Introduction
Heat exchangers play a pivotal role in various industries, facilitating efficient heat transfer between fluids. Among the myriad types of heat exchangers, shell and tube heat exchangers stand as one of the most prevalent and versatile options. In this article, we will delve into the fundamental principles, design considerations, efficiency enhancement techniques, applications across industries, advantages, and disadvantages of shell and tube heat exchangers. We will also examine case studies, maintenance practices, comparative analyses with other heat exchanger types, and future trends in this technology.
Table of Contents
Similar Articles on other Exchangers
Heat Exchanger Type | Check Article Link |
---|---|
Helical Coil Heat Exchanger | Link |
Tube-in-Tube Heat Exchanger | Link |
Spiral Heat Exchanger | Link |
U-Tube Heat Exchanger | Link |
Shell and Tube Heat Exchanger | Link |
Plate Heat Exchanger | Link |
Double Pipe Heat Exchanger | Link |
Finned Tube Heat Exchanger | Link |
Don’t miss the Detailed course on Drums/Exchanger Piping Layout & Stress Analysis
Enrollment Link
Fundamentals of Heat Exchange
Before delving into the specifics of shell & tube heat exchangers, it’s crucial to understand the fundamentals of heat exchange. Heat transfer mechanisms—conduction, convection, and radiation—form the basis of all heat exchanger designs. These mechanisms govern the movement of thermal energy from one substance to another, influencing various industrial processes. Efficient heat exchange is essential to optimize energy usage and maintain process temperatures.
Heat exchangers can be classified into different types based on their design and application. Shell and tube heat exchangers, with their distinctive construction and versatile capabilities, warrant closer examination.
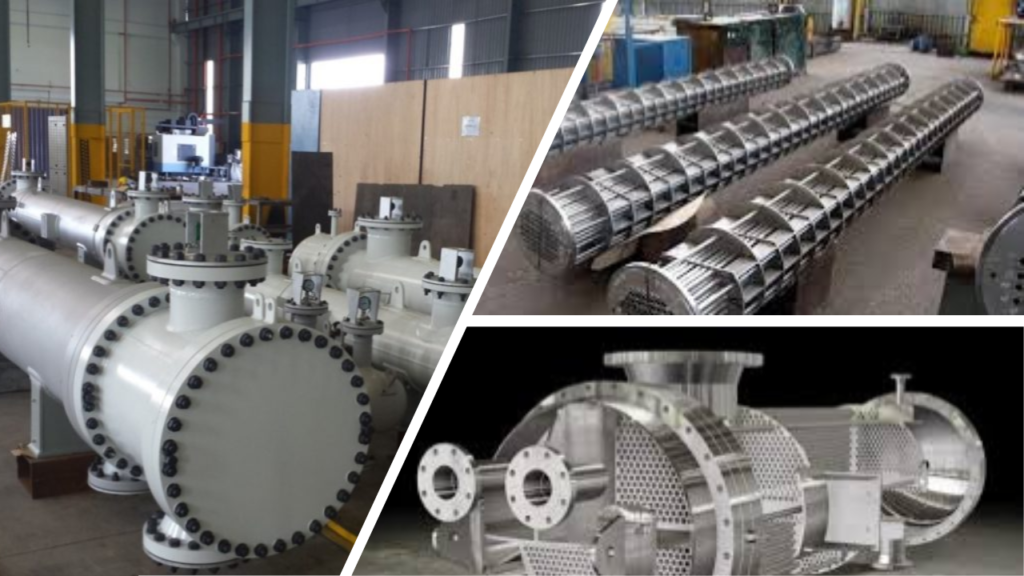
Shell & Tube Heat Exchangers: An Overview
A shell & tube heat exchanger consists of cylindrical tubes enclosed within a larger shell. The shell typically has inlet and outlet ports for one fluid, while the tubes facilitate the flow of another fluid. Components like tube sheets, baffles, and headers enhance the efficiency of these exchangers. Various types of shell and tube heat exchangers—fixed tube sheet, floating head, U-tube, and more—are tailored to suit different applications.
Working Principles
The efficiency of shell & tube heat exchangers stems from their working principles. These exchangers operate in either counterflow or parallel flow configurations. In counterflow, the hot fluid enters the exchanger from one end, while the cold fluid enters from the opposite end, resulting in optimal heat transfer. Parallel flow involves both fluids flowing in the same direction, which can lead to less efficient heat exchange.
The operation of a shell and tube heat exchanger involves fluid entry, a designated flow path within the tubes, the transfer of heat energy between fluids, and the eventual exit of the fluids. The ability to maintain a high temperature gradient between the fluids ensures effective heat transfer.
