Introduction
In the realm of industrial processes, the significance of high-temperature pipes cannot be overstated. These specialized pipelines play a pivotal role in various sectors, where extreme temperatures are not just a challenge but a critical factor that defines the operational landscape. From power generation and petrochemicals to aerospace and metallurgy, high-temperature pipes form the backbone of processes that demand the conveyance of materials under intense heat conditions.
Table of Contents
Do Not miss the detailed course on Pipe Materials i.e. 7 Modules of Pipe Materials
Enrollment Link
Importance of High-Temperature Pipes
In applications such as power plants, where steam at elevated temperatures drives turbines to generate electricity, or in the petrochemical industry, where fluid transport involves materials at high-temperature states, the integrity of pipes becomes paramount. Failure in these scenarios can result in catastrophic consequences, ranging from production downtime to safety hazards and environmental pollution.
Challenges and Considerations
The selection, design, and use of pipes for high-temperature applications are not without their challenges. The extreme heat experienced by these pipes can alter material properties, induce thermal expansion, and contribute to accelerated corrosion rates. Designing pipes that can effectively withstand these conditions demands a thorough understanding of material science, heat transfer, and structural mechanics.
As industries continue to push the boundaries of temperature and performance, it becomes crucial to delve into the nuances of high-temperature pipes. This article aims to provide a comprehensive guide to navigating the intricacies of these pipes, covering aspects from material selection to maintenance strategies. By doing so, it seeks to enhance efficiency, ensure durability, and ultimately contribute to the safe and reliable operation of high-temperature processes.
Similar Articles related to Pipe
Topic | Weblink | Topic | Weblink |
---|---|---|---|
Pipe Insulation Materials | Link | ASME B36.10 | Link |
Piping Codes & Standards | Link | Non-Metallic Pipes | Link |
Pressure-Temperature Ratings | Link | Pipe Standards & Specifications | Link |
Pipes for Different Fluids | Link | Pipe Coatings & Linings | Link |
Pipe Materials Selection Guidelines | Link | Corrosion & Pipe Protection | Link |
High-Temperature Pipes | Link | Pipe Dimensions & Sizes | Link |
Pipe Manufacturing Processes | Link | Types of Pipes in Piping Systems | Link |
Pipe Thickness Calculations | Link | Pipe Inspection & Testing | Link |
I. Understanding High-Temperature Environments
In the realm of industrial processes, the significance of high-temperature pipes cannot be overstated. These specialized pipelines play a pivotal role in various sectors, where extreme temperatures are not just a challenge but a critical factor that defines the operational landscape. From power generation and petrochemicals to aerospace and metallurgy, high-temperature pipes form the backbone of processes that demand the conveyance of materials under intense heat conditions.
Importance of High-Temperature Pipes
In applications such as power plants, where steam at elevated temperatures drives turbines to generate electricity, or in the petrochemical industry, where fluid transport involves materials at high-temperature states, the integrity of pipes becomes paramount. Failure in these scenarios can result in catastrophic consequences, ranging from production downtime to safety hazards and environmental pollution.
Challenges and Considerations
The selection, design, and use of pipes for high-temperature applications are not without their challenges. The extreme heat experienced by these pipes can alter material properties, induce thermal expansion, and contribute to accelerated corrosion rates. Designing pipes that can effectively withstand these conditions demands a thorough understanding of material science, heat transfer, and structural mechanics.
As industries continue to push the boundaries of temperature and performance, it becomes crucial to delve into the nuances of high-temperature pipes. This article aims to provide a comprehensive guide to navigating the intricacies of these pipes, covering aspects from material selection to maintenance strategies. By doing so, it seeks to enhance efficiency, ensure durability, and ultimately contribute to the safe and reliable operation of high-temperature processes.
