Introduction
Piping systems play a crucial role in a wide range of industries, serving as the circulatory system that transports fluids and gases essential for various processes. The diversity of fluids, pressures, temperatures, and environmental conditions encountered in different sectors necessitates the use of a variety of pipes. These pipes, carefully selected based on their material properties and design characteristics, facilitate the safe and efficient movement of substances within industrial operations.
Table of Contents
Do not miss the detailed course on What is Pipe II Schedule II Plastic II Jacketed II Tracing
Enrollment Link
Importance of Piping Systems
Piping systems form the backbone of infrastructure for industries such as oil and gas, water supply, chemical processing, and manufacturing. They enable the transfer of liquids, gases, and slurries between different points within a facility or even across vast distances. Whether it’s transporting crude oil from extraction sites to refineries, distributing clean water to urban centers, or facilitating chemical reactions in industrial plants, the functionality of these systems directly impacts the efficiency and productivity of various operations.
Selecting the Right Type of Pipe
Choosing the appropriate type of pipe for a given application is a critical decision. Factors like the nature of the fluid or gas being transported, the temperature and pressure conditions, and the surrounding environment all influence the selection process. For instance, corrosive chemicals may require pipes with high resistance to chemical reactions, while high-pressure systems demand pipes with exceptional strength and durability.
Purpose of the Article
In this comprehensive article, we will delve into the world of piping systems, focusing on the various types of pipes used across industries. We will explore metallic, non-metallic, and composite pipes, each with their unique properties and advantages. By examining the materials, applications, and benefits of these pipes, readers will gain insights into how the right choice of piping can optimize efficiency, ensure safety, and contribute to the success of diverse industrial processes.
Similar Articles related to Pipe
Topic | Weblink | Topic | Weblink |
---|---|---|---|
Pipe Insulation Materials | Link | ASME B36.10 | Link |
Piping Codes & Standards | Link | Non-Metallic Pipes | Link |
Pressure-Temperature Ratings | Link | Pipe Standards & Specifications | Link |
Pipes for Different Fluids | Link | Pipe Coatings & Linings | Link |
Pipe Materials Selection Guidelines | Link | Corrosion & Pipe Protection | Link |
High-Temperature Pipes | Link | Pipe Dimensions & Sizes | Link |
Pipe Manufacturing Processes | Link | Types of Pipes in Piping Systems | Link |
Pipe Thickness Calculations | Link | Pipe Inspection & Testing | Link |
1. Common Types of Pipes
In the realm of piping systems, pipes can be broadly categorized into three main types: metallic pipes, non-metallic pipes, and composite pipes. Each type possesses distinct characteristics that make it suitable for specific applications. The selection of the appropriate pipe type depends on a multitude of factors, including the nature of the substances being transported, the environmental conditions, and the desired performance criteria.
Metallic Pipes
Metallic pipes are widely used due to their inherent strength and durability. They are commonly employed in applications where high pressure, extreme temperatures, and corrosive environments are prevalent. Different types of metals are utilized to suit varying operational requirements.
Steel Pipes
Steel pipes are renowned for their exceptional strength and durability. They are often used in industries such as oil and gas, where they transport crude oil and natural gas over long distances. Additionally, steel pipes find application in construction, infrastructure development, and industrial processes due to their resistance to external stresses and corrosion.
Stainless Steel Pipes
Stainless steel pipes are highly resistant to corrosion and rust, making them ideal for transporting fluids that are prone to oxidation. They are extensively used in the food and beverage industry, pharmaceuticals, and chemical processing, where maintaining the purity of substances being transported is crucial.
Cast Iron Pipes
Cast iron pipes are recognized for their longevity and resistance to external forces. They are commonly utilized in wastewater systems and drainage systems, effectively withstanding the abrasive nature of sewage and graywater.
Copper Pipes
Copper pipes are valued for their excellent heat conductivity and antimicrobial properties. They are frequently employed in plumbing systems, heating, and cooling applications, ensuring efficient transfer of fluids while minimizing the risk of bacterial growth.
