Introduction to Tube-in-Tube Heat Exchangers
Heat exchangers play a vital role in various industries, facilitating the transfer of heat between two fluids while keeping them physically separate. Among the numerous types of heat exchangers, the tube-in-tube heat exchanger stands out for its unique design and efficient heat transfer capabilities. This article delves into the intricacies of tube-in-tube heat exchangers, exploring their operating principles, design considerations, applications, advantages, limitations, and future trends.
Table of Contents
Similar Articles on other Exchangers
Heat Exchanger Type | Check Article Link |
---|---|
Helical Coil Heat Exchanger | Link |
Tube-in-Tube Heat Exchanger | Link |
Spiral Heat Exchanger | Link |
U-Tube Heat Exchanger | Link |
Shell and Tube Heat Exchanger | Link |
Plate Heat Exchanger | Link |
Double Pipe Heat Exchanger | Link |
Finned Tube Heat Exchanger | Link |
Operating Principles of Tube-in-Tube Heat Exchangers
Tube-in-tube heat exchangers operate on the fundamental principles of fluid dynamics and heat transfer. These heat exchangers consist of two concentric tubes: an inner tube through which one fluid flows, and an outer tube (annulus) through which the second fluid flows. The heat transfer occurs primarily through convection, conduction, and sometimes radiation.
The configuration of the tube-in-tube heat exchanger can be either counterflow or parallel flow. In counterflow, the two fluids flow in opposite directions, maximizing the temperature difference between them and thus enhancing heat transfer efficiency. Parallel flow, on the other hand, involves the fluids flowing in the same direction, allowing for more efficient temperature equalization.
To further enhance heat transfer, various techniques are employed, such as introducing turbulence promoters within the annulus or using inserts like twisted tape. These mechanisms disrupt laminar flow, promoting better heat exchange between the fluids.
Don’t miss the Detailed course on Drums/Exchanger Piping Layout & Stress Analysis
Enrollment Link
Design and Construction
Tube-in-tube heat exchangers comprise several key components, each contributing to their overall functionality and efficiency. The inner and outer tubes are typically made of materials compatible with the fluids being processed, considering factors like chemical compatibility and thermal conductivity. Headers and connections facilitate the entry and exit of fluids, while the shell and casing provide structural integrity and support.
Choosing the right materials is crucial, especially when dealing with corrosive or high-temperature fluids. The sizing and geometry of the heat exchanger are determined based on the required heat transfer area and flow rates. The arrangement of the tubes and their pitch affect the overall heat transfer characteristics.
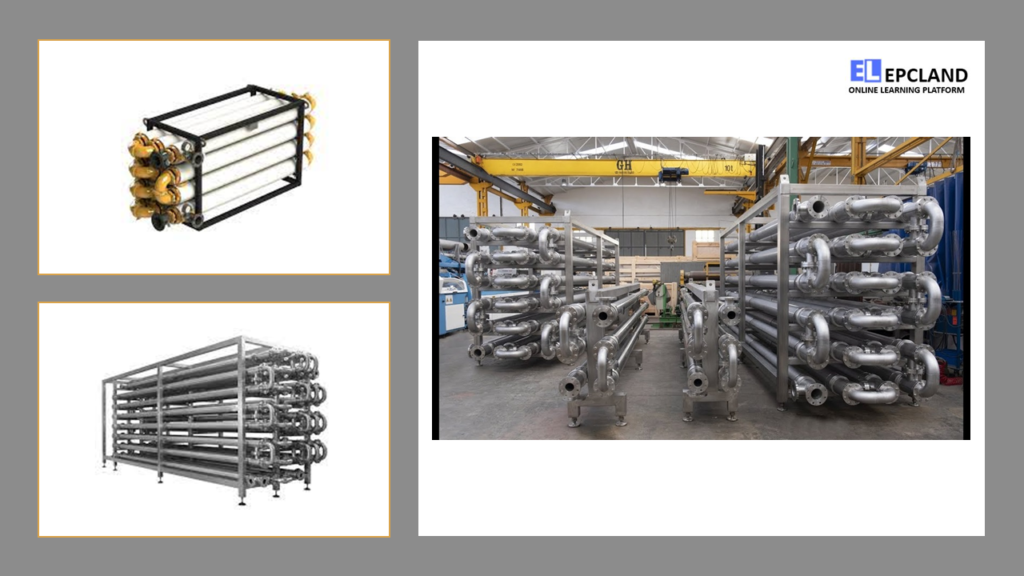
Applications of Tube-in-Tube Heat Exchangers
Tube-in-tube heat exchangers find applications across a wide range of industries. In the chemical industry, they are used for cooling, condensation, and heating processes. Their ability to handle high pressures makes them suitable for critical chemical reactions. In the food and beverage industry, tube-in-tube heat exchangers are employed for pasteurization, sterilization, and maintaining the temperature of viscous fluids.
