves play a pivotal role in the smooth operation of various industrial processes. These valves are integral components that enable precise control over parameters such as pressure, flow rate, and temperature in fluid systems. By modulating the passage of fluids, regulation valves ensure that the desired conditions are maintained, enhancing efficiency, safety, and product quality across a wide range of industries.
Table of Contents
Do not miss the course on Regulation Valves
Enrollment Link
Definition of Regulation Valves
Regulation valves, also known as control valves, are mechanical devices designed to manage the flow of fluids (liquids, gases, or steam) within a system. They are equipped with mechanisms that allow operators to adjust the valve opening, which in turn controls the rate at which fluids pass through. This adjustment capability gives industries the ability to fine-tune various process parameters and maintain optimal operating conditions.
Importance of Regulation Valves in Industrial Processes
In industrial settings, precise control over fluid parameters is crucial for achieving consistent and reliable outcomes. Regulation valves provide a means to:
- Optimize Processes: By controlling parameters like pressure, flow, and temperature, regulation valves help maintain conditions conducive to efficient production and manufacturing processes.
- Ensure Safety: Many processes require specific pressure levels or flow rates to ensure safety for both equipment and personnel. Regulation valves prevent dangerous deviations from these required levels.
- Enhance Product Quality: Industries such as food and pharmaceuticals rely on accurate temperature and flow control to produce high-quality products with consistent characteristics.
- Increase Efficiency: By adjusting flow rates and pressure levels, regulation valves minimize energy consumption and wastage, leading to cost savings and environmental benefits.
Overview of the Article’s Content
This article aims to provide a comprehensive understanding of regulation valves, covering their types, functioning principles, applications in various industries, design considerations, installation and maintenance guidelines, challenges faced, and future trends. By delving into these aspects, readers will gain insights into how regulation valves contribute to industrial processes’ smooth functioning and the evolving technologies that are shaping their future.
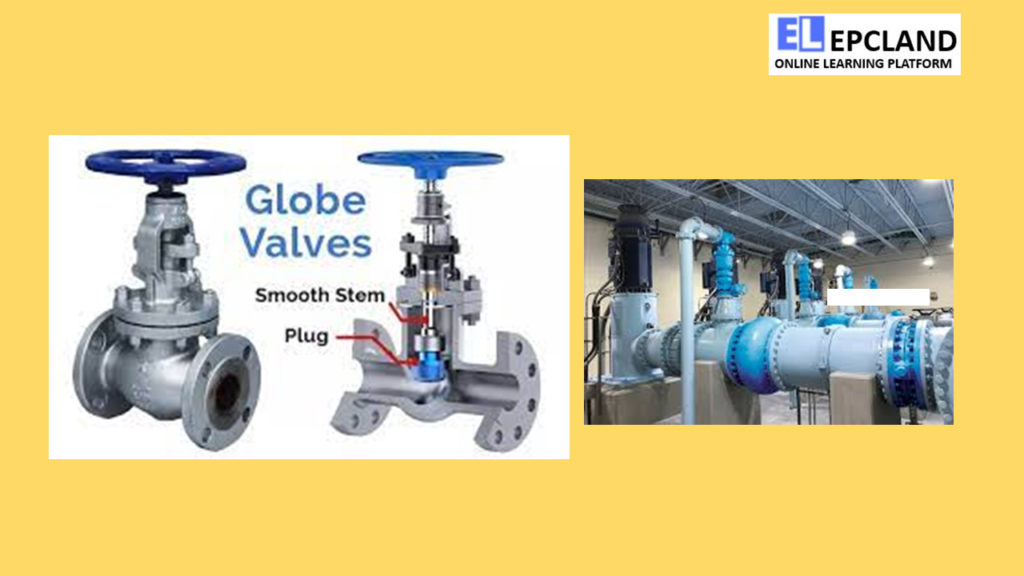
Types of Regulation Valves
Regulation valves come in various types, each designed to fulfill specific roles in controlling fluid parameters within industrial processes. These types can be broadly categorized into pressure regulation valves, flow regulation valves, and temperature regulation valves.
Pressure Regulation Valves
Pressure regulation valves are designed to maintain consistent pressure levels within a system. They include:
Pressure Reducing Valves
These valves reduce high inlet pressure to a lower, preset outlet pressure. They are commonly used to protect downstream equipment from excessive pressure and maintain safe operating conditions.