Do not miss the detailed course on What is Pipe II Schedule II Plastic II Jacketed II Tracing
Enrollment Link
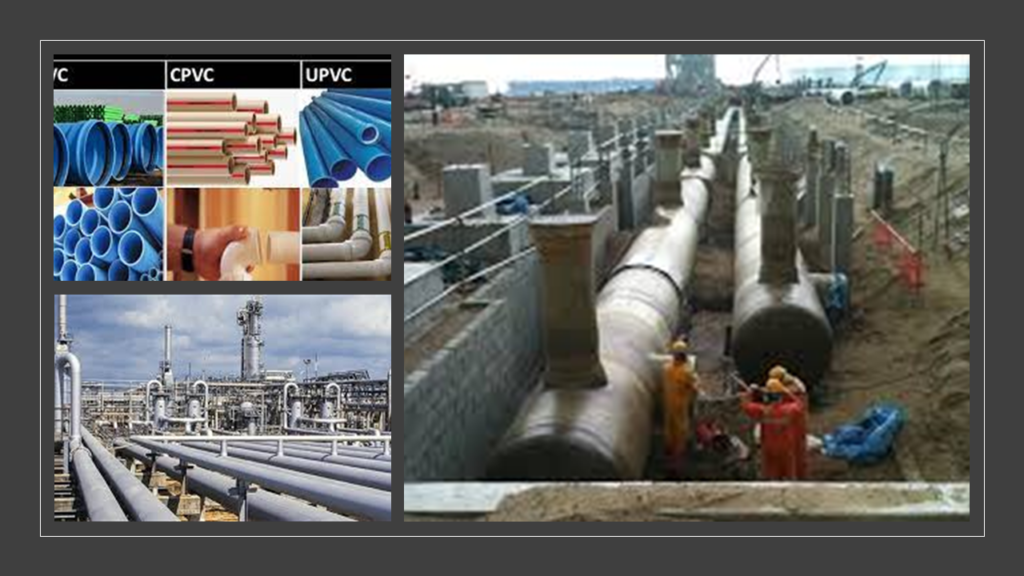
Non-Metallic Pipes
Non-metallic pipes offer advantages such as corrosion resistance, lightweight construction, and ease of installation. They find their niche in applications where avoiding chemical reactions with transported substances is crucial.
PVC (Polyvinyl Chloride) Pipes
PVC pipes are widely used for water supply and drainage systems. Their affordability, chemical resistance, and low maintenance requirements make them a popular choice in residential, commercial, and industrial settings.
HDPE (High-Density Polyethylene) Pipes
HDPE pipes are known for their flexibility, durability, and resistance to chemicals. They are commonly utilized for transporting potable water, wastewater, and even natural gas.
Fiberglass-Reinforced Plastic Pipes
Fiberglass-reinforced plastic (FRP) pipes combine the strength of glass fibers with the corrosion resistance of plastics. These pipes are employed in corrosive environments, such as chemical processing plants, where they ensure the safe transportation of aggressive fluids.
Composite Pipes
Composite pipes integrate the advantages of both metallic and non-metallic materials, making them suitable for applications that demand a balance between strength and corrosion resistance.
Composite pipes are highly adaptable, designed to address specific operational requirements while minimizing drawbacks. They are often used in industries such as offshore oil and gas exploration, where exposure to harsh marine environments necessitates exceptional durability.
By understanding the characteristics and applications of these common pipe types, industries can make informed decisions when selecting the most suitable pipe material for their specific needs. The next sections of this article will delve deeper into the properties, applications, and advantages of each type of pipe, providing a comprehensive guide for professionals across diverse sectors.
Do not miss the detailed course on What is Pipe II Schedule II Plastic II Jacketed II Tracing
Enrollment Link
2. Metallic Pipes
Steel Pipes
Steel pipes are a cornerstone of modern infrastructure, known for their unparalleled strength and versatility. They play a pivotal role in transporting a wide range of fluids and gases across industries, from water and oil to chemicals and gases. The following sections outline the key features, applications, and advantages of steel pipes.
