Introduction
In the complex world of the oil and gas industry, ensuring the integrity of piping systems is paramount. A critical component of this integrity is the proper preparation and facing of flanges. Piping flange facing, often an overlooked but essential step, plays a crucial role in preventing leaks, ensuring safety, and maintaining the efficiency of oil and gas operations. This article delves into the world of piping flange facing, exploring its history, functions, working principles, different types, applications, advantages, disadvantages, and the associated codes and standards that govern its use in oil and gas industry projects.
Table of Contents
Don’t miss the Complete Course on Piping Engineering: Check Now
Enrollment Link
Brief History
Flanges have been an integral part of piping systems for centuries. They were initially used in water supply and irrigation systems in ancient civilizations. The concept of facing flanges, however, has evolved over time. Early flanges were simple, and their facing was often a matter of practicality rather than precision. As industries like oil and gas emerged, the need for more sophisticated flange facing became apparent. Today, the history of flange facing is intertwined with the history of industrialization and the development of modern engineering practices.
Basic Function and Working Principle
Function of Piping Flange Facing
The primary function of flange facing is to ensure a leak-tight seal between two flanged pipe components. Flange facing achieves this by providing a smooth, flat, and even sealing surface. When flanges are bolted together, the mating surfaces must align perfectly to prevent leakage of fluids or gases under pressure.
Working Principle
Flange facing is achieved through machining processes that create precise surfaces on flange contact areas. The key working principles of flange facing are:
- Surface Flatness: Flange facing machines use cutting tools to remove imperfections and irregularities from the flange surface, ensuring it is perfectly flat.
- Surface Finish: Flange facing also focuses on achieving the desired surface finish, often measured in terms of roughness average (Ra). A smoother surface finish enhances sealing capabilities.
- Alignment: Proper alignment of the flange facing machine is crucial to ensure that the facing process results in a flat and parallel surface.
Types of Piping Flange Facing
Several methods and techniques are used to achieve the required flange facing. The choice of method depends on factors like the type of flange, its size, and the specific requirements of the project. Common types of flange facing include:
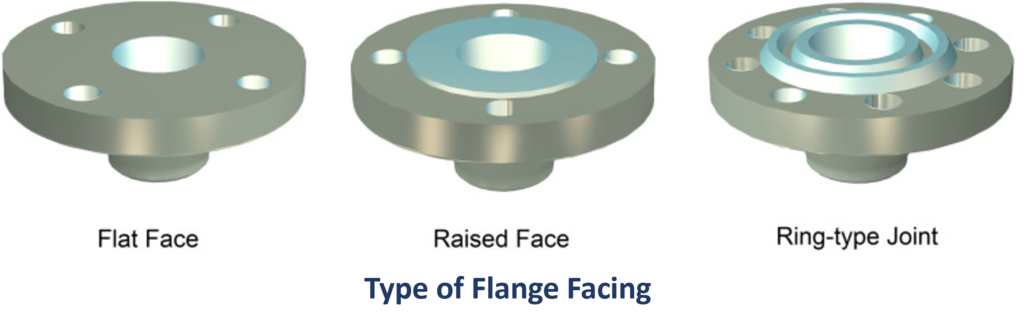
1. Raised Face (RF):
Description: Raised face flanges are among the most commonly used types in the oil and gas industry. They feature a small raised ring on their facing, which provides a contact point for the gasket.
Applications:
- Raised face flanges are typically used in low-pressure and low-temperature applications.
- They are commonly found in industries where sealing requirements are not as stringent.
Advantages:
- Simplicity: RF flanges have a straightforward design, making them easy to handle and install.
- Cost-Effective: Due to their uncomplicated design, RF flanges are often more budget-friendly compared to other types.
- Gasket Compatibility: RF flanges work well with soft gaskets, such as those made of rubber or non-metallic materials.
Disadvantages:
- Limited Pressure Rating: They may not be suitable for high-pressure applications due to their raised face design.
