Introduction
Valves play a vital role in engineering by facilitating the control of fluid flow, making them indispensable components in various industries. The ability to regulate the movement of liquids, gases, and even slurries is crucial for ensuring optimal operation and safety in applications ranging from oil and gas extraction to manufacturing processes. A fundamental aspect of understanding valves lies in their classification, which enables engineers and professionals to select the appropriate valve type for specific tasks.
In this article, we delve into the intricate world of valve classification and types. By categorizing valves based on their functions, designs, actuation methods, and applications, we aim to provide a comprehensive resource for both beginners and experts in the field. By recognizing the significance of valve classification, professionals can make informed decisions when selecting valves for diverse industrial settings. Join us as we explore the various aspects of valves, from their basic principles to cutting-edge trends, shedding light on the mechanisms that power some of the most critical processes across industries.
Table of Contents
Do not miss the Detailed course on Valve Classifications & Types
Enrollment Link
Valve Basics
Valves are mechanical devices that serve a crucial role in controlling the flow of fluids within various systems and processes. Their primary function is to start, stop, or regulate the movement of liquids, gases, or slurries. Valves are employed in a wide range of applications, from simple household plumbing to complex industrial processes. Understanding the basics of valves is essential to grasp their significance in engineering and various industries.
Components of Valves
Valves consist of several key components that work together to control fluid flow:
- Body: The main casing of the valve, which houses all internal components and provides a passage for fluid to flow through.
- Bonnet: The cover that encloses the internal parts of the valve and provides a point for attachment of the actuator or handle.
- Trim: The set of internal components that directly interact with the fluid, including the disc, seat, stem, and other parts responsible for regulating flow.
- Actuator: A mechanism that controls the opening and closing of the valve, either manually or automatically.
- Handle or Handwheel: A component used for manual operation, allowing users to turn the valve on or off.
- Connections: Inlet and outlet ports that facilitate the entry and exit of fluids from the valve.
Operating Principles
Valves operate on a simple principle: they can be manipulated to control the passage of fluids. The manipulation can involve:
- Opening: Allowing fluid to flow through the valve, often by moving the internal components away from the flow path.
- Closing: Blocking the flow of fluid by bringing the internal components into the flow path, creating a seal.
- Modulating: Adjusting the degree of openness to control the flow rate, pressure, or other parameters.
Valves are designed to function efficiently and reliably across a wide range of conditions, including variations in temperature, pressure, and fluid composition.
Importance of Valve Classification
The diversity of applications and operational requirements demands a systematic approach to categorizing valves. Valve classification allows engineers and technicians to:
- Select the Right Valve: Different applications call for different types of valves. Classification helps in identifying the best-suited valve for a specific function.
- Ensure Efficiency and Safety: Proper valve selection prevents issues like fluid leakage, flow disruptions, and overpressure situations, promoting safe and efficient operation.
- Minimize Maintenance and Downtime: Understanding the characteristics of each valve type aids in predicting maintenance needs, reducing unexpected downtime.
- Adapt to Industry Needs: Industries such as oil and gas, water treatment, and manufacturing have unique requirements. Proper classification facilitates the adaptation of valve technology to meet these needs.
In the subsequent sections of this article, we will delve deeper into the various classifications of valves based on their functions, designs, actuation methods, and applications. By the end of this guide, you’ll have a comprehensive understanding of the world of valves and how their classification plays a pivotal role in engineering and industry.
Do not miss the Detailed course on Valve Classifications & Types
Enrollment Link
Valve Classification Based on Function
Valves serve a variety of functions within fluid systems, ranging from isolating and regulating flow to preventing backflow. Categorizing valves based on their primary functions provides a clear understanding of their roles and capabilities in different applications.
Isolation Valves
Gate Valves: Gate valves are designed for full shutoff by raising or lowering a gate-like disc perpendicular to the flow path. They offer minimal flow restriction when fully open, making them suitable for applications where on/off control is required.
Ball Valves: Ball valves use a rotating ball with a bore to control fluid flow. They offer fast shutoff capabilities and are commonly used in applications that require quick and frequent operation.
Regulation Valves
Globe Valves: Globe valves provide precise control over flow by adjusting the position of a disk in relation to the flow path. They are often used in applications requiring fine-tuned regulation.
Butterfly Valves: Butterfly valves use a circular disc that pivots on a shaft to control flow. They are known for their compact design and fast operation, making them suitable for large-scale applications.