Key Features of Steel Pipes
Steel pipes exhibit exceptional mechanical properties, making them suitable for high-pressure and high-temperature applications. Some key features include:
- Strength: Steel pipes possess high tensile and compressive strength, enabling them to withstand internal and external forces.
- Durability: Steel’s robust nature ensures longevity and resistance to deformation, making it suitable for long-distance pipelines.
- Corrosion Resistance: Many steel pipes are coated or lined to enhance their resistance to corrosion, ensuring the longevity of the pipeline.
Applications of Steel Pipes
Steel pipes find applications in various industries due to their inherent strength and durability:
- Oil and Gas: Steel pipes are extensively used in the oil and gas sector for transporting crude oil, natural gas, and refined products over vast distances.
- Water Distribution: Steel pipes are employed in water supply systems, including municipal water distribution and irrigation networks.
- Industrial Processes: Industries such as manufacturing, chemicals, and power generation utilize steel pipes to transport fluids within their processes.
- Construction: Steel pipes are used in construction projects for structural support, foundation pilings, and underground utilities.
Advantages and Limitations
Advantages
- Strength and Durability: Steel pipes can handle high pressures, heavy loads, and harsh environments.
- Wide Range of Sizes: Steel pipes are available in various sizes, making them adaptable to different applications.
- Longevity: Properly maintained steel pipes can have a long service life, even under demanding conditions.
Limitations
- Corrosion: Uncoated steel pipes can be susceptible to corrosion, especially in aggressive environments.
- Weight: Steel pipes are heavier than some alternative materials, which can impact transportation and installation costs.
- Cost: Depending on the specific alloy and coating, steel pipes can be relatively expensive.
In conclusion, steel pipes are essential components in modern industrial infrastructure. Their remarkable strength, durability, and versatility enable them to fulfill critical roles in transporting fluids and gases across diverse applications. While they have certain limitations, proper selection, maintenance, and corrosion prevention strategies can ensure the longevity and reliability of steel pipe systems. The subsequent sections of this article will explore other types of metallic pipes, non-metallic pipes, and composite pipes, providing a comprehensive understanding of piping systems used in various industries.
Do not miss the detailed course on What is Pipe II Schedule II Plastic II Jacketed II Tracing
Enrollment Link
3. Non-Metallic Pipes
PVC (Polyvinyl Chloride) Pipes
PVC pipes are a prominent choice in a wide array of applications, known for their affordability, versatility, and corrosion resistance. Their unique characteristics make them suitable for various industries, ranging from residential plumbing to agricultural irrigation. Here, we delve into the features, applications, advantages, and limitations of PVC pipes.
Key Features of PVC Pipes
PVC pipes possess several key features that contribute to their popularity:
- Corrosion Resistance: PVC is inherently resistant to corrosion and chemical reactions, ensuring a long service life.
- Lightweight: PVC pipes are considerably lighter than metallic pipes, facilitating easier transportation and installation.
- Smooth Interior: The smooth inner surface of PVC pipes minimizes friction, promoting efficient fluid flow.
Applications of PVC Pipes
PVC pipes find application across multiple sectors due to their versatility and cost-effectiveness:
- Water Supply: PVC pipes are widely used in domestic and commercial water distribution systems.
- Sewage and Drainage: They are employed in sewage and wastewater systems due to their corrosion resistance and smooth flow characteristics.
- Irrigation: PVC pipes are popular in agricultural irrigation systems, delivering water efficiently to crops.
- Conduit Systems: They serve as conduits for electrical wiring and telecommunications cables in construction projects.
Advantages and Limitations
Advantages
- Affordability: PVC pipes are cost-effective compared to many metallic alternatives.
- Corrosion Resistance: PVC pipes are immune to corrosion, ensuring a longer lifespan.
- Easy Installation: Their lightweight nature makes them easy to handle and install, reducing labor costs.