- Sealing Limitations: The raised face can limit the types of gaskets that can be used, which may impact their suitability for specific fluids or gases.
2. Ring Type Joint (RTJ):
Description: RTJ flanges are designed with a groove in their facing to accommodate a metal ring gasket. This groove provides a secure location for the gasket to sit, ensuring a reliable seal.
Applications:
- RTJ flanges are the preferred choice for high-pressure and high-temperature applications.
- They are commonly used in wellhead equipment in the oil and gas industry.
Advantages:
- Superior Sealing: RTJ flanges offer excellent sealing capabilities, even under extreme conditions.
- High Pressure-Temperature Rating: They are well-suited for applications where pressure and temperature are exceptionally high.
- Durability: RTJ flanges are known for their durability and resistance to wear and tear.
Disadvantages:
- Complex Design: The groove and ring gasket design can be more intricate, requiring specialized machining and handling.
- Higher Cost: The precision required in manufacturing RTJ flanges, along with the metal ring gasket, can make them more expensive than other types.
3. Flat Face (FF):
Description: Flat face flanges have a smooth, flat facing surface without any raised features or grooves.
Applications:
- Flat face flanges are suitable for low-pressure and non-corrosive applications.
- They are commonly used in industries where pressure requirements are not demanding.
Advantages:
- Easy to Machine: The simplicity of the flat face design makes them easy to machine and prepare.
- Cost-Effective: FF flanges are typically more cost-effective due to their uncomplicated design.
- Compatibility: They can work well with a wide range of gasket materials, allowing for flexibility in gasket selection.
Disadvantages:
- Limited Sealing: Flat face flanges may not provide the same level of sealing performance as RTJ flanges, making them less suitable for high-pressure or critical applications.
- Surface Finish Control: Achieving the desired surface finish can be challenging in some cases, impacting their sealing efficiency.
Each type of flange facing method has its unique characteristics, making it suitable for specific applications within the oil and gas industry. The choice of flange facing type depends on factors such as pressure, temperature, fluid type, and project requirements, ensuring that the proper sealing integrity is maintained while balancing cost-effectiveness and practicality.
Application of Piping Flange Facing
Flange facing is a critical process in the oil and gas industry, with a wide range of applications that contribute to the integrity, safety, and efficiency of piping systems. Properly faced flanges play a pivotal role in ensuring leak-tight connections, reducing the risk of hazardous material releases, and maintaining operational efficiency. Below, we explore in detail the various applications of piping flange facing in oil and gas industry projects.
1. Pipeline Construction
Role:
- Flange facing is an essential step in the construction of pipelines, where numerous segments of pipes need to be connected securely to form a continuous network.
Importance:
- Ensures leak-tight connections between pipeline segments, preventing fluid or gas leaks into the environment.
- Minimizes the risk of contamination, especially when transporting hazardous or corrosive substances.
- Maintains the structural integrity of the pipeline, preventing leaks that could lead to soil erosion and land subsidence.
2. Oil Refineries
Role:
- In oil refineries, flanges and their precise facing are crucial in the assembly of various equipment, including pumps, valves, heat exchangers, and reactors.
Importance:
- Prevents leaks in high-pressure and high-temperature processes, ensuring the safety of personnel and equipment.
- Enhances operational safety by maintaining the integrity of the refining process.
- Helps maintain product quality by preventing contamination or mixing of different streams in the refining process.
3. Gas Processing Plants
Role:
- Gas processing plants require flange facing for connecting various processing equipment, such as compressors, separators, and fractionating columns.
Importance:
- Ensures safe and efficient operation of equipment by preventing gas leaks, which could lead to fires or explosions.
- Minimizes emissions of greenhouse gases and volatile organic compounds (VOCs) by maintaining tight seals.
- Protects the environment by preventing leaks of potentially harmful substances.
4. Petrochemical Industry
Role:
- Flange facing is widely used in the petrochemical industry for connecting equipment such as reactor vessels, storage tanks, and distillation columns.
