Introduction to Spiral Heat Exchangers
Heat exchangers play a pivotal role in various industries by enabling efficient heat transfer between two fluids without direct contact. One innovative type of heat exchanger is the spiral heat exchanger, which offers several advantages over traditional designs. In this article, we will explore the design, operation, applications, and advancements of spiral heat exchangers, shedding light on their significance in modern industrial processes.
Table of Contents
Similar Articles on other Exchangers
Heat Exchanger Type | Check Article Link |
---|---|
Helical Coil Heat Exchanger | Link |
Tube-in-Tube Heat Exchanger | Link |
Spiral Heat Exchanger | Link |
U-Tube Heat Exchanger | Link |
Shell and Tube Heat Exchanger | Link |
Plate Heat Exchanger | Link |
Double Pipe Heat Exchanger | Link |
Finned Tube Heat Exchanger | Link |
Don’t miss the Detailed course on Drums/Exchanger Piping Layout & Stress Analysis
Enrollment Link
Advantages and Applications
Spiral heat exchangers are designed to maximize heat transfer efficiency while minimizing space requirements. Their compact, coiled configuration allows for a larger heat transfer surface area within a smaller footprint. This feature makes them ideal for applications where space is limited, such as in chemical processing plants, HVAC systems, and power generation facilities.
Moreover, spiral heat exchangers excel in handling fluids with high fouling tendencies. The spiral channels create turbulent flow patterns, reducing the likelihood of fouling on the heat transfer surfaces. This makes them well-suited for processes involving viscous fluids, slurries, and fluids with particulate matter.
Importance of Studying Spiral Heat Exchangers
Studying spiral heat exchangers is essential for optimizing heat transfer processes and energy efficiency. As industries continue to seek ways to reduce energy consumption and operational costs, understanding the mechanics and benefits of spiral heat exchangers can lead to innovative solutions. This knowledge can drive advancements in various sectors, including chemical engineering, power generation, and sustainable technologies.
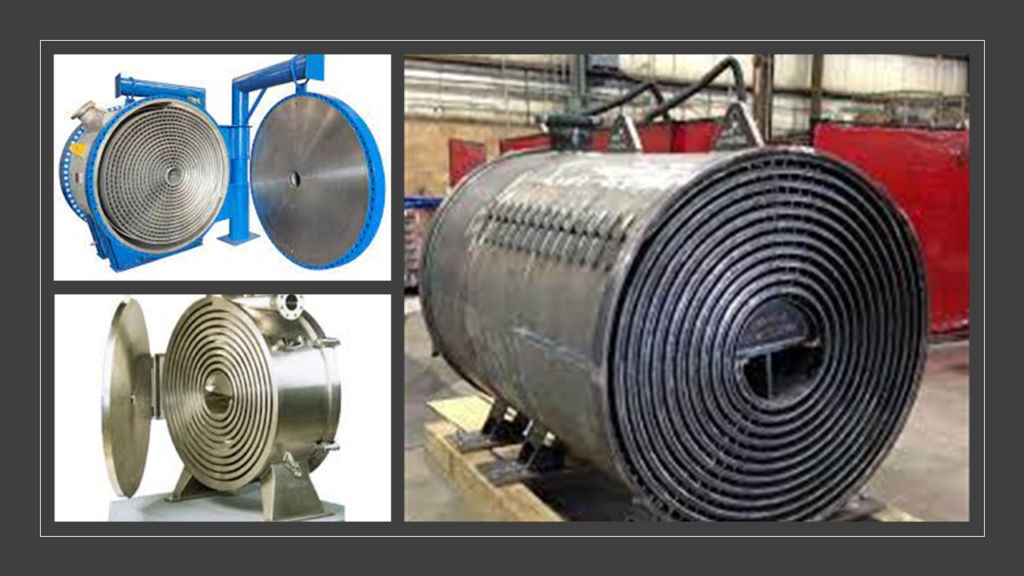
Design and Construction of Spiral Heat Exchangers
Basic Components and Structure
Spiral heat exchangers consist of three primary components: spiral coils, channels, and housing. The spiral coils, often made of stainless steel due to its corrosion resistance, are responsible for guiding the fluids through the heat exchanger. These coils are designed to create a continuous flow path, ensuring effective heat exchange.
