Introduction
Fiber Reinforced Plastic (FRP) pipes are a versatile and durable solution widely used in various industries for transporting fluids. The combination of synthetic fibers and polymer matrix makes FRP pipes an excellent choice for various applications. In this comprehensive guide, we will delve into the world of FRP pipes, covering their history, construction, working principles, types, applications, advantages, disadvantages, relevant standards, and frequently asked questions. By the end of this article, you’ll have a thorough understanding of FRP pipes and their significance in modern engineering.
Table of Contents
Don’t miss the Complete Course on Piping Engineering: Check Now
Enrollment Link
Brief History
Origins of FRP Pipes
The development of FRP pipes can be traced back to the mid-20th century when the aerospace industry sought lightweight yet strong materials for aircraft components. Researchers began experimenting with reinforcing plastic matrices with fibers such as glass and carbon. These innovations led to the birth of Fiber Reinforced Plastics, from which FRP pipes later emerged.
Milestones in the Development of FRP Pipes
- 1950s-1960s: The aerospace industry pioneers the use of FRP composites.
- 1970s-1980s: FRP pipes gain recognition in chemical and industrial applications.
- 1990s-Present: Advancements in manufacturing processes and resin technology result in widespread use of FRP pipes across various industries.
Basic Function and Working Principle
How FRP Pipes Work
FRP pipes are composed of a polymer matrix, typically epoxy or polyester resin, reinforced with fibers. The fibers, which can be glass, carbon, or other materials, provide strength and rigidity to the structure. The polymer matrix imparts corrosion resistance and seals the fibers, ensuring longevity and preventing the ingress of corrosive substances.
FRP pipes operate by conveying various fluids under pressure, offering exceptional resistance to both internal and external corrosion. The polymer matrix effectively shields the fibers, making them suitable for conveying corrosive materials.
Key Features of FRP Material
- Corrosion Resistance: FRP pipes are highly resistant to chemical and environmental corrosion, making them ideal for transporting acids, alkalis, and sewage.
- Lightweight: Their low weight compared to metal pipes simplifies transportation and installation.
- High Strength-to-Weight Ratio: The fibers within the FRP provide significant strength while maintaining a low overall weight.
- Smooth Interior Surface: FRP pipes have a smooth interior surface, which minimizes friction and enhances fluid flow.
Advantages of Using FRP Pipes
FRP pipes offer several advantages, including:
- Corrosion Resistance: They are impervious to chemical corrosion, making them ideal for transporting hazardous materials.
- Lightweight: Easy to handle and install, reducing labor and transportation costs.
- Longevity: Their resistance to degradation ensures a long service life.
- Low Maintenance: Minimal upkeep is required, leading to cost savings.
- Customizability: FRP pipes can be tailored to specific requirements, including size, length, and reinforcements.
Manufacturing Process of FRP Pipes
1. Selection of Materials
The process begins with the selection of the materials, including the choice of synthetic fibers and polymer resins. Commonly used fibers include glass, carbon, and aramid, while polymer resins like epoxy or polyester are chosen for their specific properties, such as corrosion resistance and strength.
