Introduction to Pipe Manufacturing
Pipes play a crucial role in various industries, including oil and gas, construction, water management, and transportation. These cylindrical structures are used to transport fluids, gases, and even solids, making them essential components of modern infrastructure. The process of manufacturing pipes involves a range of techniques to ensure their quality, durability, and suitability for specific applications.
Table of Contents
Do not miss the detailed course on What is Pipe II Schedule II Plastic II Jacketed II Tracing
Enrollment Link
Seamless Pipe Manufacturing
Introduction to Seamless Pipes
Seamless pipes are known for their uniformity and lack of welded seams. This characteristic makes them stronger and more suitable for high-pressure applications. Two primary methods are employed in seamless pipe manufacturing: the hot rolling process and the cold drawing process.
Hot Rolling Process
- Preparation of Raw Materials: The process begins with selecting high-quality steel billets. These billets are heated to a specific temperature for easy manipulation.
- Heating and Piercing: The heated billet is pierced to create a hollow tube-like structure. This pierced billet is then further heated and transformed into a cylindrical shape.
- Rolling and Sizing: The billet is rolled and stretched to achieve the desired diameter and thickness. This process enhances the mechanical properties of the pipe.
- Cooling and Cutting: The pipe is cooled, and its length is cut into standard sizes. The resulting seamless pipe is ready for further processing or use.
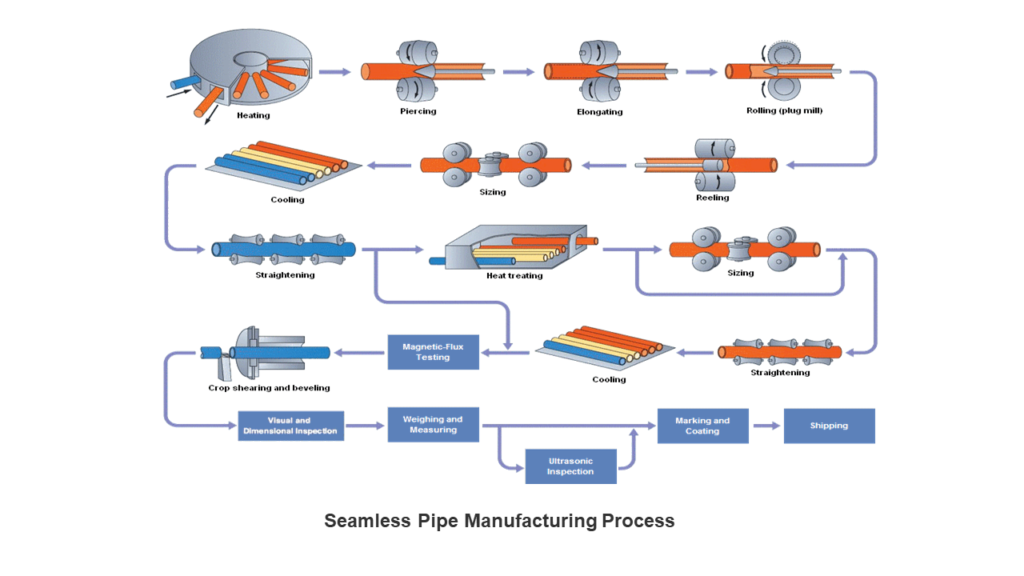
Similar Articles related to Pipe
Topic | Weblink | Topic | Weblink |
---|---|---|---|
Pipe Insulation Materials | Link | ASME B36.10 | Link |
Piping Codes & Standards | Link | Non-Metallic Pipes | Link |
Pressure-Temperature Ratings | Link | Pipe Standards & Specifications | Link |
Pipes for Different Fluids | Link | Pipe Coatings & Linings | Link |
Pipe Materials Selection Guidelines | Link | Corrosion & Pipe Protection | Link |
High-Temperature Pipes | Link | Pipe Dimensions & Sizes | Link |
Pipe Manufacturing Processes | Link | Types of Pipes in Piping Systems | Link |
Pipe Thickness Calculations | Link | Pipe Inspection & Testing | Link |
Cold Drawing Process
- Preparation of Raw Materials: Similar to the hot rolling process, high-quality steel billets are selected for the cold drawing process.