Check Valves
Swing Check Valves: Swing check valves have a hinged disc that swings open to allow flow in one direction and closes to prevent backflow. They are commonly used to prevent reverse flow in pipelines.
Lift Check Valves: Lift check valves utilize a vertically moving disc to regulate flow. They are suitable for applications with high flow rates and prevent backflow through the system.
Understanding the distinctions between isolation, regulation, and backflow prevention valves enables engineers and operators to choose the right valve for the intended function. This classification ensures that fluid systems operate efficiently while maintaining safety and reliability.
In the following sections, we will delve deeper into valve classification based on design, actuation methods, and application-specific requirements. By the end of this guide, you will have a comprehensive grasp of the various types of valves available and their roles in different industrial settings.
Valve Classification Based on Design
Valves come in various designs, each tailored to specific applications and operational requirements. By categorizing valves based on their design characteristics, engineers can better understand their mechanisms and select the most suitable option for their needs.
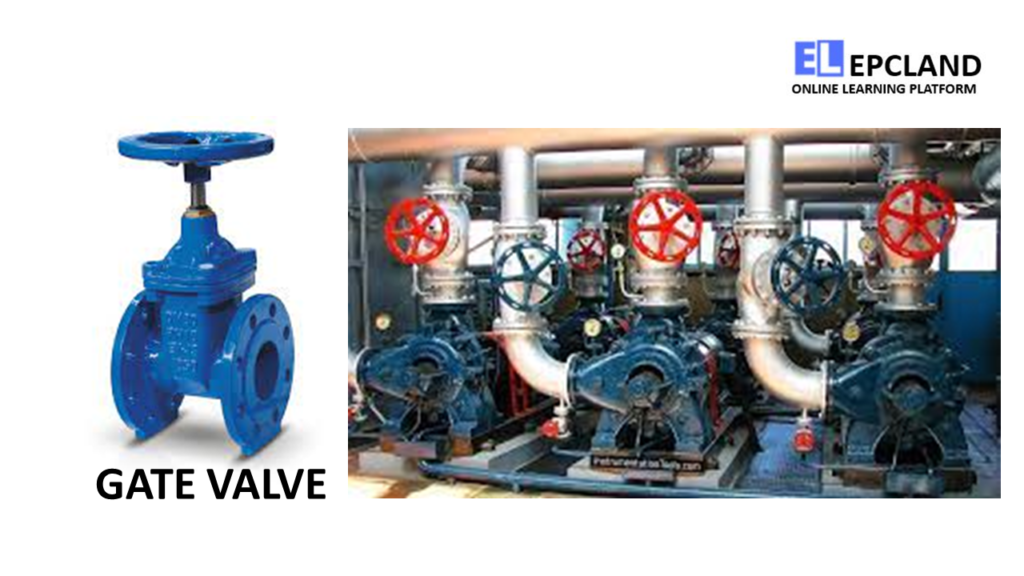
Linear Motion Valves
Gate Valves: Gate valves operate by raising or lowering a gate-like barrier to control flow. They are typically used for on/off applications and are known for their minimal pressure drop when fully open.
Globe Valves: Globe valves feature a movable disk that controls flow by modulating the position of the disk relative to the flow path. Their precise control makes them ideal for regulating flow rates.
Pinch Valves: Pinch valves use a flexible tube that can be pinched shut to stop flow. They are particularly useful for handling abrasive or corrosive fluids.
Rotary Motion Valves
Ball Valves: Ball valves use a rotating ball with a bore to regulate flow. They offer fast shutoff capabilities and are commonly used in applications that require frequent operation.
Butterfly Valves: Butterfly valves employ a disc that rotates on a shaft to control flow. They are lightweight, compact, and suitable for applications with large pipe diameters.
Plug Valves: Plug valves use a cylindrical or conical plug to control flow. They are versatile and can be used for various flow control tasks.
Specialty Valves
Diaphragm Valves: Diaphragm valves use a flexible diaphragm to regulate flow. They are often used in applications requiring a high level of cleanliness and hygiene.
Needle Valves: Needle valves have a slender, tapered needle-like stem that provides precise flow control. They are commonly used in applications requiring fine adjustments.
