Introduction to Helical Coil Heat Exchangers
Heat exchangers play a critical role in various industries by facilitating the efficient transfer of thermal energy between two fluids, while keeping them physically separate. Among the various types of heat exchangers, helical coil heat exchangers stand out for their innovative design and effective heat transfer capabilities. In this article, we will delve into the design principles, operational advantages, industrial applications, and future trends of helical coil heat exchangers.
Table of Contents
Don’t miss the Detailed course on Drums/Exchanger Piping Layout & Stress Analysis
Enrollment Link
Definition and Purpose of Heat Exchangers
Heat exchangers are devices designed to transfer heat between two or more fluids, allowing them to reach different temperatures without mixing. They are widely used in industries such as petrochemicals, HVAC, renewable energy, and food processing. Heat exchangers serve several purposes, including heating, cooling, condensation, and evaporation.
Introduction to Helical Coil Heat Exchangers
Helical coil heat exchangers are a specific type of heat exchanger that utilizes a coiled tube configuration to facilitate heat transfer between fluids. The coil’s helical shape provides a longer flow path, promoting better heat exchange. This design allows for increased heat transfer efficiency and compactness compared to traditional straight-tube heat exchangers.
Advantages and Applications of Helical Coil Heat Exchangers
Helical coil heat exchangers offer several advantages over other types of heat exchangers. Their compact design and enhanced heat transfer efficiency make them ideal for applications where space is limited. Additionally, the helical geometry promotes turbulence within the fluid, further improving heat transfer rates. These heat exchangers find applications in various industries, including petrochemicals, HVAC, renewable energy, and food processing.
Similar Articles on other Exchangers
Heat Exchanger Type | Check Article Link |
---|---|
Helical Coil Heat Exchanger | Link |
Tube-in-Tube Heat Exchanger | Link |
Spiral Heat Exchanger | Link |
U-Tube Heat Exchanger | Link |
Shell and Tube Heat Exchanger | Link |
Plate Heat Exchanger | Link |
Double Pipe Heat Exchanger | Link |
Finned Tube Heat Exchanger | Link |
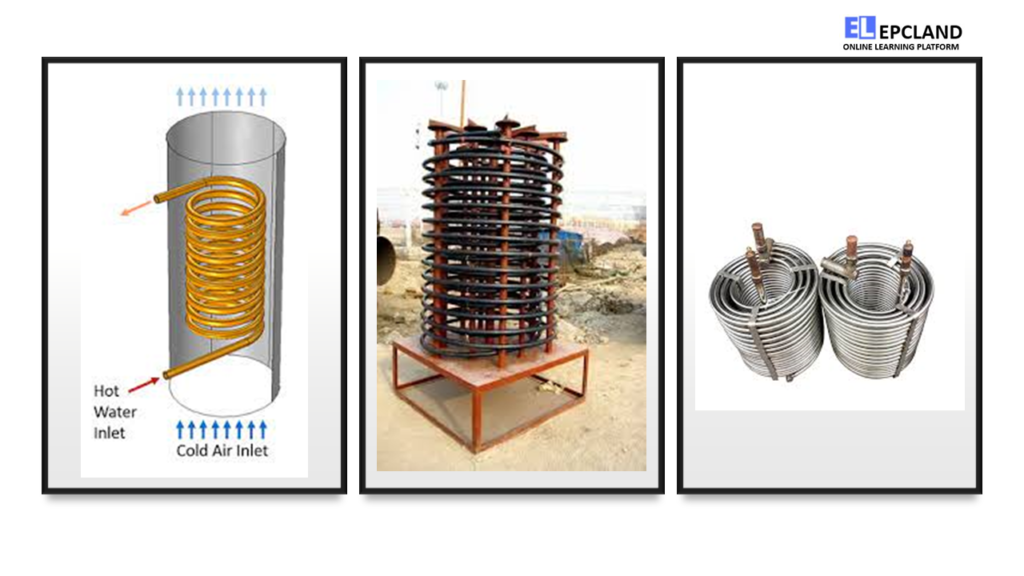
Design and Construction of Helical Coil Heat Exchangers
Basic Components of a Helical Coil Heat Exchanger
A typical helical coil heat exchanger consists of a coiled tube, which serves as the heat transfer surface, and an outer shell that encloses the coil. The coil geometry and arrangement significantly impact the heat exchanger’s performance. The tube material and size, as well as the shell and tube side configurations, play vital roles in the design.