HVAC systems benefit from these heat exchangers by enabling heat recovery, enhancing energy efficiency, and maintaining indoor air quality. Additionally, tube-in-tube heat exchangers are integrated into renewable energy systems like geothermal heat pumps and solar water heaters, where they play a crucial role in harnessing and transferring thermal energy.
Don’t miss the Detailed course on Drums/Exchanger Piping Layout & Stress Analysis
Enrollment Link
Advantages of Tube-in-Tube Heat Exchangers
The tube-in-tube design offers several advantages that contribute to their widespread use. Efficient heat transfer is a key benefit due to the large surface area available for heat exchange. This design also lends itself to compact configurations, making them suitable for applications with space constraints. The separation of fluids within the tubes minimizes the risk of cross-contamination, which is particularly important in industries like pharmaceuticals and food processing. Moreover, tube-in-tube heat exchangers are versatile and can handle various types of fluids, including liquids, gases, and even multiphase mixtures.
Limitations and Challenges
While tube-in-tube heat exchangers offer numerous benefits, they are not without limitations. One notable challenge is the potential for fouling, where deposits accumulate on the heat exchanger surfaces, reducing heat transfer efficiency. Pressure drop is another concern, especially when dealing with high-viscosity fluids or intricate designs. Cleaning and maintenance of tube-in-tube heat exchangers can be complex, requiring careful consideration of cleaning methods and intervals. Additionally, these heat exchangers are generally limited to specific temperature and pressure ranges, which may restrict their use in certain applications.
Case Studies and Real-world Examples
Several case studies highlight the practical applications of tube-in-tube heat exchangers. In chemical processing, these heat exchangers are used for cooling and condensation of reactive gases, ensuring safe and efficient reactions. In HVAC systems, tube-in-tube heat exchangers enable heat recovery from exhaust air, reducing energy consumption in buildings. Moreover, tube-in-tube heat exchangers are integral components of solar water heating systems, efficiently transferring heat from solar collectors to the water supply.
Performance Evaluation and Optimization
Assessing the performance of tube-in-tube heat exchangers involves evaluating metrics like the overall heat transfer coefficient (U-value) and effectiveness. Computational fluid dynamics (CFD) simulations provide insights into fluid flow patterns and heat transfer efficiency, aiding in design optimization. Techniques such as varying tube geometries or introducing enhanced surfaces can further improve the performance of tube-in-tube heat exchangers.
Maintenance and Cleaning Strategies
Addressing fouling challenges is essential for maintaining the efficiency of tube-in-tube heat exchangers. Mechanical cleaning methods, such as brushes or high-pressure water jets, can remove deposits from tube surfaces. Chemical cleaning agents can also be employed, but compatibility with materials and environmental considerations are crucial. Regular maintenance practices, including inspection and cleaning schedules, help prevent significant efficiency losses. Implementing monitoring systems allows for early detection of performance degradation or fouling issues.
Future Trends and Innovations
The future of tube-in-tube heat exchangers holds promising advancements. Innovations in materials, such as the use of high-performance alloys and ceramics, will enhance corrosion resistance and durability. Integration with smart and IoT technologies will enable real-time monitoring, predictive maintenance, and optimization. Miniaturization of heat exchangers could lead to micro-scale devices with applications in electronics cooling and medical devices.
