Introduction to U-Tube Heat Exchangers
Heat exchangers play a pivotal role in various industries, facilitating the efficient transfer of thermal energy between fluids while keeping them physically separate. Among the numerous types of heat exchangers, the U-Tube heat exchanger stands out for its unique design and versatile applications. In this article, we delve into the working principles, design considerations, advantages, applications, maintenance, and future trends of U-Tube heat exchangers.
Table of Contents
Similar Articles on other Exchangers
Heat Exchanger Type | Check Article Link |
---|---|
Helical Coil Heat Exchanger | Link |
Tube-in-Tube Heat Exchanger | Link |
Spiral Heat Exchanger | Link |
U-Tube Heat Exchanger | Link |
Shell and Tube Heat Exchanger | Link |
Plate Heat Exchanger | Link |
Double Pipe Heat Exchanger | Link |
Finned Tube Heat Exchanger | Link |
Don’t miss the Complete Course on Piping Engineering: Check Now
By EPCLand.com
Working Principles of U-Tube Heat Exchangers
U-Tube heat exchangers operate on the fundamental principles of heat transfer: conduction, convection, and radiation. They come in two main configurations – counterflow and parallel flow. In the counterflow setup, the hot and cold fluids flow in opposite directions, maximizing the temperature difference across the exchanger and thereby enhancing heat transfer efficiency. In parallel flow, the fluids flow in the same direction, offering more controlled heat exchange.
Heat transfer occurs through the exchange of thermal energy between the two fluids, and this process is greatly influenced by fluid dynamics. The temperature difference, flow rates, and material properties of the fluids determine the rate of heat exchange. These considerations underline the importance of fluid selection and design optimization for achieving optimal performance.
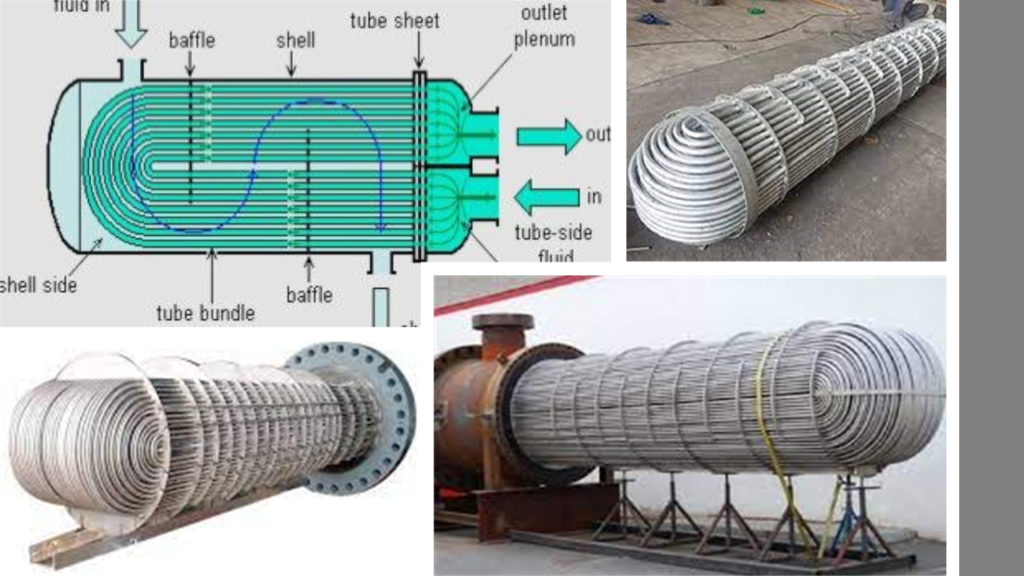
Design and Construction
The U-Tube heat exchanger derives its name from its distinctive U-shaped tubes. These tubes form the core of the exchanger and are housed within a shell. The U-shape allows for easy expansion and contraction during heating and cooling cycles, making U-Tube heat exchangers suitable for high-temperature and high-pressure applications. The tube bundle is removable, enabling convenient maintenance and inspection.
The choice of materials for U-Tube heat exchangers is crucial. Corrosion-resistant materials such as stainless steel, titanium, and nickel alloys are commonly used to ensure longevity and prevent fluid contamination. Design factors such as pressure ratings, temperature limits, and fluid compatibility must be carefully considered to ensure safe and efficient operation.
Advantages of U-Tube Heat Exchangers
U-Tube heat exchangers offer several advantages that make them preferred choices in various industries. Their U-shaped tubes accommodate thermal expansion without stressing the structure, reducing the risk of leaks and structural failures. The tube bundle’s removability simplifies cleaning and maintenance, enhancing the exchanger’s longevity and efficiency. Moreover, U-Tube heat exchangers are adept at handling high-pressure and high-temperature applications, making them versatile solutions across different sectors.