Do Not miss the detailed course on Pipe Materials i.e. 7 Modules of Pipe Materials
Enrollment Link
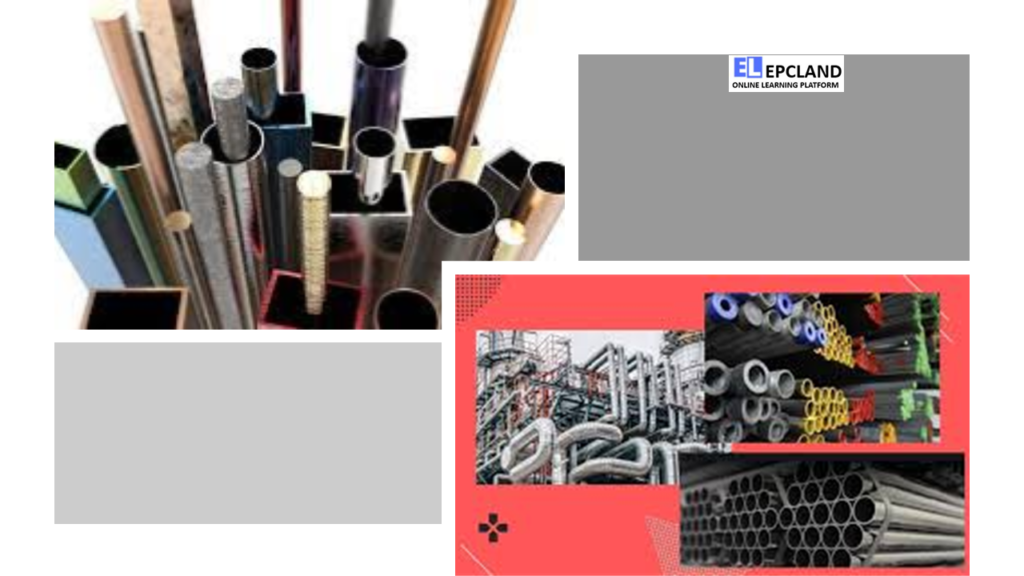
II. Material Selection for High-Temperature Pipes
In the realm of industrial processes, the significance of high-temperature pipes cannot be overstated. These specialized pipelines play a pivotal role in various sectors, where extreme temperatures are not just a challenge but a critical factor that defines the operational landscape. From power generation and petrochemicals to aerospace and metallurgy, high-temperature pipes form the backbone of processes that demand the conveyance of materials under intense heat conditions.
Importance of High-Temperature Pipes
In applications such as power plants, where steam at elevated temperatures drives turbines to generate electricity, or in the petrochemical industry, where fluid transport involves materials at high-temperature states, the integrity of pipes becomes paramount. Failure in these scenarios can result in catastrophic consequences, ranging from production downtime to safety hazards and environmental pollution.
Challenges and Considerations
The selection, design, and use of pipes for high-temperature applications are not without their challenges. The extreme heat experienced by these pipes can alter material properties, induce thermal expansion, and contribute to accelerated corrosion rates. Designing pipes that can effectively withstand these conditions demands a thorough understanding of material science, heat transfer, and structural mechanics.
As industries continue to push the boundaries of temperature and performance, it becomes crucial to delve into the nuances of high-temperature pipes. This article aims to provide a comprehensive guide to navigating the intricacies of these pipes, covering aspects from material selection to maintenance strategies. By doing so, it seeks to enhance efficiency, ensure durability, and ultimately contribute to the safe and reliable operation of high-temperature processes.
III. Design Considerations
In the realm of industrial processes, the significance of high-temperature pipes cannot be overstated. These specialized pipelines play a pivotal role in various sectors, where extreme temperatures are not just a challenge but a critical factor that defines the operational landscape. From power generation and petrochemicals to aerospace and metallurgy, high-temperature pipes form the backbone of processes that demand the conveyance of materials under intense heat conditions.
Importance of High-Temperature Pipes
In applications such as power plants, where steam at elevated temperatures drives turbines to generate electricity, or in the petrochemical industry, where fluid transport involves materials at high-temperature states, the integrity of pipes becomes paramount. Failure in these scenarios can result in catastrophic consequences, ranging from production downtime to safety hazards and environmental pollution.
Challenges and Considerations
The selection, design, and use of pipes for high-temperature applications are not without their challenges. The extreme heat experienced by these pipes can alter material properties, induce thermal expansion, and contribute to accelerated corrosion rates. Designing pipes that can effectively withstand these conditions demands a thorough understanding of material science, heat transfer, and structural mechanics.
