1. Introduction
Check valves, also known as non-return valves, are indispensable components in various fluid control systems. Their fundamental role is to allow fluid to flow in one direction while preventing backflow in the opposite direction. This simple yet crucial function finds applications in diverse industries, from plumbing and oil refineries to chemical processing and marine engineering.
Table of Contents
Don’t miss the Complete Course on Piping Engineering: Check Now
Enrollment Link
2. Brief History
The origins of check valves can be traced back centuries. In ancient civilizations, basic check valve mechanisms were employed to manage water flow for irrigation and domestic use. The concept evolved over time, with notable inventors contributing to its development. The earliest designs were rudimentary, but they laid the foundation for the sophisticated valves we use today.
3. Basic Function and Working Principle
Check valves operate on a straightforward principle: fluid flow opens the valve, while backflow closes it. The key components include a flap, hinge, body, and sometimes a spring. When the pressure of the fluid in the forward direction exceeds that of the backflow, the valve opens, allowing the fluid to pass. Once the flow direction reverses, the valve closes, preventing any backflow. This mechanism is vital for maintaining the intended direction of flow in pipelines and various other systems.
4. Main Components
- Flap: The flap is the movable part of the check valve. It opens and closes based on the direction of fluid flow.
- Hinge: The hinge connects the flap to the valve body, allowing it to pivot during operation.
- Body: The body houses the flap and hinge, providing structural support and ensuring proper alignment.
- Spring (in some designs): A spring assists in closing the valve promptly after the flow direction changes, preventing any residual backflow.
Manufacturers carefully select materials for these components based on factors such as fluid type, pressure, and temperature to ensure the valve’s durability and efficiency.
5. Types of Check Valves
- Swing Check Valves: These valves have a flap that swings open and closes on a hinge, allowing unidirectional flow. They find use in a wide range of applications due to their versatility.
- Lift Check Valves: Lift check valves contain a guided disc within the body, moving along the vertical line. They are suitable for applications with variable flow rates.
- Ball Check Valves: Ball check valves use a ball-shaped disc to control flow. When the flow stops or reverses, the ball settles into the seat, sealing the valve.
- Diaphragm Check Valves: These valves use a flexible diaphragm to regulate flow. When the pressure in the inlet exceeds the outlet pressure, the diaphragm flexes, allowing flow.
- Tilting Disc Check Valves: Tilting disc check valves feature a disc that tilts away from the seat when there is forward flow and returns to the seat when the flow reverses.
6. Application of Check Valves
Check valves play a vital role in numerous industries and applications:
- Plumbing Systems: In domestic and commercial plumbing, check valves prevent backflow, ensuring a continuous supply of water without contamination.
- Oil and Gas Industry: Check valves are used in refineries and pipelines, preventing the reverse flow of oil and gas, which is crucial for safety and operational efficiency.
- Chemical Processing: Chemical plants utilize check valves to control the flow of corrosive substances, protecting equipment and ensuring the safety of workers.
- HVAC Systems: Heating, ventilation, and air conditioning systems incorporate check valves to maintain the flow of air or water in one direction, enhancing efficiency.
- Marine Industry: Check valves are essential in marine engineering for seawater intake and discharge, ensuring proper functioning of cooling systems.
7. Relevant Picture
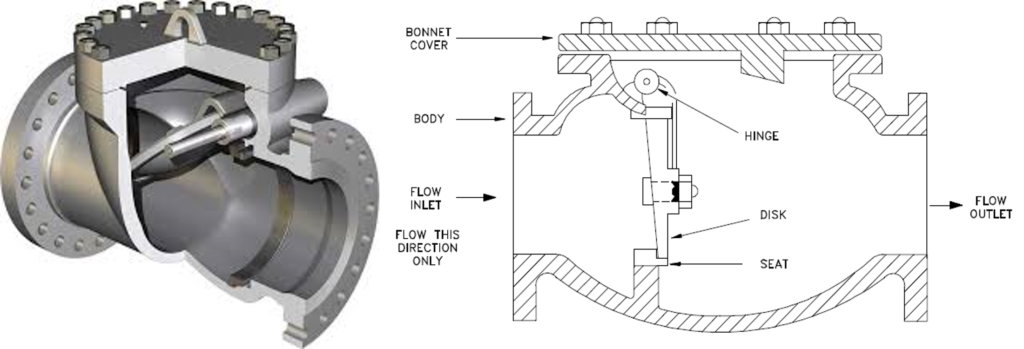
Figure 1: Internal Structure of a Check Valve.
8. Table for Advantages & Disadvantages
Advantages | Disadvantages |
---|---|
Prevents backflow | Limited to specific orientations |
Low maintenance | Pressure drop |
Diverse material options | Noise generation |
Easy installation | Potential leakage |
Suitable for various media | Size and weight constraints |
Check valves offer several advantages, such as preventing backflow and requiring minimal maintenance. However, they come with limitations, including pressure drops and potential leakage issues. The choice of check valve type depends on the specific requirements of the application.