- Cold Drawing and Pilgering: The billet is pulled through a series of dies to reduce its diameter and achieve the desired shape. Pilgering, a specialized cold rolling process, further enhances the pipe’s surface finish and dimensional accuracy.
- Annealing and Surface Treatment: The cold-drawn pipe undergoes an annealing process to relieve stress and improve its mechanical properties. Surface treatment methods like pickling or passivation are applied to enhance corrosion resistance.
Advantages and Limitations of Seamless Pipes
Seamless pipes offer several advantages, including high strength, uniformity, and suitability for high-pressure applications. However, their manufacturing is resource-intensive, leading to higher costs. Additionally, their size range is somewhat limited compared to welded pipes.
Do not miss the detailed course on What is Pipe II Schedule II Plastic II Jacketed II Tracing
Enrollment Link
Welded Pipe Manufacturing
Introduction to Welded Pipes
Welded pipes are constructed by joining two edges of a steel strip or plate. They are widely used for various applications and come in different forms, including electric resistance welding (ERW), submerged arc welding (SAW), and high-frequency welding (HFW).
Electric Resistance Welding (ERW)
- Formation of the Strip: A steel strip is uncoiled and fed through a series of rollers to form a continuous strip. The edges of the strip are then prepared for welding.
- Welding Process: The prepared edges are heated using electric resistance, and they are fused together to create a longitudinal seam.
- Sizing and Cutting: The welded pipe passes through sizing rollers to achieve the desired dimensions. The pipe is then cut to the required length.
Submerged Arc Welding (SAW)
- Process Overview: In SAW, the edges of the steel plate are prepped, and a granular flux is applied. An electrode is then fed continuously, and the welding arc is submerged beneath the flux layer.
- Longitudinal and Spiral SAW: Depending on the application, pipes can be longitudinally or spirally welded. Spiral SAW is often used for larger diameter pipes.
- Post-Weld Treatment: After welding, the pipe undergoes various treatments such as trimming, inspection, and sometimes additional surface coating.
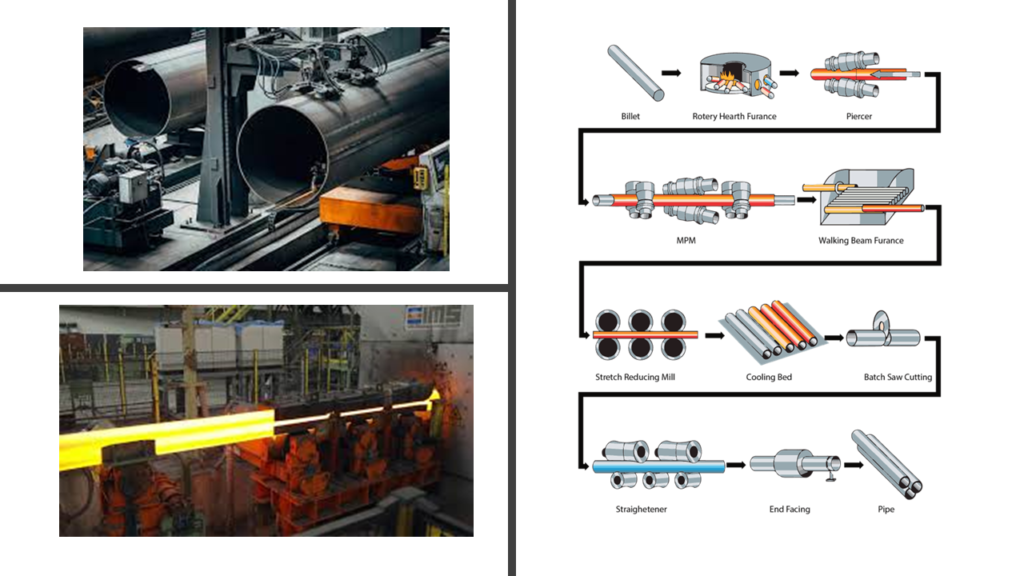
High-Frequency Welding (HFW)
- Principle of HFW: HFW utilizes high-frequency currents to heat the edges of the steel strip, which are then fused together under pressure.