Importance:
- Prevents leaks in critical processes, ensuring the safety of personnel and assets.
- Reduces the risk of chemical spills, which can have severe environmental and safety consequences.
- Maintains product quality by preventing contamination or mixing of different chemical compounds.
5. Offshore Drilling Platforms
Role:
- Flange facing is a crucial part of offshore drilling operations, where the marine environment places additional demands on equipment reliability.
Importance:
- Prevents leaks in a challenging offshore environment where containment of oil and gas is critical.
- Enhances safety by reducing the risk of equipment failure and leaks in remote locations.
- Minimizes environmental impact by preventing spills in sensitive marine ecosystems.
6. Chemical Plants
Role:
- Chemical plants rely on flange facing to connect various vessels, reactors, and pipelines in the production of chemicals.
Importance:
- Prevents chemical leaks, which can be hazardous to both personnel and the environment.
- Maintains the purity and quality of chemical products by preventing contamination.
- Ensures the safe operation of chemical processes by minimizing the risk of equipment failure.
7. Power Generation Facilities
Role:
- Flange facing is essential in power generation facilities where various equipment, including boilers, turbines, and pumps, require secure connections.
Importance:
- Prevents leaks in high-pressure and high-temperature steam and gas systems, ensuring the safety of power plant operations.
- Maintains the efficiency of power generation processes by preventing energy losses through leaks.
- Reduces the risk of equipment failure, which can lead to costly downtime and repairs.
8. Mining Operations
Role:
- In mining operations, flange facing is used in various equipment, such as slurry pumps, crushers, and conveyors.
Importance:
- Prevents leaks of abrasive and corrosive materials, which can cause equipment wear and damage.
- Enhances the safety of mining operations by reducing the risk of material spills.
- Minimizes equipment maintenance and downtime, improving overall productivity.
Don’t miss the Complete Course on Piping Engineering: Check Now
Enrollment Link
Advantages & Disadvantages
Piping flange facing offers several advantages and some disadvantages that are crucial to consider in oil and gas industry projects:
Advantages of Piping Flange Facing
Advantages | Description |
---|---|
Leak Prevention | Properly faced flanges prevent leaks, ensuring safety and environmental compliance. |
Sealing Efficiency | Achieves a tight and reliable seal, critical in high-pressure and high-temperature applications. |
Enhanced Safety | Reduces the risk of hazardous material releases and accidents. |
Longevity | Extends the service life of piping systems by reducing wear and tear on gaskets. |
Improved Efficiency | Maintains process efficiency by preventing leaks and pressure drops. |
Disadvantages of Piping Flange Facing
Disadvantages | Description |
---|---|
Cost | The precision machining required for flange facing can be expensive. |
Complexity (RTJ) | Ring type joint (RTJ) flanges are more complex to face and install. |
Surface Finish Control | Achieving the desired surface finish can be challenging in some cases. |
Associated Codes & Standards
The oil and gas industry adheres to specific codes and standards that govern the use of flange facing techniques and equipment. These codes and standards are essential to ensuring the safety and reliability of piping systems. Some of the notable standards include:
1. ASME B16.5
- Description: This standard specifies the dimensions, tolerances, and markings for pipe flanges and flanged fittings.
- Applicability: Widely used in oil and gas industry projects for designing and fabricating flanges.
2. API 6A
- Description: API 6A outlines the specifications for wellhead and Christmas tree equipment, which includes flanges used in upstream oil and gas operations.
- Applicability: Relevant for flanges used in drilling and production applications.
3. ASME B31 Series
- Description: The ASME B31 series of codes and standards cover various aspects of piping systems, including installation and maintenance.
- Applicability: Provides guidance on flange facing and installation procedures.
Conclusion
In oil and gas industry projects, the significance of piping flange facing cannot be overstated. It is a critical step in ensuring the integrity, safety, and efficiency of piping systems. Properly faced flanges prevent leaks, minimize environmental impact, and contribute to the overall success of oil and gas operations. As technology continues to advance, the methods and techniques used for flange facing will continue to evolve, but the fundamental principles of achieving leak-tight seals will remain at the core of this crucial process.