As industries continue to push the boundaries of temperature and performance, it becomes crucial to delve into the nuances of high-temperature pipes. This article aims to provide a comprehensive guide to navigating the intricacies of these pipes, covering aspects from material selection to maintenance strategies. By doing so, it seeks to enhance efficiency, ensure durability, and ultimately contribute to the safe and reliable operation of high-temperature processes.
Do Not miss the detailed course on Pipe Materials i.e. 7 Modules of Pipe Materials
Enrollment Link
IV. Manufacturing and Fabrication Techniques
In the realm of industrial processes, the significance of high-temperature pipes cannot be overstated. These specialized pipelines play a pivotal role in various sectors, where extreme temperatures are not just a challenge but a critical factor that defines the operational landscape. From power generation and petrochemicals to aerospace and metallurgy, high-temperature pipes form the backbone of processes that demand the conveyance of materials under intense heat conditions.
Importance of High-Temperature Pipes
In applications such as power plants, where steam at elevated temperatures drives turbines to generate electricity, or in the petrochemical industry, where fluid transport involves materials at high-temperature states, the integrity of pipes becomes paramount. Failure in these scenarios can result in catastrophic consequences, ranging from production downtime to safety hazards and environmental pollution.
Challenges and Considerations
The selection, design, and use of pipes for high-temperature applications are not without their challenges. The extreme heat experienced by these pipes can alter material properties, induce thermal expansion, and contribute to accelerated corrosion rates. Designing pipes that can effectively withstand these conditions demands a thorough understanding of material science, heat transfer, and structural mechanics.
As industries continue to push the boundaries of temperature and performance, it becomes crucial to delve into the nuances of high-temperature pipes. This article aims to provide a comprehensive guide to navigating the intricacies of these pipes, covering aspects from material selection to maintenance strategies. By doing so, it seeks to enhance efficiency, ensure durability, and ultimately contribute to the safe and reliable operation of high-temperature processes.
V. Corrosion and Oxidation Resistance
In the realm of industrial processes, the significance of high-temperature pipes cannot be overstated. These specialized pipelines play a pivotal role in various sectors, where extreme temperatures are not just a challenge but a critical factor that defines the operational landscape. From power generation and petrochemicals to aerospace and metallurgy, high-temperature pipes form the backbone of processes that demand the conveyance of materials under intense heat conditions.
Importance of High-Temperature Pipes
In applications such as power plants, where steam at elevated temperatures drives turbines to generate electricity, or in the petrochemical industry, where fluid transport involves materials at high-temperature states, the integrity of pipes becomes paramount. Failure in these scenarios can result in catastrophic consequences, ranging from production downtime to safety hazards and environmental pollution.
Challenges and Considerations
The selection, design, and use of pipes for high-temperature applications are not without their challenges. The extreme heat experienced by these pipes can alter material properties, induce thermal expansion, and contribute to accelerated corrosion rates. Designing pipes that can effectively withstand these conditions demands a thorough understanding of material science, heat transfer, and structural mechanics.
As industries continue to push the boundaries of temperature and performance, it becomes crucial to delve into the nuances of high-temperature pipes. This article aims to provide a comprehensive guide to navigating the intricacies of these pipes, covering aspects from material selection to maintenance strategies. By doing so, it seeks to enhance efficiency, ensure durability, and ultimately contribute to the safe and reliable operation of high-temperature processes.
Do Not miss the detailed course on Pipe Materials i.e. 7 Modules of Pipe Materials
Enrollment Link
VI. Insulation and Heat Management
In the realm of industrial processes, the significance of high-temperature pipes cannot be overstated. These specialized pipelines play a pivotal role in various sectors, where extreme temperatures are not just a challenge but a critical factor that defines the operational landscape. From power generation and petrochemicals to aerospace and metallurgy, high-temperature pipes form the backbone of processes that demand the conveyance of materials under intense heat conditions.
Importance of High-Temperature Pipes
In applications such as power plants, where steam at elevated temperatures drives turbines to generate electricity, or in the petrochemical industry, where fluid transport involves materials at high-temperature states, the integrity of pipes becomes paramount. Failure in these scenarios can result in catastrophic consequences, ranging from production downtime to safety hazards and environmental pollution.