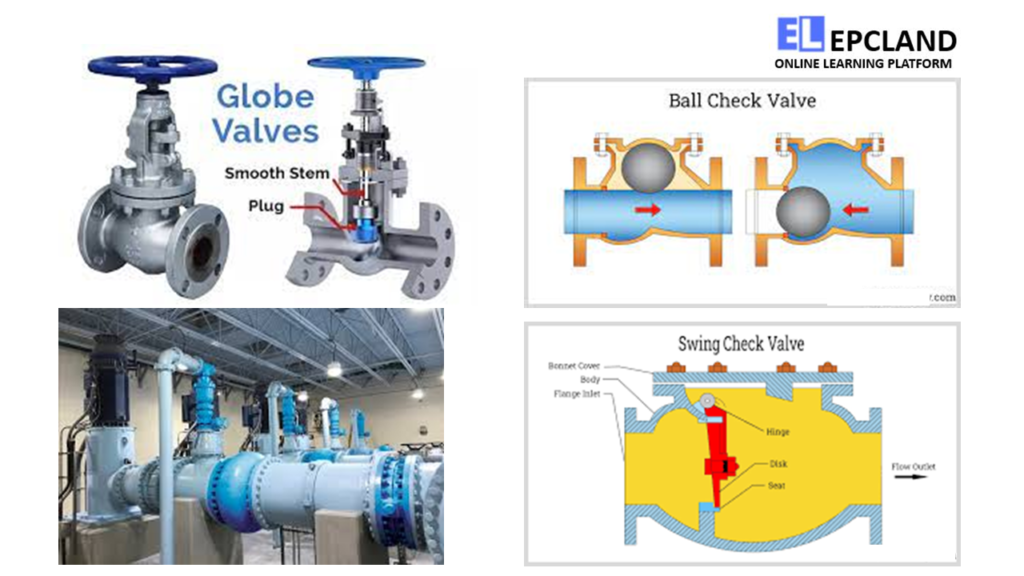
Pressure Relief Valves: Pressure relief valves automatically release excess pressure from a system to prevent overpressure. They play a critical role in maintaining system safety.
By understanding the different designs of valves, engineers can make informed decisions about which type of valve best suits their specific application requirements. In the subsequent sections, we will delve into valve classification based on actuation methods, application contexts, and material considerations, providing a comprehensive overview of valve functionality and usage.
Do not miss the Detailed course on Valve Classifications & Types
Enrollment Link
Valve Classification Based on Actuation
Valves can be operated manually, with external power, or even automatically based on certain conditions. Categorizing valves by their actuation methods helps engineers determine the most suitable control mechanism for their applications.
Manual Valves
Handwheel-operated Valves: These valves are controlled by rotating a handwheel attached to the valve stem. They are simple, reliable, and suitable for applications where frequent adjustments are not necessary.
Lever-operated Valves: Lever-operated valves use a lever to control the valve’s position. They provide quick manual control and are often used in situations where rapid adjustments are needed.
Gear-operated Valves: Gear-operated valves employ a gearbox to control the valve’s position. This mechanism provides mechanical advantage for easier operation of larger valves.
Actuated Valves
Electrically Actuated Valves: These valves use electric motors or solenoids to control the valve’s position. They offer precise control and can be integrated into automation systems.
Pneumatically Actuated Valves: Pneumatic valves are controlled using compressed air. They are widely used for quick and reliable operation in various industrial settings.
Hydraulically Actuated Valves: Hydraulic valves are operated using hydraulic fluid pressure. They are suitable for heavy-duty applications requiring high force.
Automatic Valves
Pressure-operated Valves: These valves respond to changes in fluid pressure. When the pressure reaches a certain threshold, the valve automatically opens or closes to maintain the desired pressure level.
Temperature-operated Valves: Temperature-operated valves respond to changes in temperature. They are often used to control processes that involve heat exchange.
Flow Control Valves: Flow control valves automatically adjust their position based on the flow rate of the fluid. They help maintain a consistent flow rate even when conditions change.
By classifying valves based on their actuation methods, engineers can choose the appropriate control mechanism that aligns with their specific operational needs. The subsequent sections will delve into the application-specific contexts where these valve types find utility, as well as considerations related to material compatibility and maintenance practices.
Valve Classification Based on Application
Valves are utilized across a wide range of industries and applications, each with unique requirements and challenges. Categorizing valves based on their application contexts helps engineers select valves that are optimized for specific operational demands.
Oil and Gas Industry
- Exploration and Production: Valves play a crucial role in controlling the flow of hydrocarbons from reservoirs to processing facilities.
