Abstract
Floating roof tanks are an integral part of industrial storage, offering efficient solutions for liquid commodities. This article comprehensively explores the design, applications, and safety considerations associated with floating roof tanks. The discussion covers tank components, their advantages and disadvantages, relevant industry codes and standards, historical accidents, and a detailed comparison with other types of storage tanks.
1. Introduction
Floating roof tanks, a key feature in storage industries, serve as versatile solutions for the containment of liquids. These tanks are designed to minimize vapor emissions and evaporation, enhancing safety and operational efficiency. This article delves into the various aspects of floating roof tanks, shedding light on their components, benefits, challenges, industry regulations, historical incidents, and comparative advantages.
Table of Contents
Do not miss the detailed course on Tank Farm Layout & Stress Analysis
Enrollment link
Check out Similar Articles on other Storage Tanks
2. Floating Roof Tank Components
Primary Types of Floating Roofs: External and Internal
Floating roofs can be broadly classified into two primary types: external and internal. Each type has distinct advantages and applications.
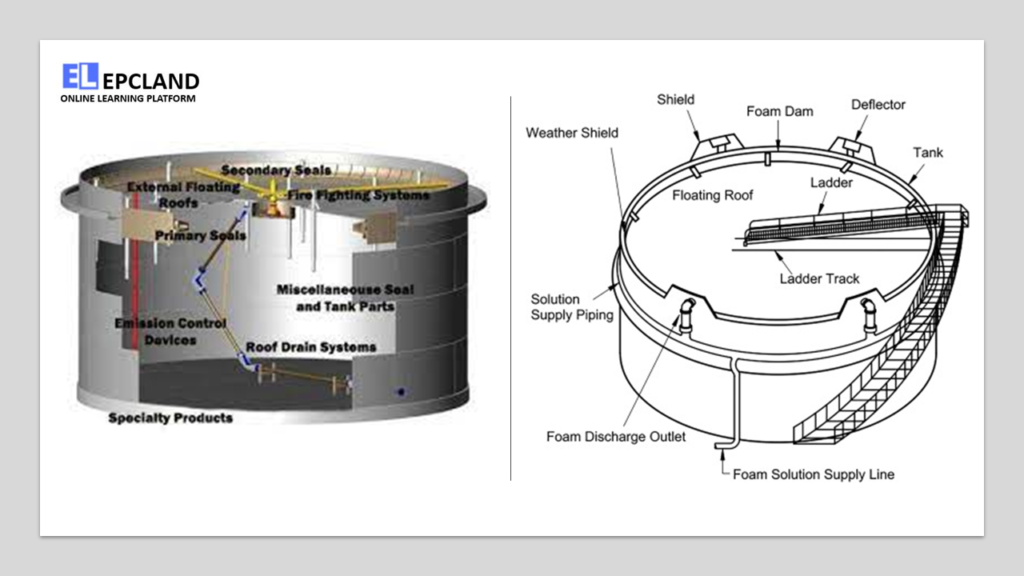
Components of External Floating Roofs
Pontoon
The pontoon, an essential component of an external floating roof, provides buoyancy and stability to the roof structure. It can be single-deck or double-deck, each having specific applications based on tank requirements.
Rim Seal
The rim seal plays a critical role in preventing vapor emissions and environmental contamination. Proper rim seal design and maintenance are crucial for the effective functioning of a floating roof tank.
Deck Fittings
Deck fittings facilitate the efficient operation of the tank. These include roof drains, manholes, roof legs, and roof supports, which contribute to the structural integrity and maintenance of the tank.
Do not miss the detailed course on Tank Farm Layout & Stress Analysis
Enrollment link
Components of Internal Floating Roofs
Buoyancy
Internal floating roofs utilize the buoyancy of the stored liquid to float on the liquid surface. This design minimizes vapor space and reduces vapor emissions, making them suitable for volatile liquids.