Don’t miss the Complete Course on Piping Engineering: Check Now
Enrollment Link
9. Table for Associated Codes & Standards
Organization | Code/Standard |
---|---|
American Society of Mechanical Engineers (ASME) | ASME B16.34 |
International Organization for Standardization (ISO) | ISO 5208 |
American Petroleum Institute (API) | API 594 |
American Water Works Association (AWWA) | AWWA C508 |
European Committee for Standardization (CEN) | EN 12334 |
Adherence to industry standards ensures the quality and performance of check valves in various applications. These standards provide guidelines for manufacturing, testing, and installation, ensuring the valves’ reliability and safety.
Conclusion
In conclusion, check valves are indispensable components in fluid control systems, ensuring the unidirectional flow of fluids in diverse applications. From their historical origins to modern innovations, check valves have come a long way, evolving into specialized designs catering to specific industry needs. Understanding the working principles and various types of check valves is essential for selecting the right valve for a particular application.
As technology advances, check valves continue to play a vital role in ensuring the efficiency, safety, and reliability of fluid systems across industries. Manufacturers and engineers must consider the specific requirements of each application to choose the most suitable type of check valve, taking into account factors such as fluid type, pressure, temperature, and flow rate.
In the ever-changing landscape of fluid control technologies, check valves remain steadfast, serving as essential components that facilitate the smooth operation of countless systems worldwide.
FAQs
Q1: What is the primary purpose of a check valve? A1: A check valve, also known as a non-return valve, is designed to allow fluid to flow in one direction while preventing backflow in the opposite direction. It ensures unidirectional flow in various fluid control systems.
Q2: How does a check valve work? A2: Check valves operate on a simple principle. When the pressure of the fluid in the forward direction exceeds that of the backflow, the valve opens, allowing the fluid to pass. If the flow direction reverses, the valve closes, preventing any backflow.
Q3: What are the main types of check valves and their applications? A3: There are several types of check valves, including swing check valves, lift check valves, ball check valves, diaphragm check valves, and tilting disc check valves. These valves find applications in plumbing, oil and gas industry, chemical processing, HVAC systems, and marine engineering.
Q4: What are the common issues faced with check valves? A4: Common issues with check valves include potential leakage, noise generation, pressure drops, and limited orientations. Proper selection, installation, and maintenance are essential to mitigate these challenges.
Q5: How do I choose the right check valve for my specific application? A5: Choosing the right check valve involves considering factors such as fluid type, pressure, temperature, flow rate, and the specific requirements of the application. Consulting with experts and adhering to industry standards can help in selecting the most suitable check valve.
Don’t miss the Complete Course on Piping Engineering: Check Now
Enrollment Link
Recommended courses (Published on EPCLand)
- Basics of Piping Engineering
- Piping Layout Engineering
- Piping Material Engineering
- Piping Stress Analysis
- Complete Course on Piping Engineering
- Material Requisitions
- Piping Material Specifications
- Valve Material Specifications
Don’t miss the published articles on following:
Attempt Quiz
Question 1:
What is the primary function of a check valve?
Explanation: A check valve is designed to prevent backflow of fluids, allowing flow in one direction only.
Question 2:
Which type of check valve uses a swinging disc to block reverse flow?
Explanation: A Swing Check Valve uses a swinging disc to block reverse flow when fluid tries to move in the opposite direction.
Question 3:
Which material is commonly used for check valve construction due to its corrosion resistance?
Explanation: Stainless Steel is commonly used for check valve construction due to its excellent corrosion resistance properties.
Question 4:
Which factor determines the cracking pressure of a check valve?
Explanation: The cracking pressure of a check valve is determined by the spring tension or the weight of the disc.
Question 5:
Which application is a tilting disc check valve commonly used for?
Explanation: Tilting disc check valves are commonly used for applications involving slurries and suspended solids due to their ability to handle these types of fluids.
Question 6:
Which type of check valve has a hinged ball that opens and closes based on fluid pressure?
Explanation: A Ball Check Valve has a hinged ball that opens and closes based on fluid pressure, allowing flow in one direction only.
Question 7:
What is the purpose of a spring in a spring-loaded check valve?
Explanation: The spring in a spring-loaded check valve provides a sealing force, ensuring the valve closes properly to prevent backflow.
Question 8:
Which type of check valve operates silently and prevents water hammer?
Explanation: A Silent Check Valve operates silently and prevents water hammer, making it suitable for applications where noise and water hammer are concerns.
Question 9:
Which check valve design is commonly used in vertical flow applications?
Explanation: Lift Check Valves are commonly used in vertical flow applications due to their design, which allows for efficient flow control in vertical pipes.
Question 10:
What is the advantage of a dual-plate check valve over a swing check valve?
Explanation: A dual-plate check valve offers reduced pressure drop compared to a swing check valve, making it advantageous in applications where minimizing flow resistance is essential.