Don’t miss the Detailed course on Drums/Exchanger Piping Layout & Stress Analysis
Enrollment Link
Applications in Various Industries
HVAC Systems: Heating, Ventilation, and Air Conditioning
U-Tube heat exchangers find extensive use in HVAC systems for space heating and cooling. They help transfer heat between the building’s interior and the external environment, ensuring comfort and energy efficiency. The counterflow configuration is often employed in these systems, maximizing heat exchange efficiency.
Petrochemical Industry: Crude Oil Refining and Chemical Processing
In the petrochemical industry, U-Tube heat exchangers play a vital role in refining crude oil and processing chemicals. Their ability to withstand high temperatures and pressures makes them valuable components in processes such as distillation, catalytic cracking, and hydrocarbon processing.
Power Generation: Condensers and Cooling Systems
Power plants rely on U-Tube heat exchangers for efficient cooling and condensation processes. They are integral to condensers in steam power plants, aiding in the conversion of steam back into water for reuse. Additionally, U-Tube heat exchangers assist in cooling systems, maintaining optimal temperatures for generators and turbines.
Food and Beverage Industry: Pasteurization and Food Processing
The food and beverage industry benefits from U-Tube heat exchangers for pasteurization, sterilization, and food processing. Their hygienic design and efficient heat transfer capabilities ensure that perishable products are treated effectively while maintaining quality.
Renewable Energy Sector: Geothermal Power Plants and Solar Thermal Systems
U-Tube heat exchangers play a pivotal role in harnessing renewable energy sources. In geothermal power plants, they facilitate the transfer of thermal energy from the Earth’s interior to generate electricity. Similarly, in solar thermal systems, U-Tube heat exchangers aid in capturing and storing solar energy for various applications.
Performance Optimization and Efficiency Enhancement
Optimizing the performance of U-Tube heat exchangers involves several key strategies. The choice of fluids is critical; selecting the right fluids with suitable thermophysical properties can significantly enhance heat transfer efficiency. Additionally, preventing fouling and scaling within the tubes is essential to maintain efficient operation over time. Regular maintenance practices, including cleaning and inspection, ensure that the heat exchanger operates at its full potential.
Advanced computational tools have revolutionized the design process, enabling engineers to simulate and model heat exchanger performance under different conditions. These tools aid in achieving optimal designs and identifying potential challenges before implementation.
Don’t miss the Detailed course on Drums/Exchanger Piping Layout & Stress Analysis
Enrollment Link
Case Studies
Real-world examples underscore the effectiveness of U-Tube heat exchangers. In a large-scale HVAC system overhaul, a manufacturing facility replaced its outdated heat exchangers with U-Tube units, resulting in a 30% reduction in energy consumption. In the petrochemical sector, a refinery implemented U-Tube heat exchangers in its distillation process, leading to higher product yields and reduced energy expenditure.
Challenges during installation and operation are not uncommon. In one instance, a power plant faced vibration issues due to inadequate support structures for the U-Tube heat exchangers. By redesigning the supports and implementing vibration dampening measures, stable operation was achieved.
Comparison with Other Heat Exchanger Types
Shell-and-Tube Heat Exchangers
Compared to shell-and-tube heat exchangers, U-Tube variants offer distinct advantages. The U-Tube design allows for greater thermal expansion, reducing the risk of tube leaks and failures. Additionally, their ease of maintenance and inspection due to the removable tube bundle simplifies upkeep, setting them apart from shell-and-tube designs.
Plate Heat Exchangers
While plate heat exchangers excel in compactness and efficiency, U-Tube heat exchangers stand out in applications where fouling is a concern. U-Tube designs are more tolerant of particulate-laden fluids, making them suitable for processes prone to fouling.
Coil Heat Exchangers
Coil heat exchangers are prevalent in smaller-scale applications, but U-Tube heat exchangers are more versatile in handling larger fluid volumes and higher pressures. The U-Tube design offers enhanced thermal performance and better expansion capabilities.
Maintenance and Troubleshooting
Routine maintenance is crucial to sustaining U-Tube heat exchanger efficiency. Regular cleaning of the tube bundle and shell interior prevents the accumulation of deposits that can impede heat transfer. Inspections should also include checking for corrosion, leaks, and structural integrity issues. In cases of reduced heat transfer efficiency, diagnosing and addressing potential causes such as fouling or fluid imbalance is essential.
Future Trends and Innovations
The future of U-Tube heat exchangers is poised for innovation. Integrating these heat exchangers with smart technologies and the Internet of Things (IoT) enables real-time monitoring of performance and facilitates predictive maintenance. Advances in materials science are leading to the development of novel materials with improved heat transfer properties and corrosion resistance. Environmental concerns are also driving the exploration of more sustainable and energy-efficient heat exchange solutions.