- Low Maintenance: PVC pipes require minimal maintenance due to their resistance to rust and chemical degradation.
Limitations
- Temperature Sensitivity: PVC pipes can deform under high temperatures, limiting their suitability for hot water systems.
- Brittleness: In colder climates, PVC pipes can become brittle and prone to cracking.
- Limited Strength: PVC pipes have lower tensile strength compared to some metallic pipes, making them less suitable for high-pressure applications.
In conclusion, PVC pipes offer a cost-effective and versatile solution for various piping needs. Their corrosion resistance, lightweight nature, and ease of installation make them ideal for applications where high temperatures and pressures are not a concern. While they have certain limitations, proper design and installation practices can maximize the benefits of PVC pipes in diverse industries. The subsequent sections of this article will explore more types of non-metallic pipes, metallic pipes, and composite pipes, providing a comprehensive understanding of the range of options available for piping systems.
Do not miss the detailed course on What is Pipe II Schedule II Plastic II Jacketed II Tracing
Enrollment Link
4. Composite Pipes
Introduction to Composite Pipes
Composite pipes represent an innovative solution that combines the advantages of both metallic and non-metallic materials. These pipes are engineered to address specific challenges in industries where a balance between strength, durability, and corrosion resistance is paramount. In this section, we delve into the construction, applications, advantages, and potential drawbacks of composite pipes.
Construction of Composite Pipes
Composite pipes typically consist of multiple layers of different materials, strategically combined to optimize performance. The layers can include:
- Inner Layer: This layer is in direct contact with the transported fluid or gas and is often made of a non-corrosive material such as HDPE or PVC.
- Middle Layer: The middle layer provides structural integrity and strength, commonly utilizing materials like fiberglass-reinforced plastic (FRP) or carbon fiber.
- Outer Layer: The outer layer acts as a protective shield, guarding the pipe against external forces and environmental factors.
Applications of Composite Pipes
Composite pipes are employed in industries where traditional materials may fall short:
- Oil and Gas Offshore Applications: Composite pipes are used in offshore oil and gas operations due to their resistance to corrosion and lightweight construction, which reduces platform weight.
- Chemical Processing: In corrosive environments, composite pipes ensure the safe transport of aggressive chemicals.
- Marine Industries: Composite pipes find applications in marine environments, offering resistance to saltwater and harsh conditions.
- Highly Specialized Uses: Industries such as aerospace and nuclear power may use composite pipes in highly specialized applications that demand specific material properties.
Advantages and Considerations
Advantages
- Corrosion Resistance: Composite pipes offer excellent resistance to corrosion, extending their service life.
- Strength and Lightweight: They provide high strength-to-weight ratios, making them suitable for demanding applications without the weight concerns of metallic pipes.
- Tailored Properties: Composite pipes can be engineered with specific characteristics to meet the needs of particular industries.
Considerations
- Manufacturing Complexity: The construction of composite pipes can be intricate, requiring specialized manufacturing processes.
- Cost: Composite pipes can be more expensive to produce compared to traditional materials.
- Compatibility: The compatibility of composite materials with certain fluids or gases needs careful consideration.
In conclusion, composite pipes represent a cutting-edge solution that bridges the gap between metallic and non-metallic pipes. Their unique construction allows for tailored properties that cater to specific industry requirements. While they may present challenges in terms of manufacturing complexity and cost, their advantages make them indispensable in industries where durability, corrosion resistance, and strength are vital. The subsequent sections of this article will continue to explore other types of pipes, providing a comprehensive understanding of the diverse options available for piping systems in various applications.
Do not miss the detailed course on What is Pipe II Schedule II Plastic II Jacketed II Tracing
Enrollment Link
5. Specialized Pipes
Introduction to Specialized Pipes
In addition to the common types of pipes discussed earlier, certain industries require specialized pipes to meet unique challenges and specific operational needs. These specialized pipes are designed to withstand extreme conditions, transport aggressive substances, or ensure the integrity of sensitive materials. In this section, we delve into some of these specialized pipe types, their applications, and the benefits they offer.