Challenges and Considerations
The selection, design, and use of pipes for high-temperature applications are not without their challenges. The extreme heat experienced by these pipes can alter material properties, induce thermal expansion, and contribute to accelerated corrosion rates. Designing pipes that can effectively withstand these conditions demands a thorough understanding of material science, heat transfer, and structural mechanics.
As industries continue to push the boundaries of temperature and performance, it becomes crucial to delve into the nuances of high-temperature pipes. This article aims to provide a comprehensive guide to navigating the intricacies of these pipes, covering aspects from material selection to maintenance strategies. By doing so, it seeks to enhance efficiency, ensure durability, and ultimately contribute to the safe and reliable operation of high-temperature processes.
VII. Maintenance and Inspection Strategies
In the realm of industrial processes, the significance of high-temperature pipes cannot be overstated. These specialized pipelines play a pivotal role in various sectors, where extreme temperatures are not just a challenge but a critical factor that defines the operational landscape. From power generation and petrochemicals to aerospace and metallurgy, high-temperature pipes form the backbone of processes that demand the conveyance of materials under intense heat conditions.
Importance of High-Temperature Pipes
In applications such as power plants, where steam at elevated temperatures drives turbines to generate electricity, or in the petrochemical industry, where fluid transport involves materials at high-temperature states, the integrity of pipes becomes paramount. Failure in these scenarios can result in catastrophic consequences, ranging from production downtime to safety hazards and environmental pollution.
Challenges and Considerations
The selection, design, and use of pipes for high-temperature applications are not without their challenges. The extreme heat experienced by these pipes can alter material properties, induce thermal expansion, and contribute to accelerated corrosion rates. Designing pipes that can effectively withstand these conditions demands a thorough understanding of material science, heat transfer, and structural mechanics.
As industries continue to push the boundaries of temperature and performance, it becomes crucial to delve into the nuances of high-temperature pipes. This article aims to provide a comprehensive guide to navigating the intricacies of these pipes, covering aspects from material selection to maintenance strategies. By doing so, it seeks to enhance efficiency, ensure durability, and ultimately contribute to the safe and reliable operation of high-temperature processes.
Do Not miss the detailed course on Pipe Materials i.e. 7 Modules of Pipe Materials
Enrollment Link
VIII. Future Trends and Innovations
In the realm of industrial processes, the significance of high-temperature pipes cannot be overstated. These specialized pipelines play a pivotal role in various sectors, where extreme temperatures are not just a challenge but a critical factor that defines the operational landscape. From power generation and petrochemicals to aerospace and metallurgy, high-temperature pipes form the backbone of processes that demand the conveyance of materials under intense heat conditions.
Importance of High-Temperature Pipes
In applications such as power plants, where steam at elevated temperatures drives turbines to generate electricity, or in the petrochemical industry, where fluid transport involves materials at high-temperature states, the integrity of pipes becomes paramount. Failure in these scenarios can result in catastrophic consequences, ranging from production downtime to safety hazards and environmental pollution.
Challenges and Considerations
The selection, design, and use of pipes for high-temperature applications are not without their challenges. The extreme heat experienced by these pipes can alter material properties, induce thermal expansion, and contribute to accelerated corrosion rates. Designing pipes that can effectively withstand these conditions demands a thorough understanding of material science, heat transfer, and structural mechanics.
As industries continue to push the boundaries of temperature and performance, it becomes crucial to delve into the nuances of high-temperature pipes. This article aims to provide a comprehensive guide to navigating the intricacies of these pipes, covering aspects from material selection to maintenance strategies. By doing so, it seeks to enhance efficiency, ensure durability, and ultimately contribute to the safe and reliable operation of high-temperature processes.
Conclusion
In the realm of industrial processes, the significance of high-temperature pipes cannot be overstated. These specialized pipelines play a pivotal role in various sectors, where extreme temperatures are not just a challenge but a critical factor that defines the operational landscape. From power generation and petrochemicals to aerospace and metallurgy, high-temperature pipes form the backbone of processes that demand the conveyance of materials under intense heat conditions.