Deck and Accessories
The internal floating roof deck is supported by pontoons or other buoyant structures. Accessories such as rolling ladder systems, foam dams, and gauge pole wells enhance the roof’s functionality and safety.
Table: Comparison of Components in External and Internal Floating Roofs
Component | External Floating Roof | Internal Floating Roof |
---|---|---|
Pontoon | ✓ | ✓ |
Rim Seal | ✓ | – |
Deck Fittings | ✓ | – |
Buoyancy | – | ✓ |
Deck Accessories | – | ✓ |
3. Advantages and Disadvantages
Advantages of Floating Roof Tanks
Floating roof tanks offer several advantages that make them preferable in various industries:
Vapor Emission Control
One of the primary benefits is their effective control of vapor emissions, reducing the environmental impact and ensuring regulatory compliance.
Evaporation Minimization
Floating roofs significantly reduce evaporation losses, making them ideal for storing volatile and valuable liquids.
Reduced Fire Hazard
By eliminating the headspace that can contain flammable vapors, floating roofs reduce the risk of ignition sources reaching the vapor space.
Suitable for Various Liquids
Floating roof tanks can accommodate a wide range of liquids, from crude oil to chemicals, making them versatile solutions for different industries.
Disadvantages of Floating Roof Tanks
Despite their advantages, floating roof tanks also come with certain limitations:
Maintenance Complexities
Maintenance of floating roofs can be complex due to the moving components, requiring specialized procedures and skilled personnel.
Higher Initial Costs
The installation and construction of floating roof tanks can be costlier compared to other tank types, mainly due to their intricate design.
Weather Sensitivity
External floating roofs are susceptible to weather conditions, which can affect their performance and require additional safety measures.
Table: Pros and Cons of Floating Roof Tanks
Advantages/Disadvantages | Floating Roof Tanks |
---|---|
Advantages | |
Vapor Emission Control | ✓ |
Evaporation Minimization | ✓ |
Reduced Fire Hazard | ✓ |
Suitable for Various Liquids | ✓ |
Disadvantages | |
Maintenance Complexities | ✓ |
Higher Initial Costs | ✓ |
Weather Sensitivity | ✓ |
Do not miss the detailed course on Tank Farm Layout & Stress Analysis
Enrollment link
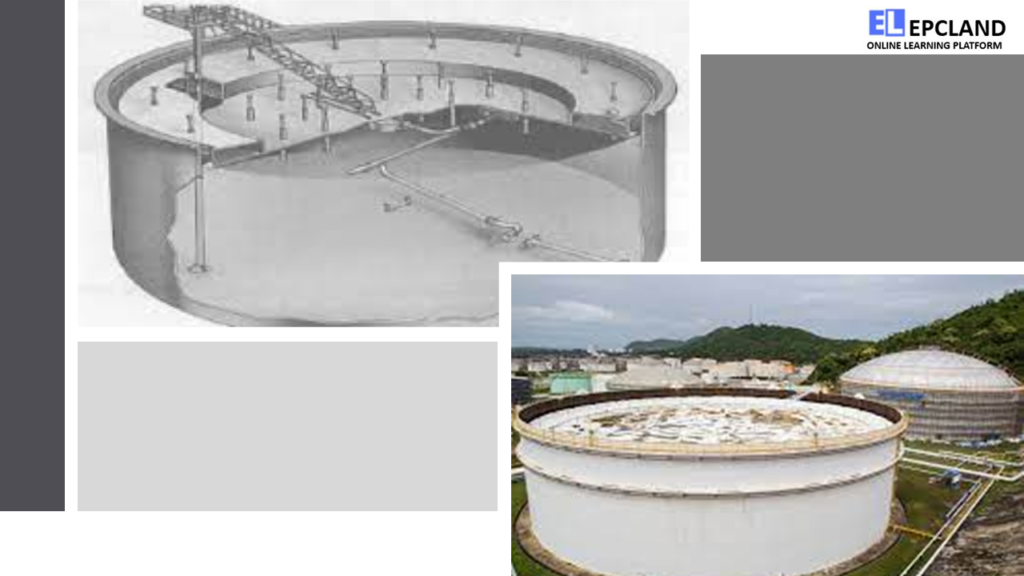
4. Codes and Standards
The design and operation of floating roof tanks are governed by industry standards to ensure safety, environmental protection, and consistent performance.
