Introduction
In the realm of the oil and gas industry, pipelines are the unsung heroes, silently facilitating the transportation of hydrocarbons to power our world. Within this vast network of pipelines, there are various types of pipes used for different applications. In this comprehensive article, we delve into two popular choices – Electric Fusion Welded (EFW) pipes and Electric Resistance Welded (ERW) pipes. Understanding the differences, applications, advantages, and disadvantages of EFW vs ERW pipes is crucial for engineers, project managers, and anyone interested in the oil and gas sector.
Table of Contents
Don’t miss the Complete Course on Piping Engineering: Check Now
Enrollment Link
Brief History
Electric Resistance Welded (ERW) Pipes
Electric Resistance Welding, commonly known as ERW, dates back to the late 19th century. It gained prominence during World War II when the demand for pipes surged. ERW pipes were produced to meet the ever-increasing requirements for oil and gas transportation.
Electric Fusion Welded (EFW) Pipes
Electric Fusion Welding, or EFW, is a more recent development compared to ERW. This technology has evolved over the past few decades to cater to the unique needs of the oil and gas industry, especially for the transport of corrosive and high-temperature fluids.
Basic Function and Working Principle
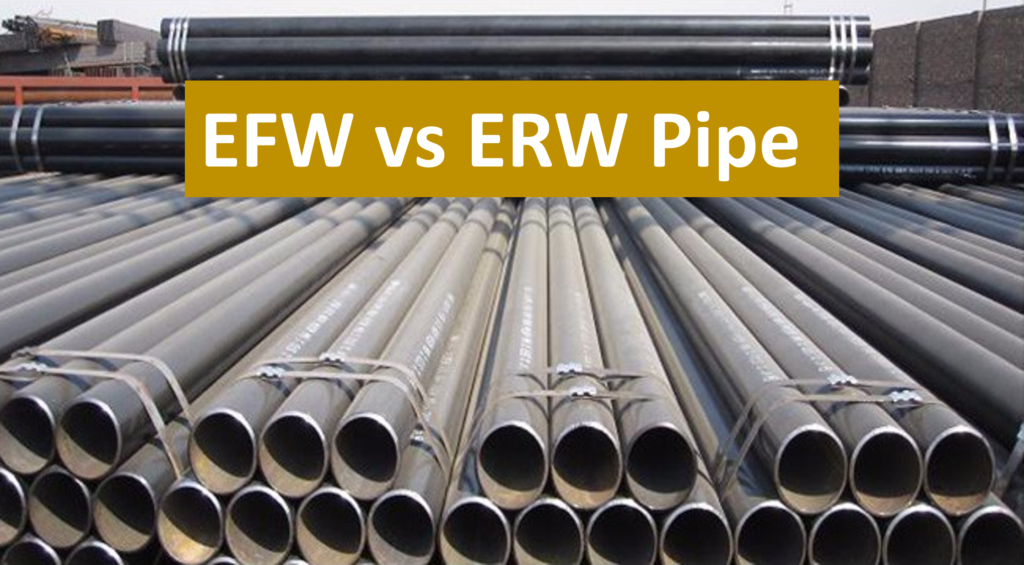
Electric Resistance Welded (ERW) Pipes
ERW pipes are created by continuously forming a flat strip of steel into a pipe shape and then welding the edges together using an electric current. The heat generated during the resistance welding fuses the edges, forming a strong and durable joint.
Electric Fusion Welded (EFW) Pipes
EFW pipes, on the other hand, are manufactured by heating the edges of two pieces of steel to the melting point and then fusing them together. This fusion process results in a seamless, high-integrity pipe.
Manufacturing Process of EFW and ERW Pipes
The manufacturing process of Electric Fusion Welded (EFW) and Electric Resistance Welded (ERW) pipes is a critical aspect that directly influences the quality, integrity, and performance of these pipes in the oil and gas industry. Understanding how EFW and ERW pipes are produced provides insight into their key differences and characteristics. Let’s delve into the manufacturing process of both types.
Manufacturing Process of Electric Resistance Welded (ERW) Pipes
Electric Resistance Welded (ERW) pipes are produced through a well-established and cost-effective manufacturing process. Here’s a detailed breakdown of how ERW pipes are made:
1. Material Selection
The process begins with the selection of raw materials, typically steel coils or strips. These materials are chosen based on factors like the intended application, required strength, and corrosion resistance.
2. Uncoiling and Straightening
The steel coils are uncoiled and then straightened to ensure that the material is in the proper form for processing. Straightening is essential to achieve uniform pipe dimensions.
3. Formation of a Flat Strip
The straightened steel strip is shaped into a flat strip with one edge curled to create a rounded shape, resembling a pipe.
4. Welding
The edges of the flat strip are then welded together using an electric current. This welding process is the defining characteristic of ERW pipes. The electric current generates heat, causing the edges to fuse and create a strong, durable joint. The weld seam is usually located along the length of the pipe.
5. Sizing
After welding, the pipe is passed through a series of rollers to achieve the desired outer diameter and wall thickness. These dimensions are carefully controlled to meet the specifications of the intended application.