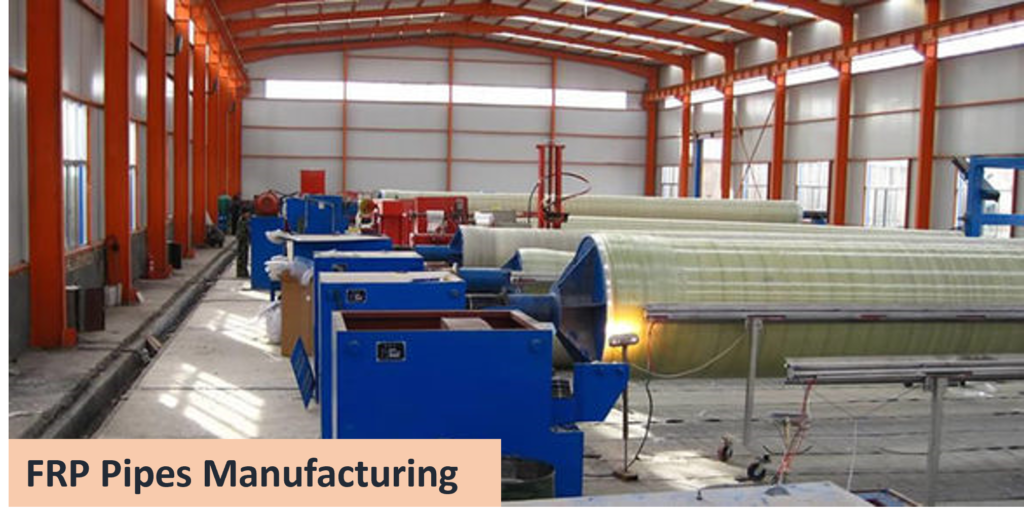
2. Fiber Preparation
The selected fibers are typically in the form of rovings, mats, or fabrics. To prepare them for the manufacturing process, the fibers are cut to the desired length and sometimes coated with sizing agents to improve their adhesion to the resin matrix.
3. Resin Mixing
The polymer resin is prepared by mixing it with additives, catalysts, and curing agents. The specific formulation of the resin depends on the desired properties of the finished FRP pipe, such as corrosion resistance, fire resistance, or strength.
4. Layering or Filament Winding
There are two common methods for forming the pipe structure:
a. Hand Lay-Up Method:
- In this method, layers of resin-saturated fiber mats or fabrics are manually placed into a mold.
- The layers are carefully positioned to achieve the desired thickness and fiber orientation.
- After each layer is placed, it is thoroughly wetted with the resin to ensure proper adhesion.
- The hand lay-up method is suitable for producing small or custom-shaped FRP pipes.
b. Filament Winding:
- Filament winding is an automated process in which fibers are wound continuously onto a rotating mandrel or mold.
- As the fibers are wound, they are impregnated with resin to ensure proper bonding.
- This method is ideal for producing pipes with a consistent and uniform wall thickness and is often used for larger-diameter pipes.
5. Curing
Once the layers of fibers and resin are in place, the pipe is allowed to cure. Curing typically occurs at elevated temperatures to promote the polymerization of the resin. The curing process can take several hours, and the temperature and curing time are carefully controlled to achieve the desired properties of the finished pipe.
6. Trimming and Inspection
After curing, the FRP pipe is removed from the mold. Excess material is trimmed, and the pipe is inspected for defects, such as voids, delaminations, or dimensional inaccuracies. Any imperfections are repaired or trimmed as needed.
7. Surface Finish
The external surface of the FRP pipe can be finished as per the requirements. This may involve applying a gel coat or other protective finishes to enhance UV resistance, aesthetics, and surface smoothness.
8. Testing and Quality Control
To ensure the quality and performance of the finished FRP pipe, various tests are conducted. These tests may include hydraulic pressure tests, vacuum tests, and non-destructive examinations to verify the integrity of the pipe structure.
9. Delivery
The completed FRP pipes are packaged and prepared for shipping to their intended destination, where they will be installed and put into service for the intended application.
Don’t miss the Complete Course on Piping Engineering: Check Now
Enrollment Link
Types of FRP Pipes
Different Classifications Based on Density and Applications
FRP pipes come in various types, classified based on their composition, density, and specific applications. The primary types include:
- Glass-Fiber Reinforced Plastic (GRP) Pipes: These pipes are reinforced with glass fibers, offering excellent corrosion resistance. They are commonly used for conveying water, sewage, and chemicals.
- Carbon-Fiber Reinforced Plastic (CFRP) Pipes: CFRP pipes use carbon fibers for reinforcement and are known for their high strength-to-weight ratio. They are used in demanding applications, such as aerospace and automotive industries.