Coil Geometry and Arrangement
The helical coil’s geometry, including parameters such as coil pitch, diameter, and number of turns, affects the heat transfer characteristics. A tighter coil pitch and larger diameter generally enhance heat transfer rates, but at the cost of increased pressure drop.
Tube Materials and Sizing
The choice of tube material is crucial, as it determines the heat exchanger’s compatibility with the fluids being processed. Common materials include stainless steel, copper, and various alloys. Proper sizing of the tube diameter ensures optimal heat transfer while considering fluid flow rates and pressure drop.
Shell and Tube Side Configurations
Helical coil heat exchangers can have single or multiple coils arranged in parallel or series. The arrangement affects fluid flow patterns and heat transfer rates. Co-current and counter-current flow configurations offer different temperature profiles and overall heat transfer efficiency.
Heat exchangers are devices designed to transfer heat between two or more fluids, allowing them to reach different temperatures without mixing. They are widely used in industries such as petrochemicals, HVAC, renewable energy, and food processing. Heat exchangers serve several purposes, including heating, cooling, condensation, and evaporation.
Don’t miss the Detailed course on Drums/Exchanger Piping Layout & Stress Analysis
Enrollment Link
Types of Helical Coil Heat Exchangers
Helical coil heat exchangers can be categorized based on the number of coils and the flow direction of the fluids.
Single Coil vs. Multi-Coil Arrangements
Single coil heat exchangers are simpler in design and suitable for applications with single-phase fluids. Multi-coil arrangements provide increased heat transfer surface area and flexibility to handle multiple fluid streams.
Co-Current vs. Counter-Current Flow
In co-current flow, both fluids move in the same direction, while in counter-current flow, they move in opposite directions. Counter-current flow generally yields higher heat transfer rates and improved overall efficiency due to the larger temperature difference across the coil.
Factors Influencing Design Considerations
Several factors influence the design of helical coil heat exchangers, ensuring optimal performance and operational efficiency.
Heat Transfer Requirements
The required heat transfer rate dictates the heat exchanger’s size and configuration. Balancing this requirement with other factors is essential for achieving desired results.
Fluid Properties and Compatibility
Fluid properties, such as viscosity, density, and thermal conductivity, influence heat transfer rates. Compatibility between the fluids and the materials of construction must also be considered to prevent corrosion or contamination.
Fouling and Maintenance Considerations
The coil’s helical geometry can mitigate fouling to some extent, but it’s essential to account for potential fouling due to impurities in the fluids. Proper maintenance strategies should be implemented to ensure sustained performance.
Don’t miss the Detailed course on Drums/Exchanger Piping Layout & Stress Analysis
Enrollment Link
Heat Transfer Principles in Helical Coil Heat Exchangers
Conduction, Convection, and Radiation in Heat Transfer
Heat transfer in helical coil heat exchangers occurs through conduction, convection, and, to a lesser extent, radiation. Conduction involves the transfer of heat through direct contact between solids. Convection is the heat transfer due to fluid motion, which is enhanced by the coil’s helical shape. Radiation is the transfer of heat through electromagnetic waves but is typically negligible in these types of heat exchangers.
Heat Transfer Mechanisms within the Helical Coil
The helical coil’s design promotes turbulent flow within the fluid, leading to increased convective heat transfer. The extended flow path along the coil enhances contact time between the fluids, further improving heat exchange efficiency. The choice of flow direction (co-current or counter-current) significantly affects heat transfer rates.
Calculation of Overall Heat Transfer Coefficient (U-Value)
The overall heat transfer coefficient (U-value) is a crucial parameter that represents the heat transfer effectiveness of the exchanger. It accounts for conduction, convection, and other factors. The U-value is used in conjunction with the log mean temperature difference (LMTD) to calculate the heat exchanger’s performance.