Projects”:
1. What is flange facing, and why is it important in the oil and gas industry?
- Flange facing is the process of machining and preparing the contact surfaces of flanges to ensure a leak-tight seal when two flanged pipe components are bolted together. It is crucial in the oil and gas industry to prevent leaks, ensure safety, and maintain the efficiency of piping systems.
2. What are the different types of flange facing, and how do they differ in their applications?
- There are three common types of flange facing: Raised Face (RF), Ring Type Joint (RTJ), and Flat Face (FF). RF is used in low-pressure applications, RTJ is suitable for high-pressure and high-temperature environments, and FF is employed in low-pressure and non-corrosive applications.
3. What are the advantages of proper flange facing in oil and gas projects?
- Proper flange facing offers several advantages, including leak prevention, sealing efficiency, enhanced safety, longevity of piping systems, and improved operational efficiency by maintaining process integrity.
4. Are there any disadvantages or challenges associated with flange facing in the industry?
- Flange facing can be costly due to the precision machining required. RTJ flanges are more complex to face and install, and achieving the desired surface finish can be challenging in some cases.
5. Which industry standards and codes govern the use of flange facing techniques and equipment in oil and gas projects?
- Flange facing in the oil and gas industry is regulated by standards such as ASME B16.5, API 6A, and the ASME B31 series. These standards specify dimensions, tolerances, and procedures for designing, fabricating, and installing flanges in various applications.
Recommended courses (Published on EPCLand)
- Basics of Piping Engineering
- Piping Layout Engineering
- Piping Material Engineering
- Piping Stress Analysis
- Complete Course on Piping Engineering
- Material Requisitions
- Piping Material Specifications
- Valve Material Specifications
Don’t miss the published articles on following:
Don’t miss the Complete Course on Piping Engineering: Check Now
Enrollment Link
Attempt Quiz
Question 1:
What is the primary purpose of flange facing in the Oil & Gas Industry?
Explanation: Flange facing in the Oil & Gas Industry primarily serves to improve flange sealing and integrity.
Question 2:
Which type of flange facing surface finish is commonly used to achieve a tight seal in piping flanges?
Explanation: A serrated finish is commonly used to achieve a tight seal in piping flanges.
Question 3:
What is the purpose of a raised face on a flange in the Oil & Gas Industry?
Explanation: The raised face on a flange serves the purpose of providing a sealing surface in the Oil & Gas Industry.
Question 4:
What type of material is commonly used for flange facing in corrosive environments?
Explanation: Stainless Steel is commonly used for flange facing in corrosive environments.
Question 5:
Which flange facing type is preferred for high-pressure applications in the Oil & Gas Industry?
Explanation: Ring-type joint (RTJ) flange facing type is preferred for high-pressure applications in the Oil & Gas Industry.
Question 6:
What is the purpose of flange facing on pipe joints in the Oil & Gas Industry?
Explanation: Flange facing on pipe joints in the Oil & Gas Industry ensures proper alignment and sealing.
Question 7:
Which standard governs the dimensions and tolerances for flange facing in the Oil & Gas Industry?
Explanation: ASME B16.5 governs the dimensions and tolerances for flange facing in the Oil & Gas Industry.
Question 8:
What is the primary advantage of using a serrated flange facing?
Explanation: The primary advantage of using a serrated flange facing is improved grip and sealing.
Question 9:
Which flange facing type is often used in applications where flanges need to be easily disassembled and reassembled?
Explanation: The grooved finish is often used in applications where flanges need to be easily disassembled and reassembled.
Question 10:
What is the typical surface roughness (Ra) value for flange facing in oil & gas applications?
Explanation: The typical surface roughness (Ra) value for flange facing in oil & gas applications is 3.2 to 6.3 micrometers.