The channels, which alternate between hot and cold fluid paths, are formed by the spacing between adjacent coils. This arrangement promotes counterflow or parallel flow depending on the design, enhancing the heat transfer efficiency. The housing or casing encloses the spiral coils and channels, maintaining the structural integrity of the heat exchanger.
Geometry Variations and Effects
Spiral heat exchangers come in various geometries to suit specific applications. Single-channel configurations are common when handling two clean fluids with minimal fouling potential. On the other hand, multi-channel designs allow for efficient heat exchange between fluids with differing fouling tendencies or varying flow rates.
The direction of flow, whether axial or radial, also impacts performance. Axial flow designs are preferred for low-viscosity fluids with moderate heat transfer requirements, while radial flow configurations are effective when dealing with highly viscous fluids or when compactness is essential.
Manufacturing Processes
The manufacturing of spiral heat exchangers involves several key processes to ensure quality and performance. Stamping and forming techniques are used to shape the coils accurately and consistently. Welding plays a crucial role in assembling the coils and creating a robust structure. Techniques like laser welding and orbital welding ensure the integrity of the joints, preventing leaks and ensuring long-term reliability.
Quality control measures, including non-destructive testing, pressure testing, and dimensional checks, are performed to verify the heat exchanger’s integrity before it enters service.
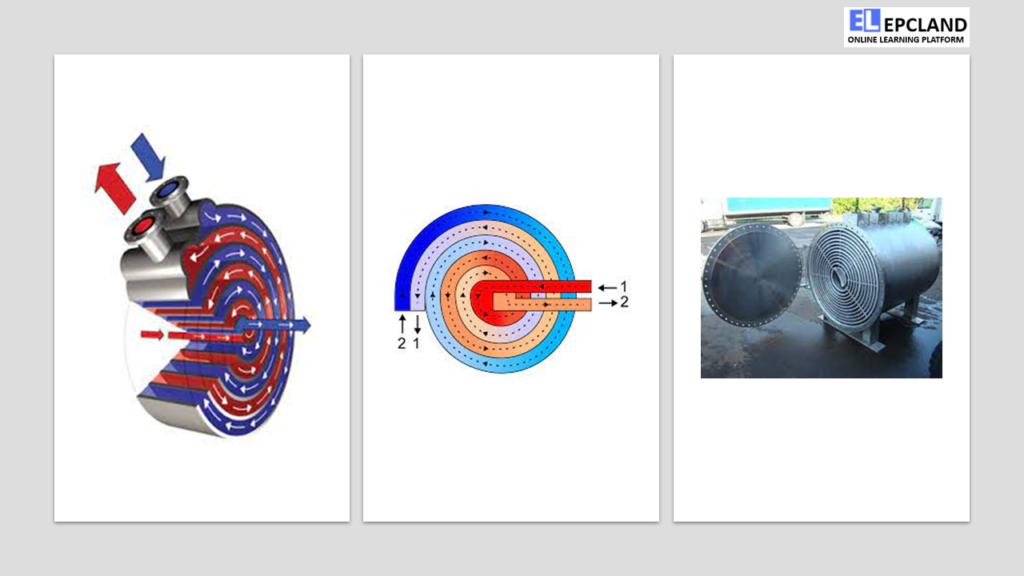
Don’t miss the Detailed course on Drums/Exchanger Piping Layout & Stress Analysis
Enrollment Link
Operating Principles of Spiral Heat Exchangers
Counterflow and Parallel Flow Mechanisms
Spiral heat exchangers operate on the principles of counterflow and parallel flow. In counterflow, the hot and cold fluids flow in opposite directions, maximizing the temperature difference across the heat exchanger. This results in efficient heat transfer and a high degree of temperature uniformity within the fluids.