- Refining and Petrochemicals: Valves are used in refining processes to regulate the flow of various products and chemicals.
- Pipeline Transport: Valves are deployed to manage the flow of oil and gas through pipelines and distribution networks.
Water Treatment
- Water Purification: Valves are used in water treatment plants to control the flow of water through different treatment stages.
- Distribution Systems: Valves regulate the flow of treated water through pipelines for distribution to homes and businesses.
- Wastewater Management: Valves manage the flow of wastewater for treatment and disposal.
Manufacturing Sector
- Process Control: Valves are integral to manufacturing processes, regulating the flow of raw materials, chemicals, and gases.
- Industrial Automation: Automated valves are used to optimize manufacturing efficiency and reduce manual intervention.
Pharmaceutical and Food Industries
- Hygienic Valves: Valves with sanitary design are crucial for maintaining the purity of pharmaceutical and food products.
- Sterilization Processes: Valves are used in processes requiring steam or other sterilization methods.
By understanding how valves are employed in specific industries, engineers can make informed decisions regarding valve selection and deployment. In the subsequent sections, we will explore considerations related to material compatibility, valve selection criteria, and maintenance practices, providing a comprehensive guide to understanding and using valves effectively.
Do not miss the Detailed course on Valve Classifications & Types
Enrollment Link
Material and Media Compatibility
The materials used in valves must be carefully selected to ensure compatibility with the fluids they will handle. Different fluids and operational conditions can lead to corrosion, erosion, and other forms of damage. Proper material selection is crucial to ensure the longevity and reliability of valves.
Common Valve Materials
- Cast Iron: Used for general-purpose applications where corrosion resistance is not a primary concern.
- Stainless Steel: Offers excellent corrosion resistance and is suitable for a wide range of fluids.
- Bronze: Known for its resistance to corrosion and wear, often used in marine and freshwater applications.
- Plastic: Used for applications where chemical compatibility and corrosion resistance are critical.
Material Considerations
- Corrosion Resistance: Choosing materials that can withstand the corrosive effects of the fluid being handled.
- Abrasion Resistance: For applications with abrasive fluids, materials that can withstand wear and erosion are essential.
- Temperature and Pressure: Selecting materials that maintain their mechanical properties under specific temperature and pressure conditions.
- Chemical Compatibility: Ensuring that the materials are compatible with the chemicals present in the fluid.
By understanding the importance of material compatibility, engineers can make informed decisions when selecting valves to ensure their long-term reliability and performance. In the subsequent sections, we will delve into valve selection considerations, maintenance practices, and troubleshooting techniques to further enhance your understanding of valves and their applications.
Valve Selection Considerations
Selecting the right valve for a specific application involves considering a range of factors to ensure optimal performance and reliability. Understanding these considerations is essential to avoid issues such as flow disruptions, leakage, and inefficiencies.
Operating Conditions
- Pressure: Choosing a valve that can withstand the operating pressure without failure or leakage.
- Temperature: Selecting materials and designs that can handle the temperature range of the fluid.
- Flow Characteristics: Matching the valve design to the expected flow profile, whether it’s laminar, turbulent, or transitional.
Valve Sizing
- Flow Rate: Ensuring the valve size can handle the required flow rate without excessive pressure drop.
- Cv Value: Using the Cv value to quantify the valve’s capacity to pass a specific flow rate with a given pressure drop.
Type of Valve
- Functionality: Selecting the appropriate valve type based on its intended function, whether it’s isolation, regulation, or backflow prevention.
- Design: Choosing a valve design that aligns with the system’s requirements and constraints.
Industry Standards
- Compliance: Ensuring the selected valve meets relevant industry standards and regulations.
- Quality: Opting for valves from reputable manufacturers known for producing high-quality products.
Consulting Engineers
- Expertise: Involving consulting engineers or valve specialists to provide insights and recommendations based on their expertise.
Application-specific Considerations
- Fluid Properties: Understanding the properties of the fluid being handled, including corrosiveness, viscosity, and more.
- Environmental Conditions: Considering factors such as exposure to the elements, potential contamination, and safety risks.
By thoroughly evaluating these considerations, engineers can make well-informed decisions when selecting valves, leading to improved system efficiency and reliability. In the upcoming sections, we will delve into maintenance practices, troubleshooting guidelines, and future trends in valve technology, providing a comprehensive overview of valve usage and advancement.