Overview of Industry Standards for Floating Roof Tanks
API 650: Welded Steel Tanks for Oil Storage – This widely recognized standard outlines the design, fabrication, and erection practices for welded steel tanks, including floating roof tanks.
API 620: Design and Construction of Large, Welded, Low-Pressure Storage Tanks – This standard provides guidance for the design and construction of large welded storage tanks with pressures of up to 15 psi.
Specific Regulations for Different Stored Products
API 653: Tank Inspection, Repair, Alteration, and Reconstruction – This standard focuses on the inspection, repair, alteration, and reconstruction of existing tanks, including floating roof tanks.
Comparison of International Standards
EN 14015: Specification for the design and manufacture of site-built, vertical, cylindrical, flat-bottomed, above-ground, welded, steel tanks for the storage of liquids at ambient temperature and above – This European standard provides guidelines for the design and construction of above-ground storage tanks, including floating roof tanks.
Table: Summary of Key Codes and Standards for Floating Roof Tanks
Standard | Description |
---|---|
API 650 | Welded Steel Tanks for Oil Storage |
API 620 | Design and Construction of Large, Welded, Low-Pressure Storage Tanks |
API 653 | Tank Inspection, Repair, Alteration, and Reconstruction |
EN 14015 | Specification for the design and manufacture of site-built, vertical, cylindrical, flat-bottomed, above-ground, welded, steel tanks for the storage of liquids at ambient temperature and above |
Do not miss the detailed course on Tank Farm Layout & Stress Analysis
Enrollment link
5. Historical Accidents and Lessons Learned
Several historical incidents involving floating roof tanks have highlighted the importance of design, maintenance, and operational practices.
Buncefield Oil Depot, UK (2005)
The Buncefield incident, one of the most severe industrial accidents in the UK, involved the failure of a storage tank’s floating roof due to overfilling.
Jaipur Oil Depot, India (2009)
The Jaipur incident highlighted the catastrophic consequences of rim seal fires in floating roof tanks, leading to a large-scale fire and environmental pollution.
These accidents underscore the critical need for strict adherence to safety protocols, maintenance practices, and operational vigilance to prevent similar incidents.
6. Comparison with Other Types of Storage Tanks
Comparison with Fixed Roof Tanks
Vapor Control: Floating roof tanks excel in vapor control due to their ability to eliminate the vapor space, which fixed roof tanks cannot achieve.
Construction Complexity: While fixed roof tanks are simpler in design, floating roof tanks have more complex components, leading to higher construction complexities.
Maintenance Requirements: Fixed roof tanks generally have lower maintenance requirements compared to floating roof tanks due to their static nature.
Comparison with Spherical Tanks
Structural Integrity: Spherical tanks are known for their high structural integrity, but they are more challenging to fabricate and transport compared to floating roof tanks.
Space Efficiency: Spherical tanks offer efficient space utilization due to their rounded design, whereas floating roof tanks are suitable for larger capacities on limited land.
Material Usage: Spherical tanks often require more material due to their unique shape, whereas floating roof tanks are more material-efficient.
Comparison with Bullet Tanks
Footprint and Space Utilization: Bullet tanks have a small footprint and are space-efficient, making them suitable for limited space installations. Floating roof tanks require more land area.
Installation Flexibility: Bullet tanks are more versatile in installation locations, while floating roof tanks are often chosen for larger storage capacities.
Maintenance Challenges: Bullet tanks can have maintenance challenges due to their compact design, whereas floating roof tanks’ maintenance complexities are associated with their moving components.