- Welding Process Steps: The strip edges are heated, squeezed, and welded by the high-frequency current. The pipe is then cooled and further processed.
Advantages and Limitations of Welded Pipes
Welded pipes are more cost-effective than seamless pipes and offer a wider range of sizes. However, their welds can be potential weak points, especially in corrosive environments. Proper welding techniques and quality control are crucial to ensure the durability of welded pipes.
Do not miss the detailed course on What is Pipe II Schedule II Plastic II Jacketed II Tracing
Enrollment Link
Pipe Coating and Finishing
Importance of Coating and Finishing
Coating and finishing processes are essential to enhance the longevity and performance of pipes. They protect against corrosion, abrasion, and chemical exposure, especially in harsh operating conditions.
Types of Pipe Coatings
- External Coatings: Fusion-bonded epoxy (FBE), polyethylene, and polypropylene coatings provide protection against external factors and corrosion.
- Internal Coatings: Epoxy and cement mortar coatings are used to prevent internal corrosion and facilitate smooth fluid transport.
Surface Finishing Techniques
- Shot Blasting: This process cleans and prepares the pipe’s surface for coating by removing impurities and creating a textured surface.
- Galvanization: Pipes are coated with a layer of zinc to provide corrosion resistance. This process is commonly used for smaller pipes.
- Passivation and Pickling: Acid treatments are applied to remove impurities and oxides from the pipe’s surface, enhancing its corrosion resistance.
Quality Control and Inspection
Stringent quality control measures are implemented throughout the coating and finishing processes to ensure the effectiveness and longevity of the coatings. Inspection techniques such as visual examination, thickness measurement, and adhesion testing are carried out to identify any defects.
Emerging Technologies in Pipe Manufacturing
3D Printing of Pipes
- Additive Manufacturing Process: 3D printing, or additive manufacturing, is gaining traction in pipe manufacturing. It involves layer-by-layer deposition of material to create complex structures.
- Materials and Applications: 3D printing enables the production of customized and intricate pipe designs using various materials, including metals and polymers.
Advanced Welding Techniques
- Laser Welding: Laser welding offers high precision and minimal heat-affected zones, making it suitable for thin-walled pipes and critical applications.
- Hybrid Welding: Combining different welding techniques, such as laser and arc welding, results in improved weld quality and efficiency.
Automation and Robotics in Manufacturing
- Robotics for Handling and Inspection: Robots are increasingly used for material handling, welding, and quality control, ensuring consistent and precise manufacturing.
- AI-Driven Quality Control: Artificial intelligence is being integrated into manufacturing processes to identify defects, optimize welding parameters, and enhance overall quality.
Environmental Considerations
Energy Consumption and Carbon Footprint
Pipe manufacturing processes can be energy-intensive, contributing to carbon emissions. Energy-efficient technologies and sustainable practices are being adopted to reduce the environmental impact.
Efforts to Reduce Environmental Impact
- Efficient Manufacturing Processes: Improving process efficiency and reducing waste generation can significantly lower energy consumption and environmental footprint.
- Recycling and Reuse of Materials: Recycling steel and other materials used in pipe manufacturing reduces the need for virgin resources and minimizes waste.
Do not miss the detailed course on What is Pipe II Schedule II Plastic II Jacketed II Tracing
Enrollment Link
Case Studies and Industry Applications
- Oil and Gas Industry: Pipes are vital for transporting oil, gas
, and other fluids across long distances. Corrosion-resistant coatings are crucial to withstand harsh conditions.
- Construction and Infrastructure: Pipes are used in building structures, sewage systems, and water supply networks. Quality and durability are key factors in these applications.
- Water and Wastewater Management: Pipes play a vital role in supplying clean water and managing wastewater. Internal coatings prevent contamination and corrosion.
- Automotive and Transportation: Pipes are essential components in vehicle exhaust systems and fuel lines, demanding precise manufacturing and corrosion resistance.