6. Cutting
Once the pipe reaches the desired length, it is cut into individual sections, ready for further processing or application.
7. Testing
ERW pipes undergo various tests to ensure their quality and adherence to industry standards. This may include non-destructive testing methods such as ultrasonic testing, radiographic testing, and hydrostatic testing.
Manufacturing Process of Electric Fusion Welded (EFW) Pipes
Electric Fusion Welded (EFW) pipes, in contrast to ERW pipes, are known for their seamless construction. The manufacturing process of EFW pipes involves some distinct steps:
1. Material Selection
Similar to ERW pipes, EFW pipes start with the selection of appropriate raw materials, which often include stainless steel, nickel alloys, or other corrosion-resistant materials. The material choice is driven by the specific application and the need for corrosion resistance.
2. Melting
The selected raw materials are heated to their melting point, typically in an electric arc furnace. This process transforms the solid material into a molten state.
3. Forming a Hollow Tube
The molten material is then formed into a hollow tube shape using a continuous casting process. This process allows for the creation of a seamless pipe without the need for welding.
4. Sizing and Shaping
The hollow tube is sized and shaped by a series of rollers and mandrels to achieve the desired dimensions and outer diameter.
5. Heat Treatment
EFW pipes often undergo heat treatment processes to improve their mechanical properties and eliminate residual stresses. This step enhances the material’s corrosion resistance and overall performance.
6. Cutting and Finishing
Once the pipe reaches the desired length, it is cut into individual sections. Additional finishing processes, such as end beveling and threading, may be applied to prepare the pipe for its specific application.
7. Testing
EFW pipes are subjected to rigorous testing procedures to ensure that they meet the required standards. This includes non-destructive testing techniques, such as ultrasonic testing and radiographic examination.
Don’t miss the Complete Course on Piping Engineering: Check Now
Enrollment Link
Key Differences in the Manufacturing Processes
The primary difference between the manufacturing processes of EFW and ERW pipes lies in the welding step. ERW pipes are created by electric resistance welding, which involves fusing the edges of a flat strip to form a pipe with a visible weld seam. In contrast, EFW pipes are made through the electric fusion welding of a molten material, resulting in a seamless pipe without any weld seam.
Types of EFW and ERW Pipes
Electric Resistance Welded (ERW) Pipes
ERW pipes come in various sizes and thicknesses. They can be classified into low-frequency ERW and high-frequency ERW, depending on the welding process. Low-frequency ERW is used for thicker pipes, while high-frequency ERW is suitable for thinner pipes.
Electric Fusion Welded (EFW) Pipes
EFW pipes are known for their exceptional corrosion resistance and are available in a wide range of materials, including stainless steel and nickel alloys. They are commonly used for transporting corrosive and high-temperature fluids in the oil and gas industry.
EFW vs ERW Pipes: Comparison
Aspect | EFW Pipes | ERW Pipes |
---|---|---|
Construction | Seamless, no weld seam | Welded, has a visible weld seam |
Corrosion Resistance | Highly corrosion-resistant | Susceptible to corrosion at the weld seam |
Cost | Generally more expensive | Cost-effective |
Applications | Corrosive environments, high-temperature applications | Various applications including oil and gas, construction |
Availability | May not be as readily available | Readily available in various sizes |
Standards Compliance | Must comply with API 5L, ASME B36.10M/B36.19M | Must comply with API 5L, ASME B36.10M/B36.19M |
Seam Integrity | Strong and seamless | Potential weak point at the weld seam |
High-Temperature Tolerance | Can withstand high temperatures | Suitable for low and moderate-temperature applications |
Versatility | Typically for specialized applications | Versatile for a wide range of applications |
Applications of EFW and ERW Pipes
Electric Resistance Welded (ERW) Pipes
ERW pipes are widely used in the oil and gas industry for various applications, including:
- Transportation of crude oil and natural gas
- Construction of pipelines and pipelines for water supply
- Structural components in construction
- Conveying chemicals and corrosive substances
Electric Fusion Welded (EFW) Pipes
EFW pipes are specifically chosen for applications requiring superior corrosion resistance and high-temperature performance, such as:
- Chemical processing industries
- Petrochemical plants
- Heat exchangers
- Power generation facilities
Advantages and Disadvantages
Electric Resistance Welded (ERW) Pipes
Advantages
- Cost-Effective: ERW pipes are cost-effective to manufacture, making them a popular choice for various applications.
- Availability: They are readily available in various sizes and specifications.
- Versatility: ERW pipes are suitable for both low and high-pressure applications.
Disadvantages
- Weld Seam: ERW pipes have a weld seam, which can be a weak point in high-pressure applications.
- Corrosion Susceptibility: The weld seam is more prone to corrosion compared to the rest of the pipe.
Don’t miss the Complete Course on Piping Engineering: Check Now
Enrollment Link
Electric Fusion Welded (EFW) Pipes
Advantages
- Seamless Design: EFW pipes have a seamless construction, eliminating the weak point of a weld seam.
- High Corrosion Resistance: They are highly resistant to corrosion, making them suitable for corrosive environments.