Pros & Cons
Pros of U-Tube Heat Exchangers | Cons of U-Tube Heat Exchangers |
---|---|
Enhanced thermal efficiency due to counterflow design | Complex design may lead to higher manufacturing costs |
Flexibility to handle thermal expansion and contraction | Limited to certain fluid types and temperature ranges |
Easy maintenance and inspection with removable tube bundle | Bulkier compared to some compact heat exchanger designs |
Suitable for high-pressure and high-temperature applications | Larger space requirement in some installations |
Versatility in applications across various industries | Limited to moderate to high flow rates for optimal performance |
Efficient heat transfer even in fouling-prone environments | Potential for vibration issues in some configurations |
Potential energy savings and reduced operating costs | Greater pressure drop compared to some other designs |
Adaptable to both counterflow and parallel flow configurations | Requires precise fluid balancing for optimal performance |
U-Tube heat exchangers offer numerous advantages, including their efficient heat transfer capabilities, flexibility in design, and ease of maintenance. However, they may also have some drawbacks, such as higher manufacturing costs, limitations in terms of flow rates and fluids, and potential space requirements. The complexity of their construction could lead to increased maintenance needs, and counterflow designs might require larger surface areas. Careful consideration of these pros and cons is essential when determining the suitability of U-Tube heat exchangers for specific applications.
Don’t miss the Detailed course on Drums/Exchanger Piping Layout & Stress Analysis
Enrollment Link
Codes & Standards
Codes and Standards | Description |
---|---|
ASME Boiler and Pressure Vessel Code | Establishes rules for the design, fabrication, and inspection of pressure vessels, including heat exchangers. |
TEMA (Tubular Exchanger Manufacturers Association) Standards | Provides guidelines for the design, construction, and maintenance of shell-and-tube heat exchangers, including U-Tube variants. |
API (American Petroleum Institute) Standards | Offers standards for the design and operation of equipment used in the petroleum and petrochemical industries, including heat exchangers. |
ANSI (American National Standards Institute) Standards | Publishes standards related to various industries, including heat exchangers, to ensure safety and performance. |
ISO (International Organization for Standardization) Standards | Provides international standards for various aspects of industrial equipment, including heat exchangers, to ensure quality and consistency. |
ASTM (American Society for Testing and Materials) Standards | Offers standards for materials and testing methods used in the construction of heat exchangers to ensure material quality and performance. |
HEI (Heat Exchange Institute) Standards | Publishes standards for the design and operation of heat exchangers, including U-Tube models, to ensure efficient heat transfer. |
ASHRAE (American Society of Heating, Refrigerating and Air Conditioning Engineers) Standards | Offers guidelines for HVAC systems, including heat exchangers, to ensure energy efficiency and occupant comfort. |
NFPA (National Fire Protection Association) Standards | Provides standards for fire safety, which may apply to heat exchangers in certain industries and applications. |
IEC (International Electrotechnical Commission) Standards | Publishes international standards for electrical and electronic equipment that may be integrated into heat exchanger systems. |
It’s important to note that the specific codes and standards applicable to a U-Tube heat exchanger will depend on the industry, location, and intended use of the heat exchanger. Manufacturers and designers should consult the appropriate codes and standards to ensure compliance with safety, quality, and performance requirements.
Comparison Table with Other type of exchangers
Aspect | U-Tube Heat Exchangers | Shell-and-Tube Heat Exchangers | Plate Heat Exchangers | Coil Heat Exchangers |
---|---|---|---|---|
Design | U-shaped tubes within a shell | Bundles of tubes within a shell | Stacked plates with alternating fluid passages | Coiled tubes |
Thermal Efficiency | High | Moderate to High | High | Moderate to High |
Thermal Expansion Handling | Excellent | Limited | Good | Limited |
Maintenance and Inspection | Easy | Requires removal of bundle | Easy | Moderate |
Space Efficiency | Moderate | Requires less space | Compact | Compact |
Pressure and Temperature Tolerance | High | Moderate to High | Moderate to High | Moderate to High |
Fluid Compatibility | Versatile | Versatile | Limited | Limited |
Application Versatility | Wide range of industries | General industrial applications | HVAC, industrial processes | Small-scale applications |
Fouling and Scaling Tolerance | Moderate | Moderate to High | Low to Moderate | Moderate |
Initial Cost | Moderate to High | Moderate | Moderate | Low to Moderate |
Maintenance Cost | Moderate | Moderate | Low to Moderate | Moderate |
Efficiency under Fouling Conditions | Moderate | Moderate | High | Moderate |
Vibration and Stress Handling | Generally good | Adequate | Sensitive | Sensitive |
Installation Flexibility | Good | Moderate | Limited | Good |
Compactness | Not as compact | Moderate | Very Compact | Compact |
Fluid Flow Turbulence | Good | Moderate | High | Good |
This comparison table provides an overview of how U-Tube heat exchangers compare with other common types of heat exchangers. Each type has its strengths and limitations, making them suitable for specific applications depending on factors like efficiency, space constraints, fluid characteristics, and operational conditions.