Pressure Sustaining Valves
Pressure sustaining valves, also known as back-pressure control valves, ensure that a minimum pressure is maintained upstream of the valve. They are often used in systems where a certain pressure is required for proper operation.
Back-Pressure Regulators
These valves control the system’s back pressure, ensuring that it doesn’t drop below a specified level. They are crucial in processes where maintaining back pressure is critical.
Do not miss the course on Regulation Valves
Enrollment Link
Flow Regulation Valves
Flow regulation valves control the rate of fluid flow through a system. Some common types include:
Globe Valves
Globe valves offer precise control over flow by modulating the valve’s position. They are commonly used in applications that require fine-tuned adjustments.
Butterfly Valves
Butterfly valves have a disc that rotates in the flow path to control fluid flow. They are ideal for applications requiring quick shut-off and relatively low-pressure drops.
Ball Valves
Ball valves have a spherical disc with a hole that can be aligned with the flow path or closed by rotating the ball. They are suitable for on/off control rather than fine flow modulation.
Needle Valves
Needle valves provide fine control over flow rates with a threaded stem and a small port. They are often used in applications where precise adjustments are necessary.
Temperature Regulation Valves
Temperature regulation valves manage fluid temperature by mixing hot and cold fluids. They include:
Thermostatic Valves
Thermostatic valves automatically adjust the mixing ratio of hot and cold fluids to maintain a desired temperature. They are commonly used in heating and cooling systems.
Mixing Valves
Mixing valves manually or automatically adjust the proportion of hot and cold fluids to achieve the desired temperature. They find use in applications where consistent water temperature is crucial, such as showers and HVAC systems.
Understanding these different types of regulation valves is essential for selecting the appropriate valve for a specific application. Each type serves a unique purpose and contributes to the efficient control of fluid parameters within industrial processes.
Do not miss the course on Regulation Valves
Enrollment Link
Functioning Principles
Regulation valves operate based on specific principles that enable them to control various fluid parameters effectively. The functioning principles depend on the type of regulation valve and the parameter it is designed to control.
Pressure Regulation
Control of Fluid Pressure
Pressure regulation valves control fluid pressure by adjusting the valve’s opening, which in turn affects the flow rate. When the valve is partially closed, the fluid encounters resistance, leading to a drop in pressure. Conversely, opening the valve wider allows for increased flow and higher pressure.
Spring-Loaded Mechanisms and Pilot Systems
Many pressure regulation valves utilize spring-loaded mechanisms or pilot systems. A spring applies force to the valve, counteracting the fluid pressure. As the fluid pressure increases, the spring’s force is overcome, allowing the valve to open and release excess pressure. Pilot systems use a separate fluid to control the valve’s opening, offering precise pressure control.
Flow Regulation
Varying Valve Openings
Flow regulation valves control fluid flow by adjusting the valve’s opening, which directly impacts the flow rate. By increasing or decreasing the valve opening, operators can achieve the desired flow rate for a particular application.
Control of Fluid Volume
The ability to control fluid volume through flow regulation valves is essential for maintaining consistent processes. In applications where precise flow rates are necessary, these valves ensure optimal performance and product quality.
Temperature Regulation
Mixing Hot and Cold Fluids
Temperature regulation valves, such as mixing valves and thermostatic valves, operate by blending hot and cold fluids. By adjusting the ratio of hot to cold fluids, these valves achieve the desired temperature output.
Bimetallic and Thermostatic Elements
Some temperature regulation valves utilize bimetallic elements that react to temperature changes. These elements expand or contract, affecting the valve’s opening and subsequently altering the blend of hot and cold fluids. Thermostatic valves incorporate temperature-sensing components to automatically adjust the valve’s position based on temperature variations.
Understanding these functioning principles is essential for effectively utilizing regulation valves in industrial processes. The ability to control pressure, flow rate, and temperature accurately enhances process efficiency, safety, and product quality.
Do not miss the course on Regulation Valves
Enrollment Link
Applications in Industries
Regulation valves find wide-ranging applications across various industries, each benefiting from their ability to precisely control fluid parameters.