Pros & Cons
Pros | Cons |
---|---|
Efficient heat transfer due to large area | Potential for fouling and reduced efficiency |
Compact design saves space | Pressure drop concerns in complex designs |
Reduced risk of cross-contamination | Complex maintenance and cleaning requirements |
Versatile for various fluid types | Limited temperature and pressure ranges |
Suitable for high-pressure applications | Higher initial costs compared to some designs |
Enables efficient heat recovery | |
Compatible with a wide range of fluids |
Remember that the suitability of tube-in-tube heat exchangers depends on the specific application and the trade-offs that need to be considered based on the pros and cons listed above.
Don’t miss the Detailed course on Drums/Exchanger Piping Layout & Stress Analysis
Enrollment Link
Codes & Standards
Codes and Standards | Description |
---|---|
ASME Boiler and Pressure Vessel Code | Comprehensive standard for the design, fabrication, and inspection of boilers, pressure vessels, and related equipment. |
ASME B16.9 | Standard for factory-made wrought steel butt-welding fittings. |
ASME B31.1 | Code for pressure piping systems used in power plants and industrial facilities. |
API 660 | Standard for the design, materials, fabrication, inspection, and testing of air-cooled heat exchangers. |
TEMA | Tubular Exchanger Manufacturers Association standards for shell-and-tube heat exchangers. |
ISO 15547 | International standard for shell-and-tube heat exchangers. |
ANSI/HI 11.6.6 | Standard for testing of industrial air-cooled heat exchangers. |
ASTM A249 | Standard specification for welded austenitic steel boiler, superheater, heat-exchanger, and condenser tubes. |
ASTM A789/A789M | Standard specification for seamless and welded ferritic/austenitic stainless steel tubing for general service. |
ASTM A214 | Standard specification for electric-resistance-welded carbon steel heat-exchanger and condenser tubes. |
These codes and standards provide guidelines for the design, materials, fabrication, testing, and inspection of tube-in-tube heat exchangers, ensuring their safety, efficiency, and reliability. The specific codes and standards applicable to a particular project may vary depending on factors such as industry, location, and regulatory requirements. Always refer to the latest versions of these codes and standards when designing or working with tube-in-tube heat exchangers.
Comparison with Other Exchangers
Characteristics | Tube-in-Tube Heat Exchangers | Shell-and-Tube Heat Exchangers | Plate Heat Exchangers | Finned Tube Heat Exchangers |
---|---|---|---|---|
Heat Transfer Mechanism | Convection, Conduction | Convection | Convection | Convection, Conduction |
Design Complexity | Moderate | Complex | Simple | Moderate |
Space Efficiency | High | Moderate | High | Moderate |
Cleaning and Maintenance | Complex | Complex | Simple | Moderate |
Fouling Resistance | Moderate | Moderate | High | Moderate |
Pressure Drop | Varies | Moderate to High | Low to Moderate | Varies |
Corrosion Resistance | Material-dependent | Material-dependent | Limited | Material-dependent |
Versatility | Various Fluids | Various Fluids | Limited Fluids | Various Fluids |
Temperature and Pressure Range | Moderate | High | Moderate | Moderate |
Initial Cost | Moderate to High | Moderate to High | Low to Moderate | Moderate to High |
Heat Recovery Potential | High | Moderate to High | Low to Moderate | Moderate |
Applications | Diverse Industries | Chemical, Petrochemical, Power | HVAC, Industrial | HVAC, Industrial |
Please note that the characteristics mentioned above are generalizations and can vary based on specific design configurations, materials used, and operating conditions. The choice of a heat exchanger type should be based on a thorough assessment of the specific requirements and constraints of the application.