Don’t miss the Detailed course on Drums/Exchanger Piping Layout & Stress Analysis
Enrollment Link
Conclusion
U-Tube heat exchangers represent a cornerstone in heat transfer technology, serving a wide array of industries with their unique design, efficiency, and adaptability. Their significance in promoting energy efficiency, enhancing thermal processes, and contributing to various sectors cannot be overstated. As industries evolve and technology advances, U-Tube heat exchangers will continue to play a pivotal role in shaping the future of heat exchange systems worldwide.
FAQs
- What is a U-Tube heat exchanger, and how does it work?A U-Tube heat exchanger is a type of heat transfer device used to efficiently exchange thermal energy between two fluids while keeping them physically separated. It consists of U-shaped tubes housed within a shell. Hot and cold fluids flow through separate tubes, allowing heat to transfer between them. The U-shape of the tubes accommodates thermal expansion, making U-Tube heat exchangers suitable for high-temperature and high-pressure applications.
- What are the advantages of using U-Tube heat exchangers?U-Tube heat exchangers offer several advantages, including:
- High thermal efficiency due to their design and flow configurations.
- Flexibility in handling thermal expansion, reducing the risk of leaks.
- Easy maintenance and inspection with removable tube bundles.
- Suitability for high-pressure and high-temperature applications.
- Versatility across industries like HVAC, petrochemicals, power generation, and more.
- Where are U-Tube heat exchangers commonly used?U-Tube heat exchangers find applications in various industries:
- HVAC systems for heating and cooling buildings.
- Petrochemical industry for refining and chemical processing.
- Power generation in condensers and cooling systems.
- Food and beverage industry for pasteurization and processing.
- Renewable energy sector in geothermal and solar thermal systems.
- What are the challenges associated with U-Tube heat exchangers?While U-Tube heat exchangers have numerous advantages, they also have challenges:
- The design complexity can lead to higher manufacturing costs.
- They may require more space compared to compact designs.
- Counterflow designs might need larger surface areas for effective heat transfer.
- Inadequate support structures can lead to vibration issues.
- Are there any standards or codes for designing U-Tube heat exchangers?Yes, there are several standards and codes that provide guidelines for the design, fabrication, and operation of U-Tube heat exchangers. Some relevant standards include:
- ASME Boiler and Pressure Vessel Code.TEMA (Tubular Exchanger Manufacturers Association) Standards.API (American Petroleum Institute) Standards.ANSI (American National Standards Institute) Standards.ISO (International Organization for Standardization) Standards.
Recommended courses (Published on EPCLand)
- Basics of Piping Engineering
- Piping Layout Engineering
- Piping Material Engineering
- Piping Stress Analysis
- Complete Course on Piping Engineering
- Material Requisitions
- Piping Material Specifications
- Valve Material Specifications
Don’t miss the published articles on following:
Recommended Video
Attempt Quiz
Question 1:
What is a U-Tube Heat Exchanger?
Explanation: A U-Tube Heat Exchanger is a type of heat exchanger with tubes that are bent or arranged in the shape of a U, allowing for thermal energy transfer between two fluids.
Question 2:
What is the main advantage of a U-Tube Heat Exchanger?
Explanation: One of the main advantages of a U-Tube Heat Exchanger is its higher heat transfer efficiency due to the U-shaped tube configuration, which promotes better fluid mixing and improved heat exchange.
Question 3:
What is a common application of U-Tube Heat Exchangers?
Explanation: U-Tube Heat Exchangers are commonly used in various applications, including steam power generation, where they facilitate efficient heat transfer between steam and water in steam generators.
Question 4:
What is the advantage of removable tube bundles in U-Tube Heat Exchangers?
Explanation: Removable tube bundles in U-Tube Heat Exchangers simplify the process of tube cleaning and maintenance, allowing for easy access to the tubes and reducing downtime for maintenance tasks.
Question 5:
What consideration is important when selecting materials for U-Tube Heat Exchangers?
Explanation: Material compatibility with process fluids is an important consideration when selecting materials for U-Tube Heat Exchangers. The selected materials should be resistant to corrosion and suitable for the specific operating conditions.