Table: Comparative Analysis of Floating Roof Tanks with Other Tank Types
Comparison Factors | Fixed Roof Tanks | Spherical Tanks | Bullet Tanks |
---|---|---|---|
Vapor Control | – | – | – |
Construction Complexity | Simple | Complex | Moderate |
Maintenance Requirements | Low | Moderate | High |
Structural Integrity | Lower | High | Moderate |
Space Efficiency | Moderate | High | Moderate |
Material Usage | Less | More | Moderate |
Footprint & Space Utilization | Larger | Moderate | Small |
Installation Flexibility | Limited | High | High |
Maintenance Challenges | – | – | High |
Do not miss the detailed course on Tank Farm Layout & Stress Analysis
Enrollment link
7. Design Considerations for Safety
To ensure the safety of floating roof tanks, specific design considerations are paramount.
Fire Protection Measures
Rim Seal Fire Protection: Proper design and maintenance of rim seals, along with automatic foam suppression systems, help prevent and mitigate rim seal fires.
Foam Systems: Foam systems are crucial for fire suppression in floating roof tanks, effectively controlling and extinguishing fires that may occur.
Vapor Control and Emission Reduction
Controlled Atmosphere Design: Implementing controlled atmosphere designs, including inert gas blanketing, minimizes vapor emissions and reduces the risk of flammable atmospheres.
Nitrogen Blanketing: The use of nitrogen blanketing helps maintain a non-reactive environment within the tank, preventing oxidation and reducing vapor emissions.
Wind and Weather Considerations
Wind Girders: Wind girders provide structural stability to the floating roof, preventing damage during high winds and adverse weather conditions.
Emergency Drains: Properly designed emergency drainage systems prevent rainwater accumulation on the floating roof, reducing the risk of roof overload and instability.
Table: Safety Features in Floating Roof Tank Design
Safety Measures | Description |
---|---|
Fire Protection Measures | |
Rim Seal Fire Protection | Design and maintenance of rim seals, foam systems |
Vapor Control and Emission Reduction | |
Controlled Atmosphere Design | Inert gas blanketing |
Nitrogen Blanketing | Prevents oxidation and reduces vapor emissions |
Wind and Weather Considerations | |
Wind Girders | Structural stability during adverse weather |
Emergency Drains | Prevents rainwater accumulation and roof overload |
8. Future Trends and Innovations
As technology advances, several trends and innovations are shaping the future of floating roof tanks:
Enhanced Rim Seal Technology
Advancements in rim seal materials and designs contribute to more effective vapor emission control and fire prevention.
Integration of Digital Monitoring and IoT
IoT-based monitoring systems enable real-time tracking of tank conditions, facilitating proactive maintenance and safety management.
Sustainable Materials and Designs
Incorporating sustainable materials and designs reduces environmental impact and enhances the longevity of floating roof tanks.
Improved Flexibility in Roof Movements
Innovations in roof design allow for controlled movements in response to varying liquid levels, optimizing vapor space management.
Do not miss the detailed course on Tank Farm Layout & Stress Analysis
Enrollment link
9. Conclusion
Floating roof tanks continue to be indispensable components in industries requiring efficient liquid storage. Their ability to minimize vapor emissions, control evaporation, and enhance safety makes them an essential choice for a range of liquids. By understanding the components, advantages, challenges, and safety considerations associated with floating roof tanks, industries can make informed decisions to ensure effective storage solutions and contribute to safer operations.
References
Tables
- Table: Comparison of Components in External and Internal Floating Roofs
- Table: Pros and Cons of Floating Roof Tanks
- Table: Summary of Key Codes and Standards for Floating Roof Tanks
- Table: Comparative Analysis of Floating Roof Tanks with Other Tank Types
- Table: Safety Features in Floating Roof Tank Design
FAQs
1. What are floating roof tanks? Floating roof tanks are specialized storage tanks used in various industries to store liquids, such as crude oil, chemicals, and petrochemical products. These tanks feature a floating roof that rests on the liquid’s surface, minimizing the vapor space above the stored liquid. This design reduces vapor emissions, evaporation losses, and fire hazards associated with volatile liquids.