- High-Temperature Tolerance: EFW pipes can withstand high temperatures, which is crucial in certain applications.
Disadvantages
- Higher Cost: EFW pipes are more expensive to manufacture compared to ERW pipes.
- Limited Availability: They may not be as readily available as ERW pipes due to their specialized nature.
Associated Codes and Standards
In the oil and gas industry, adhering to specific codes and standards is paramount to ensure the safety and integrity of pipelines. Both EFW and ERW pipes must comply with various standards, including:
- API 5L: This American Petroleum Institute standard defines the requirements for the manufacturing and testing of ERW and EFW pipes used in the oil and gas industry.
- ASME B36.10M and ASME B36.19M: These standards outline the dimensions and sizes of steel pipes, including EFW and ERW pipes.
Compliance with these standards ensures that EFW and ERW pipes meet the necessary quality and safety requirements.
Conclusion
In the complex world of oil and gas transportation, choosing the right type of pipe is essential for ensuring the safety, efficiency, and longevity of pipelines. Electric Fusion Welded (EFW) and Electric Resistance Welded (ERW) pipes each have their own advantages and disadvantages, making them suitable for different applications. Understanding the distinctions between EFW and ERW pipes and considering their specific use cases is crucial for making informed decisions in the oil and gas industry. By adhering to industry standards and codes, project managers and engineers can ensure that the chosen pipes meet the necessary quality and safety requirements, contributing to the success of oil and gas projects worldwide.
Frequently Asked Questions (FAQs)
FAQ 1: What are the key differences between EFW and ERW pipes?
EFW pipes are seamless and have higher corrosion resistance, while ERW pipes have a welded seam and are more cost-effective.
FAQ 2: Which type of pipe is suitable for transporting crude oil and natural gas?
ERW pipes are commonly used for transporting crude oil and natural gas due to their cost-effectiveness and versatility.
FAQ 3: Where are EFW pipes predominantly used?
EFW pipes are preferred in industries with corrosive environments, such as chemical processing and petrochemical plants.
FAQ 4: Are there specific standards that EFW and ERW pipes must meet in the oil and gas industry?
Yes, both EFW and ERW pipes must comply with standards such as API 5L and ASME B36.10M/B36.19M to ensure quality and safety.
FAQ 5: What factors should I consider when choosing between EFW and ERW pipes for my project?
Consider factors like the application, operating conditions, and budget when selecting between EFW and ERW pipes.
Don’t miss the Complete Course on Piping Engineering: Check Now
Enrollment Link
Recommended courses (Published on EPCLand)
- Complete Course on Piping Engineering
- Basics of Piping Engineering
- Piping Layout Engineering
- Piping Material Engineering
- Piping Stress Analysis
- Material Requisitions
- Piping Material Specifications
- Valve Material Specifications
- Plant Design & Layouts-OISD 118
- Isometric Management
Library of Technical Articles
Don’t miss out the collection of 15+ articles on following topics:
- Basics of Oil and Gas Industry
- Valves
- Testing
- Tank
- Piping Bulk Items
- Pipe
- Metallurgy
- Piping Materials
- Layout
- Instrumentation
- Heat Exchanger
- Type of Contracts
- Codes and Standards
- ASTM Standards
- Articles on Piping Specialty Items
Video details of Complete Course on Piping Engineering
Attempt Quiz
Question 1:
What does EFW stand for in the context of pipes used in the Oil & Gas Industry?
Explanation: EFW stands for Electric Fusion Welding.
Question 2:
What is the primary method of joining pipes in ERW pipe manufacturing?
Explanation: ERW pipes are manufactured using the Electric Resistance Welding method.
Question 3:
Which type of pipe, EFW or ERW, is typically considered more cost-effective in terms of manufacturing?
Explanation: ERW pipes are typically considered more cost-effective in terms of manufacturing.
Question 4:
Which type of pipe is known for its high-strength and corrosion resistance, making it suitable for offshore applications?
Explanation: ERW pipes are known for their high-strength and corrosion resistance, making them suitable for offshore applications.
Question 5:
Which of the following factors is an advantage of EFW pipes over ERW pipes?
Explanation: EFW pipes have the advantage of a wider size range compared to ERW pipes.
Question 6:
Which welding method involves the use of a consumable electrode?
Explanation: Electric Fusion Welding (EFW) involves the use of a consumable electrode.
Question 7:
Which type of pipe is often used for transporting oil and natural gas over long distances?
Explanation: ERW pipes are often used for transporting oil and natural gas over long distances.
Question 8:
Which type of pipe is more commonly used in structural and construction applications?
Explanation: ERW pipes are more commonly used in structural and construction applications.
Question 9:
Which type of pipe manufacturing method results in a continuous seam along the length of the pipe?
Explanation: ERW pipe manufacturing results in a continuous seam along the length of the pipe.
Question 10:
Which type of pipe is commonly used for high-pressure and high-temperature applications in the Oil & Gas Industry?
Explanation: Neither EFW nor ERW pipes are commonly used for high-pressure and high-temperature applications in the Oil & Gas Industry; other methods like seamless pipes are preferred for such applications.