Lined Pipes
Lined pipes are specifically engineered to handle corrosive fluids and gases. They consist of a metallic outer layer for structural support and an inner lining made of materials such as PTFE (polytetrafluoroethylene) or PFA (perfluoroalkoxy), which are highly resistant to chemical reactions.
Applications
- Chemical Industries: Lined pipes are crucial for transporting aggressive chemicals without corroding the outer metallic layer.
- Pharmaceutical Manufacturing: They ensure the purity of transported substances, preventing contamination.
Insulated Pipes
Insulated pipes are designed to maintain the temperature of the transported fluid, preventing heat loss or gain. They are used to transport substances that are temperature-sensitive, such as hot water, steam, or chilled liquids.
Applications
- District Heating and Cooling: Insulated pipes are used in centralized heating and cooling systems for residential and commercial buildings.
- Industrial Processes: They transport steam or other heated substances within industrial operations while minimizing heat loss.
Jacketed Pipes
Jacketed pipes consist of an outer pipe (jacket) surrounding an inner core pipe. The annular space between the two pipes is used to circulate a temperature-controlling medium, such as hot water or steam.
Applications
- Viscous Fluids: Jacketed pipes are used to transport substances with high viscosity that require temperature control to maintain flow.
- Food Processing: They are employed in industries where maintaining consistent temperatures is crucial for processing.
Advantages and Considerations
Advantages
- Corrosion and Temperature Resistance: Specialized pipes are designed to withstand extreme conditions, ensuring the integrity of transported materials.
- Process Efficiency: These pipes optimize the transport of specific substances, contributing to process efficiency and product quality.
Considerations
- Complexity: Specialized pipes may have intricate designs, increasing manufacturing complexity and potentially affecting maintenance.
- Cost: The added features and materials in specialized pipes can result in higher production costs.
In conclusion, specialized pipes cater to industries with unique requirements, providing solutions for transporting corrosive materials, maintaining temperature integrity, and addressing other specific challenges. While they may come with added complexity and costs, their benefits are essential in ensuring the smooth operation of critical processes. The subsequent sections of this article will continue to explore factors influencing pipe selection and future trends in pipe technology, offering a comprehensive understanding of the evolving world of piping systems.
Do not miss the detailed course on What is Pipe II Schedule II Plastic II Jacketed II Tracing
Enrollment Link
6. Factors Influencing Pipe Selection
Key Considerations for Pipe Selection
Selecting the right type of pipe for a specific application involves a comprehensive assessment of various factors to ensure optimal performance, safety, and cost-effectiveness. Engineers and professionals must collaborate closely to make informed decisions. In this section, we explore the critical factors that influence pipe selection.
Fluid or Gas Characteristics
The nature of the substance being transported is a primary consideration. Factors include acidity, alkalinity, corrosiveness, viscosity, and whether the substance is a liquid or gas. Different materials react differently to various fluids and gases, impacting the pipe’s longevity and performance.
Pressure and Temperature Conditions
Understanding the operating pressure and temperature of the system is crucial. Some materials can withstand high pressures and temperatures, while others may degrade or deform under such conditions. Proper selection ensures the pipe can handle the anticipated stresses.
Corrosion Resistance
Corrosion can compromise the integrity of pipes and lead to leaks or failures. Industries dealing with aggressive chemicals or corrosive environments require pipes that offer exceptional corrosion resistance to ensure long-term reliability.
Environmental Factors
External conditions such as exposure to UV radiation, extreme weather, or soil conditions can affect the durability of pipes. Pipes installed above or below ground may have different material requirements to withstand environmental stresses.
Fluid Flow Characteristics
The efficiency of fluid flow is influenced by factors like the pipe’s inner surface roughness and diameter. Smooth interior surfaces reduce friction and pressure drop, contributing to better fluid flow rates.