2. What are the primary components of floating roof tanks? Floating roof tanks consist of several key components:
- Pontoon: Provides buoyancy to the roof structure, maintaining its position on the liquid surface.
- Rim Seal: Prevents vapor emissions and environmental contamination by sealing the gap between the tank wall and the floating roof.
- Deck Fittings: These include roof drains, manholes, and roof legs, contributing to the tank’s functionality and maintenance.
- Buoyant Deck: Internal floating roofs utilize buoyancy from the stored liquid, while external floating roofs use pontoons for buoyancy.
3. What are the advantages and disadvantages of using floating roof tanks? Advantages:
- Vapor Emission Control: Floating roof tanks effectively control vapor emissions, reducing environmental impact.
- Evaporation Minimization: They minimize evaporation losses, making them ideal for storing volatile liquids.
- Reduced Fire Hazard: By eliminating vapor space, they reduce the risk of igniting flammable vapors.
- Suitable for Various Liquids: Floating roof tanks can accommodate a wide range of liquids. Disadvantages:
- Maintenance Complexities: Moving components can make maintenance more intricate.
- Higher Initial Costs: Their complex design can lead to higher installation costs.
- Weather Sensitivity: External floating roofs can be affected by weather conditions.
4. Which industry standards govern floating roof tank design? Several industry standards are relevant to floating roof tanks:
- API 650: Provides guidelines for the design and construction of welded steel tanks for oil storage.
- API 620: Offers guidance for large, low-pressure storage tanks’ design and construction.
- API 653: Focuses on inspection, repair, alteration, and reconstruction of existing tanks.
- EN 14015: European standard for the design and manufacture of cylindrical, flat-bottomed, above-ground, welded steel tanks.
5. What safety features are integrated into floating roof tank designs? Floating roof tanks incorporate various safety measures:
- Rim Seal Fire Protection: Properly designed rim seals and foam systems prevent and mitigate rim seal fires.
- Controlled Atmosphere Design: Inert gas blanketing reduces vapor emissions and prevents flammable atmospheres.
- Nitrogen Blanketing: Maintains a non-reactive environment within the tank, minimizing oxidation and vapor emissions.
- Wind Girders: Structural stability during adverse weather conditions prevents roof damage.
- Emergency Drains: Prevent accumulation of rainwater on the floating roof, reducing the risk of roof overload.
Recommended courses (Published on EPCLand)
- Basics of Piping Engineering
- Piping Layout Engineering
- Piping Material Engineering
- Piping Stress Analysis
- Complete Course on Piping Engineering
- Material Requisitions
- Piping Material Specifications
- Valve Material Specifications
Don’t miss the published articles on following:
Related Video
Attempt Quiz
Question 1:
What is a floating roof tank?
Explanation: A floating roof tank is a type of storage tank with a roof that floats on the surface of the stored liquid. The roof moves vertically based on the liquid level, reducing vapor space and emissions.
Question 2:
What is the primary purpose of a floating roof in storage tanks?
Explanation: The primary purpose of a floating roof in storage tanks is to minimize vapor space and emissions. The roof’s movement with the liquid level reduces the volume of vapor that can escape to the atmosphere.
Question 3:
Which of the following types of floating roofs is commonly used for volatile liquids?
Explanation: The External Floating Roof is commonly used for volatile liquids because it provides better protection against evaporation and emissions due to its ability to completely seal the tank’s vapor space.
Question 4:
What is the purpose of the rim seal in an external floating roof tank?
Explanation: The rim seal in an external floating roof tank is designed to prevent vapors from escaping the tank. It provides a barrier against vapor emissions, enhancing the overall environmental performance of the storage system.
Question 5:
What are some advantages of using floating roof tanks?
Explanation: Floating roof tanks offer advantages such as reduced emissions and product loss, as well as enhanced environmental performance. They help minimize vapor emissions and can reduce the risk of fire due to lower vapor space.