Don’t miss the Detailed course on Drums/Exchanger Piping Layout & Stress Analysis
Enrollment Link
Conclusion
Tube-in-tube heat exchangers have proven themselves as versatile and efficient devices for heat transfer across a range of industries. Their unique design, combined with ongoing research and advancements, ensures their continued relevance in addressing complex heat exchange challenges. As industries continue to demand higher efficiency and sustainability, tube-in-tube heat exchangers will remain essential components in the thermal engineering landscape.
FAQs
1. What is a tube-in-tube heat exchanger, and how does it work?
- A tube-in-tube heat exchanger is a type of heat transfer device consisting of two concentric tubes, an inner tube and an outer tube (annulus). One fluid flows through the inner tube, while another fluid flows through the outer annulus. Heat is transferred through the tube walls, facilitating efficient heat exchange between the two fluids.
2. What are the advantages of using tube-in-tube heat exchangers?
- Tube-in-tube heat exchangers offer several advantages, including efficient heat transfer due to their large surface area, space-saving design, reduced risk of cross-contamination between fluids, versatility in handling various fluid types, and suitability for high-pressure applications. They also enable heat recovery and energy efficiency improvements in systems like HVAC and industrial processes.
3. What are the main challenges associated with tube-in-tube heat exchangers?
- One of the main challenges is the potential for fouling, where deposits accumulate on the heat exchanger surfaces and reduce efficiency. Pressure drop concerns can arise in complex designs, and maintenance can be complex due to the need for thorough cleaning of the inner and outer tubes. Additionally, tube-in-tube heat exchangers are limited to specific temperature and pressure ranges, which may restrict their use in certain applications.
4. What industries commonly use tube-in-tube heat exchangers?
- Tube-in-tube heat exchangers find applications in diverse industries. They are used in the chemical industry for processes like cooling, condensation, and heating of reactive gases. In the food and beverage industry, they are employed for pasteurization, sterilization, and temperature control of viscous fluids. HVAC systems utilize these heat exchangers for heat recovery, and they are also integrated into renewable energy systems like geothermal heat pumps and solar water heaters.
5. How are tube-in-tube heat exchangers maintained and cleaned?
- Maintaining tube-in-tube heat exchangers involves addressing fouling issues through regular inspection and cleaning schedules. Mechanical methods, such as brushes or high-pressure water jets, can remove deposits from tube surfaces. Chemical cleaning agents can also be used, but compatibility with materials and environmental considerations are important. Monitoring systems help detect performance degradation or fouling early on, allowing for timely maintenance.
Recommended courses (Published on EPCLand)
- Basics of Piping Engineering
- Piping Layout Engineering
- Piping Material Engineering
- Piping Stress Analysis
- Complete Course on Piping Engineering
- Material Requisitions
- Piping Material Specifications
- Valve Material Specifications
Don’t miss the published articles on following:
Recommended Video
Attempt Quiz
Question 1:
What is a tube-in-tube heat exchanger?
Explanation: A tube-in-tube heat exchanger is a type of heat exchanger where one set of tubes is positioned inside another set of larger tubes. The fluids flow through the inner and outer tubes, allowing for heat transfer between them.
Question 2:
What is a common application of tube-in-tube heat exchangers?
Explanation: Tube-in-tube heat exchangers are commonly used in applications where compactness and efficient heat transfer are required, such as air conditioning systems for both residential and commercial buildings.
Question 3:
What is the advantage of using a tube-in-tube heat exchanger?
Explanation: One of the advantages of tube-in-tube heat exchangers is their ease of cleaning and maintenance. The design allows for easy access to the inner tubes, making it simpler to clean and inspect the heat exchanger.
Question 4:
Which type of fluid arrangement is common in a tube-in-tube heat exchanger?
Explanation: Counterflow is a common fluid arrangement in a tube-in-tube heat exchanger. In counterflow, the hot and cold fluids flow in opposite directions, which maximizes the temperature difference between them and improves heat transfer efficiency.
Question 5:
What material is often used for the tubes in a tube-in-tube heat exchanger?
Explanation: Copper is a commonly used material for the tubes in a tube-in-tube heat exchanger. Copper is known for its excellent thermal conductivity, corrosion resistance, and suitability for heat transfer applications.