Parallel flow, on the other hand, involves both fluids moving in the same direction. While this may result in a lower temperature difference, it is useful in cases where precise temperature control is required.
Heat Transfer Mechanisms
Heat transfer within spiral heat exchangers occurs through conduction and convection. Conduction involves the transfer of heat through direct contact between adjacent layers of the spiral coils. Convection, in contrast, relies on the fluid’s movement to carry heat from one point to another. The turbulent flow patterns created by the spiral channels enhance convection, further improving heat transfer efficiency.
Fluid Dynamics and Pressure Drop
The design of spiral heat exchangers promotes turbulent flow, which enhances heat transfer but also leads to increased pressure drop. The pressure drop across the heat exchanger depends on factors such as fluid viscosity, flow rates, and the geometry of the channels. Engineers must carefully consider these factors during the design phase to ensure optimal performance and efficient energy usage.
Fouling and Maintenance Considerations
Fouling, the accumulation of deposits on heat transfer surfaces, can significantly degrade the performance of heat exchangers. However, spiral heat exchangers’ turbulent flow patterns help mitigate fouling by preventing the buildup of deposits. This unique feature reduces maintenance requirements and enhances the heat exchanger’s operational lifespan.
Nevertheless, regular inspections and maintenance are still essential to prevent unexpected issues. Cleaning strategies, including mechanical cleaning and chemical cleaning, can be employed to maintain the heat exchanger’s efficiency over time.
Codes & Standards for Spiral Heat Exchangers
Code/Standard | Description | Applicability |
---|---|---|
ASME Boiler and Pressure Vessel Code | Provides guidelines for pressure vessels and heat exchangers. | Applicable sections: VIII, Division 1 or Division 2, based on design and conditions. |
TEMA Standards | Guidelines for shell-and-tube heat exchangers. | While not specific to spiral heat exchangers, principles can offer insights. |
API 660 | Design, fabrication, and testing of shell-and-tube heat exchangers in the petrochemical industry. | Relevance to design and certain aspects of spiral heat exchangers. |
ISO 15547 | Covers design and performance of gasketed plate heat exchangers. | Insights into thermal performance and pressure drop considerations. |
EN 13445 | European standard for unfired pressure vessels, including heat exchangers. | Relevant for design, fabrication, and inspection requirements. |
ASTM A249/A249M | Standard for welded austenitic steel tubes for heat exchangers. | Applicable to components of spiral heat exchangers. |
Local Regulations | Depending on region and industry, specific regulations apply. | Could cover safety, environmental considerations, etc. |
Performance Analysis and Efficiency
Heat Transfer Coefficient Determination
The heat transfer coefficient is a crucial parameter that quantifies the rate of heat transfer between the fluids. It is influenced by factors such as fluid properties, flow rates, and channel geometry. Engineers often use empirical correlations and computational fluid dynamics (CFD) simulations to accurately estimate the heat transfer coefficient and optimize the design for maximum efficiency.
Overall Heat Transfer Calculation
The overall heat transfer rate in a spiral heat exchanger is influenced by the temperature difference between the fluids, the heat transfer coefficient, and the heat exchanger’s surface area. By accurately calculating these parameters, engineers can assess the heat exchanger’s performance and make informed decisions about its design and operation.
Effectiveness-NTU Analysis
Effectiveness-Number of Transfer Units (ε-NTU) analysis is a powerful method for evaluating heat exchanger performance. It provides insights into the relationship between heat exchanger effectiveness, the number of transfer units, and the heat capacity rates of the fluids. This analysis aids in comparing different heat exchanger designs and predicting their performance under various operating conditions.
Comparisons with Other Heat Exchanger Types
Spiral heat exchangers offer distinct advantages compared to other heat exchanger types, such as shell-and-tube or plate heat exchangers. The compact design and turbulent flow patterns set them apart, enabling efficient heat transfer even in challenging applications. However, the choice between heat exchanger types depends on factors like fluid properties, fouling tendencies, and space limitations.