- Aramid-Fiber Reinforced Plastic (AFRP) Pipes: Aramid fibers, known for their high impact resistance, are used to reinforce these pipes. AFRP pipes are suitable for applications where impact resistance is critical.
- Polyester and Epoxy Resin FRP Pipes: The choice of resin affects the overall properties of FRP pipes. Polyester resin provides good chemical resistance, while epoxy resin offers enhanced strength and adhesion.
Key Specifications of FRP Pipes
FRP pipes are manufactured in various sizes and specifications, including:
- Diameter: Ranging from small-diameter pipes used in plumbing to large-diameter pipes for industrial applications.
- Pressure Rating: Different pipes are designed to withstand various levels of internal pressure, depending on the application.
- Reinforcement Material: The type and orientation of the fibers used in the construction.
- End Connections: Options include flanged, threaded, or socketed ends for easy installation.
- Interior Lining: Some FRP pipes may have specific interior linings for added protection or to meet industry requirements.
Notable Variations and Their Uses
- Dual Laminate FRP Pipes: These pipes combine the benefits of FRP with other materials, such as thermoplastics or other composites, to offer enhanced corrosion resistance.
- Abrasion-Resistant FRP Pipes: Designed to withstand abrasive materials, these pipes are used in mining and slurry transport applications.
- Fire-Retardant FRP Pipes: In applications where fire safety is crucial, these pipes incorporate fire-resistant additives in the resin matrix.
Applications of FRP Pipes
Overview of Diverse Industries and Sectors
FRP pipes find applications across a wide range of industries, including:
- Chemical Processing: FRP pipes are used for transporting acids, bases, and corrosive chemicals due to their exceptional corrosion resistance.
- Water and Wastewater Management: They are employed in water treatment plants, sewage systems, and desalination facilities.
- Oil and Gas: FRP pipes are used for transporting crude oil, natural gas, and various petrochemical products.
- Marine and Offshore: Their corrosion resistance makes them ideal for offshore platforms, ships, and marine infrastructure.
- Aerospace: In the aerospace industry, CFRP pipes are used in aircraft fuel systems and hydraulic lines.
- Mining: Abrasion-resistant FRP pipes are employed in the mining industry for transporting abrasive materials.
Real-World Examples and Case Studies
Case Study 1: Water Treatment Plant Upgrade In a water treatment plant upgrade project, GRP pipes were used to replace aging steel pipes. The corrosion-resistant nature of GRP pipes significantly reduced maintenance costs and prolonged the system’s lifespan.
Case Study 2: Chemical Plant Expansion A chemical plant expanded its operations and required a reliable solution for transporting corrosive chemicals. FRP pipes were chosen for their resistance to chemical corrosion, ensuring safety and operational efficiency.
Advantages of FRP Pipes in Various Applications
- Corrosion Resistance: FRP pipes protect against chemical corrosion, reducing the risk of leaks and contamination in sensitive industries.
- Longevity: Their resistance to degradation results in a long service life, reducing replacement costs.
- Versatility: FRP pipes can be tailored to specific applications, meeting a wide range of requirements.
- Low Friction: The smooth interior surface of FRP pipes minimizes friction, enhancing fluid flow and energy efficiency.
- Environmental Benefits: FRP pipes are environmentally friendly, as they do not corrode, reducing the risk of soil or water contamination.