Oil and Gas Industry
- Pressure Regulation in Pipelines: Pressure reducing valves ensure that the pressure within pipelines remains at safe and optimal levels during transportation, preventing equipment damage and ensuring efficient flow.
- Flow Control in Refineries: Flow regulation valves help manage the flow of crude oil, gases, and various refinery products, enabling efficient refining processes.
Chemical Manufacturing
- Precise Flow Control for Reaction Processes: Flow regulation valves play a critical role in controlling the flow of reactants in chemical reactions, ensuring accurate mixing and preventing dangerous fluctuations.
- Temperature Regulation in Chemical Reactors: Temperature regulation valves help maintain consistent temperatures in chemical reactors, contributing to optimal reaction kinetics and product quality.
Water Treatment
- Pressure Regulation in Distribution Networks: Pressure reducing valves maintain the pressure within water distribution networks, preventing bursts and leaks while ensuring a steady supply of water to consumers.
- Temperature Control in Water Heaters: Mixing valves blend hot and cold water to achieve the desired temperature in water heaters, providing comfortable and safe water temperatures.
HVAC Systems (Heating, Ventilation, and Air Conditioning)
- Temperature Regulation for Comfortable Environments: Thermostatic and mixing valves in HVAC systems maintain precise indoor temperatures, ensuring occupants’ comfort and energy efficiency.
- Energy-Efficient Operation Through Precise Control: Regulation valves contribute to energy savings by enabling precise control over heating and cooling processes, preventing wastage.
These examples highlight the vital role that regulation valves play in maintaining efficient and safe operations in diverse industries. The ability to manage pressure, flow, and temperature parameters ensures optimal performance, product quality, and safety across various processes.
Do not miss the course on Regulation Valves
Enrollment Link
Design and Selection Factors
The design and selection of regulation valves are crucial to their effective operation within industrial processes. Several key factors must be considered during the design and selection process.
Material Selection
- Compatibility with Fluid Properties: Valves should be made from materials that are compatible with the properties of the fluid they will handle. Corrosive fluids, for instance, may require valves made from corrosion-resistant materials.
- Corrosion Resistance and Durability: Valves should be constructed from materials that can withstand the corrosive effects of the fluids and the operating environment, ensuring a longer lifespan.
Sizing Considerations
- Matching Valve Capacity: Properly sizing regulation valves involves matching their capacity to the required flow rate, pressure, and temperature conditions of the process. Oversizing or undersizing can lead to inefficiencies and operational issues.
- Avoiding Cavitation and Pressure Drop: Incorrect sizing can lead to cavitation (formation of vapor bubbles) and pressure drop issues, which can damage the valve and affect process performance.
Actuation Methods
- Manual, Pneumatic, Hydraulic, Electric, and Digital Control: Valves can be operated manually or using various actuation methods. The choice depends on factors like the required precision, speed, and automation level of the process.
- Automation for Remote and Precise Control: Automated valves, especially in critical processes, allow for remote and precise control, enabling operators to make adjustments based on real-time data.
Installation and Maintenance
- Proper Installation Practices: Valves should be installed in positions that optimize their performance and accessibility for maintenance. Correct sealing techniques and proper connections are vital for preventing leaks and ensuring safety.
- Regular Maintenance: Regular cleaning, inspection, and maintenance routines are necessary to keep valves operating optimally. Calibrations and adjustments ensure that the valve’s performance remains accurate.
Understanding these design and selection factors is essential for ensuring that regulation valves are appropriately chosen, installed, and maintained for their intended applications. Proper design and selection contribute to efficient and reliable operation within industrial processes.
Installation and Maintenance
Proper installation and regular maintenance are essential to ensure the optimal performance and longevity of regulation valves within industrial processes.
Proper Installation Practices
- Positioning for Optimal Performance: Valves should be installed in positions that allow for easy access, operation, and maintenance. Proper orientation and alignment ensure that the valve functions as intended.
- Connection Considerations and Sealing Techniques: Correctly connecting the valve to the piping system and using appropriate sealing techniques are crucial to prevent leaks and maintain system integrity.
Regular Maintenance
- Cleaning and Inspection Routines: Regular cleaning prevents clogs and buildup that can affect valve performance. Routine inspections identify wear, damage, or other issues that require attention.
