Introduction to Finned Tube Heat Exchangers
Heat exchangers play a crucial role in various industries, facilitating the efficient transfer of heat from one fluid to another. Among the various types of heat exchangers, finned tube heat exchangers stand out for their exceptional heat transfer capabilities and versatility. These devices find application in a wide range of sectors, from HVAC systems to industrial processes. In this article, we will explore the intricacies of finned tube heat exchangers, their design principles, applications, challenges, and the promising future trends shaping their evolution.
Table of Contents
Similar Articles on other Exchangers
Heat Exchanger Type | Check Article Link |
---|---|
Helical Coil Heat Exchanger | Link |
Tube-in-Tube Heat Exchanger | Link |
Spiral Heat Exchanger | Link |
U-Tube Heat Exchanger | Link |
Shell and Tube Heat Exchanger | Link |
Plate Heat Exchanger | Link |
Double Pipe Heat Exchanger | Link |
Finned Tube Heat Exchanger | Link |
Don’t miss the Detailed course on Drums/Exchanger Piping Layout & Stress Analysis
Enrollment Link
Types of Heat Exchangers
Heat exchangers can be classified based on their construction, and among these classifications are shell and tube heat exchangers, plate heat exchangers, and finned tube heat exchangers. While all three types serve the purpose of heat transfer, finned tube heat exchangers exhibit distinct advantages. These devices consist of tubes with extended surfaces, known as fins, attached to them. The primary benefit of finned tubes is the substantial increase in surface area, which enhances heat transfer efficiency. This characteristic makes them ideal for applications where compactness and high efficiency are paramount.
Understanding Finned Tube Heat Exchangers
What are Finned Tubes?
Finned tubes are tubes that have extended surfaces, called fins, running along their length. These fins effectively increase the surface area available for heat transfer between the fluid inside the tubes and the fluid surrounding them. Fins can come in various configurations, including plain, serrated, and perforated, each offering specific advantages depending on the application.
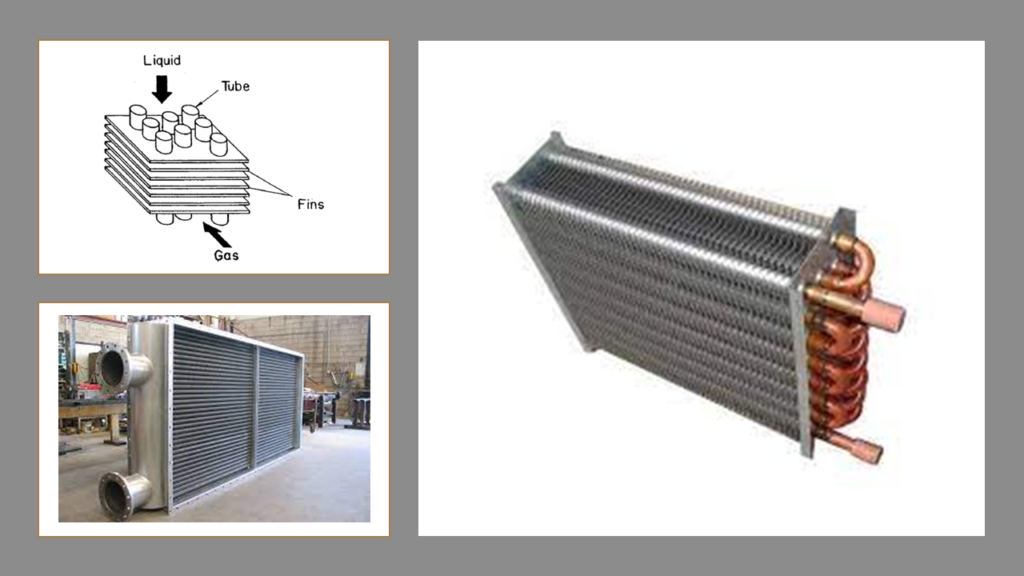
Mechanism of Heat Transfer
Heat transfer in finned tube heat exchangers involves conduction, convection, and radiation. Conduction occurs within the tube walls, while convection facilitates the exchange of heat between the fluid and the finned surface. The increased surface area due to fins promotes convective heat transfer. Additionally, radiation heat transfer occurs between surfaces at different temperatures. The combination of these mechanisms results in efficient heat exchange, making finned tube heat exchangers highly effective.