Codes & Standards for Shell and Tube Heat Exchangers
Code/Standard | Description |
---|---|
ASME Boiler and Pressure Vessel Code | Provides rules for design, fabrication, inspection of pressure vessels, including heat exchangers. Divisions I and II cover design, Division IX covers welding and brazing qualifications. |
TEMA Standards | Guidelines for design, construction of shell and tube heat exchangers. Covers various types of exchangers and design considerations. |
API Standards | Relevant to petrochemical and oil industries. API 660 covers design, fabrication of shell-and-tube heat exchangers. API 661 focuses on air-cooled heat exchangers. |
ISO Standards | ISO 16812 provides guidelines for design, thermal performance of shell-and-tube heat exchangers. ISO 15547-1 specifies mechanical design requirements. |
ASTM Standards | Standards for materials used in construction and manufacturing. Ensures quality, compatibility of materials in heat exchangers. |
EN Standards | European standards for materials, pressure vessel design. EN 10216 and EN 13445 are relevant to shell and tube heat exchangers in European regions. |
National and Local Regulations | Regulations from governmental bodies such as OSHA (US), HSE (UK), specifying safety and operational requirements for heat exchangers. |
Heat Exchanger Design Considerations
Designing a shell & tube heat exchanger requires careful consideration of several factors. Fluid properties, flow rates, and temperature differences between the hot and cold fluids significantly influence the design. The overall heat transfer coefficient (U-value) and thermal efficiency of the exchanger are crucial parameters that determine its performance.
Material selection for the tubes, shell, and other components is equally critical. Compatibility with the fluids, corrosion resistance, and thermal conductivity play vital roles in preventing degradation and ensuring optimal heat transfer efficiency.
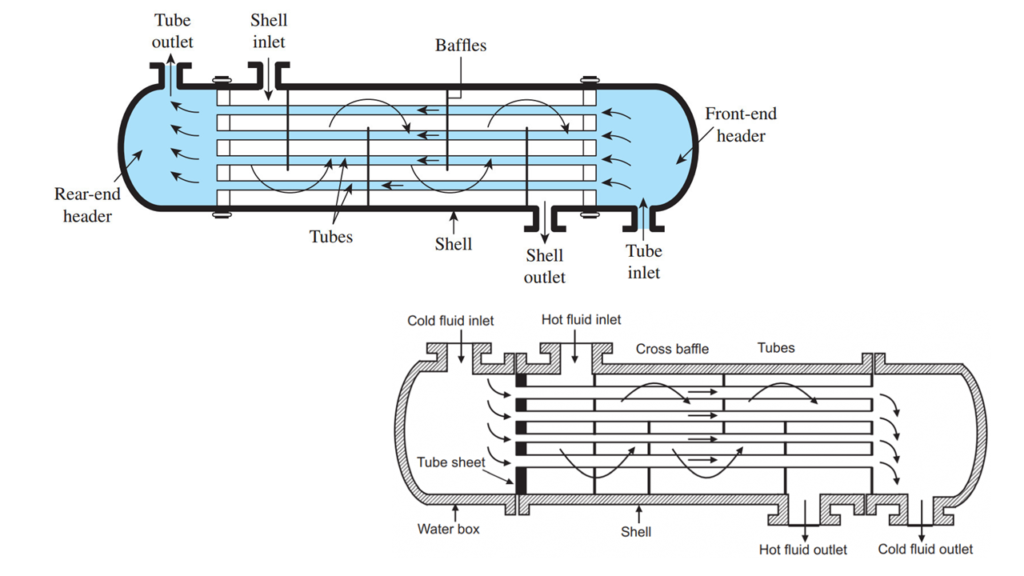
Efficiency Enhancement Techniques
Efficiency is paramount in heat exchanger operation, but fouling can hinder this efficiency over time. Fouling, the accumulation of deposits on tube surfaces, reduces heat transfer rates. Cleaning methods such as mechanical cleaning, chemical cleaning, and online cleaning systems help mitigate fouling and maintain the exchanger’s efficiency.
To enhance heat transfer rates, extended surface tubes and turbulators are employed. These structures increase the surface area available for heat exchange, promoting more efficient energy transfer between fluids.
Don’t miss the Detailed course on Drums/Exchanger Piping Layout & Stress Analysis
Enrollment Link
Applications Across Industries
The versatility of shell and tube heat exchangers finds application across a multitude of industries:
- Petrochemical Industry: Shell and tube heat exchangers are used in cooling and heating processes in refineries, contributing to the efficient operation of distillation units and catalytic converters.
- Power Generation: They play a vital role in power plants as condensers and feedwater heaters, optimizing energy conversion and reducing operational costs.
- HVAC Systems: Heat recovery and air conditioning systems benefit from these exchangers, maintaining comfortable indoor environments while conserving energy.
- Food and Beverage Industry: Shell and tube heat exchangers facilitate processes such as pasteurization and sterilization, ensuring product safety and quality.
- Pharmaceutical Sector: Critical process temperatures in pharmaceutical manufacturing are maintained with precision using these exchangers.
Advantages and Disadvantages
As with any technology, shell and tube heat exchangers come with their own set of advantages and disadvantages. On the positive side, they boast high efficiency due to their extensive surface area for heat transfer. They are also suitable for high-pressure and high-temperature applications. However, the initial cost of these exchangers can be relatively high, and their complex construction can pose challenges during maintenance. Additionally, the space requirements for installation should not be overlooked.