- Calibration and Adjustment Procedures: Valves may need periodic calibration and adjustment to ensure they maintain accurate control. This is especially important for applications requiring precise parameter control.
Preventive Maintenance
- Scheduled Maintenance Plans: Establishing preventive maintenance schedules helps prevent unexpected breakdowns and extends the valve’s lifespan.
- Replacement of Wear Parts: Regularly replacing worn-out parts, such as seals and gaskets, prevents leaks and maintains the valve’s effectiveness.
Training and Documentation
- Operator Training: Properly trained personnel can operate and maintain valves correctly, minimizing the risk of errors and ensuring safe operations.
- Documentation: Keeping records of maintenance activities, adjustments, and repairs provides valuable insights for future maintenance and troubleshooting.
By following these installation and maintenance practices, industries can ensure that their regulation valves perform optimally, contributing to the efficiency, safety, and reliability of their processes.
Do not miss the course on Regulation Valves
Enrollment Link
Challenges and Solutions
While regulation valves offer numerous benefits, they can also pose challenges that need to be addressed for effective operation. Here are some common challenges and potential solutions:
Noise and Vibration Issues
- Challenge: Valve operations can generate noise and vibrations, which can be disruptive and damaging to equipment and structures.
- Solution: Damping mechanisms, such as adding vibration-absorbing materials or installing acoustic insulation, can help mitigate noise and vibration issues.
Cavitation and Erosion
- Challenge: Improperly sized valves or high-pressure differentials can lead to cavitation, causing damage to valve components. Erosion can occur due to high-velocity fluid flow.
- Solution: Proper valve sizing, using anti-cavitation trim, and selecting materials resistant to erosion can help mitigate these issues.
Corrosion and Fouling
- Challenge: Corrosive fluids or contaminants can lead to corrosion and fouling, reducing valve efficiency and lifespan.
- Solution: Choosing corrosion-resistant materials, applying protective coatings, and implementing regular maintenance practices can help combat corrosion and fouling.
Compatibility and Interoperability
- Challenge: Integrating regulation valves into existing systems may require compatibility and interoperability considerations.
- Solution: Ensure that the selected valves are compatible with the system’s components and that communication protocols for automated valves are compatible with control systems.
Technical Expertise and Training
- Challenge: Properly operating and maintaining regulation valves requires technical expertise that may not always be readily available.
- Solution: Offering training programs to personnel, collaborating with valve manufacturers for support, and establishing clear documentation can address knowledge gaps.
Energy Efficiency
- Challenge: Inefficient valve designs can contribute to energy wastage, especially in processes with varying flow rates.
- Solution: Investing in energy-efficient valve designs and automation systems can help optimize energy consumption while maintaining process control.
Addressing these challenges proactively contributes to the effective and reliable operation of regulation valves in industrial applications. Implementing appropriate solutions ensures that valves continue to deliver their intended benefits while minimizing disruptions and maintenance requirements.
Future Trends
The landscape of regulation valves is evolving with technological advancements and industry trends. Several key trends are shaping the future of regulation valve technology:
Digitalization and Smart Valves
- IoT Integration for Real-time Monitoring and Control: Internet of Things (IoT) technology enables real-time data collection, remote monitoring, and control of regulation valves. This enhances visibility and facilitates timely adjustments.
- Predictive Maintenance Using Data Analytics: IoT-enabled sensors and data analytics allow predictive maintenance, reducing downtime and optimizing maintenance schedules.
Energy Efficiency and Sustainability
- Improved Valve Designs for Reduced Energy Consumption: Valve manufacturers are developing designs that minimize energy losses, leading to more energy-efficient operations.
- Recycling and Environmentally Friendly Materials: Sustainable practices in valve manufacturing involve using recycled materials and developing environmentally friendly coatings, contributing to reduced environmental impact.
Advanced Material Science
- Development of High-Performance Materials: Advances in materials science are leading to the creation of materials with enhanced resistance to corrosion, erosion, and wear, prolonging valve lifespan.
- Nanotechnology Applications: Nanomaterials are being explored to improve valve performance, including better sealing, reduced friction, and improved durability.
Automation and Artificial Intelligence
- Greater Integration with Control Systems: Automation of valve operations is increasing, allowing for seamless integration with overall process control systems.