Importance of Fins in Heat Exchangers
Fins significantly enhance the heat transfer process. By increasing the surface area exposed to the fluid, fins amplify the rate of heat exchange. This characteristic is particularly advantageous when dealing with fluids that have low heat transfer coefficients. The augmented heat transfer efficiency provided by fins allows heat exchangers to achieve the desired temperature changes with reduced equipment size, making them a valuable solution in situations with space constraints.
Design and Construction
Tube-and-Fin Arrangements
Finned tubes can be arranged in two primary configurations: inline and staggered. In the inline arrangement, the fins of adjacent tubes are aligned, creating a regular pattern. Staggered arrangements introduce a deliberate offset between the fins of neighboring tubes, disrupting the flow path and promoting better heat transfer. Staggered arrangements are preferred for applications where enhanced efficiency is a priority.
Tube and Fin Materials
The choice of materials for tubes and fins is crucial for ensuring the longevity and effectiveness of finned tube heat exchangers. Common materials include aluminum, copper, stainless steel, and carbon steel. The selection depends on factors such as the fluids involved, operating temperatures, and the potential for corrosion. Compatibility between materials is essential to prevent galvanic corrosion.
Manufacturing Processes
Finned tubes are manufactured using various techniques, each catering to specific requirements. Extruded finned tubes involve the creation of fins by extruding material from the tube’s surface. Welded finned tubes, on the other hand, have fins welded onto the tubes. Embedded finned tubes feature fins embedded into the tube walls through a metal deformation process. Each manufacturing method offers distinct advantages in terms of efficiency, cost, and performance.
Don’t miss the Detailed course on Drums/Exchanger Piping Layout & Stress Analysis
Enrollment Link
Performance and Efficiency
Heat Transfer Coefficients
The efficiency of a finned tube heat exchanger is influenced by the heat transfer coefficients between the fluids and the finned surface. External flow configurations, where fluids flow outside the tubes, typically have lower coefficients than internal flow configurations. The geometry of the fins, such as fin thickness and spacing, plays a crucial role in determining these coefficients.
Factors Affecting Performance
Several factors impact the performance of finned tube heat exchangers. Fluid velocity and flow regimes affect the convective heat transfer process. Higher velocities can lead to turbulence, enhancing heat transfer. Temperature differences between the fluids also influence the rate of heat exchange. Fouling, the accumulation of deposits on the heat transfer surfaces, can decrease efficiency over time and necessitate maintenance.
Thermal Design Considerations
The Log Mean Temperature Difference (LMTD) method is commonly used in the thermal design of heat exchangers. It considers the inlet and outlet temperatures of both fluids to calculate the temperature difference driving the heat transfer. The Effectiveness-NTU (Number of Transfer Units) method is another approach that relates the heat exchanger’s effectiveness to the NTU value, incorporating the heat capacity rates of the fluids.
Applications of Finned Tube Heat Exchangers
HVAC Systems
Finned tube heat exchangers find extensive use in heating, ventilation, and air conditioning (HVAC) systems. In air conditioning and refrigeration units, they facilitate the transfer of heat between refrigerants and air. Heat recovery ventilation systems employ finned tube heat exchangers to recover heat from exhaust air, preheating incoming fresh air and improving energy efficiency.
Don’t miss the Detailed course on Drums/Exchanger Piping Layout & Stress Analysis
Enrollment Link
Industrial Processes
The versatility of finned tube heat exchangers is evident in their applications across various industries. In the petrochemical sector, these exchangers play a pivotal role in refining processes, where they facilitate the exchange of heat between fluids in different stages of production. Power generation plants utilize them in cooling systems for efficient dissipation of excess heat. The food and beverage industry benefits from their use in pasteurization and sterilization processes.