Case Studies
Real-world case studies underscore the effectiveness of shell and tube heat exchangers. In a chemical plant, these exchangers were employed to cool reaction processes, leading to improved reaction rates and product quality. In a power plant, shell and tube exchangers contributed to enhanced energy efficiency and reduced operational costs by efficiently condensing steam.
Maintenance and Troubleshooting
The longevity of shell and tube heat exchangers hinges on proper maintenance. Routine practices such as regular inspection, cleaning, and repairs are essential to prevent fouling and ensure optimal performance. Troubleshooting issues like leaks, flow imbalances, and reduced heat transfer efficiency necessitates a systematic approach to identify and rectify problems promptly.
Don’t miss the Detailed course on Drums/Exchanger Piping Layout & Stress Analysis
Enrollment Link
Comparative Analysis
While shell and tube heat exchangers offer numerous advantages, it’s essential to compare them with other heat exchanger types. Plate heat exchangers, for instance, are compact and suitable for applications with space limitations. Finned-tube exchangers enhance heat transfer by increasing surface area. The choice between these types depends on factors like efficiency requirements, available space, and fluid properties.
Future Trends and Innovations
The field of heat exchangers continues to evolve. Advancements in materials and coatings hold promise for improved heat transfer efficiency and extended equipment lifetimes. The integration of Industry 4.0 technologies enables predictive maintenance, minimizing downtime and maximizing productivity. The pursuit of greater energy efficiency and sustainability also drives innovation in heat exchange technology.
Conclusion
Shell and tube heat exchangers emerge as an indispensable component in industries that rely on efficient heat exchange. Their versatility, efficiency, and wide range of applications make them a cornerstone of modern engineering. As industries continue to evolve, so too will heat exchange technology, with shell and tube exchangers at the forefront of innovation. It is clear that the efficient exchange of thermal energy will remain a driving force in industrial processes, and shell and tube heat exchangers will continue to play a vital role in this endeavor.
FAQs
1. What is a shell and tube heat exchanger?
A shell and tube heat exchanger is a device used to transfer heat between two fluids that are at different temperatures. It consists of cylindrical tubes enclosed within a larger shell. One fluid flows through the tubes, while the other flows around the outside of the tubes within the shell. This design allows for efficient heat exchange between the fluids.
2. What are the main components of a shell and tube heat exchanger?
The main components of a shell and tube heat exchanger include the shell, tubes, tube sheets, baffles, front head, rear head, channel covers, pass partitions, tie rods or spacers, tube supports, and nozzles or connections. Each component serves a specific purpose in facilitating fluid flow and heat transfer.
3. What are the advantages of using shell and tube heat exchangers?
Shell and tube heat exchangers offer several advantages, including high heat transfer efficiency due to their extensive surface area, versatility to handle high-pressure and high-temperature applications, and suitability for a wide range of industries such as petrochemicals, power generation, HVAC systems, and more.
4. How do you maintain and clean shell and tube heat exchangers?
Regular maintenance is crucial for the optimal performance of shell and tube heat exchangers. Maintenance practices include routine inspection, cleaning of tube surfaces to prevent fouling, and addressing issues such as leaks or flow imbalances. Various methods like mechanical cleaning, chemical cleaning, and online cleaning systems are employed to keep the heat exchanger efficient.
5. What are some typical applications of shell and tube heat exchangers?
Shell and tube heat exchangers find applications in various industries. They are used in the petrochemical industry for cooling and heating processes, in power generation as condensers and feedwater heaters, in HVAC systems for heat recovery, in the food and beverage industry for pasteurization, and in the pharmaceutical sector to maintain critical process temperatures.
Recommended courses (Published on EPCLand)
- Basics of Piping Engineering
- Piping Layout Engineering
- Piping Material Engineering
- Piping Stress Analysis
- Complete Course on Piping Engineering
- Material Requisitions
- Piping Material Specifications
- Valve Material Specifications
Don’t miss the published articles on following:
Related Video
Attempt Quiz
Question 1:
What is the primary purpose of a shell and tube heat exchanger?
Explanation: The primary purpose of a shell and tube heat exchanger is to transfer heat between two different fluids, allowing them to exchange thermal energy without direct contact.
Question 2:
What are the main components of a shell and tube heat exchanger?
Explanation: The main components of a shell and tube heat exchanger are the tubes and the shell (casing) that houses the tubes. These components enable the heat transfer process.
Question 3:
Which fluid flows through the tubes in a typical shell and tube heat exchanger?
Explanation: In a shell and tube heat exchanger, one of the heat exchange fluids flows through the tubes, while the other fluid (often referred to as the “shell-side” fluid) flows around the tubes in the shell.
Question 4:
What is the purpose of baffles inside the shell of a shell and tube heat exchanger?
Explanation: Baffles are plates or vanes inside the shell of a shell and tube heat exchanger that create turbulence in the shell-side fluid flow. This turbulence enhances heat transfer efficiency by promoting mixing and preventing stagnant regions.
Question 5:
What factors influence the selection of a shell and tube heat exchanger?
Explanation: The selection of a shell and tube heat exchanger is influenced by factors such as the physical properties of the heat exchange fluids (viscosity, flow rate, temperature), required heat transfer rate, pressure drop considerations, and space limitations.