Advantages & Disadvantages
Table: Advantages of FRP Pipes
Advantage | Description |
---|---|
1. Corrosion Resistance | Highly resistant to chemical and environmental corrosion, ideal for transporting acids, alkalis, and sewage. |
2. Lightweight | Easy to handle and install, reducing labor and transportation costs. |
3. Longevity | Resistant to degradation, ensuring a long service life. |
4. Low Maintenance | Minimal upkeep required, leading to cost savings. |
5. Customizability | FRP pipes can be tailored to specific requirements, including size, length, and reinforcements. |
Don’t miss the Complete Course on Piping Engineering: Check Now
Enrollment Link
Table: Disadvantages of FRP Pipes
Disadvantage | Description |
---|---|
1. Limited Temperature Resistance | FRP pipes may not be suitable for high-temperature applications. |
2. Susceptibility to UV Degradation | Without proper UV protection, FRP pipes may degrade when exposed to sunlight. |
3. Installation Challenges | Specialized installation techniques and equipment may be required. |
4. Environmental Concerns | The manufacturing process and disposal of FRP materials may raise environmental questions. |
Associated Codes & Standards
Overview of Industry Standards for FRP Pipes
The use of FRP pipes in various industries is governed by specific standards and codes to ensure safety and performance. Some of the key standards and organizations include:
- ASTM D2996: Standard Specification for Filament-Wound “Fiberglass” (Glass-Fiber-Reinforced Thermosetting-Resin) Pipe.
- AWWA M45: Fiberglass Pipe Design.
- ISO 14692: Petroleum and natural gas industries – Glass-reinforced plastics (GRP) piping – Part 1: Vocabulary, symbols, applications, and materials.
- API 15LR: Specification for Low Pressure Fiberglass Line Pipe.
- NACE SP0169: Control of External Corrosion on Underground or Submerged Metallic Piping Systems.
Conclusion
In conclusion, Fiber Reinforced Plastic (FRP) pipes stand as a testament to the remarkable synergy between engineering innovation and material science. These pipes have evolved from humble beginnings in the aerospace industry to become an essential component of diverse industrial applications. This comprehensive guide has explored the origins, working principles, types, applications, advantages, disadvantages, relevant standards, and answered common questions about FRP pipes.
The inception of FRP pipes in the mid-20th century, driven by the aerospace sector’s need for lightweight yet strong materials, marked the beginning of their remarkable journey. Over the years, FRP pipes have demonstrated their prowess in withstanding the most challenging environments and conveying a multitude of fluids, from corrosive chemicals to potable water.
The core of the FRP pipe’s success lies in its design and composition. The combination of a polymer matrix, often epoxy or polyester resin, and reinforcing fibers, such as glass, carbon, or aramid, provides a unique set of advantages. These pipes are celebrated for their corrosion resistance, light weight, and high strength-to-weight ratio. Their smooth interior surface reduces friction and enhances fluid flow. Furthermore, FRP pipes offer customizability, allowing them to be tailored to specific applications.
The diverse array of applications for FRP pipes underscores their adaptability and reliability. They find use in critical industries such as chemical processing, water and wastewater management, oil and gas, aerospace, marine and offshore, and mining, offering protection against corrosion and ensuring the safe transportation of various fluids.
While the advantages of FRP pipes are evident, it’s essential to acknowledge their limitations. These include limited temperature resistance, susceptibility to UV degradation without proper protection, specialized installation requirements, and environmental concerns related to their manufacturing process and disposal.
Industry standards and codes, including ASTM, AWWA, ISO, API, and NACE, guide the use of FRP pipes, ensuring safety and performance across various applications. Adherence to these standards is crucial to guarantee the reliability of FRP pipes in demanding environments.
In addressing frequently asked questions, we’ve provided clarity on what FRP pipes are, their common applications, installation and maintenance requirements, and the environmental considerations associated with their use. Understanding these aspects is vital for making informed decisions when considering FRP pipes for specific applications.
In a world where industries demand durability, corrosion resistance, and efficiency in fluid transportation, FRP pipes continue to be a dependable solution. Their growth, from their early days in aerospace to becoming a cornerstone in numerous sectors, is a testament to human ingenuity and the relentless pursuit of excellence in engineering. As technology continues to advance, it is likely that FRP pipes will only further expand their reach, bringing the benefits of durability and reliability to even more applications across the globe.
Frequently Asked Questions (FAQs)
FAQ 1: What Are FRP Pipes?