Automotive and Aerospace Applications
Finned tube heat exchangers also find application in the automotive and aerospace industries. In vehicles, they assist in engine cooling, air conditioning, and transmission oil cooling. In aerospace, these heat exchangers help regulate temperatures in electronic systems, hydraulics, and cabin ventilation. Their compact design and efficient heat transfer capabilities make them essential components in ensuring optimal performance and safety.
Advancements and Innovations
High-Efficiency Fin Geometries
Researchers are continually exploring innovative fin geometries to enhance heat transfer efficiency. These geometries may include vortex generators, perforated fins, and enhanced surface coatings. Such developments aim to further amplify heat exchange rates and improve overall performance.
Computational Fluid Dynamics (CFD) in Design
Computational Fluid Dynamics (CFD) simulations play a significant role in the design and optimization of finned tube heat exchangers. These simulations allow engineers to visualize fluid flow patterns, temperature distributions, and pressure gradients, enabling them to fine-tune design parameters for maximum efficiency.
Compact and Micro Finned Heat Exchangers
Advancements in microfabrication techniques have led to the development of compact and micro finned heat exchangers. These miniaturized versions find application in electronics cooling, medical devices, and portable cooling systems. Their reduced size and weight make them suitable for applications where space constraints are critical.
Integration with Renewable Energy Systems
Finned tube heat exchangers are being integrated into renewable energy systems, such as solar thermal installations and geothermal heat pumps. These applications leverage the heat transfer capabilities of finned tubes to enhance energy capture and utilization, contributing to the growth of sustainable energy solutions.
Challenges and Limitations
Cost Considerations
The manufacturing complexity and material costs associated with finned tube heat exchangers can contribute to higher upfront expenses compared to other heat exchanger types. However, the enhanced performance and energy savings over time often justify these initial costs.
Maintenance and Cleaning Difficulties
Fouling and scaling can decrease heat exchanger efficiency over time. The presence of fins can complicate cleaning processes, requiring specialized methods to ensure optimal heat transfer performance. Regular maintenance practices are crucial to prevent a decline in efficiency.
Potential for Corrosion and Erosion
In environments with aggressive fluids or varying temperatures, corrosion and erosion can affect the longevity of finned tube heat exchangers. Proper material selection, coatings, and corrosion prevention measures are essential to mitigate these challenges.
Performance in Extreme Conditions
Finned tube heat exchangers may face challenges when exposed to extreme temperatures, pressure differentials, or corrosive environments. Design modifications and careful consideration of materials are necessary to ensure reliable performance under these conditions.
Don’t miss the Detailed course on Drums/Exchanger Piping Layout & Stress Analysis
Enrollment Link
Comparison with Other Heat Exchanger Types
Finned Tube vs. Shell and Tube Exchangers
While both finned tube heat exchangers and shell and tube exchangers serve similar purposes, they excel in different scenarios. Finned tubes are more compact and suited for applications requiring high heat transfer efficiency within limited space. Shell and tube exchangers, on the other hand, are better suited for high-pressure applications and situations where maintenance and cleaning are more accessible.
Finned Tube vs. Plate Heat Exchangers
Finned tube heat exchangers and plate heat exchangers are often compared due to their compact designs. Plate heat exchangers are preferred for applications requiring efficient heat transfer between low-viscosity fluids, while finned tube exchangers are better suited for situations involving high-viscosity fluids or air-to-fluid heat transfer.