Future Trends and Challenges
Sustainability and Green Manufacturing
Manufacturers are exploring ways to reduce energy consumption, minimize waste, and adopt more sustainable materials, contributing to greener pipe manufacturing.
Integration of IoT and Industry 4.0
The Internet of Things (IoT) and Industry 4.0 concepts are being integrated to enable real-time monitoring, predictive maintenance, and data-driven process optimization.
Addressing Quality and Safety Standards
Maintaining high quality and safety standards is essential to ensure the reliability and performance of pipes. Stricter regulations and industry standards drive continuous improvement.
Conclusion
Pipes are the lifelines of modern infrastructure, serving critical functions in various industries. Understanding the intricacies of different manufacturing processes, coatings, and finishing techniques is essential for producing durable and reliable pipes. As the industry evolves, adopting emerging technologies and sustainable practices will shape the future of pipe manufacturing, addressing challenges and meeting the needs of a rapidly changing world.
frequently asked questions (FAQs) about pipe manufacturing processes along with their answers:
Q1: What are the main differences between seamless and welded pipes? A1: Seamless pipes are manufactured without any welded seams and are generally stronger, suitable for high-pressure applications. Welded pipes, on the other hand, are made by joining two edges of a steel strip or plate. While welded pipes are more cost-effective and versatile in terms of size, the welds can be potential weak points, especially in corrosive environments.
Q2: How are pipes coated to protect against corrosion? A2: Pipes are coated using various methods to protect them from corrosion. External coatings, such as fusion-bonded epoxy (FBE) and polyethylene, shield pipes from environmental factors. Internal coatings, like epoxy and cement mortar, are applied to prevent corrosion inside the pipes and ensure smooth fluid transport.
Q3: What emerging technologies are impacting pipe manufacturing? A3: Emerging technologies include 3D printing, where pipes can be produced with intricate designs using layer-by-layer deposition. Advanced welding techniques like laser welding and hybrid welding offer higher precision and efficiency. Additionally, automation and robotics are used for handling, welding, and quality control, enhancing manufacturing consistency.
Q4: How is sustainability being addressed in pipe manufacturing? A4: Sustainability efforts in pipe manufacturing involve energy-efficient processes, reduced waste generation, and the use of recycled materials. Greener manufacturing practices contribute to lower carbon emissions and reduced environmental impact.
Q5: What industries rely heavily on pipes, and why are they crucial? A5: Industries such as oil and gas, construction, water management, and transportation heavily rely on pipes. Pipes are essential for transporting fluids, gases, and solids across long distances, building infrastructure, managing water supply, and facilitating vehicle systems. The quality and durability of pipes directly impact the efficiency and safety of these industries.
Recommended courses (Published on EPCLand)
- Basics of Piping Engineering
- Piping Layout Engineering
- Piping Material Engineering
- Piping Stress Analysis
- Complete Course on Piping Engineering
- Material Requisitions
- Piping Material Specifications
- Valve Material Specifications
Don’t miss the published articles on following:
Related Video
Attempt Quiz
Question 1:
Which pipe manufacturing process involves heating a flat steel plate and forming it into a cylindrical shape?
Explanation: The Welded Pipe Process involves heating a flat steel plate and forming it into a cylindrical shape, followed by welding the seam.
Question 2:
Which pipe manufacturing process involves forcing a heated billet through a mandrel to create a hollow tube?
Explanation: The Seamless Pipe Process involves forcing a heated billet through a mandrel to create a hollow tube without any welding.
Question 3:
Which pipe manufacturing process uses an electric current to melt the edges of a steel strip and form a welded seam?
Explanation: The ERW (Electric Resistance Welding) Process uses an electric current to melt the edges of a steel strip and form a welded seam.
Question 4:
Which pipe manufacturing process involves forcing molten metal through a die to create a pipe with a specific shape?
Explanation: The Extrusion Process involves forcing molten metal through a die to create a pipe with a specific shape and dimensions.
Question 5:
Which type of pipe is typically produced using the Seamless Pipe Process?
Explanation: The Seamless Pipe Process is often used to produce large-diameter pipes with a smooth interior and exterior surface.