- Artificial Intelligence for Optimization: AI algorithms are being employed to optimize valve settings based on complex process conditions, leading to more efficient and precise control.
Modular and Customizable Designs
- Modular Valve Configurations: Modular designs enable quicker customization and replacement of components, reducing downtime during maintenance or changes in process requirements.
- Tailored Solutions for Specific Applications: Valve manufacturers are offering more customized solutions that cater to specific industry needs and unique process requirements.
By staying abreast of these future trends, industries can make informed decisions about adopting new technologies and strategies to enhance the performance, efficiency, and sustainability of their regulation valves.
Do not miss the course on Regulation Valves
Enrollment Link
Conclusion
Regulation valves are indispensable components in various industrial processes, enabling precise control over fluid parameters such as pressure, flow rate, and temperature. Their importance spans across industries, from oil and gas to chemical manufacturing, water treatment, and HVAC systems. By maintaining optimal conditions, regulation valves contribute to process efficiency, safety, product quality, and energy conservation.
Selecting the right type of regulation valve, designing for compatibility and efficiency, and ensuring proper installation and maintenance are essential for maximizing their benefits. Overcoming challenges related to noise, cavitation, corrosion, and technical expertise requires proactive measures and innovative solutions.
As technology advances, the integration of digitalization, smart capabilities, and sustainable materials will shape the future of regulation valve technology. Embracing these trends will lead to even more efficient and effective valve systems, contributing to safer, more reliable, and environmentally friendly industrial operations.
FAQs
Frequently asked questions (FAQs) related to regulation valves:
1. What are regulation valves used for?
Regulation valves, also known as control valves, are used to control the flow of fluids (liquids, gases, or steam) within industrial processes. They enable precise adjustments of parameters such as pressure, flow rate, and temperature to maintain optimal operating conditions, improve process efficiency, ensure safety, and enhance product quality.
2. How do regulation valves work?
Regulation valves work by adjusting the valve’s opening to control fluid flow. For instance, pressure regulation valves adjust the opening to control pressure levels, flow regulation valves adjust the opening to control flow rates, and temperature regulation valves adjust the blending of hot and cold fluids to achieve the desired temperature.
3. What challenges can arise with regulation valves?
Challenges associated with regulation valves include noise and vibration issues, cavitation (formation of vapor bubbles) and erosion due to high velocities, corrosion and fouling of valve components, compatibility and interoperability issues, and the need for technical expertise to operate and maintain valves effectively.
4. How can I choose the right regulation valve for my application?
Choosing the right regulation valve involves considering factors such as the type of fluid, required flow rate, pressure, and temperature, as well as compatibility with materials, actuation methods, and automation needs. Consulting with experts, valve manufacturers, and considering the specific needs of your application is essential.
5. What is the future of regulation valve technology?
The future of regulation valve technology is characterized by digitalization and smart valves, energy efficiency and sustainability initiatives, advanced materials science, automation and artificial intelligence integration, and modular and customizable designs. These trends will lead to more efficient, reliable, and environmentally friendly valve systems in various industrial processes.
Recommended courses (Published on EPCLand)
- Basics of Piping Engineering
- Piping Layout Engineering
- Piping Material Engineering
- Piping Stress Analysis
- Complete Course on Piping Engineering
- Material Requisitions
- Piping Material Specifications
- Valve Material Specifications
Don’t miss the published articles on following:
Related Video
Attempt Quiz
Question 1:
What is the primary function of a regulation valve?
Explanation: The primary function of a regulation valve is to regulate and control the flow rate of fluid through a pipeline or system.
Question 2:
Which type of valve is commonly used for precise flow control?
Explanation: Globe valves are commonly used for precise flow control due to their design that allows throttling of the flow through the valve.
Question 3:
Which factor does a regulation valve control in a fluid system?
Explanation: A regulation valve primarily controls the flow rate, which affects the pressure in a fluid system. Therefore, it controls the pressure in the system.
Question 4:
Which type of regulation valve is often used to maintain a constant pressure downstream?
Explanation: Control valves are often used to maintain a constant pressure downstream by adjusting the valve opening based on the pressure feedback.
Question 5:
Which component of a regulation valve controls the flow rate?
Explanation: The plug or disc, often located inside the valve body, is the component that controls the flow rate by adjusting its position in response to the valve actuator.