Aspect | Finned Tube Heat Exchangers | Shell and Tube Exchangers | Plate Heat Exchangers |
---|---|---|---|
Heat Transfer Mechanism | Conduction, Convection, Radiation | Conduction, Convection | Conduction, Convection |
Efficiency | High due to extended surface area | Efficient | Efficient |
Compactness | Compact design with enhanced surface area | Bulkier | Compact |
Space Constraints | Ideal for limited space applications | Require more space | Space-efficient |
Fluid Compatibility | Versatile for various fluid types | Versatile | Suitable for low-viscosity fluids |
Maintenance and Cleaning | Cleaning may be challenging due to fins | Easier maintenance | Easier maintenance |
Pressure Handling | Lower pressure handling capacity | High pressure handling | Moderate pressure handling |
Corrosion Resistance | Material selection critical for corrosion resistance | Resistant materials | Material-dependent |
Applications | HVAC, Industrial, Automotive, Aerospace | Industrial, Chemical | HVAC, Industrial |
Adaptability | Adaptable to different fluid and temperature ranges | Suitable for diverse fluids | Limited to specific fluids |
Heat Transfer Area | Larger effective surface area due to fins | Adequate area | Moderate area |
Maintenance | Regular maintenance required due to fin cleaning | Regular maintenance | Regular maintenance |
Don’t miss the Detailed course on Drums/Exchanger Piping Layout & Stress Analysis
Enrollment Link
Future Trends in Finned Tube Heat Exchangers
Enhanced Materials and Coatings
Advancements in material science are expected to yield heat exchanger materials with improved corrosion resistance and thermal conductivity. Innovative coatings may also play a role in enhancing heat transfer efficiency and extending the lifespan of finned tube heat exchangers.
IoT and Automation Integration
The integration of Internet of Things (IoT) technology and automation systems will enable real-time monitoring and control of heat exchanger performance. Data analytics and predictive maintenance algorithms can optimize heat exchanger operation, improving efficiency and reducing downtime.
Sustainability and Eco-Friendly Designs
As industries focus on sustainability, heat exchangers will see advancements in designs that minimize energy consumption and environmental impact. Efforts to reduce refrigerant leakage in HVAC systems and the incorporation of eco-friendly materials align with global efforts to mitigate climate change.
Case Studies
Heat Exchangers in Oil Refineries
In oil refineries, finned tube heat exchangers play a vital role in processes such as crude oil distillation, catalytic cracking, and hydrocracking. Their efficient heat transfer capabilities contribute to the production of refined products while minimizing energy consumption.
Aerospace Cooling Systems
In the aerospace industry, finned tube heat exchangers are crucial for regulating temperatures in aircraft components. These exchangers assist in managing heat generated by avionics, engines, and environmental control systems, ensuring optimal performance and safety.
Geothermal Power Plants
Finned tube heat exchangers play a key role in geothermal power generation, where they facilitate heat exchange between the geothermal fluid and a working fluid used to generate electricity. Their efficiency is essential in harnessing the Earth’s natural heat for sustainable energy production.
Conclusion
Finned tube heat exchangers stand as exemplars of efficient heat transfer technology, finding applications across industries where compactness, efficiency, and versatility are paramount. Their ability to enhance heat exchange rates through the use of extended surfaces offers significant benefits, from space-saving designs to improved energy efficiency. As research and innovation continue to shape the field of heat exchangers, finned tube heat exchangers are poised to play a pivotal role in meeting the world’s growing energy and thermal management needs. By understanding their design principles, applications, challenges, and future trends, engineers and industries can harness the potential of these remarkable devices to create more sustainable and efficient systems.
FAQs
FAQ 1: What is a finned tube heat exchanger, and how does it work?
Answer: A finned tube heat exchanger is a type of heat transfer device designed to efficiently exchange heat between two fluids. It consists of tubes with extended surfaces, called fins, attached along their length. The fins significantly increase the surface area available for heat transfer, which enhances the overall efficiency of the exchanger. The mechanism involves conduction, convection, and radiation. Conduction occurs through the tube walls, while convection facilitates the transfer of heat between the fluid and the finned surface. The increased surface area due to the fins promotes convective heat transfer, and radiation heat transfer occurs between surfaces at different temperatures.