Efficiency Factors
Spiral heat exchanger efficiency is influenced by both thermal efficiency and hydraulic efficiency. Thermal efficiency measures the heat transferred divided by the maximum possible heat transfer, considering the temperature difference between the fluids. Hydraulic efficiency, on the other hand, considers the pressure drop and fluid flow characteristics to assess the energy consumed by the pumping process. Balancing these factors ensures optimal overall efficiency.
Don’t miss the Complete Course on Piping Engineering: Check Now
By EPCLand.com
Applications across Industries
Chemical and Petrochemical Industries
In chemical processing, where precise temperature control and efficient heat transfer are crucial, spiral heat exchangers find extensive use. They excel in handling corrosive and fouling-prone fluids, making them suitable for applications involving heat recovery, cooling, and chemical reactions. The compact design of spiral heat exchangers helps optimize space utilization within complex chemical plants.
Power Generation and Waste Heat Recovery
Spiral heat exchangers play a pivotal role in power generation by enhancing energy efficiency through waste heat recovery. They are utilized in various processes, including combined heat and power systems, geothermal power plants, and cogeneration facilities. By efficiently transferring heat from exhaust gases or other sources, spiral heat exchangers contribute to reducing greenhouse gas emissions and improving overall power plant efficiency.
HVAC and Refrigeration Systems
In the realm of HVAC and refrigeration, spiral heat exchangers are employed for both heating and cooling applications. They enable efficient heat exchange in air handling units, chillers, and heat pumps. Their compact design and ability to handle variable flow rates make them suitable for providing comfortable indoor environments while optimizing energy consumption.
Food and Pharmaceutical Processing
Industries like food and pharmaceutical processing require precise temperature control to ensure product quality and safety. Spiral heat exchangers are employed in processes such as pasteurization, sterilization, and heating or cooling of various products. Their ability to handle viscous fluids and particulate matter makes them valuable assets in industries where maintaining hygienic conditions is paramount.
Emerging Applications and Future Trends
Spiral heat exchangers continue to find new applications as technology evolves. Their integration with renewable energy systems, such as solar thermal collectors and waste heat recovery from industrial processes, showcases their adaptability to sustainable practices. Additionally, advancements in materials, surface coatings, and manufacturing techniques contribute to improving efficiency and expanding their potential applications.
Advancements and Innovations
Computational Fluid Dynamics (CFD) Modeling
Computational fluid dynamics (CFD) simulations have revolutionized the design and optimization of spiral heat exchangers. These simulations provide insights into fluid flow patterns, temperature distribution, and heat transfer characteristics. Engineers can use CFD to predict performance under various operating conditions, enabling them to fine-tune designs for maximum efficiency.
Enhanced Surface Coatings
Advancements in surface coatings have a significant impact on heat exchanger performance. Coatings that resist fouling, corrosion, and scaling can extend the heat exchanger’s operational lifespan and reduce maintenance requirements. By selecting appropriate coatings based on the fluids and operating conditions, engineers can enhance the overall efficiency and reliability of spiral heat exchangers.
Compact and Modular Designs
The trend toward compact and modular designs addresses space constraints while maintaining or improving heat transfer efficiency. Modular spiral heat exchangers offer the advantage of scalability—additional modules can be added as needed. This flexibility is particularly beneficial in industries with fluctuating process demands, ensuring efficient heat transfer while adapting to changing requirements.
Integration with Renewable Energy Systems
Spiral heat exchangers can be integrated with renewable energy systems to enhance energy capture and utilization. In solar thermal applications, they transfer heat from solar collectors to storage tanks or other heat sinks. This integration reduces the reliance on traditional energy sources and contributes to a more sustainable energy mix.