Maintenance Requirements
Consideration of long-term maintenance is vital. Some pipes require more frequent inspections, cleaning, or replacement, impacting operational downtime and costs.
Cost-effectiveness
Balancing the initial cost of the pipe with its expected lifespan, maintenance needs, and potential operational savings is essential. Cheaper pipes might incur higher maintenance costs over time, while more expensive options could provide better long-term value.
Compatibility with Other Components
Pipes often connect to various components like valves, fittings, and pumps. Ensuring compatibility between the selected pipe and these components is crucial for a seamless system.
Collaboration and Informed Decisions
Selecting the right pipe involves multidisciplinary collaboration between engineers, materials experts, project managers, and stakeholders. A thorough understanding of the system’s requirements and careful consideration of all relevant factors are essential to making informed decisions that align with safety, performance, and cost objectives.
In the subsequent sections of this article, we will explore future trends in pipe technology, providing insights into the evolving landscape of piping systems and how industries are adapting to meet changing needs.
Do not miss the detailed course on What is Pipe II Schedule II Plastic II Jacketed II Tracing
Enrollment Link
7. Future Trends in Pipe Technology
Evolving Pipe Technology and Innovations
The field of pipe technology is continuously advancing, driven by the need for improved efficiency, sustainability, and safety across various industries. Emerging technologies and innovative materials are shaping the future of piping systems. In this section, we explore some of the notable trends and advancements in pipe technology.
Smart Pipe Systems
Smart pipes equipped with sensors and monitoring systems are revolutionizing how pipelines are managed. These sensors can detect factors such as temperature, pressure, flow rate, and even structural integrity in real-time. By providing valuable data, smart pipes enable predictive maintenance, minimizing downtime and preventing failures.
Enhanced Materials and Coatings
Research into advanced materials and coatings aims to create pipes that offer superior corrosion resistance, durability, and thermal stability. Nanotechnology and composite materials are being explored to enhance the mechanical properties of pipes while reducing their environmental impact.
Sustainable Pipe Manufacturing
The focus on sustainability is driving the development of eco-friendly pipe manufacturing processes. Innovations in recycling, reduced energy consumption, and environmentally friendly materials contribute to more sustainable pipe production methods.
Modular and Prefabricated Systems
Modular pipe systems that are pre-engineered and prefabricated off-site are gaining traction. These systems streamline installation, reduce on-site labor requirements, and enhance project efficiency.
3D Printing for Customization
3D printing is being explored for pipe manufacturing, allowing for intricate designs and customization. This technology could revolutionize the production of complex pipe shapes tailored to specific applications.
Integration with Data Analytics
Combining pipe sensor data with data analytics allows industries to gain insights into system performance, optimize operations, and make informed decisions for maintenance and improvements.
Robotics and Automation
Robotic systems are being developed to assist with pipe inspection, maintenance, and repair tasks. These systems can access hard-to-reach areas and perform tasks efficiently, reducing human intervention and associated risks.
The Path Forward
As industries continue to evolve and demand more from their piping systems, the field of pipe technology will adapt to meet these challenges. The trends mentioned above indicate a future where pipes are not only conduits for fluids and gases but also intelligent components that contribute to efficient and sustainable operations. By staying at the forefront of these innovations, industries can achieve enhanced performance, reduced costs, and a smaller environmental footprint.
In the concluding section of this article, we will summarize the key insights gained from exploring the diverse types of pipes, their applications, and the factors influencing their selection. We’ll highlight the critical role that pipe systems play in various industries and underscore the importance of making informed decisions to ensure optimal performance and success.
Do not miss the detailed course on What is Pipe II Schedule II Plastic II Jacketed II Tracing
Enrollment Link
8. Conclusion
Piping systems stand as the lifelines of modern industries, facilitating the transport of fluids and gases that drive essential processes. As we’ve explored throughout this article, the choice of pipe type is a pivotal decision that directly impacts the efficiency, safety, and reliability of these operations.