Do not miss the Detailed course on Valve Classifications & Types
Enrollment Link
Maintenance and Troubleshooting
Ensuring the long-term reliability and performance of valves requires regular maintenance and prompt troubleshooting when issues arise. Proper maintenance practices can extend the lifespan of valves and prevent costly downtime.
Valve Maintenance Practices
- Regular Inspections: Periodic visual inspections to identify signs of wear, corrosion, leaks, or other abnormalities.
- Lubrication: Applying appropriate lubricants to moving parts to reduce friction and ensure smooth operation.
- Cleaning: Removing debris, scale, and buildup that can hinder valve performance.
- Seal Replacement: Replacing seals and gaskets to prevent leaks and maintain proper sealing.
- Actuator Maintenance: Maintaining actuators to ensure proper valve actuation.
Troubleshooting Common Valve Issues
- Leakage: Identifying and addressing leaks at seals, joints, or valve components.
- Sticking or Binding: Investigating the causes of valves not opening or closing smoothly.
- Noise and Vibration: Analyzing sources of vibration or noise during valve operation and mitigating them.
- Cavitation: Addressing cavitation, a phenomenon that can lead to erosion and valve damage.
- Excessive Wear: Determining the cause of wear and erosion on valve components and taking corrective actions.
Valve Testing and Calibration
- Performance Testing: Conducting tests to ensure valves meet desired flow rates, pressure ratings, and leakage limits.
- Calibration: Verifying that valves open and close at the correct positions as per control signals.
By implementing effective maintenance practices and troubleshooting techniques, engineers can ensure the reliable operation of valves, minimize downtime, and extend the lifecycle of the equipment. In the following section, we will explore emerging trends in valve technology and their potential impact on the field.
Future Trends in Valve Technology
As technology continues to advance, valves are also evolving to meet the demands of modern industries. Several trends are shaping the future of valve technology, offering new possibilities for efficiency, automation, and enhanced performance.
Smart Valve Technology
- Sensor Integration: Valves equipped with sensors for monitoring variables such as pressure, temperature, and flow rate.
- Remote Monitoring: Enabling real-time monitoring and control of valves through connected systems and the Internet of Things (IoT).
Automation and Control
- Advanced Actuation: Integration of advanced actuators for precise and rapid valve control.
- Intelligent Control Algorithms: Implementation of algorithms that optimize valve settings based on changing operational conditions.
Energy Efficiency
- Energy Recovery Valves: Valves that capture and reuse energy from fluid systems, enhancing energy efficiency.
- Flow Optimization: Valves designed to reduce pressure drops and energy losses during flow control.
Material Advancements
- Advanced Coatings: Development of coatings to enhance valve material performance and extend lifespan.
- Composite Materials: Exploration of lightweight and corrosion-resistant composite materials for valve construction.
Predictive Maintenance
- Condition Monitoring: Predictive maintenance using data analytics to identify potential valve failures before they occur.
- Reduced Downtime: Timely maintenance based on data-driven insights, minimizing unplanned downtime.
Environmental Sustainability
- Low Emission Valves: Valves designed to minimize fugitive emissions and contribute to environmental protection.
- Water Conservation: Valves optimized for water-efficient processes and conservation.
As these trends continue to shape the field of valve technology, engineers and professionals in various industries will have access to innovative solutions that enhance efficiency, safety, and environmental responsibility. By staying informed about these developments, engineers can adapt their practices and systems to leverage the benefits offered by these emerging technologies.
Do not miss the Detailed course on Valve Classifications & Types
Enrollment Link
Conclusion
Valves are essential components in a wide array of industries, from oil and gas to manufacturing and beyond. Understanding valve classification and types is crucial for making informed decisions about their selection, deployment, and maintenance. By comprehending their functions, designs, actuation methods, and applications, engineers can optimize processes, enhance system reliability, and contribute to the advancement of various industries. Staying abreast of future trends in valve technology ensures that engineers remain equipped to harness the benefits of cutting-edge innovations, ensuring a productive and sustainable future for fluid control systems.
FAQs
Frequently asked questions (FAQs) related to valve classification and types:
1. What is the primary function of valves in engineering? Valves serve as mechanical devices that regulate, control, or direct the flow of fluids, including liquids, gases, and slurries. They are crucial for starting, stopping, or modulating fluid movement in various industrial applications.