Sustainability and Environmental Considerations
As industries focus on sustainability and environmental responsibility, heat exchangers play a crucial role in minimizing energy consumption and emissions. Spiral heat exchangers’ ability to optimize heat transfer efficiency aligns with these goals. The use of eco-friendly materials, efficient manufacturing processes, and the reduction of fouling-related maintenance all contribute to a greener industrial landscape.
Don’t miss the Detailed course on Drums/Exchanger Piping Layout & Stress Analysis
Enrollment Link
Case Studies
Case Study 1: Spiral Heat Exchanger in Chemical Processing
In a chemical processing plant, a spiral heat exchanger is used to recover heat from the effluent gases produced during a chemical reaction. The compact design of the spiral heat exchanger allows for efficient heat transfer, ensuring that valuable energy is not wasted. The turbulent flow patterns in the spiral channels prevent fouling, reducing maintenance downtime. As a result, the chemical plant experiences improved energy efficiency and cost savings.
Case Study 2: Spiral Heat Exchanger in Geothermal Power Generation
In a geothermal power plant, spiral heat exchangers are utilized to extract heat from the geothermal fluid and transfer it to a working fluid that drives a turbine. The spiral design’s efficiency in handling fluids with high fouling tendencies ensures continuous operation with minimal downtime. This application showcases how spiral heat exchangers contribute to sustainable power generation by efficiently utilizing renewable geothermal energy sources.
Case Study 3: Spiral Heat Exchanger in HVAC System Optimization
A commercial building’s HVAC system incorporates spiral heat exchangers to optimize energy usage. By efficiently transferring heat between incoming and outgoing air streams, the building’s indoor climate control is achieved with reduced energy consumption. The compact design of the spiral heat exchangers also allows for space-saving installation, making them an ideal choice for retrofitting existing HVAC systems.
Pros & Cons of Spiral Heat Exchanger
Pros of Spiral Heat Exchangers | Cons of Spiral Heat Exchangers |
---|---|
Compact Design: Efficient use of space due to coiled structure. | High Initial Costs: Specialized design and manufacturing can lead to higher upfront expenses. |
High Heat Transfer Efficiency: Turbulent flow patterns promote effective heat exchange. | Customization Needed: Often require customization to match specific application requirements. |
Fouling Resistance: Turbulent flow reduces fouling, leading to lower maintenance. | Complexity of Maintenance: Spiral channels can be challenging to clean and maintain. |
Versatile Applications: Suitable for various industries and fluid properties. | Limited Standardization: Each application requires careful consideration and design. |
Energy Recovery: Effective for waste heat recovery and energy optimization. | Limited for Some Fluids: Not suitable for fluids with extreme pH or aggressive properties. |
Viscous Fluid Handling: Well-suited for handling viscous or particulate-laden fluids. | Potential Pressure Drop: Turbulent flow may result in increased pressure drop. |
Longevity: Reduced fouling leads to extended operational lifespan. | Moderate Complexity: Some designs require axial and radial flow considerations. |
Sustainability: Can integrate with renewable energy systems for eco-friendly solutions. | Limited Codes: Specific codes may not exist; general standards must be applied. |
Challenges and Limitations
High Initial Costs and Customization
Spiral heat exchangers, due to their specialized design and manufacturing processes, may incur higher initial costs compared to more traditional heat exchanger types. Additionally, customization is often required to match the specific requirements of each application. Despite these challenges, the long-term benefits of improved efficiency and reduced maintenance costs can outweigh the initial investment.
Potential for Fouling and Maintenance Complexity
While spiral heat exchangers are designed to mitigate fouling, no heat exchanger is entirely immune. In some cases, fouling may still occur, necessitating cleaning and maintenance. The complexity of the spiral channel geometry can make maintenance more challenging compared to other designs. However, advancements in maintenance techniques, such as robotic cleaning systems, are addressing this limitation.
Limited Standardization
Unlike some traditional heat exchanger types, spiral heat exchangers do not have standardized designs that can be readily applied to various applications. Each installation requires careful consideration of factors like fluid properties, flow rates, and temperature requirements. This lack of standardization can add complexity to the design and selection process.