From metallic pipes known for their strength and durability, to non-metallic pipes prized for their corrosion resistance and versatility, and innovative composite pipes that combine the best of both worlds – each type serves distinct purposes in various industries. Specialized pipes cater to unique challenges, while considerations like fluid characteristics, pressure, temperature, and environmental conditions guide the selection process.
In the dynamic landscape of pipe technology, future trends like smart systems, sustainable materials, and advanced manufacturing techniques promise to revolutionize the way we view and use pipes. These innovations will optimize operations, enhance maintenance practices, and contribute to a more sustainable future.
As industries continue to evolve and diversify, the importance of selecting the right pipe for the job cannot be overstated. Engineers, materials experts, and stakeholders must collaborate to make informed decisions that align with operational needs, safety requirements, and cost-effectiveness.
In closing, the world of piping systems is vast and ever-evolving. By understanding the types of pipes available, their applications, and the factors that guide their selection, professionals across industries can ensure the seamless functioning of their operations, contributing to progress, efficiency, and innovation.
Frequently Asked Questions (FAQs)
Q1: What are the main types of pipes used in piping systems?
A1: Pipes used in piping systems can be categorized into metallic, non-metallic, and composite pipes. Metallic pipes include steel, stainless steel, cast iron, and copper pipes. Non-metallic pipes encompass materials like PVC and HDPE, while composite pipes combine characteristics of both metallic and non-metallic materials.
Q2: How do I choose the right type of pipe for my industry?
A2: Choosing the right pipe involves considering factors like the nature of the fluid or gas being transported, pressure and temperature conditions, corrosion resistance, environmental factors, and cost-effectiveness. Collaborate with experts in materials, engineering, and industry-specific needs to make informed decisions.
Q3: What are the advantages of using composite pipes?
A3: Composite pipes offer a blend of strength, corrosion resistance, and durability. They are especially useful in industries where traditional materials may fall short, such as offshore oil and gas operations, chemical processing, and corrosive environments.
Q4: How are future trends shaping pipe technology?
A4: Future trends in pipe technology include smart pipe systems with sensors for real-time monitoring, enhanced materials and coatings for better corrosion resistance, sustainable manufacturing methods, 3D printing for customization, and integration with data analytics for improved operations and maintenance.
Q5: Why is pipe selection important in industries?
A5: Pipe selection is critical because the right choice directly affects the efficiency, safety, and reliability of industrial processes. Proper pipe selection ensures optimal performance, durability, and cost-effectiveness, while also considering factors like fluid characteristics, pressure, temperature, and environmental conditions.
Recommended courses (Published on EPCLand)
- Basics of Piping Engineering
- Piping Layout Engineering
- Piping Material Engineering
- Piping Stress Analysis
- Complete Course on Piping Engineering
- Material Requisitions
- Piping Material Specifications
- Valve Material Specifications
Don’t miss the published articles on following:
Related Video
Attempt Quiz
Question 1:
Which type of pipe is commonly used for water supply and drainage systems?
Explanation: PVC (Polyvinyl Chloride) pipe is commonly used for water supply and drainage systems due to its corrosion resistance and cost-effectiveness.
Question 2:
Which type of pipe is often used for high-pressure and high-temperature applications?
Explanation: Stainless Steel pipe is often used for high-pressure and high-temperature applications due to its strength, corrosion resistance, and ability to withstand extreme conditions.
Question 3:
Which type of pipe is known for its flexibility and ability to resist chemical corrosion?
Explanation: HDPE (High-Density Polyethylene) pipe is known for its flexibility, durability, and resistance to chemical corrosion, making it suitable for a wide range of applications.
Question 4:
Which type of pipe is often used for natural gas distribution?
Explanation: Steel pipe, often coated with anti-corrosive materials, is commonly used for natural gas distribution due to its strength, durability, and ability to withstand pressure.
Question 5:
Which type of pipe is often used for conveying corrosive fluids?
Explanation: Stainless Steel pipe is often used for conveying corrosive fluids due to its resistance to corrosion, ensuring that the pipe remains durable and free from chemical degradation.