Importance of High-Temperature Pipes
In applications such as power plants, where steam at elevated temperatures drives turbines to generate electricity, or in the petrochemical industry, where fluid transport involves materials at high-temperature states, the integrity of pipes becomes paramount. Failure in these scenarios can result in catastrophic consequences, ranging from production downtime to safety hazards and environmental pollution.
Challenges and Considerations
The selection, design, and use of pipes for high-temperature applications are not without their challenges. The extreme heat experienced by these pipes can alter material properties, induce thermal expansion, and contribute to accelerated corrosion rates. Designing pipes that can effectively withstand these conditions demands a thorough understanding of material science, heat transfer, and structural mechanics.
As industries continue to push the boundaries of temperature and performance, it becomes crucial to delve into the nuances of high-temperature pipes. This article aims to provide a comprehensive guide to navigating the intricacies of these pipes, covering aspects from material selection to maintenance strategies. By doing so, it seeks to enhance efficiency, ensure durability, and ultimately contribute to the safe and reliable operation of high-temperature processes.
Do Not miss the detailed course on Pipe Materials i.e. 7 Modules of Pipe Materials
Enrollment Link
FAQs about High-Temperature Pipes
1. Why are high-temperature pipes important in industrial processes? High-temperature pipes are essential in industries where materials need to be transported under extreme heat conditions, such as power generation and petrochemicals. They ensure the integrity of fluid conveyance systems, preventing catastrophic failures and maintaining operational efficiency.
2. What challenges are associated with high-temperature pipe applications? High-temperature pipes face challenges like altered material properties, thermal expansion, and increased corrosion rates due to extreme heat. Designing pipes that can withstand these conditions requires expertise in material science, heat transfer, and structural mechanics.
3. How are materials selected for high-temperature pipes? Material selection depends on factors like the temperature range, corrosion resistance, mechanical properties, and cost. Common materials include stainless steel, alloy steel, and nickel alloys, each chosen for their suitability in specific temperature ranges and environments.
4. What role does insulation play in high-temperature pipes? Insulation is crucial for minimizing heat loss and maintaining pipe integrity. Various insulation materials and techniques, including heat shields and refractory linings, help prevent excessive heat transfer to the surroundings, ensuring energy efficiency and worker safety.
5. How can maintenance and inspection ensure the reliability of high-temperature pipes? Regular maintenance and inspection are vital for identifying potential issues and preventing unexpected failures. Advanced techniques like infrared thermography and ultrasonic testing help detect problems early, allowing for timely repairs and replacements, thus extending the pipes’ service life.
Recommended courses (Published on EPCLand)
- Basics of Piping Engineering
- Piping Layout Engineering
- Piping Material Engineering
- Piping Stress Analysis
- Complete Course on Piping Engineering
- Material Requisitions
- Piping Material Specifications
- Valve Material Specifications
Don’t miss the published articles on following:
Related Video
Attempt Quiz
Question 1:
What type of material is commonly used for pipes in high-temperature applications?
Explanation: Carbon steel is commonly used for pipes in high-temperature applications due to its strength and resistance to elevated temperatures.
Question 2:
What is the significance of selecting the appropriate alloy for high-temperature pipes?
Explanation: Selecting the appropriate alloy for high-temperature pipes is significant because it enhances corrosion resistance, ensuring the pipe’s integrity and longevity in high-temperature and corrosive environments.
Question 3:
Which of the following pipe manufacturing methods is suitable for high-temperature applications?
Explanation: Welding is a suitable pipe manufacturing method for high-temperature applications, as it allows for the creation of strong and reliable joints that can withstand elevated temperatures.
Question 4:
What is the significance of thermal expansion in high-temperature pipes?
Explanation: Thermal expansion in high-temperature pipes can lead to stress and deformation, which may impact the integrity of the pipe and its connections over time.
Question 5:
What type of insulation is commonly used for high-temperature pipes to minimize heat loss?
Explanation: Fiberglass insulation is commonly used for high-temperature pipes to minimize heat loss, improve energy efficiency, and protect personnel from contacting hot surfaces.