FRP pipes, or Fiber Reinforced Plastic pipes, are composite materials made of synthetic fibers and polymer matrix, used for transporting various fluids in a wide range of industries.
FAQ 2: What Are the Common Applications of FRP Pipes?
FRP pipes are used in chemical processing, water and wastewater management, oil and gas, aerospace, marine and offshore, mining, and many other industries where corrosion resistance and durability are critical.
FAQ 3: How Are FRP Pipes Installed and Maintained?
FRP pipes require specialized installation techniques and equipment. Regular maintenance involves visual inspections and cleaning, with minimal need for repair or replacement.
FAQ 4: Are There Environmental Concerns with FRP Pipes?
While the manufacturing process and disposal of FRP materials may raise environmental concerns, the long lifespan and corrosion resistance of FRP pipes reduce the risk of soil or water contamination.
FAQ 5: How Do FRP Pipes Compare to Other Pipe Materials?
FRP pipes offer advantages such as corrosion resistance, lightweight construction, and low maintenance compared to traditional materials like steel or concrete. Their specific advantages depend on the application and requirements.
Recommended courses (Published on EPCLand)
- Complete Course on Piping Engineering
- Basics of Piping Engineering
- Piping Layout Engineering
- Piping Material Engineering
- Piping Stress Analysis
- Material Requisitions
- Piping Material Specifications
- Valve Material Specifications
- Plant Design & Layouts-OISD 118
- Isometric Management
Library of Technical Articles
Don’t miss out the collection of 15+ articles on following topics:
- Basics of Oil and Gas Industry
- Valves
- Testing
- Tank
- Piping Bulk Items
- Pipe
- Metallurgy
- Piping Materials
- Layout
- Instrumentation
- Heat Exchanger
- Type of Contracts
- Codes and Standards
- ASTM Standards
- Articles on Piping Specialty Items
Video details of Complete Course on Piping Engineering
Don’t miss the Complete Course on Piping Engineering: Check Now
Enrollment Link
Attempt Quiz
Question 1:
What is the primary advantage of using FRP pipes in Oil & Gas projects?
Explanation: FRP pipes are preferred in Oil & Gas projects due to their high strength and corrosion resistance.
Question 2:
Which material is commonly used as a reinforcement in FRP pipes?
Explanation: Glass fibers are commonly used as reinforcement in FRP pipes.
Question 3:
What is the maximum temperature range that FRP pipes can handle in Oil & Gas applications?
Explanation: FRP pipes can typically handle a temperature range from -40°C to 150°C in Oil & Gas applications.
Question 4:
What is the primary advantage of FRP pipes over traditional steel pipes?
Explanation: FRP pipes have the advantage of being lighter in weight and offering corrosion resistance compared to traditional steel pipes.
Question 5:
Which industry standard is commonly followed in the manufacturing of FRP pipes for Oil & Gas applications?
Explanation: API 15LR is a commonly followed industry standard for the manufacturing of FRP pipes used in Oil & Gas applications.
Question 6:
What is the purpose of the inner liner in an FRP pipe?
Explanation: The inner liner in an FRP pipe is designed to resist chemical corrosion and protect the pipe.
Question 7:
What type of fluids can FRP pipes transport in Oil & Gas projects?
Explanation: FRP pipes can transport a wide range of fluids, including oil, gas, and various chemicals in Oil & Gas projects.
Question 8:
What is the typical lifespan of high-quality FRP pipes in Oil & Gas applications?
Explanation: High-quality FRP pipes in Oil & Gas applications typically have a lifespan ranging from 20 to 25 years when properly maintained and used under appropriate conditions.
Question 9:
What is the primary application of FRP pipes in the Oil & Gas Industry?
Explanation: FRP pipes find versatile applications in the Oil & Gas Industry, including offshore, onshore, and chemical processing.
Question 10:
What does the acronym “FRP” stand for in the context of these pipes?
Explanation: The acronym “FRP” stands for “Fiber-Reinforced Plastics” in the context of these pipes.