Fluid Compatibility Issues
Spiral heat exchangers may face challenges when handling fluids with extreme pH levels or aggressive chemical properties. Material selection becomes critical in such cases to ensure the heat exchanger’s longevity and reliability. It’s important to thoroughly assess fluid compatibility and consult with materials experts to select appropriate materials for construction.
Don’t miss the Detailed course on Drums/Exchanger Piping Layout & Stress Analysis
Enrollment Link
Maintenance and Cleaning Strategies
Fouling Mitigation Techniques
To mitigate fouling and maintain optimal performance, various techniques can be employed. Mechanical cleaning involves using brushes or scrapers to physically remove deposits from heat transfer surfaces. Chemical cleaning, on the other hand, utilizes cleaning agents to dissolve or loosen fouling layers. The choice of cleaning method depends on factors such as the nature of fouling and the heat exchanger’s design.
Maintenance Best Practices
Regular inspections are key to identifying potential issues before they impact the heat exchanger’s performance. Monitoring pressure drop, temperature differentials, and fluid flow rates can provide insights into fouling tendencies and any required maintenance. Implementing a proactive maintenance schedule ensures that the heat exchanger operates at peak efficiency and reduces the risk of unexpected downtime.
Comparison of Spiral Heat Exchangers with Other Heat Exchangers
Aspect | Spiral Heat Exchangers | Shell-and-Tube Heat Exchangers | Plate Heat Exchangers |
---|---|---|---|
Design | Coiled spiral channels | Tubes within a cylindrical shell | Stacked metal plates |
Heat Transfer Efficiency | High due to turbulent flow | Moderate | Moderate to high |
Footprint | Compact | Larger | Compact |
Space Utilization | Efficient | Less efficient | Efficient |
Fouling Resistance | High | Moderate | Moderate to high |
Maintenance | Lower due to less fouling | Moderate fouling requires regular cleaning | Moderate to high fouling requires regular cleaning |
Customization | Often required for specific applications | Customizable to some extent | Standard designs |
Fluid Handling | Suitable for viscous or particulate-laden fluids | Flexible | Limited to non-viscous fluids |
Energy Recovery | Effective for waste heat recovery | Commonly used | Effective for waste heat recovery |
Future Outlook and Potential Developments
Growing Adoption Due to Efficiency Improvements
As industries continue to prioritize energy efficiency and sustainability, spiral heat exchangers are likely to see increased adoption. Their ability to enhance heat transfer efficiency while addressing challenges like fouling positions them as valuable tools in optimizing industrial processes.
Integration with Industry 4.0 and IoT
The integration of spiral heat exchangers with Industry 4.0 and the Internet of Things (IoT) holds potential for advanced monitoring and control. Real-time data collection on temperature, pressure, and flow rates can enable predictive maintenance and optimize heat exchanger performance. This data-driven approach enhances operational efficiency and reduces downtime.
Focus on Sustainable Designs and Materials
Environmental considerations will continue to influence heat exchanger design. The development of eco-friendly materials and coatings that resist fouling and corrosion aligns with sustainability goals. Additionally, the design of heat exchangers that can efficiently recover waste heat contributes to reducing carbon footprints across industries.
Advances in Predictive Maintenance Techniques
Advances in technology will likely lead to more sophisticated predictive maintenance techniques for spiral heat exchangers. Machine learning algorithms and AI-powered systems can analyze data patterns to predict when maintenance is needed, optimizing uptime and preventing costly unplanned shutdowns.
Don’t miss the Detailed course on Drums/Exchanger Piping Layout & Stress Analysis
Enrollment Link
Conclusion
Spiral heat exchangers represent a cutting-edge solution to the challenges of efficient heat transfer in various industries. Their compact design, ability to handle fouling-prone fluids, and compatibility with renewable energy systems position them as essential components of modern industrial processes. As technology and research continue to advance, spiral heat exchangers will play an increasingly important role in optimizing energy usage, reducing operational costs, and promoting sustainability across diverse sectors.