Effectiveness-NTU Method for Performance Evaluation
The Effectiveness-Number of Transfer Units (ε-NTU) method is commonly used to evaluate the performance of helical coil heat exchangers. It relates the heat exchanger’s effectiveness (ε) to the number of transfer units (NTU) based on the heat capacity rates of the fluids.
Performance Enhancement Techniques
Flow Optimization within the Coil
Reynolds Number and Laminar/Turbulent Flow
The Reynolds number determines the flow regime within the coil—laminar or turbulent. Turbulent flow, characterized by higher Reynolds numbers, enhances heat transfer by promoting fluid mixing and increasing the convective heat transfer coefficient.
Helix Pitch and Diameter Effects
Optimizing the helix pitch and diameter influences heat transfer rates and pressure drop. Smaller pitch values and larger diameters generally enhance heat transfer efficiency but might result in higher pressure drop. Balancing these factors is essential for optimal design.
Surface Enhancements for Improved Heat Transfer
Extended Surfaces and Fins
The addition of fins or extended surfaces to the coil tube further amplifies heat transfer. Fins increase the surface area available for heat exchange, improving overall efficiency without significantly increasing the size of the heat exchanger.
Nanocoatings and Enhanced Materials
Advanced coatings and materials, such as nanocoatings and heat-conductive polymers, can be applied to the coil surface to enhance heat transfer properties. These materials often have high thermal conductivity and improve the efficiency of the heat exchanger.
Don’t miss the Detailed course on Drums/Exchanger Piping Layout & Stress Analysis
Enrollment Link
Fluid-Side Enhancements
Phase Change Materials (PCMs)
Phase change materials are substances that undergo a phase transition, such as solid-to-liquid or liquid-to-gas, as they exchange heat. Incorporating PCMs in the heat exchanger can significantly enhance heat storage and release capabilities, making them useful in applications requiring thermal energy storage.
Nanofluids and Their Applications
Nanofluids are suspensions of nanoparticles in a base fluid. These fluids exhibit improved heat transfer properties due to the enhanced thermal conductivity of nanoparticles. Helical coil heat exchangers can benefit from nanofluids in terms of increased heat transfer rates and improved energy efficiency.
Industrial Applications of Helical Coil Heat Exchangers
Helical coil heat exchangers find diverse applications across various industries, where their compact design and efficient heat transfer capabilities offer significant advantages.
Petrochemical and Chemical Industries
In petrochemical and chemical processes, helical coil heat exchangers are used for tasks such as crude oil refining and chemical synthesis. Their compact design allows for integration into tight spaces within complex chemical plants.
Crude Oil Refining
Helical coil heat exchangers are employed in the distillation of crude oil, where they facilitate the separation of different fractions based on their boiling points. The efficient heat transfer properties of helical coils enable precise control over the distillation process.
Chemical Synthesis Processes
In chemical synthesis, precise temperature control is crucial to achieve desired reaction rates and product yields. Helical coil heat exchangers play a vital role in maintaining optimal reaction temperatures while ensuring efficient heat transfer.
HVAC and Refrigeration Systems
The HVAC and refrigeration industry benefits from helical coil heat exchangers due to their compactness and versatility.
Heat Pumps and Air Conditioning
Helical coil heat exchangers are used in heat pumps and air conditioning systems to transfer heat between the refrigerant and the indoor/outdoor air. The efficient heat exchange within the coils contributes to energy-efficient cooling and heating.
Refrigerant Condensation and Evaporation
Helical coil heat exchangers aid in refrigerant condensation and evaporation processes. During condensation, the coils release heat to the surroundings, while during evaporation, they absorb heat from the surroundings, enabling efficient cooling cycles.
Renewable Energy Systems
Renewable energy sources like solar and geothermal energy benefit from the heat transfer capabilities of helical coil heat exchangers.
Solar Water Heaters
In solar water heaters, helical coil heat exchangers are used to transfer heat from solar collectors to the water supply. The coils efficiently capture and transfer solar energy to heat water for domestic or industrial use.