2. Why is valve classification important in engineering? Valve classification categorizes valves based on their functions, designs, actuation methods, and applications. This helps engineers and professionals choose the right valve type for specific tasks, ensuring optimal performance, safety, and efficiency in various industries.
3. How do isolation valves differ from regulation valves? Isolation valves, such as gate valves and ball valves, are designed for full shut-off to block fluid flow. Regulation valves, such as globe valves and butterfly valves, are used to control flow rates and pressure levels with precision.
4. What factors should be considered when selecting a valve for an application? Several factors should be considered, including operating conditions (pressure, temperature), flow rate requirements, valve type (isolation, regulation), material compatibility, industry standards, and the expertise of consulting engineers.
5. What are the emerging trends in valve technology? Emerging trends in valve technology include smart valves with integrated sensors for remote monitoring and control, advanced actuation mechanisms, energy-efficient designs, predictive maintenance using data analytics, and a focus on environmental sustainability through low emission and water-efficient valves.
Recommended courses (Published on EPCLand)
- Basics of Piping Engineering
- Piping Layout Engineering
- Piping Material Engineering
- Piping Stress Analysis
- Complete Course on Piping Engineering
- Material Requisitions
- Piping Material Specifications
- Valve Material Specifications
Don’t miss the published articles on following:
Related Video
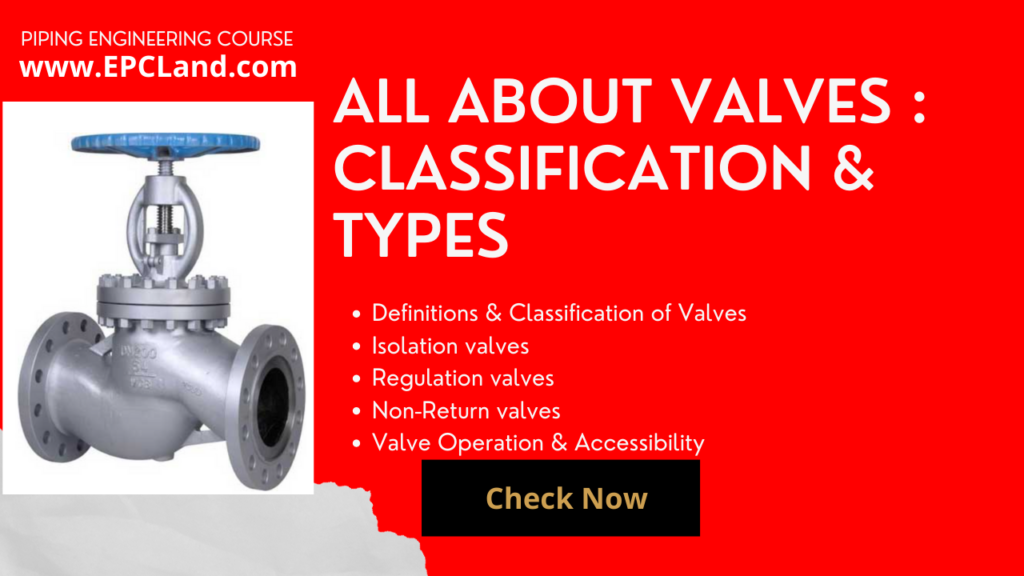
Attempt Quiz
Question 1:
Which of the following is not a common type of valve?
Explanation: “Cylinder Valve” is not a common type of valve. The other options (Gate Valve, Control Valve, and Diaphragm Valve) are commonly used in various industries.
Question 2:
Which type of valve provides bi-directional isolation with a sliding gate mechanism?
Explanation: A “Gate Valve” provides bi-directional isolation using a sliding gate mechanism that moves perpendicular to the flow direction.
Question 3:
Which type of valve is commonly used for regulating fluid flow by adjusting the position of a disk?
Explanation: A “Globe Valve” is commonly used for regulating fluid flow by adjusting the position of a disk, which moves perpendicular to the flow direction.
Question 4:
Which type of valve is suitable for applications requiring a tight shut-off and reduced pressure drop?
Explanation: A “Ball Valve” is suitable for applications requiring a tight shut-off and reduced pressure drop due to its design with a spherical ball as the closing element.
Question 5:
Which type of valve allows flow in one direction and prevents backflow?
Explanation: A “Check Valve” allows flow in one direction and prevents backflow by automatically closing when the flow direction reverses.