FAQ 2: What are the advantages of using finned tube heat exchangers?
Answer: Finned tube heat exchangers offer several advantages:
- Enhanced Efficiency: The extended surface area provided by fins results in higher heat transfer rates and improved efficiency.
- Compact Design: Finned tubes allow for efficient heat transfer in a relatively small space, making them suitable for applications with space constraints.
- Adaptability: They are versatile and can handle various fluid types, making them suitable for different industries and processes.
- Temperature Control: Finned tube exchangers are effective at regulating fluid temperatures, making them ideal for applications requiring precise temperature control.
FAQ 3: What are some common applications of finned tube heat exchangers?
Answer: Finned tube heat exchangers are used in a wide range of applications, including:
- HVAC Systems: They are integral components of air conditioning, refrigeration, and heat recovery ventilation systems.
- Industrial Processes: They find use in the petrochemical industry, power generation, food processing, and other industrial processes.
- Automotive and Aerospace: These exchangers play roles in engine cooling, cabin ventilation, and electronics cooling in vehicles and aircraft.
FAQ 4: What factors should be considered during the design of finned tube heat exchangers?
Answer: Several factors influence the design of finned tube heat exchangers:
- Fluid Properties: The properties of the fluids involved, such as viscosity and thermal conductivity, impact heat transfer rates.
- Finned Geometry: The design of the fins, including thickness, spacing, and arrangement, affects heat transfer efficiency.
- Flow Rates: Fluid flow rates, velocity, and flow patterns influence the overall performance of the heat exchanger.
- Temperature Differences: The temperature difference between the fluids significantly influences heat transfer rates.
- Materials: Choosing suitable materials based on the fluids, temperatures, and potential corrosion is crucial.
FAQ 5: What are the future trends and innovations in finned tube heat exchangers?
Answer: The future of finned tube heat exchangers holds several exciting trends:
- Advanced Materials: Research is focusing on materials with improved thermal conductivity and corrosion resistance.
- IoT Integration: Internet of Things (IoT) technology and automation will enable real-time monitoring and optimization of heat exchanger performance.
- Sustainability: Design advancements will prioritize energy efficiency and environmentally friendly materials.
- Enhanced Geometries: Ongoing research aims to develop novel fin geometries to further enhance heat transfer efficiency.
Don’t miss the Detailed course on Drums/Exchanger Piping Layout & Stress Analysis
Enrollment Link
Recommended courses (Published on EPCLand)
- Basics of Piping Engineering
- Piping Layout Engineering
- Piping Material Engineering
- Piping Stress Analysis
- Complete Course on Piping Engineering
- Material Requisitions
- Piping Material Specifications
- Valve Material Specifications
Don’t miss the published articles on following:
Related Video
Attempt Quiz
Question 1:
What is the primary purpose of finned tubes in a heat exchanger?
Explanation: The primary purpose of finned tubes in a heat exchanger is to enhance heat transfer efficiency by increasing the surface area available for heat exchange.
Question 2:
What are some common applications of finned tube heat exchangers?
Explanation: Finned tube heat exchangers are commonly used in air conditioning systems, automotive engine cooling, and various industrial processes where efficient heat exchange is essential.
Question 3:
Which type of finned tube arrangement provides better heat transfer performance?
Explanation: Staggered finned tube arrangements are known to provide better heat transfer performance compared to inline arrangements, as they disrupt the flow and enhance heat exchange.
Question 4:
What is the purpose of using fins with different shapes and materials in finned tube heat exchangers?
Explanation: Fins with different shapes and materials are used in finned tube heat exchangers to optimize heat transfer performance for specific applications, ensuring efficient heat exchange between fluids.
Question 5:
What is the term for the ratio of the actual heat transfer rate to the theoretical maximum heat transfer rate in a finned tube heat exchanger?
Explanation: The term for the ratio of the actual heat transfer rate to the theoretical maximum heat transfer rate in a finned tube heat exchanger is called “Effectiveness.”