Geothermal Heat Exchange
Helical coil heat exchangers are integral components of geothermal heat exchange systems. They facilitate the transfer of thermal energy between the ground and a fluid circulating through the coil, providing heating or cooling for buildings.
Don’t miss the Detailed course on Drums/Exchanger Piping Layout & Stress Analysis
Enrollment Link
Food and Beverage Processing
In the food and beverage industry, hygienic heat transfer solutions are crucial for processes like pasteurization, sterilization, cooking, and cooling.
Pasteurization and Sterilization Processes
Helical coil heat exchangers ensure precise temperature control during pasteurization and sterilization, effectively eliminating harmful microorganisms while preserving the quality of the product.
Cooking and Cooling Applications
From large-scale food production to smaller commercial kitchens, helical coil heat exchangers are employed in cooking and cooling applications, where they facilitate rapid heating or cooling of food products.
Case Studies: Real-World Examples
Helical Coil Heat Exchanger in a Petrochemical Plant
In a petrochemical plant’s distillation unit, a helical coil heat exchanger was integrated to enhance the separation of crude oil fractions. The design considered the optimal coil pitch and diameter for efficient heat transfer. Challenges included maintaining a low pressure drop to avoid disrupting the distillation process. Through computational fluid dynamics (CFD) simulations, the design was refined, resulting in improved heat transfer rates and reduced energy consumption. The helical coil heat exchanger successfully contributed to higher yield and purity of the distillation products.
Helical Coil Heat Exchanger in Renewable Energy
A solar water heating system incorporated a helical coil heat exchanger to transfer solar energy to water for domestic use. The coil’s geometry was optimized to maximize heat transfer efficiency while maintaining a compact design. The solar water heater’s performance was enhanced by using nanofluids as the heat transfer medium. The combination of the helical coil and nanofluids resulted in increased energy capture and improved overall system efficiency. This example showcases how innovative design and advanced materials can amplify the benefits of helical coil heat exchangers in renewable energy applications.
Helical Coil Heat Exchanger for Food Processing
In a food processing facility, a helical coil heat exchanger was employed for rapid cooling of a liquid food product after sterilization. The coil’s design minimized fouling and ensured compliance with food safety regulations. Regular inspection and cleaning procedures were implemented to prevent contamination. The helical coil heat exchanger contributed to efficient cooling, extending the shelf life of the product and maintaining its quality. This case study emphasizes the importance of hygienic design and maintenance in food processing applications.
Advantages and Limitations of Helical Coil Heat Exchangers
Pros | Cons |
---|---|
Compact design, space-efficient | Higher pressure drop compared to other designs |
Enhanced heat transfer efficiency | Complex design and manufacturing |
Versatile for diverse industrial applications | Limited compatibility with certain fluids |
Suitable for applications with space constraints | Potential for fouling and maintenance challenges |
Efficient turbulent flow enhances heat transfer | Requires expertise in design and operation |
Improved performance in counter-current flow | |
Potential for innovative material and design |
Don’t miss the Detailed course on Drums/Exchanger Piping Layout & Stress Analysis
Enrollment Link
Codes & Standards
Code/Standard | Description |
---|---|
ASME Boiler and Pressure Vessel Code | Set of standards for the design, fabrication, and inspection of boilers, pressure vessels, and related equipment. |
ASME B16.9 | Standard for factory-made wrought buttwelding fittings. |
ASME B31.3 | Process Piping Code specifying requirements for process piping systems. |
TEMA | Tubular Exchanger Manufacturers Association’s standards for shell-and-tube heat exchangers. |
API 661 | Air-Cooled Heat Exchangers for General Refinery Service, providing specifications for air-cooled heat exchangers. |
ASTM | American Society for Testing and Materials standards for materials and testing methods. |
ANSI | American National Standards Institute, responsible for promoting and facilitating voluntary consensus standards. |
ISO | International Organization for Standardization, develops and publishes international standards. |
PED (Pressure Equipment Directive) | European Union directive concerning the design, manufacturing, and conformity assessment of pressure equipment. |
EN | European Norm standards applicable to mechanical equipment, materials, and testing. |
Future Trends and Innovations
The field of helical coil heat exchangers is evolving, with several trends and innovations shaping their future.