FAQs
1. What is a spiral heat exchanger, and how does it work?
A spiral heat exchanger is a type of heat exchanger designed to efficiently transfer heat between two fluids without direct contact. It consists of coiled spiral channels through which the two fluids flow in counterflow or parallel flow patterns. The spiral design promotes turbulent flow, enhancing heat transfer by maintaining a high temperature difference between the fluids. Heat is transferred through conduction and convection between the fluid layers and the coil walls, ensuring efficient energy exchange.
2. What are the advantages of using spiral heat exchangers over traditional designs?
Spiral heat exchangers offer several advantages over traditional designs like shell-and-tube or plate heat exchangers. Their compact coiled structure provides a larger heat transfer surface area within a smaller footprint, making them ideal for space-constrained applications. Additionally, the turbulent flow patterns within the spiral channels reduce the likelihood of fouling, resulting in lower maintenance requirements and longer operational lifespans.
3. In which industries are spiral heat exchangers commonly used?
Spiral heat exchangers find applications across various industries. They are often used in chemical processing for heat recovery, power generation for waste heat utilization, HVAC systems for efficient temperature control, and food and pharmaceutical processing for hygienic heat exchange. Their versatility in handling different fluid properties and fouling tendencies makes them valuable assets in industries where heat transfer efficiency is crucial.
4. What challenges should be considered when using spiral heat exchangers?
While spiral heat exchangers offer many benefits, there are certain challenges to be aware of. Initial costs can be higher due to their specialized design and manufacturing processes. Customization is often required to match specific application requirements, which can add complexity to the design phase. Additionally, while spiral heat exchangers are less prone to fouling, they are not entirely immune, and proper maintenance strategies should be implemented to ensure consistent performance.
5. How are spiral heat exchangers maintained and cleaned?
Maintaining the efficiency of spiral heat exchangers involves proactive strategies. Regular inspections, monitoring pressure drops, and assessing fluid flow rates can provide insights into the heat exchanger’s condition. Fouling mitigation techniques include mechanical cleaning using brushes or scrapers to physically remove deposits and chemical cleaning using cleaning agents to dissolve fouling layers. Selecting the appropriate cleaning method depends on the type of fouling and the heat exchanger’s design.
Recommended courses (Published on EPCLand)
- Basics of Piping Engineering
- Piping Layout Engineering
- Piping Material Engineering
- Piping Stress Analysis
- Complete Course on Piping Engineering
- Material Requisitions
- Piping Material Specifications
- Valve Material Specifications
Don’t miss the published articles on following:
Recommended Video
Attempt Quiz
Question 1:
What is a spiral heat exchanger primarily used for?
Explanation: A spiral heat exchanger is primarily used for heat recovery applications, where it efficiently transfers heat between two fluid streams, often at different temperatures.
Question 2:
How does a spiral heat exchanger achieve high heat transfer efficiency?
Explanation: A spiral heat exchanger achieves high heat transfer efficiency by utilizing a compact design with a long flow path, which allows for effective heat exchange between the fluid streams.
Question 3:
Which fluid flow configuration is typically used in a spiral heat exchanger?
Explanation: A counterflow configuration is typically used in a spiral heat exchanger. In counterflow, the hot and cold fluid streams flow in opposite directions, maximizing the temperature difference and enhancing heat transfer efficiency.
Question 4:
What is the geometry of a spiral heat exchanger?
Explanation: The geometry of a spiral heat exchanger is helical, with two fluid channels coiled around a central core. This design maximizes the surface area available for heat exchange.
Question 5:
Which industries commonly use spiral heat exchangers?
Explanation: Spiral heat exchangers are commonly used in industries such as chemical and petrochemical, as well as in power generation, HVAC systems, waste heat recovery, and various processes that involve heat transfer.