Computational Fluid Dynamics (CFD) in Design
Advancements in CFD simulations allow for detailed analysis of fluid flow and heat transfer within helical coils. CFD tools help optimize coil geometry and flow patterns, leading to more efficient designs.
Additive Manufacturing for Customized Coils
Additive manufacturing, or 3D printing, enables the production of intricate coil geometries that were previously challenging to manufacture. Customized coils can be designed for specific applications, further enhancing heat transfer efficiency.
Integration of Smart Technologies for Real-Time Monitoring
The integration of sensors and monitoring systems allows real-time tracking of heat exchanger performance. Smart technologies enable timely maintenance and optimization, leading to increased operational efficiency.
Advances in Heat Transfer Fluids and Materials
Ongoing research in heat transfer fluids and materials will likely yield new options that can enhance heat exchange efficiency. This includes the development of fluids with improved thermal conductivity and stability.
Don’t miss the Detailed course on Drums/Exchanger Piping Layout & Stress Analysis
Enrollment Link
Comparison
Criteria | Helical Coil Heat Exchangers | Shell-and-Tube Heat Exchangers | Plate Heat Exchangers |
---|---|---|---|
Design | Compact, efficient use of space | Larger footprint, more space required | Compact and space-efficient |
Heat Transfer Efficiency | Enhanced due to turbulent flow and extended surface | Good heat transfer efficiency | Good heat transfer efficiency |
Pressure Drop | Can have higher pressure drop | Moderate pressure drop | Lower pressure drop |
Flexibility | Moderate flexibility in design due to coil geometry | High flexibility in design, multiple configurations | Moderate flexibility |
Maintenance | May require specialized maintenance due to coil complexity | Generally straightforward maintenance | Generally straightforward maintenance |
Cost | Can be cost-effective due to compact design | Typically higher initial cost | Moderately priced |
Materials Compatibility | Limited by fluid compatibility | Versatile materials compatibility | Versatile materials compatibility |
Applications | Diverse applications, especially in limited space | Wide range of industrial applications | Compact installations, limited by pressure and temperature |
Heat Transfer Mechanisms | Conduction, convection, radiation | Conduction, convection | Conduction, turbulence |
Efficiency in Counter-Current Flow | Generally efficient due to extended surface | Efficient due to temperature difference | Efficient due to turbulent flow |
Installation Complexity | Moderate complexity due to coil arrangement | Moderate complexity due to tube bundle | Relatively simple installation |
Size and Weight | Compact and lightweight | Bulkier and heavier | Compact and lightweight |
Maintenance and Cleaning Considerations | Potential for fouling in coil | Generally accessible for cleaning | Generally accessible for cleaning |
Please note that the comparison is meant to provide a general overview and that specific applications and requirements may lead to variations in performance. It’s essential to consider factors such as heat transfer efficiency, pressure drop, maintenance, and compatibility with the fluid being processed when selecting the most suitable heat exchanger type for a particular application.
Maintenance and Operational Considerations
Cleaning and Fouling Prevention Strategies
Regular cleaning and maintenance are essential to prevent fouling, which can reduce heat transfer efficiency. Proper fluid filtration, use of suitable materials, and adherence to maintenance schedules are crucial.
Inspection and Maintenance Procedures
Helical coil heat exchangers should undergo regular inspection to identify signs of corrosion, fouling, or mechanical damage. Non-destructive testing methods can be employed to assess the coil’s integrity.
Troubleshooting Common Issues
Addressing issues such as uneven heat distribution, inadequate heat transfer, or excessive pressure drop requires a thorough understanding of the heat exchanger’s design and operation. Troubleshooting protocols should be established to quickly identify and rectify problems.
Conclusion
Helical coil heat exchangers exemplify the innovation and efficiency that modern engineering brings to thermal management. Their unique coil design, coupled with enhanced heat transfer capabilities, makes them invaluable across industries ranging from petrochemicals to renewable energy. As technology continues to advance, helical coil heat exchangers will likely play an increasingly significant role in meeting the heat transfer needs of diverse applications. The ongoing research and development in this field promise to unlock even greater efficiency and versatility in the years to come.
This table provides a quick overview of the advantages and limitations of helical coil heat exchangers. Keep in mind that the significance of each point may vary depending on the specific application and operational context.
Don’t miss the Detailed course on Drums/Exchanger Piping Layout & Stress Analysis
Enrollment Link
FAQs
1. What is a helical coil heat exchanger, and how does it work?
A helical coil heat exchanger is a type of heat exchanger that uses a coiled tube arrangement to transfer heat between fluids. The coil’s helical shape enhances heat transfer efficiency by promoting turbulent flow and extending the flow path. Fluids flow through the coil, where heat is transferred from one fluid to the other through conduction, convection, and, to a lesser extent, radiation.
2. What are the advantages of using helical coil heat exchangers?
Helical coil heat exchangers offer several advantages, including:
- Compact design, making them suitable for installations with limited space.
- Enhanced heat transfer efficiency due to the coil’s geometry and turbulent flow.
- Versatility across various industries and applications.
- Efficient performance in counter-current flow configurations.
- Potential for innovative material choices and custom designs.
3. What are the limitations or challenges associated with helical coil heat exchangers?
Some limitations and challenges of helical coil heat exchangers include:
- Higher pressure drop compared to certain other designs.
- Complex design and manufacturing processes.
- Limited compatibility with specific fluids due to potential fouling or material concerns.
- The need for expertise in both design and operation.
- Potential maintenance challenges due to the coil’s intricate geometry.
4. How are helical coil heat exchangers used in different industries?
Helical coil heat exchangers find applications in various industries, such as:
- Petrochemical and chemical industries for distillation and chemical synthesis.
- HVAC and refrigeration systems for efficient heating and cooling.
- Renewable energy systems, including solar water heaters and geothermal heat exchange.
- Food and beverage processing for pasteurization, sterilization, cooking, and cooling.
5. What future trends are expected in the field of helical coil heat exchangers?
Future trends in helical coil heat exchangers include:
- Increased use of computational fluid dynamics (CFD) for optimized designs.
- Integration of additive manufacturing for customized coil geometries.
- Incorporation of smart technologies for real-time monitoring and optimization.
- Advances in heat transfer fluids and materials for improved efficiency.
- Further exploration of innovative applications and industries for helical coil heat exchangers.
Recommended courses (Published on EPCLand)
- Basics of Piping Engineering
- Piping Layout Engineering
- Piping Material Engineering
- Piping Stress Analysis
- Complete Course on Piping Engineering
- Material Requisitions
- Piping Material Specifications
- Valve Material Specifications
Don’t miss the published articles on following:
Related Video
Attempt Quiz
Question 1:
What is a Helical Coil Heat Exchanger?
Explanation: A Helical Coil Heat Exchanger is a type of heat exchanger that uses a coiled tube configuration to transfer heat between two fluids. The coiled design allows for efficient heat transfer and compact size.
Question 2:
What is the advantage of using a helical coil design in heat exchangers?
Explanation: One advantage of using a helical coil design in heat exchangers is reduced fouling and scaling. The curved geometry of the coils helps prevent the accumulation of deposits on the heat transfer surface.
Question 3:
Which industries commonly use Helical Coil Heat Exchangers?
Explanation: Helical Coil Heat Exchangers are commonly used in industries such as petrochemical and chemical processing, where efficient heat transfer between fluids is required for various processes.
Question 4:
What is the primary function of a Helical Coil Heat Exchanger?
Explanation: The primary function of a Helical Coil Heat Exchanger is to transfer heat between two fluids. The coiled tube configuration enhances heat transfer efficiency and allows for temperature exchange between the fluids.
Question 5:
What is a potential drawback of using a Helical Coil Heat Exchanger?
Explanation: A potential drawback of using a Helical Coil Heat Exchanger is limited fluid compatibility. The choice of materials and design should consider the nature of the fluids being processed to avoid corrosion or other compatibility issues.